Manufacturing and industrial facilities can be particularly complex projects, involving large facilities containing behemoth machinery, hazardous chemicals, and a range of other concerns. Building automation systems and system integration are discussed.
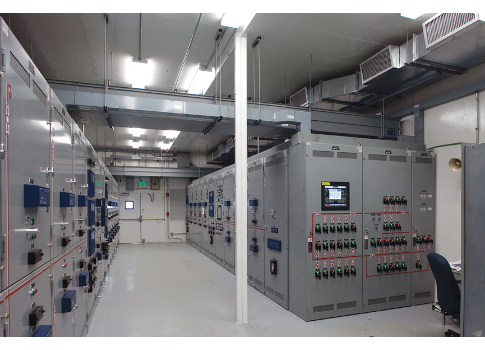
- C. Erik Larson, PE, LEED AP BD+C, Principal, Industrial Systems, Wood Harbinger, Bellevue, Wash.
- Ronald R. Regan, PE, Principal, Triad Consulting Engineers, Morris Plains, N.J.
- John Schlagetter, NCARB, PMP, CSI, CCS, CCCA, LEED Green Associate, Senior Architect, Process Plus, Cincinnati
- Wallace Sims, SET, NICET Fire Alarm Level IV, Lead Life Safety Engineer, CH2M Hill, Portland, Ore.
CSE: When designing integration monitoring and control systems, what factors do you consider?
Larson: It really is all about the user interface and how it compares with other user interfaces around the plant. You can’t design a control system with an operator interface without talking to all of the operators who will be using the interface, or you can bet that someone won’t be happy. Take the time to make sure that everyone who will need to know how the controls work buys into the arrangement. A green light might not always mean the same thing to everyone. Other factors include building in the flexibility to add, modify, or expand controls as the process needs change.
Regan: Being in the business for decades tends to make you pragmatic. The No. 1 issue for us, and echoed by the majority of our clients, is reliability of the equipment, reputation of the manufacturer/vendor, and long-term support of the system by the vendor. Nothing is more upsetting than to have a state-of-the-art high-tech system with all the possible options and have it fail, or be plagued with downtime because of bad sensors, slow response, or loss of control. The vendors that can demonstrate true reliability, yet with state-of-the-art systems, are becoming mainstream and viable, making the selection process easier.
CSE: A recent poll at www.csemag.com indicated that automation and controls is the No. 1 challenge for engineers working in these facilities. Do you agree? Why or why not?
Larson: The biggest challenge is taking the time to make sure that the automation and controls make sense to everyone who has to live with it. If you’re given the opportunity to work on-site in an industrial or manufacturing environment, jump at the opportunity and take the time to get to know the process and the people. The best way to collaborate on these topics is to immerse yourself in the environment and get to know what matters and where the opportunities to improve are. Having the time and personnel to commit to this level of engagement is where the challenges and difficulties arise.
Regan: I wouldn’t say it’s the No. 1 challenge. Certainly, it’s way up there. Most of the challenge stems, in my opinion, from the owner or his representative wanting myriad preferred vendors incorporated into one system: Brand X for sensors, Brand Y for HMI, Brand Z for CPU, Brand Q for lighting, Brand T for power, and Brand R for integrating, and, of course, some brands are proprietary and don’t want to talk to others. So, stage one in an automation project should be an open and frank discussion with the owner’s engineer to bring the system design to a reasonable and reliable level. After proof of design reliability level is established, 99% of the time a workable, practical owner-accepted system can be achieved.
CSE: Describe a recent manufacturing/industrial facility project in which you integrated HVAC, lighting, and/or daylighting with the building automation or building management systems.
Larson: The push for sustainable construction and energy efficiency has brought many opportunities to the marketplace that allow better integration between HVAC, lighting, and energy/water use monitoring. Occupancy sensors can now control not only light levels but also occupancy states for the HVAC system. This can, in turn, be used with carbon dioxide monitoring and outdoor airflow measurement to ensure that energy is only expended when there’s no other choice. The Aeroman hangar includes all of these measures, and also includes a translucent membrane roof that provides all of the light needed for aircraft maintenance, while turning on electrical lighting only when light levels fall below prescribed levels.
Regan: We recently designed a large, very upscale high-rise retail mall in the Caribbean. The owner wanted U.S. Green Building Council LEED certification and all the “bells and whistles” from cogeneration, solar, lighting controls for daylight streaming, a 200-ft-long atrium bubble skylight he saw in Dubai, energy strategic cost of cogeneration based on utility time of day costs versus load/generator fuel costs, and even an integrated control system with histogram for every parking spot; all to be tied into one central building management system (BMS). Taking each independent control system that was straightforward and integrating into a single controller was not cost-effective or practical for his application. What proved acceptable was a simple data acquisition system that was fed data from the other systems to give the owner the look of the system he wanted.
CSE: What types of cutting-edge control systems have you specified into these buildings? What type of push-back are you receiving from the contractors, clients, or other team members?
Larson: Typically, we’re adding to or extending existing control systems that are already in use, so it’s more about cutting-edge sensors and devices that add safety, reliability, or opportunities for information gathering. Remember, whatever is measured improves, so provide instrumentation that allows you to measure what your client and operators would like to make better. Sometimes, as was the case with the Aeroman hangar in El Salvador, selection of a control system was based on the availability of skilled labor to install, maintain, and modify the systems down the road.