John Yoon provides an overview of electrical and circuit protection and the different standards and best practices engineers need to know.
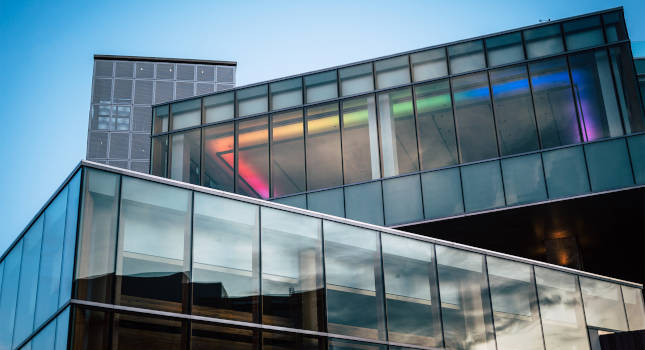
Electrical protection insights
- The electrical engineer is responsible for many different distribution systems in buildings and it is crucial to know what is needed, how much is needed and the codes and standards designed to keep people safe.
- Failing to understand can lead to serious injury or death if not properly adhered to, which makes electrical safety all the more important.
The electrical engineer is responsible for designing power distribution systems for buildings. Understanding the full circuit–protection requirements will enable the engineer to design the safest and most reliable electrical distribution systems for buildings.
Circuit protection requires an understanding of the power distribution system as well as the development of a protection scheme for circuit overloads, ground faults, and short circuits. Circuit protection can be further enhanced by implementing selective coordination design techniques.
John Yoon, lead electrical engineer at McGuire Engineers, goes over electrical circuit protection and what engineers need to know from the Jun. 28, 2023, webcast: “Electrical: Circuit Protection.” This has been edited for clarity.
John Yoon: It should be understood that the purpose of the NEC is to safeguard people and property from the hazards associated with the use of electricity. This requirement supersedes anything else. So, what we discuss here should be considered in this context, but in the same breath, the NEC is not a design manual. For example, it doesn’t make a distinction between the electrical distribution required for a hotdog stand versus a mission-critical facility. So, when designing electrical distribution systems, we have to make some type of evaluation regarding suitability of use.
Suitability of use means understanding the client’s project requirements and constraints. There’s a concept called the triple constraint that illustrates this balance between three different goals: Time, cost, and quality. The joke goes something along the lines that you can only accomplish two of these three goals. Every other solution that attempts to get all three ends up being a failed compromise. It’s a bit simplistic, but for the sake of our discussion, it gives us a starting point to evaluate project goals.
The four “Rs” of resiliency
With electrical distribution system design, our primary focus is on safety and reliability when distributing electricity. However, the top owner focus is ensuring reliability. Most don’t have to worry about their electrical distribution system if it’s going to fail unexpectedly, but what does reliability really mean? What is an acceptable level of reliability or risk for that matter for your client given their project requirements? This brings up the concept of the four “Rs” of resiliency. These are broad holistic evaluation criteria concepts that we’ll discuss each in turn.
Number one is robustness. The ability to resist an external disruptive event to define magnitude without failure. Robustness aligns with our traditional electrical design concepts for selecting devices to protect against faults, overloads, harmonics, whatever.
But in the same breath, things like fuses and circuit breakers work by interrupting the flow of electricity like turning off power. Given project constraints, how do we minimize that potential disturbance to the smallest portion of our electrical distribution system? Things like selective coordination, things along those lines. We’ll get a little bit more into that later.
Number two of the R’s of resiliency, redundancy, the ability to substitute alternate resources should the primary resource fail because of that external event. So, the primary resource for most electrical distribution systems is the local utility company. But what happens if that goes away during a storm event or some other catastrophe? The solution for redundancy can be any one of the items listed on the slide or potentially other things as well. But the question is what is appropriate for your client if it isn’t specifically required by a code or standard?
There are prescriptive redundancy requirements in codes and standards such as this excerpt from NFPA 110, but again, as illustrated by six different levels of required redundancy, one size doesn’t necessarily fit all.
Redundancy also typically adds complexity and cost. However, the application may demand it. Randy has a case study later that has excellent examples of redundancy in an electrical distribution system where the loss of power could mean loss of life.
Number three, resourcefulness, being adaptive in response to an incident. Resourcefulness is a natural extension of redundancy. How flexible is your distribution design? If something should be catastrophically damaged, what happens then? Or, for example, what about maintainability? Do I have to shut down my distribution system to perform regular maintenance? Is that going to be acceptable to the clients?
