Several new and retrofit manufacturing building projects show trends in fire and life safety systems
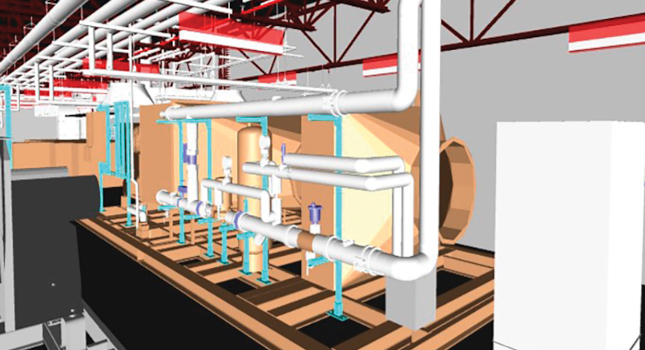
- Brian Arend, PE, LEED AP, Electrical Engineering Manager, SSOE Group, Toledo, Ohio
- Shane R. Eckman, PE, LEED AP, Vice President, Industrial & Institutional Practice Leader, Stanley Consultants Inc., Minneapolis
- Kevin LaPlante, PE, LEED AP, Mechanical Group Leader, CRB, Medford, Massachusetts
- Sunondo Roy, PE, LEED AP, Director, Design Group, Romeoville, Illinois

What are some of the unique challenges regarding fire/life safety system design that you’ve encountered for such projects? How have you overcome these challenges?
Shane R. Eckman: Our biggest challenge is getting information on the chemicals being used in a process area. Information requested would normally include which chemicals and amounts, concentration levels, how they are being used (closed or open systems), storage and spill containment and if normal operation involves sampling or handling of chemicals that could result in a release of the chemical. As a lot of these processes involve intellectual property, the client may not want to share this information so we find a way to gather enough information to provide a safe and code-compliant design.
Brian Arend: The real challenge isn’t with the life safety systems, but with how we design these systems in plants using technologies where code hasn’t been applied yet. The battery and electric vehicle markets are offering some challenges with applying code. Lithium batteries offer unique challenges with fire safety and personnel evacuation in case of emergency or failure. In some cases, we’re working closely with the code officials and offering detailed code reviews to assist.
Sunondo Roy: One of the biggest project risks and design challenges are associated with systems that can cause catastrophic operational failures. Top on that list includes fire/explosion hazards due to uncontrolled dust and flammable vapors. Working closely with the entire design team, the client and their dust hazard assessment consultant ensures that major risks associated with airborne dust and flammable vapors is mitigated. Communicating the potential risks and working as a team to make sure the risks are properly investigated and credible threats are mitigated is the key to successful projects.
What fire, smoke control and security features might you incorporate in these facilities that you wouldn’t see on other projects?
Shane R. Eckman: As some buildings house processes that could generate chemical vapors or dust, the spaces need to be designed to address the possibility of an explosion. The areas will normally incorporate HVAC systems designed to negate the buildup of these gases and dust and incorporate pressure release wall panels and blast-resistant walls to mitigate the potential explosion and damage it might cause.