Fire/life safety in manufacturing facilities must consider the impact that plant processes and storage can have on systems and people.
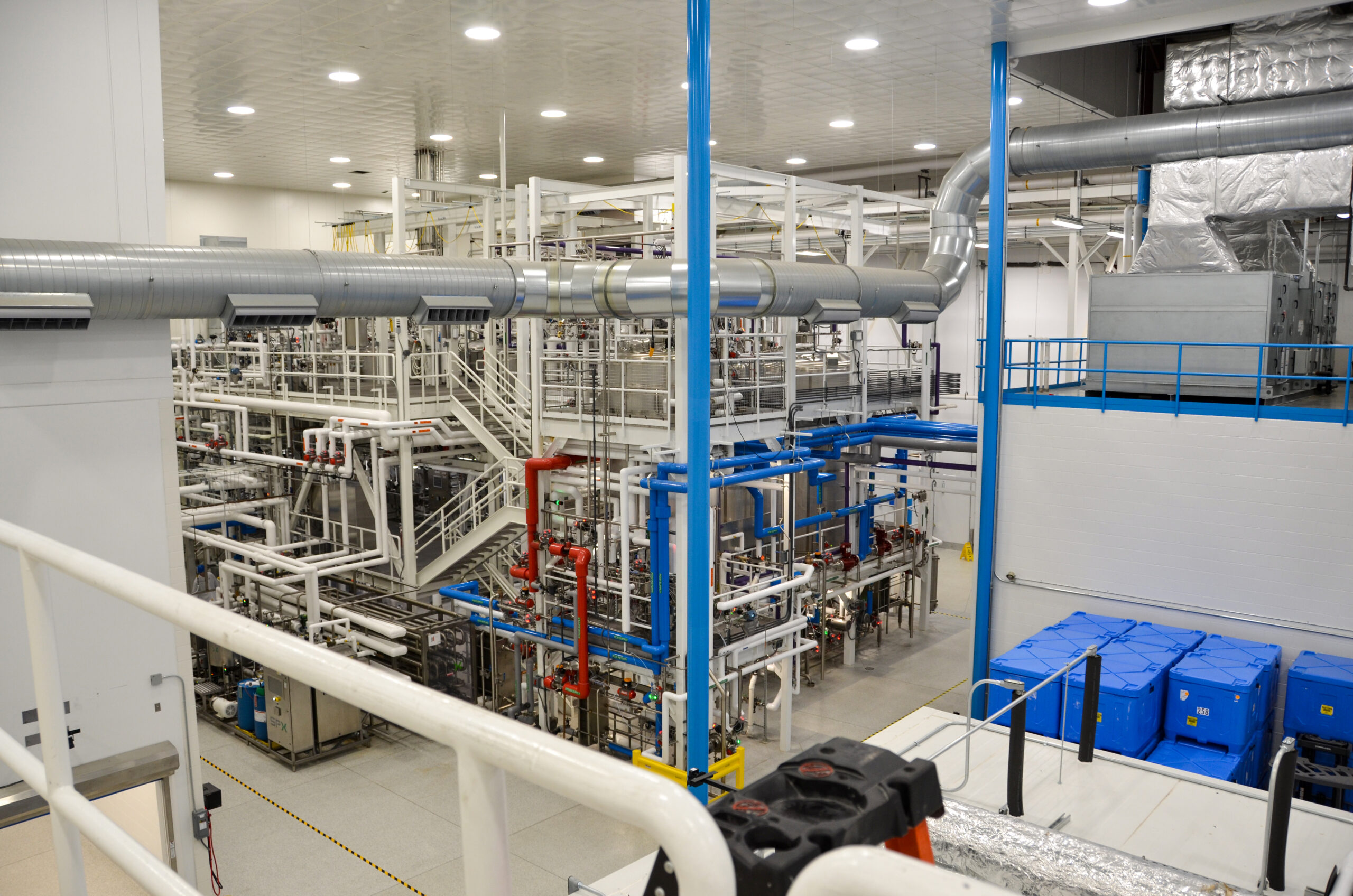
Learning objectives:
- Understand what codes and standards are used to design fire and life safety systems for industrial buildings.
- Identify how unique storage considerations can change sprinkler and alarm systems specifically.
Fire and life safety insights:
- Fire and life safety considerations in manufacturing facilities are often difficult due to the scale of such projects.
- Many codes and standards are emphasizing sustainability, changing engineers’ considerations for these facilities.
Respondents:
- Jason R. Gerke, PE, LEED AP BD+C, BCxP, Senior Design Phase Manage, JP Cullen, Milwaukee
- Jarron Gass, PE, CFPS, Fire Protection Discipline Leader, CDM Smith, Pittsburgh
- Matt Merli, PE, Principal / Client Services Director, Fitzemeyer & Tocci Associates, Inc., Woburn, Mass.
