Industrial, manufacturing facilities have high power needs, and electrical engineers must rise to the challenge
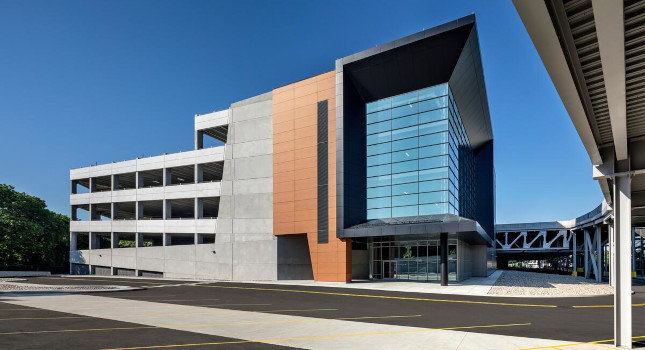
Insights on manufacturing facility electrical systems
- The end-use determines how electrical and power systems are designed in an industrial or manufacturing building.
- Lighting and lighting control specifications are often determined by long-term use and maintenance.
Respondents:
- Jason Gass, PE, CFPS, Fire Protection Discipline Engineer, CDM Smith, Pittsburgh, Pennsylvania
- Alex Engelman, PE, LEED AP, CEM, Associate Principal, Syska Hennessy Group, New York, New York
- Matthew Merli, PE, Principle/Science & Technology Market Leader, Fitzmeyer & Tocci Associates Inc., Woburn, Massachusetts

Are there any issues unique to designing electrical/power systems for these types of facilities?
Alex Engelman: High concentration of nonlinear loads in industrial and manufacturing facilities generates high levels of harmonic distortion. The harmonic distortion, if not addressed, can affect equipment functionality, longevity and operating cost. Harmonic studies are performed to identify the most cost-effective ways of addressing the harmonics and confirm that distortion does not exceed IEEE recommended limits.
There are several ways in which harmonics are mitigated such as active and passive filters, specifying distribution equipment capable of handling the harmonics such as k-rated transformers, increasing feeder sizes. Increasingly, with newer equipment eliminating or minimizing harmonics at the sources is becoming one of the best ways to handle harmonics. Often, this requires close coordination with end-user equipment. Power factor correction for large industrial sites also very commonplace; our designs help anticipate these for budgeting with the final selection of active harmonic filters and power factor correction being selected after operations start.
Matthew Merli: There are unique issues to electrical/power systems for industrial type projects, mostly depending on what the end-user is doing. Some things to consider that are typical issues are things like clean power. If the process is susceptible to surges, then evaluating ways to protect that is critical. Also, coordinating with the utility is very important at the outset of any project. Many of these buildings have enormous electrical loads and coordination with utility to make sure design, construction and utility teams are aligned is important.
What types of unusual standby, emergency or backup power systems have you specified for industrial and manufacturing facilities?
Alex Engelman: Besides providing emergency generators, a lot of facilities are keen on being able to use roll-up generators to supplement and support facility operations during a power outage. The electrical service is designed such that a roll-up generator can be easily connected. Additionally, fuel-cells and various types of battery systems are often evaluated, however, our clients have not taken that leap. In denser cities, we often consider providing Tier 4 generators to participate in utility demand response programs. This allows the facility to support operations throughout an outage but also gain revenue and help the utility by turning on generators during peak demands on the grid. For some critical production, we are using uninterruptible power supply (UPS) systems that allow for continuation of a process until completion or generator power is up.
Matthew Merli: For backup power, it is critical to understand the process. There are certainly projects where the process may need a UPS because a sample could be lost in event of power outage or something of that nature.
What are some key differences in electrical, lighting and power systems you might incorporate in this kind of facility, compared to other projects?
Alex Engelman: Future flexibility is one of the key elements in industrial facilities that we run across. Not knowing the exact equipment that would ultimately be provided by the owner, requires us to design with flexibility in mind by making future provisions and allocations within electrical distribution. Moreover, for distribution and sortation type of facilities, the advent of electric vehicles (EV) is significantly impacting the electrical service due to large quantity of fleet parking. Understanding the operations and EV charge management system becomes critical to right-size the facility electrical service. Bus type electrical distribution is very common for our manufacturing clients as machines change over time, and plug-in bus allows for quick changes to electrical distribution at the process level.
Matthew Merli: Regarding lighting, typically these facilities are large and have higher footcandle level requirements within process areas (when compared to a typical office area or something like that). The process/manufacturing/industrial areas typically have heavy and/or precise machinery where higher (and even) lighting levels are important for occupant safety.

How does your team work with the architect, owner’s rep and other project team members so the electrical/power systems are flexible and sustainable?
Alex Engelman: We always try to understand the ultimate operations and logistics of the facility, this allows us to advise the owners and architects of various new technologies and options as opposed to having a top-down approach. On a recent project, we were able to implement an electrified strut systems (bus) that provided the client with flexibility of connecting lighting and various power and telecommunication/security devices directly to the bus distribution. Similar systems are used in laboratories and data centers but not frequently implemented outside of those markets.
Matthew Merli: Expansion capability for industrial/manufacturing buildings is critical. Large electrical infrastructure (transformers, switchgear, generators) still has very long lead times (years, in many cases), so to have to deal with that issue again on a future build-out would be troublesome. Getting the equipment for future flexibility and expandability is critical. Additionally, since these buildings have such large energy usage, if you can demonstrate savings and sustainability techniques, the utility often has rebates available that is important to investigate.
When designing lighting systems for these types of structures, what design factors are being requested? Are there any technical advantages that are or need to be considered?
Alex Engelman: Cost and ease of maintenance/installation is a major driver. High-bay lighting fixtures have evolved into their own independent lighting zone with the standardization of programmable integral control sensors. This control layer can range from “dumb” analog sensors all the way to networkable, wireless mesh-type communicating sensors that are readily adjustable and reconfigurable. Controls are an important design consideration, but often installation flexibility and maintenance convenience are overlooked. Modular, plug-and-play fixture supports with integral low-ampacity busway is trending as a cost-effective means to install and power light fixtures and other various ceiling-mounted wiring devices. The goal is to simplify for the owner and bring value by consolidating functions. Centralized emergency lighting inverters echo this design approach by funneling all NFPA-required testing to a single piece of equipment.