Learn tips on how to design labs and research facilities — some of the most high-tech buildings around
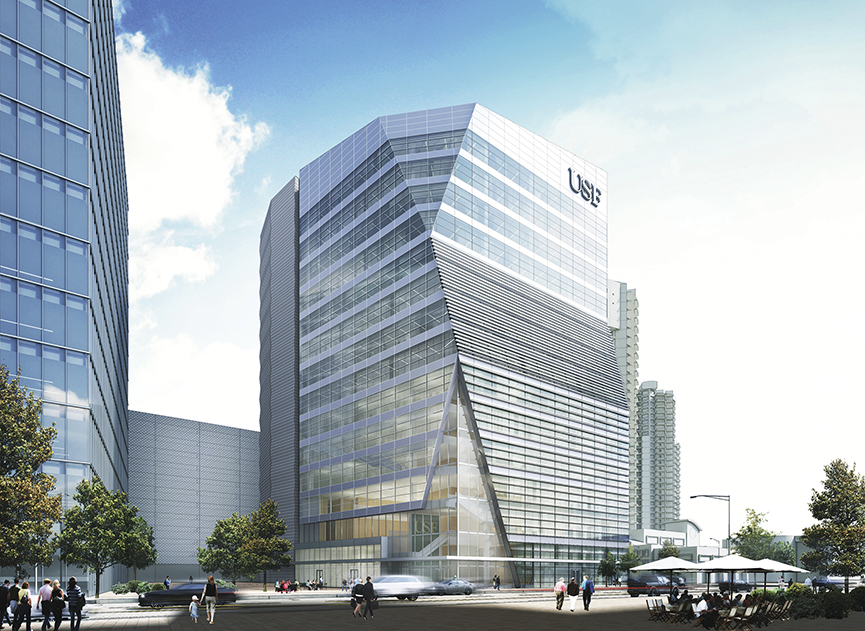
Respondents
Kelley Cramm, PE, LEED AP BD+C
Associate/Mechanical Technical Leader
Kansas City
Bryan Floth, LEED AP, AIA
Senior Project Manager
Kansas City, Mo.
George Isherwood, PE
Vice President, Health Care/Laboratory Group Leader
Troy, Mich.
Adam Judge, PE
Associate/Mechanical Project Engineer
Tampa, Fla.
Iain Siery, PE
Senior Mechanical Engineer
Philadelphia
David Wilson, PE, LEED AP
Senior Engineer
Raleigh, N.C.
Bios
Kelley Cramm
Cramm is an associate and mechanical technical leader at Henderson Engineers. She received a 2019 ASHRAE Exceptional Service Award and has more than 30 years of industry experience.
Bryan Floth
Floth leads architecture and integrated design-build projects across the U.S. for the company. With nearly 30 years of experience, he has partnered with clients throughout his career to design and implement complex higher education, commercial, industrial, institutional and mission critical facilities.
George Isherwood
Over his 35-year career, Isherwood has worked on numerous new-construction and renovation projects. His health care work includes patient towers, ambulatory care facilities, operating rooms, cardiac catheterization labs and more.
Adam Judge
As Associate/Mechanical Engineer, Judge works on a broad range of project types. He has a wealth of laboratory experience, including recent renovations at the University of South Florida College of Medicine.
Iain Siery
Siery brings 14 years of progressive experience to the science and technology sector to CRB. His areas of specialty include mechanical utilities, HVAC, industrial ventilation and plumbing design for critical environments in R&D and manufacturing.
David Wilson
As senior engineer with Dewberry, Wilson centers his work on mechanical, electrical and plumbing projects. He brings more than three decades of engineering experience to the firm.
CSE: What unique heating or cooling systems have you specified into such projects?
Judge: On one large research laboratory building project, the typical floor plate was approximately half laboratory space and half office and circulation space. Naturally, the laboratory half of the building needed to be fully exhausted, which would typically require 100% outside air. The nonlab half of the building had a fairly significant excess of outside air due to the ventilation requirements being much greater than the exhaust requirements. Typically, this excess outside air would be exhausted as relief air from the building.
Instead of throwing this conditioned outside air away, we transferred all of the excess outside air from the nonlab half of the building to the large open labs on each flow via transfer ducts and grilles. This reduced the total quantity of outside air that had to be brought into the building and conditioned, which presented a significant energy savings in the hot, humid Florida environment. In addition, large fixed core energy recovery units were used to transfer both sensible and latent energy from incoming outside air to the exhaust air stream.
Siery: Precise humidity control can be critical for some laboratories where the science requires low humidity. Where room dewpoint must be maintained below roughly 48°F reliably, the use of desiccant dehumidification is required. These systems have additional utility demands for reactivation of the desiccant and require specific moisture load calculations and careful psychrometric analysis. This becomes even more challenging when spaces are exhaust driven or 100% exhausted. The lower the humidity requirement, the more critical the complimentary design of the room becomes. Considerations include things like: Is a vapor barrier required to separate the low humidity space from surrounding spaces? Should an airlock be included? Answering these questions requires a careful analysis of the room operations and criteria.
