Engineering mixed-use buildings is a fine art—specifiers must combine multiple engineered systems for several business and residence types into one structure. Codes and standards from NFPA to IECC challenge engineers.
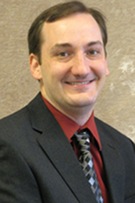
Participants:
Robbie Chung, PE, LEED AP, Senior associate, Environmental Systems Design Inc., Chicago
Raymond Holdener, PE, Senior associate, Dewberry, Fairfax, Va.
Andrew Lasse, PE, LEED AP, Associate principal/senior mechanical engineer, Interface Engineering, Portland, Ore.
Gary Pomerantz, PE, LEED AP, Executive vice president, building systems, WSP, New York City
John Sauer, PE, LEED AP, Senior director, BSA LifeStructures, Indianapolis
LeJay Slocum, Assistant director, Atlanta regional office, Aon Fire Protection Engineering Corp., Suwanee, Ga.
CSE: How have changing HVAC, fire protection, life safety, and/or electrical codes and standards affected your work on mixed-use buildings?
Slocum: The past decade has seen significant changes with regard to the requirements for design, construction, and monitoring of smoke control systems. Many mixed-use buildings incorporate some aspect of smoke control, be it an atrium exhaust system, a pressure sandwich system for residential floor, or simply stair well pressurization. These changes impact every aspect of a project’s engineering, including the fire protection engineering to prepare the smoke control rational analysis, the design of the HVAC ducting to exhaust smoke or supply makeup air, the emergency power systems, and the fire alarm or BAS system, which either individually or in tandem control and monitor the smoke control systems. Code changes impacting smoke control systems have broad impact on the design of mixed-use buildings and require the greatest level of coordination among design teams to successfully address all aspects of the system.
Chung: The recent implementation of the 2012 International Energy Conservation Code has been a learning experience for all parties. More stringent requirements have created challenges for architects and engineers, including design strategies on the building exterior façade, lighting design needs to meet lighting power density requirements, and proper implementation of daylighting control, just to name a few. However, all issues can be resolved with careful due diligence and early identification of potential concerns.
Pomerantz: Life safety codes tend to produce the most challenges in the design of a project. In general, codes address more simple buildings—single-use buildings. Each building type has its own specific code requirements associated with it. When designing a mixed-use building, which code is applicable? Does the designer use the most stringent of the codes that governs each of the constituents over the whole project? It is unclear and it is best to have discussion with the relevant authority having jurisdiction (AHJ) early in the design. And it is equally important to meet with them as the design develops. Items of concern often include egress stairs and elevators that serve multiple use groups, fire alarm systems, and the sequences of operation in user areas that are outside the area that is in alarm.
Holdener: Recent codes have changed with respect to required smoke-rated shafts—this has led to reduction in the number of smoke dampers and related smoke detectors, damper actuators, wiring, or access doors, often in areas of the project where spatial constraints and finishes impacted the design and installation of these dampers. There appears to be more emphasis on enforcement of annual fire damper inspection, testing, and documentation. Several fire damper manufacturers are advocating motorized fire dampers monitored by the BAS. This allows the fire dampers to be periodically cycle tested with automatic documentation via the BAS.
CSE: Which code or standard proves to be most challenging in this type of work?
Lasse: One of the keys is to work very closely with the local AHJ. In some areas, mixed-use buildings have been and continue to be constructed at a rapid pace, and local AHJs are responding by developing firm interpretations of the building code and specialty codes. Oftentimes there are local code guides, directives, and/or supplemental requirements for systems like combined dryer exhaust systems, generators, garage exhaust, and fire life safety systems. Checking in with the AHJ early on in design and having a complete understanding of the additional constraints is paramount.
Slocum: The building and fire codes present the greatest challenge when working on fully integrated mixed-use projects. While the code intent to apply the most restrictive requirements to all occupancies is clear, variation in enforcement of requirements, misunderstandings among team members regarding what is the most stringent requirement, and the extent to which the requirements must be applied are all challenges for this type or project. In addition to the general requirements of the building code, many municipalities and states also adopt the NFPA 101: Life Safety Code. Mixed-use projects that are subject to both the building code and NFPA 101 are often more challenging, as the two codes may have conflicting or different requirements necessitating the engineer thoroughly assess for each code-driven design decision to ensure compliance with the most stringent requirements.
Holdener: Codes that deal with providing and maintaining fire-rated assemblies and enclosures of ductwork are still somewhat challenging, especially in high-rise residential projects with multiple types of vertical duct systems such as outside air, toilet exhaust, residential kitchen exhaust, clothes dryer vents, and commercial kitchen exhausts where retail spaces are located below the residential portions of the building. Fire-rated architectural enclosures, fire-rated insulation, and a combination of both are commonly used to achieve code compliance. We see the zero-clearance fire-rated insulation products being used to help reduce the overall size of the rated ductwork assembly because physical dimensions are so critical in these types of projects. Ventilation codes in combination with UL fire and smoke rated doors on residential units have created challenges with the outside air supply systems. Today’s residential doors do not leak as much as older designs. U.S. Green Building Council LEED pressure differential requirements between residential units also require tighter, lower leakage construction. Design engineers cannot rely on the old method of supplying outside air via the corridors as the only means of injecting outside air into the residential buildings.