Number four, rapidity, the ability to quickly respond to prevent further degradation or to recover after an incident. While it would be nice to instantly provide an alternate source of power like a UPS for every project, but again, we usually have project constraints. Sometimes there’ll be prescriptive code requirements like this excerpt from NFPA 110. But what if there are no specific requirements within the codes or standards? What do you do then?
Again, these four broad resiliency concepts are intended to provide some basic evaluation criteria to frame the conversation. While they are not specifically part of the code, thinking in terms of the four R’s can help when there are not specific prescriptive code requirements to guide you in your project.
The importance of electrical safety and electrical codes
So, getting back to safety, reliability to most owners means maximizing uptime. But again, our primary goal from the NEC is to ensure the safety of our electrical distribution system. But when we get into very large and very large distribution designs, there are greater inherent hazards associated with those designs. So, we need to balance the owner’s goal of reliability with our own goal of safety.
Let’s get back to basics here. We talked about safety and resiliency. Let’s talk about the basic definitions. So, we typically characterize the objectionable flow of current as one of two things, overloads and faults.
Let’s talk about overloads first. In this slide, we have the NEC’s definition. The key takeaway here is that an overload is the excessive flow of current through the intended path. The only issue here is that the magnitude of current flowing through that circuit is greater than what we anticipated. It could be any number of things. It could be a seized motor pulling a locked rotor current. It could be one too many devices plugged into a branch circuit because everyone decided to bring in unit heaters under their desk. A whole bunch of different things. But again, an overload is different from a fault.
Faults, on the other hand, are where current flows through a path other than the intended circuit. For some odd reason, the National Electrical Code doesn’t formally define what a generic fault is. The only type of fault defined in Article 100 Definitions is a ground fault. A ground fault is defined as an unintentional electrically conductive connection between an ungrounded conductor of an electrical circuit and a normally non-current carrying conductor, so forth, so on.
However, a line to ground fault isn’t the only potential fault mode. There’s also the potential for having a line-to-line fault where multiple phase conductors come into contact and form an unintended conductive path.
Many things can form unintended conductive paths. It could be an electrician working on a panel and dropping a screwdriver that actually bridges a live bus. It could be frayed wiring, touching a grounded part or enclosure. It could be a number of different things.
The magnitude of a fault is dictated by the capacity of the power source and the impedance of the fault path which the current flows through. For some ground faults with relatively high impedances where whatever is causing a fault isn’t firmly fixed or vaulted into place, the low magnitude of fault current may not be enough to open an overcurrent protection device (OCPD). As such, the NEC requires ground fault protection for solidly grounded Y systems, a thousand amps and larger, greater than 150 volts to ground. But on the other end of the spectrum, arc flashes and arc faults are typically characterized by an unusually high level of fault current.
An arc flash is the uncontrolled release of energy from a fault flowing through an electrical arc plasma typically through an air gap. We’ll touch on arc energy reduction in a later slide.
To interrupt the objectionable flow of current, whether it be an overload or a fault, we use OCPDs. This slide has the definition straight out of Article 100 of the NEC. The most common devices are fuses and molded-case circuit breakers, which we will jump into next.
Fuses. Fun fact: There’s no formal definition within the NEC for what a fuse is. As such, we have to rely on a definition from another source. There are two applicable standards for fuses, UL 248 and NEMA FU 1. Let’s use the definition from NEMA. “A fuse is a protected device that opens a circuit during a specified overcurrent condition by means of a current-responsive element.”
So, reading that definition, the question is what’s an element? An element is a fusible portion of the fuse that melts during an overcurrent condition to clear the circuit. Basically, we have a sacrificial conductor that melts, maybe even vaporizes based on the magnitude of current when exposed to an overcurrent condition, and that opens the circuit to prevent damage to downstream devices.
Under normal operating conditions, that element has a reasonably low resistance, so it’s functionally no different than any other conductor within that circuit. However, in an abnormal operating condition of fault or an overload, that element becomes sacrificial. We either have to melt or vaporize the element to open a circuit. Just like any other conductor, the thermal energy that melts stuff is represented by i2t. If we have something that happens in free air with that conductor, that simple act of melting an element or releasing that energy, that in of itself could be potentially dangerous. So, as such, we have to somehow contain or dissipate that energy.