Wilson: Research spaces requiring low temperature and relative humidity are certainly a challenge for chilled water and/or direct expansion refrigeration cooling systems. Several projects I have been involved in incorporated dedicated desiccant dehumidification systems to meet low space temperature and humidity requirements.
CSE: Describe a recent project with specialized fume hood requirements. How did you meet the client’s needs?
Isherwood: Some laboratories that we have been designing have multiple operating conditions. If a hazardous spill or contamination leak is detected, the system needs to go into high purge mode to evaporate the hazard. Therefore, we are design separate systems for each operating condition. The normal condition is using a smaller energy recovery device and the purge system is using a high flow, limited temperature conditioning equipment. This is being used to keep costs down for a condition that hopefully will never occur in the laboratories.
Wilson: Providing a hydrofluoric acid fume hood in the center core of the lowest floor of an existing five-story facility. An acid scrubber was provided above the fume hood along with a booster exhaust fan and then the scrubber discharge was connected to the building manifolded hazardous exhaust system. A route for a dedicated exhaust duct for the fume hood was not available, so the acid scrubber was provided as an alternative that was acceptable to the owner’s environmental health and safety department and research manager.
Siery: An R&D client of ours was looking for a containment solution to replace a chemical waste bulking function in a waste staging room. A laboratory services group collected waste daily from the building labs and collected them in this room. They bulked compatible chemicals into 55-gallon drums for disposal off-site by a third party. They used bung funnels and had a rough secondary containment setup.
Through EH&S monitoring of the personnel exposure during this process, it was discovered that significant exposure was possible while the operators poured volatile chemicals into the drum funnels. We worked with fume hood manufacturers to design a custom floor-mounted fume hood with integrated secondary containment that allowed operators to wheel 55-gallon drums in and out as needed. A customized double sash arrangement was designed to provide a shield for the operator while still allowing for an ergonomic working position. The interior of the hood was complete with a ground bar with grounding clips to easily attach to the drums.
We ended up with a much safer operation than before. The main takeaway for me was that we could not have met the owner’s expectations if we had not included all the right stakeholders in the design process. From operators helping explain their challenges and vet ergonomic issues to the fume hood manufacturers willingly exploring the possibilities with us, integrating the right people in the process ultimately helped us succeed.
Cramm: We had a recent project that included multiple large floor-mounted hoods, several perchloric acid hoods and numerous fully exhausted clean benches that use hazardous materials. Perchloric acid hoods present a unique challenge due the inherent danger associated with perchloric acid. The ductwork should extend directly to the roof and have a washdown system to prevent the buildup of perchloric salts. We used fans that induce air rather than fans that are directly in the airstream.
Rooms with multiple hoods present a challenge in supplying makeup air. The cross draft in front of a hood face should preferably be less than one-third of the hood face velocity. Standard diffusers can’t be used. We use special diffusers that supply air at an extremely low velocity.
Judge: A large university research building included radioisotope hoods. The air from these specialized hoods had to be independently exhausted through bag-in bag-out high-efficiency particulate air filters and a high plume exhaust fan on the roof.
CSE: What types of unique building pressurization have you designed in labs/research facilities?
Cramm: We’ve designed some laboratory projects that included a biosafety level 3 suite. The pressurization in these facilities was a challenge. We create a pressurization plan for every lab project we design. This plan illustrates the pressure relationships between all rooms and shows which way the air should move between the spaces. It’s important to understand cascading pressures and design systems that maintain the needed relationships over time.
Siery: Active room pressure controls are the most complicated pressurization system I have encountered. These systems automatically adjust to maintain a direct measure of the room pressure and are used particularly in high containment situations. Typical laboratories leverage offset tracking to maintain a bulk directional airflow. However, they do not measure the actual room pressure. When critical pressure differentials are necessary and the containment requirements necessitate direct control of room pressures, it is typical to leverage room to reference pressure measurement and relatively slow control loops to accomplish stable control. Often the room to adjacent room differentials are monitored to provide feedback and potentially alarming of a pressure out of range or reverse of directional airflow to improve safety. These systems must be carefully designed but can be an important measure to achieve high levels of containment.
Wilson: Passive pressure control with cubic feet per minute offset between supply air and exhaust airflow has been used numerous times and is a common approach for laboratory HVAC systems. Active pressure control with modulation of supply airflow from minimum to maximum to meet the desired building pressurization offset has been used on numerous projects with success.
CSE: What unusual or infrequently specified products or systems did you use to meet challenging heating or cooling needs?
Judge: On a large laboratory building, the vivarium required not only stringent temperature control, but also humidity. To prevent animal spaces from becoming too dry during the winter months, humidifiers were required. Instead of the traditional atmospheric steam humidifiers, we used adiabatic humidifiers. These units use pumps to pressurize water, which is expelled through nozzles as a mist into the airstream. The system eliminates the need for steam generation, which results in significant heating energy reduction.
