In this follow-up Q&A, learn how to select and specify the correct transfer switch control, based on application
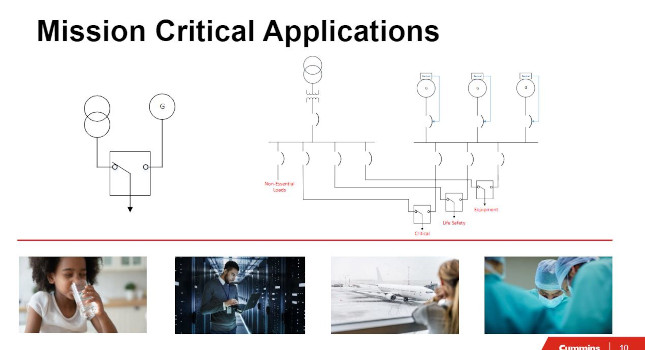
A critical component of a transfer switch is the control. Transfer switches and their control systems are an important piece of the puzzle in any electrical or power system. Available in a variety of types with a wide array of options, it is important to understand a transfer switch’s features and functions for the success of any power system.
As a follow-up to the June 9, 2022, webcast on “Specifying transfer switch controls,” questions were answered by Hassan Obeid, Senior Global Technical Advisor – Energy Management Solutions, Cummins Power Generation.
What needs to be coordinated for controls when attached to paralleling gear?
This question may vary a bit depending on supplier. For Cummins, the paralleling functions are all handled by the generator set controls, so there is a set of load sharing wiring that runs from generator set to generator set, and each generator set also gets a start signal from each transfer switch. When a system level control is used, the start signals can come from the transfer switch through the system level control to the generator sets.
When do we use closed transition switches versus open transition switches, and what are the pros/cons?
Open transition is less expensive. Of course, you do have a very brief power failure every time it switches, even if both sources are available. Closed transition transfer eliminates the total power interruption on transfer, but does not completely eliminate a “disturbance” due to switching if the timing of all the closed transition switches are set appropriately. However, it is typically not a large enough disturbance to cause a problem. Please refer to the closed transition white paper for more information.
What alarms points can be sent to the building management system? How many dry contacts are available on each transformer sw?
Anything displayed by the controls can typically be transmitted to a BMS/SCADA.
Any specifics to address for 13.8 KV level equipment?
Transfer switches are generally available for systems rated at up to 600 Vac per UL 1008. At higher voltages, the transfer functions are handled by insulated case or power air circuit breaker pairs. When breaker pairs are used, the transfer logic should be accomplished via dedicated control. Control functions should be the same as you would use for a typical transfer switch application at lower voltage levels (600 Vac).
What is the industry standard allowable export value in kw/time when setting a 32 relay for paralleling?
There is no industry standard for this parameter. You need to check with the utility and get the intertie agreement.
What is the difference between utility-to-utility setup versus utility-to-generator for transfer switch controls? Can a transfer switch be field modified and still maintain UL listing?
For Cummins the same product is used for both types of sites. The service technician sets it up for proper operation. Yes, it can be modified in the field and you would have to check with the local authority having jurisdiction to see if an AHJ is needed to come and inspect.
Since one does not know which manufacturer will be feeding the transfer switch, do you advocate using fused switches to make the feed brand agnostic?
No, as most clients don’t like the idea of having to stock fuses to cover their system needs. Murphy’s law says you won’t have a fuse on hand when you really need it.
How much do controls vary among manufacturers?
Everyone watches everyone else, and there are multiple levels of controls from most suppliers. Most suppliers have at least two types of controls for line voltage applications. There are commonalties between the control functions. The latest controls from Cummins have the highest level of features that you can find in the industry all packaged in one control for the outmost level of reliability, serviceability and operation.
Typical time delays for switch over from utility to backup and reverse?