What are some of the unique challenges regarding fire/life safety system design that you’ve encountered for such projects? How have you overcome these challenges?
Jarron Gass: I am seeing an increased use of performance-based design approaches to fire protection systems in buildings that, either due to their sheer size or the processes being performed, do not have prescriptive solutions. Recently, I had an opportunity to apply a performance-based approach to a plant manufacturing and storing lithium-ion batteries, where the building stored product higher and was taller than prescriptive solutions allow. Using data derived from full-scale fire testing, published by a manufacturer and a testing agency, we were able to identify an alternative solution that we believe provides a commensurate level of protection.
Matt Merli: The challenge with these projects is that they are all very unique. There is no one-size-fits-all approach as the equipment, lines and products are typically unique and proprietary. This means, from a life safety perspective, starting each project with a review of what they do, along with the associated hazards, risks and life safety considerations, is important.
What clean agent, aerosol, chemical, oxygen reduction or other specialty fire suppression systems are typically specified? Describe a project and the system specified.
Jarron Gass: Alternative suppression systems, such as clean agent or inert gas suppression, are generally limited in larger manufacturing environments but have a role in small, specific areas within these facilities. This is especially true for clean rooms within semiconductor plants or highly sensitive electronic equipment areas inside larger facilities. Foam suppression systems are often used in high-hazard areas, such as flammable and combustible liquid storage, or in facilities where these materials are involved in open or closed manufacturing processes. Recent trends in alternative suppression focus on developing options that are less hazardous to human health and the environment, while still providing effective fire protection.
How have the trends in fire/life safety changed in industrial and manufacturing facility projects?
Jarron Gass: As manufacturing increasingly shifts toward automation, the fire protection industry has had to adapt and innovate to address growing fire challenges that don’t fit neatly into standard prescriptive protection concepts. An emerging trend in fire protection is the closer integration of safety systems. Fire alarms, suppression systems and ventilation controls are increasingly designed to function collaboratively rather than as isolated components. For example, ventilation systems can be programmed to activate automatically in response to fire alarm signals. The rise of Internet of Things technologies has also enabled more automated and coordinated safety responses. This shift supports a performance-based design approach, offering more comprehensive and effective fire protection strategies.
What fire, smoke control and security features might you incorporate in these facilities that you wouldn’t see on other projects?
Jarron Gass: In a specific project at a recycling facility, a performance-based approach was employed to address a challenging fire scenario where traditional prescriptive suppression methods fell short. This innovative strategy integrated several systems through automated logic to work in harmony and enhance fire and life safety measures. The approach combined smoke and heat detection with automatic water monitors, which directed water spray at specific heat signatures identified by infrared detection. Additionally, automatic venting was activated to help control the smoke layer. While none of these measures were conventional on their own, they collectively provided the level of protection required to safeguard life and property in this challenging environment.”
Do you see any future changes/requests to the structural design of these buildings regarding fire/life safety systems?
Jarron Gass: This is another challenging aspect from a fire protection standpoint, where engineers and architects constantly strive to balance competing factors, primarily constructability, survivability and sustainability. The goal is to achieve maximum strength with minimal material, whether by volume or density, to create a cost-effective yet safe structure that meets minimum code requirements and incorporates stakeholder needs. This involves balancing the size of structural elements with factors, such as supports, aiming to maximize clear spans. Finding new methods to treat structural members with fire retardant materials that maintain necessary fire ratings while allowing increased loads or spans could influence future building designs.
How has the cost and complexity of fire protection systems involved with industrial and manufacturing facility projects changed over the years? How did these changes impact the overall design process?
Jarron Gass: Costs have risen at least commensurate with inflation, and with each new advancement or breakthrough, whether it’s a new material, a new listed approach or a new protection scheme based on full-scale fire testing. It’s becoming increasingly expensive to get products listed through national testing protocols like UL or approved by FM Global. Similarly, the costs associated with performance-based design approaches can be higher, as these efforts are often unique to a single challenge and cannot be repeated on subsequent projects. This is especially true when full-scale fire testing in a laboratory is relied upon for developing proper protection schemes.
How have changes to codes, BIM and wireless devices/systems impacted fire and life safety system design for these buildings?
Jarron Gass: In my experience, codes and standards have lagged behind available technology, especially considering the time it takes for a new product or process to be formally adopted into regulations. This process typically involves approval by the regulating body, followed by acceptance by the AHJ. It can easily take three years or more for these advancements to be fully developed, tested, listed, codified and accepted. The natural delay in the code adoption process has hindered the implementation of wireless fire alarm devices. However, the use of wireless devices is increasing as reliability, security protocols and protection from interference continue to improve.