Siery: Desiccant dehumidifiers can be challenging to get right. In order to precisely control moisture in low-humidity environments, these systems rely on detailed room moisture load calculations which few engineers have extensive experience with. Factors such as the moisture permeance of walls and ceiling materials along with challenges in estimating infiltration make them particularly interesting to work with. Room humidity less than 40% relative humidity at typical laboratory temperatures (approximately 72°F) quickly become complicated to achieve and involve combined effort from the architect and engineer working together. HVAC engineers don’t typically get to consider how interior partitions are detailed, but when precise humidity control is needed, it is critical that the whole picture is considered.
CSE: How have you worked with HVAC system or equipment design to increase a building’s energy efficiency?
Cramm: Energy recovery in lab buildings is a given, especially buildings with a lot of fume hoods. Since ASHRAE 62.1: Standards for Ventilation and Indoor Air Quality strongly discourages the use of energy recovery strategies that allow cross contamination, the options are limited. We typically use a run-around loop, which is only about 50% efficient. One of the most important strategies to decrease the energy consumption in a lab building is to install only the number of fume hoods that are necessary and to keep air change rates to a minimum. In the past, lab designers routinely designed lab air supply for 10 to 12 air changes per hour. We now know that lower air change rates, with efficient air distribution strategy, provide as good or better containment at a much lower energy consumption.
Judge: We try to maximize the effectiveness of energy recovery systems by selecting and specifying highly efficient systems. On the University of South Florida project, the chilled water from the district plant was guaranteed to be supplied at 37°F to 39°F — much lower than typical plants. We economized on this by designing our AHUs with lower leaving air temperatures than typical, resulting in lower airflows required to meet cooling loads.
Siery: High-efficiency equipment and energy recovery have become commonplace in research environments. As the systems engineer, we can specify those things and achieve the best possible efficiency for generating heating or cooling energy. But to step further requires we challenge conventions for designing the system distribution and consider how to reduce the required energy consumption.
One area I have focused on recently is pressure drop in HVAC distribution systems. The cost in terms of fan power to push through the entire system is often overlooked. We specify air handlers almost without considering if 500 feet per minute is the best choice for sizing cooling coils. The purchase cost of an air handler occurs one time in its life span, but the fans run possibly 30 or more years for custom AHUs. Obviously reducing pressure loss in AHUs and duct systems means smaller fans but physically larger systems (coils and duct), so finding the right balance is important.
In Europe, energy regulations for maximum fan power requirements force cooling coils selections at closer to 300 fpm (maximum). I think it is important to pay attention to the life cycle costs of these decisions so we can help our clients make the best choices.
CSE: What best practices should be followed to ensure an efficient HVAC system is designed for this kind of building?
Judge: Work with the owner’s EH&S department to set minimum air change rates. Don’t settle for arbitrarily high rates. Specify high-efficient low-flow fume hoods with either automatic sash closers or zone presence sensors. Maximize energy recovery without compromising air quality and occupant safety. Think about getting your exhaust and outside air ducts adjacent in your equipment rooms during schematic design. If your outside and exhaust air ducts cannot run past each other, it will be much more difficult to design an effective energy recovery system.
CSE: What is the most challenging thing when designing HVAC systems in such buildings?
Judge: Anticipating equipment thermal loads and exhaust requirements, especially if they are not programmed from day one. Systems must be designed with sufficient flexibility, but not grossly oversized.
CSE: What type of specialty piping, plumbing or other systems have you specified recently?
Wilson: Laboratory and research projects commonly require specialty piping materials for lab waste and vent systems as well as acid neutralization systems (passive systems with limestone chips in tanks or active systems that monitor pH and inject chemicals to maintain desired pH levels) before discharging to municipal sewer systems. Other specialty piping systems include ultrahigh purity piping systems for specialty gases, oil-free compressed air systems and high purity (reverse osmosis deionized) water systems.
Cramm: We had a recent project that had the need for several different types of ultrahigh purity gases including hydrogen, nitrogen, carbon dioxide and argon. These gases require special materials, joining methods and installation protocols to ensure they are not contaminated. They were distributed from high-purity cylinders located in a service area adjacent to the labs. This allowed for automatic changeover manifolds with alarms.
One thing that often gets missed with asphyxiant gases such as nitrogen, argon and CO2 is the need for O2 sensors to alarm in the event of a gas leak. The plumbing system we encounter on most labs that tends to be the least understood is purified water. It’s important to understand how the water will be used so the correct levels of purification and the strategies used will meet the lab’s needs.
Judge: A recent research laboratory project contained a specialized lab that required very high-purity nitrogen gas piped in. Copper and solder could potentially leach enough material into the nitrogen that it would be unusable for the equipment and processes used in the lab. So, the high-purity nitrogen had to be piped with stainless steel and orbital welded.