This fusible element is installed within a cartridge body, as displayed in this diagram above and is usually surrounded by sand to contain and dissipate that energy. Traditional single-element fuses are a compromise. Either short circuit or overcurrent protection characteristics are emphasized.
You can design the single element to melt very quickly and have it be very fast-acting, or you can sacrifice speed and have it be a time delay. This is a pretty significant trade-off and it’s unacceptable if you’re trying to protect loads with very high inrush currents like motors and transformers.
To address this issue, the fusing industry came up with the concept of a dual-element fuse. It’s exactly what it sounds like. You have two separate elements connected together as you can see in this diagram. One is optimized for low magnitude overcurrent conditions and the other for high magnitude fault conditions. The vast majority of fuses that you encounter in low-voltage power distribution systems will be this dual-element type.
So, based on what we’ve seen so far, you should be getting the impression that these OCPDs will react differently depending on how much current they see, whether it’s a minor overload or a major fault current on the other end of the spectrum. To be able to compare different overcurrent protection devices, you need something that’s called a time-current curve (TCC). All manufacturers have these and they’re in a similar format, so you can make easy comparisons.
Now, if we look closely at this graph, you’ll notice the scales aren’t linear. This is a log-log graph. So, our per-unit values go from 0.1 to 1 to 10 to 100 and so forth and so on. And these time-current curves, time and seconds is always on the vertical y-axis and current and amps is always on the horizontal x-axis.
The type of current curve that we have here is for a 100-A RK5 fuse. That red band that you see there represents the minimum and maximum melt times for the elements within that fuse. Everything to the left of that curve is normal operating conditions and the fuse won’t open. But once you hit that red band or go to the right of it, the fuse will open.
You can see that that red band is not thin, red-lined, or some weight to it. This is due to manufacturing tolerances. The fuse is guaranteed to open somewhere within that band, not necessarily an exact number, but somewhere in that band. You can see that if you follow the graph up to the timescale towards the 202nd mark at the top, if you cross-reference that with current, you can see that that 100-A fuse holds considerably more than what it’s rated for a period of time.
Circuit breakers and electrical safety
What about circuit breakers? The NEC definition, “A device designed to open the circuit automatically on a predetermined overcurrent without damage to itself when properly applied within its rating.”
Basically, a circuit breaker can be opened and closed against all magnitudes of current up to its short circuit rating. The UL standard that applies to most circuit breakers is UL 489, and there’s also a UL 1066 standard for low-voltage power circuit breakers that Randy may get a chance to touch on briefly in this case study.
Circuit breakers are also called inverse time devices. This means that the greater the magnitude of current is, the faster it trips. If we are looking at that time-current curve before, again, it reacts very slowly when you have low magnitudes occurring and very, very quickly when you get to the bottom.
This is the inside of a generic single-pole molded-case circuit breaker. There are two fundamental elements I want to focus on here. The bi-metal element and the magnetic element. The bi-metal is for overload protection. It consists of two strips of metal with different coefficients of thermal expansion, so when they get hotter, basically resistive heating, one strip will expand quicker than the other. It bends and triggers the circuit breaker open just like the spring on a mousetrap. The magnetic function is the short circuit protection. As a current flows in a conductor, it generates a rotating magnetic field. The more current, the greater the magnetic field. So, if you double back the conductor on itself, the opposing magnetic fields going in opposite directions will repulse each other. This forces the contacts apart and triggers the breaker to open.
This is a characteristic time-current curve for a molded-case circuit breaker. This has the same type of log-log graph as the fuse. You can see how the shape of the curve changes at about half a second at about eight to 10 times the rated current. That’s where the magnetic function of the breaker starts to take over. Above that point is mostly the thermal function of the breaker.
If you look at the bottom, you see that weird dogleg at about 0.0167 seconds. There’s a typo on the slide. That extra zero is missing. It’s 0.0167. All molded-case breakers had that characteristic dogleg. The top of it will never be more than three cycles’ worth of time, three divided by six seconds, 60 seconds, and then they often overlap between various different breaker sizes.
Traditional thermomagnetic breakers use simple mechanisms that work via heated magnetism as we described to operate. You can’t adjust them, but, for example, what if you could measure the actual true RMS current flowing through a circuit breaker and then input that data into a microprocessor-based algorithm to determine if a breaker should trip? What if you could adjust that algorithm to change the threshold where that breaker trips? You want it to trip faster? You want to trip slower? You want to give it a little bit more whatever? That gets us into the concept of solid-state trip units where you can separate the sensing and tripping functions to accommodate that flexibility. You can also accommodate a whole bunch of other different protective relaying functions. Adding this flexibility also means adding cost and complexity. However, in some applications, it’s unavoidable.