From utility to back up power, the allowable time delay per NFPA 110: Standard for Emergency and Standby Power Systems is one second. From backup power to utility, once a site has experienced a normal source failure it is a good idea to stay connected to the generator for at least 30 minutes or so —just to make sure that there isn’t another power interruption that is likely to occur.

Can you discuss automatic transfer switch reliability calculations?
There is no standard for defining reliability of any emergency power equipment that I am aware of. Designers should be aware of this because no standard in place today attempts to require system reliability. Because of this, it’s important to specify transfer switch equipment that can be directly supported by the generator set supplier, rather than having two companies to call on a power failure, or for that matter any issue with the emergency power system.
Does Cummins offer medium-voltage transfer switches?
Cummins does a lot of MV systems, which typically use MV power circuit breakers as the switching mechanism.
If we have an outdoor ATS (NEMA 3R) in the Pacific Northwest, should we both a heater and dehumidifier or just a heater inside? Would the heater be powered from the ATS or powered from a separate power source (i.e., customer’s power source)?
If the ATS is in a controlled environment (such as indoors), it probably does not need a heater. If it is not, then a heater is a good idea. Power for the heater should come from the load side of the switch. Also, thermostat within enclosure to control heater is typically specified.
Since we normally do not know at bid time which brand of transfer switch or upstream overcurrent device is going to be selected, do you advocate specifying a fuse upstream from a transfer switch to ensure the proper withstand current rating at the ATS?
You should only specify fuses if you are CERTAIN they are needed for proper protection, and the site has maintenance practices to keep proper fuses in stock.
What is the impact on cost due to changes in the level of control required?
The Cummins transfer switch control has all these features with no additional cost.
How common is the three-source system and what are the typical applications?
This type of system is used with VERY critical applications that have very little tolerance for power failure. This isn’t as common as it used to be because of the advances in paralleling controls that make paralleling a very low cost (almost free) feature from many suppliers.
To what extent, if at all, is arc flash an issue with the switch?
Arc flash is primarily related to protection of an operator that is servicing the transfer switch. The protection engineer should perform a system level analysis to calculate the incident energy and the proper personal protective equipment. These labels then can be added to the front of the switch.
What should be ambient temperature of the controls?
The acceptable temperature range for a transfer switch depends on the manufacturer. Cummins transfer switch control range is -40ºC to 70ºC.
What maintenance person should do if the transfer switch does not close?
In most cases, the operator or a service technician would put the transfer switch in manual mode, then operate the switch with a manual handle. This is required per code in extreme conditions if the switch fails to operate.
What are the tolerances for passive synchronization (+/-)?
Cummins typically uses frequency within 0.1 Hz, voltage within 25 volts.
How transfer switch handles with inrush current such as large motor loads?
The surge current from any motor starting will always be considerably lower than the potential short circuit current from the normal source. So, we typically only look at the normal source for verification of the protection needed for a transfer switch. If there is a paralleling application with multiple generators, you should check both the generator bus available fault current, as well as the normal source.
Are elevators the only devices in which the ATS must send a pre-transfer signal?
Clearly the most common, but I would not say “only.” Certain medical equipment requires controlled retransfer time to avoid delivering poor results.
What considerations should we look at to ensure we are energy efficient in our specifications?
Transfer switches generally don’t consume power, but they do impact on the fuel consumption of the generator set based on time delays that you use.
Could you please compare advantages and disadvantages of a manual transfer switch and generator docking station?
A manual transfer switch and generator docking station is required in the latest version of NFPA 110. In general, where the system uses a single installed generator, the temporary generator will be set up to automatically start on a power failure when the permanent generator is out of service.
Would it be helpful to perform a power transient stability study and do computer simulations before commissioning in order to help with settings such as time delays and generator wind down.
I don’t think this would be very practical. There is enough difference in performance between suppliers, and even common practices for describing transient performance that it would be difficult to make a study that could be “standardized.”
Are the Cummins ATSs complaint with NFPA 110?
Yes. Note that NFPA 110 Type 10 is a system-level standard, and not only on transfer switches.