Read this webcast transcript for tips on specifying overcurrent devices, such as fuses and breakers
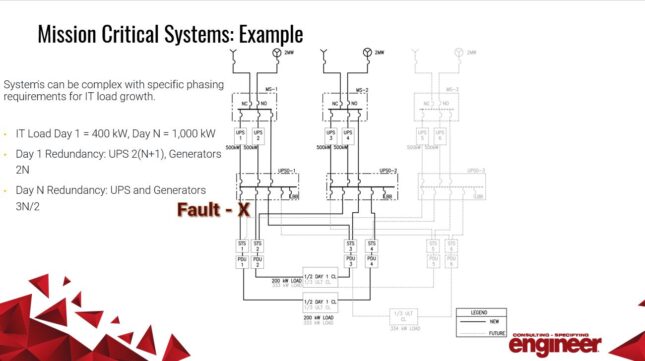
Overcurrent device insights
- The topic discusses the intricacies of selecting and coordinating overcurrent devices, such as fuses and breakers, particularly in building design.
- It delves into the advantages, challenges and considerations involved in achieving optimal selectivity and safety within electrical distribution systems.
Learn about the choices and criteria for the planning and design of mission critical facility overcurrent devices, fuses, circuit breakers and other electrical systems. Design engineers must coordinate electrical systems so that the protective device closest to the fault opens first, and quickly enough, to prevent the upstream devices from operating.
This edited transcript of the Jan. 31, 2024, webcast Critical power: How to design for selective coordination in mission critical systems can be used to help electrical engineers when specifying overcurrent devices.
Presenters:
- Radames Cocco, PE, LEED AP, Principal Electrical Engineer, Spectrum Engineers
- Joshua Fluecke, PE, LEED AP, Senior Principal, Syska Hennessy Group
Joshua Fluecke: Here’s a mission critical system example. In Figure 1, we see data center equipment typical for a commercial data center. These are optional standby systems for NFPA 70: National Electrical Code (NEC).

However, we’ll want to take the same approach as the NEC requirements for selective coordination to minimize outages of a business data center function. We want to ensure a fault on a downstream circuit breaker does not cause an upstream circuit breaker to trip under several different failure scenarios.
As you can see here, we have multiple utility sources, generators, specific data center electrical equipment like static transfer switches, power distribution units and uninterruptable power supply systems. Additionally, this system is designed to expand and cross-tie with new sources as the future IT load grows for this type of facility.
It’s important to understand the facility and how it will function in the future, all needs to be taken into consideration for selective coordination. This adds another layer of complexity to selectivity analysis and protective device selection for these systems and components.
If we’re to create some definition around what is a mission critical facility, what does that look like? These facilities have many of the same things in common, such as 24/7 operations and functions that cannot be interrupted. But keep in mind that the NEC mandates for selective coordination are related to life safety and legally required standby systems intended to continue operation for preservation of human life and critical systems. There are also several business functions, for instance, like a commercial data center that benefit from having the selective coordination philosophy in place for business continuity reasons which are not NEC mandated and they have no relation to life safety or legally required standby systems.
A data center is like other building types where there will be prescriptive code requirements for selective coordination of life safety and legally required critical systems. There will be people in these facilities, occupied by people just like a health care facility or other business function. They will have elevators, perhaps have some fire pumps, egress lighting, all this is going to require selective coordination.
In addition to data centers requiring a high degree of reliability and resiliency supporting the compute function of the business and their power and cooling needs with backup power, these systems are considered optional systems by the code, you do not need to do this. The business is choosing to provide this level of protection for its systems. Due to the critical nature of their business function, designers need to implement stringent selective coordination requirements for these systems to behave as intended.
Data centers are somewhat unique compared to other types of facilities due to their electrical systems’ complexity and unique components which need to be considered for selective coordination studies. A few common differences are multiple utility sources. In that study, each utility source will need to be modeled independently from each other with actual RMS values available from the utility and short circuit information provided by the serving utility.
Usually there’s multiple standby sources, so each engine generator source will need to be modeled separately from the utility and analyzed for selective coordination. These facilities typically have large-scale UPS systems with battery backup, which is a different component than most other types of buildings.
Also, a data center has many possible different failure scenarios depending on the complexity of design and the resiliency and redundancy required by that customer or client. So each failure scenario, and there could be many, would need to be modeled independently and evaluated on its own to determine the best criteria for selective coordination.
Watch the webcast to review a SKM one-line output file, but they have these complex electrical distribution schemes with all these discrete components, so here’s an example, this type of one-line, once you input this information in a power systems analysis module like SKM and it’s generated.
This is the output generated with multiple sources, you may see a generator, you may see utility source in here, but each individual component in here, and this is crucial, like motors, branch circuit, feeder lengths, protective devices, system topology, etc., is required to be modeled correctly per the manufacturer’s drawing parameters and the settings of that device. The information that goes specifically in the model needs to be correct for what’s actually installed. This is a critical point of understanding to make sure that we’re selectively coordinating with exactly what is installed in your project.
Designing overcurrent devices
Radames Cocco: Designing overcurrent devices, particularly for buildings, involves choosing between fuses or breakers, each with its advantages and disadvantages. Fuses offer full selectivity to high fault currents more easily and are simpler to maintain. However, after an event, the fuse must be replaced, necessitating a good spare program. They can also be larger than breaker-based solutions.
Breakers, on the other hand, are commonly used throughout distribution systems, are easy to reset, and can be more compact. Yet, achieving selectivity becomes more challenging in the instantaneous region, and there are limited combinations at higher fault current levels. It’s also important to note that breakers require recertification after a few operations.
A time current curve is shown in Figure 2. It’s a log-log function, essential for visualizing quick occurrences from 0.01 to a thousand or more seconds. On the right side of the distribution, various fuses are integrated, with one feeding a transformer and another leading to downstream branches. The coordination between them is crucial, ensuring efficient operation.

Different types of fuses, like dual element or time delay, can be selected based on the loads they will serve. Similarly, breaker curves require careful consideration, with various parameters like longtime pickup, short time pickup, and instantaneous pickup playing roles in ensuring selectivity. Selectivity ratios guide the design process, ensuring a well-coordinated system.
Selective coordination is vital, as outlined by NEC, especially concerning overcurrent device operating times and associated currents. Breaker curves should not overlap, particularly concerning fault currents. Manufacturer specifications and limitations must be observed for proper coordination.
Ground fault protection is comparatively straightforward, usually electronic and adjustable. However, health care facilities require at least two levels of ground fault protection.
Increased selectivity affects arc flash energy, with devices operating at higher fault levels or after more time passes. This trade-off must be carefully considered in the design process to mitigate risks effectively.
Competitive bidding is facilitated by designing systems with adaptable overcurrent devices, ensuring functionality without compromising on cost-effectiveness. Specifications define the required level of selectivity for different systems, ensuring clarity for all stakeholders involved.
Coordination extends beyond overcurrent devices, necessitating collaboration with other disciplines to ensure overall system integrity and safety.