Here’s a direct comparison between a typical 100-A thermomagnetic circuit breaker and a dual-element fuse-type current curve. The fuse is the red line again. The circuit breaker is the blue again. When they’re overlaid, the difference between how each reacts to overcurrents is quite pronounced. You can see that characteristic transition between magnetic and thermal overload protection in the blue band at about half a second. That 30-cycle region. We can see in this particular case, the circuit breaker reacts considerably faster in the overload region at the top of the graph. However, if we take a look further down at the short-time region of the graph where the magnetic function starts to become dominant, there’s a pretty high uncertainty whether that circuit breaker will trip first or the fuse will trip first. Again, they’re both a hundred amps, but you can see that they react quite differently.
Again, if we go down to that three-cycle reach at that 0.067 seconds, we can see that that dogleg, which is characteristic of circuit breakers, the circuit breaker can trip anywhere within that shaded region, whereas the red band, which represents the average melt time of the fuse, is really well-defined at the bottom of that graph. So, down at that portion of the graph, I can’t tell you if a circuit breaker or fuse will open first.
Advantages and disadvantages of circuit breakers and fuses
Based on your particular application, you should understand the relative advantages and disadvantages of fuses and circuit breakers, and then you have to decide what makes the most sense for your client based on their budget and their expectation of reliability.
Here are some pros and cons starting out with fuses. For me, the biggest pro for fuses is the ease of selective coordination. Again, we don’t have that characteristic dogleg at the bottom. The biggest con for me is the inability to easily accommodate protective relaying functions like ground fault and arc energy reduction. Those types of functions are unavoidable in larger distributions. The code mandates that you have to have them.
There is one caveat in this list here. We say that fuses are current limiting. However, we should put a brief explanation to that. Fuses do not limit current for all values of all current. There’s a concept called the threshold current ratio. If the fault current is equal to or greater than that threshold current, then the fuse is current limiting. This ratio can range from anywhere from 30 times to 65 times the rated ampacity of that fuse. For very high magnitudes of fault current, they’re very effective at limiting current, but for lower magnitudes of fault current, like an RK event, they may not be particularly effective at limiting that fault current.
Here’s the same thing for circuit breakers. The biggest benefit for me here is the ability to specify solid-state trip units to tweak the shape of that time-current curve to meet my loads overcurrent protection requirements. This gives me flexibility, but in the same breath, that’s also a con in that this additional functionality adds cost and complexity to my design and I have to determine if that is appropriate for my client or if I have a requirement based on prescriptive code requirements to include it within my design.
The importance of arc flash and electrical safety
If you recall, we briefly mentioned arc flash. Arc flash mitigation is mandatory in any municipality that has adopted the 2017 NEC or a later version. The associated sections of the NEC are titled Arc Energy Reduction with the emphasis on the word energy. If you reduce the energy that’s released during an arc flash, you reduce the potential severity of injuries like burns. However, the question is how do we reduce that released energy? You can find the equation for calculating the theoretical possible incident energy in the back of NFPA 90E, the safety code. The primary variable in that equation is the distance from the arc, the time and duration of the arc, and the available short circuit current.
While we can’t necessarily control how close a person is to the arc, that first one, we can sometimes control the magnitude of available fault current by changing the characteristic impedance of the circuit, like adding a transformer, but in most cases, we can most certainly control the time duration, that last variable, by opening the circuit faster.
Arc energy reduction requirements apply to both fuses and circuit breakers. For fuses, it’s required for sizes of 1,200 amps and larger. Listed are the prescriptive methods required by code. The fuse itself can’t accomplish these functions that are listed here by itself. At this point, to accomplish these functions, we’re grafting on electronic protective relaying functions, and by doing this, we’re starting to blur the difference between fuses and circuit breakers to accommodate these code requirements.
The basic prescriptive requirements for circuit breakers and fuses more or less accomplish the same thing: trip the breaker or open the fuse sooner. If we can trip a circuit breaker faster and somehow reduce the available fault current, that should reduce the amount of energy that’s released. I don’t know if you caught it in the last slide, but you can see at the bottom of this slide there is an approved equivalent means method. That last item is a catch-all to allow it to be addressed by other emerging technologies, which would accomplish more or less the same thing as methods that are listed.