There are specific ventilation, cooling and energy efficiency considerations in manufacturing facilities due to their unique scale and uses.
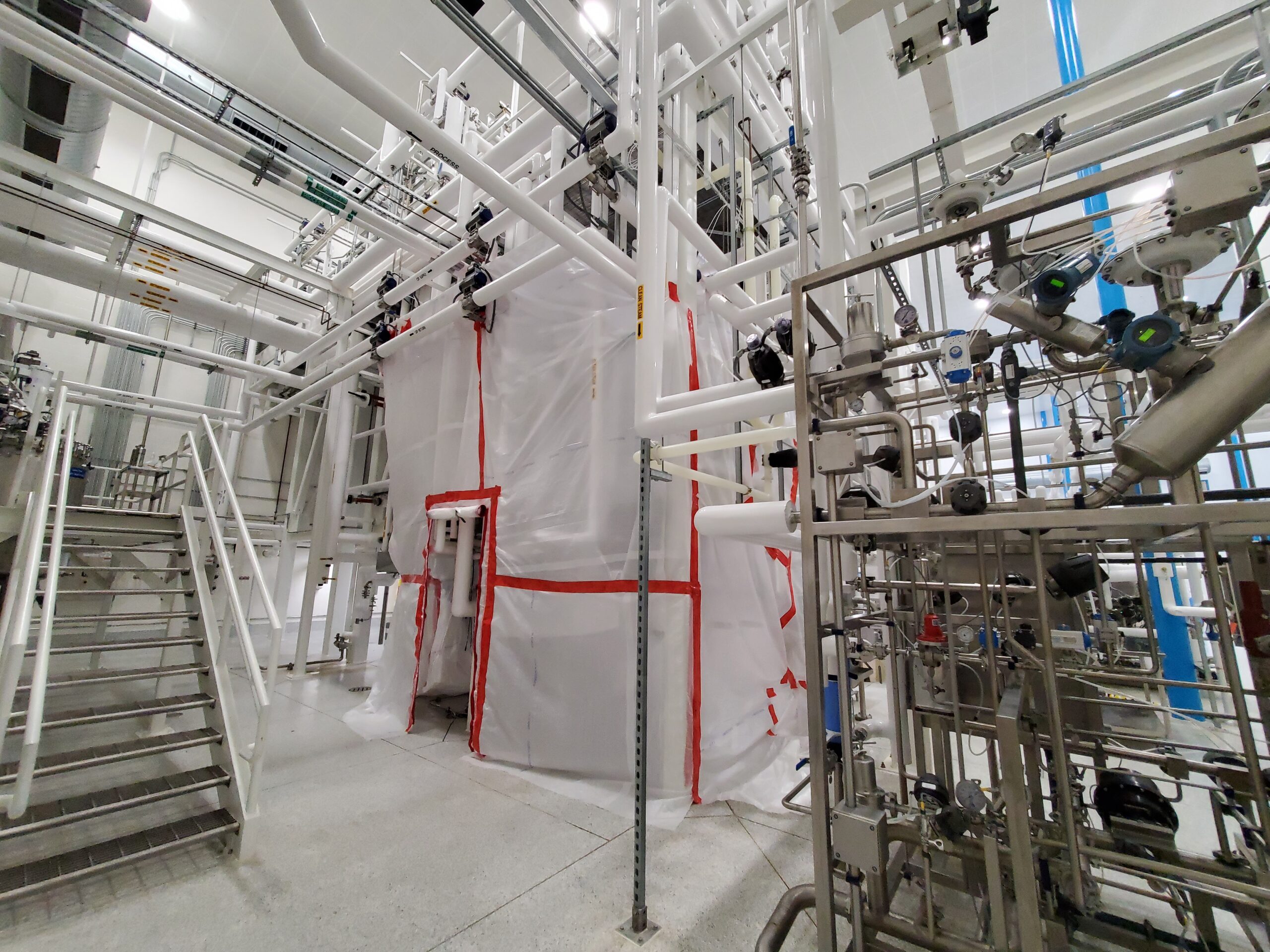
Learning objectives:
- Identify how codes and standards, like ASHRAE, impact industrial facility design.
- Understand the unique needs and wants of manufacturing owners and operators for mechanical systems.
- Learn how automation and controls are changing the way that these facilities operate.
HVAC insights:
- Increased control of mechanical systems can be helpful in many parts of industrial facility design.
- Specific cooling designs may need to be considered depending on the products or processes within these facilities.
Respondents:
- Jason R. Gerke, PE, LEED AP BD+C, BCxP, Senior Design Phase Manage, JP Cullen, Milwaukee
- Jarron Gass, PE, CFPS, Fire Protection Discipline Leader, CDM Smith, Pittsburgh
- Matt Merli, PE, Principal / Client Services Director, Fitzemeyer & Tocci Associates, Inc., Woburn, Mass.
What unique cooling systems have you specified into such projects? Describe a difficult climate in which you designed an HVAC system for an industrial or manufacturing facility.
Matt Merli: Cooling requirements have wide ranges in manufacturing. There are typically enhanced ventilation needs (dust collectors, ovens, furnaces, etc.) and depending on the products and lines, there may be a wide range of temperature and humidity requirements. It’s important to understand exactly what temperature/humidity requirements are for the products being developed in the space, as there may be an opportunity to save a lot of time/money if ‘full cooling’ is not required. Additionally, there may be portions of a line that require tight temperature/humidity requirements, where other aspects don’t. It’s worth looking to see if that can be isolated in a separate space to have a much smaller volume of temperature and humidity control, which saves enormous upfront and long-term costs.
How have you worked with HVAC system or equipment design to increase a building’s energy efficiency?
Jason R. Gerke: One important step in HVAC design includes evaluation of airflow in large spaces, or ones with unique geometry. Performing an airflow study utilizing computational fluid dynamics (CFD) modeling has proven to be a great tool to not only prove out the design concept and refine air distribution, but also ensure the systems are right-sized and do not include too much airflow. The CFD process will allow the design team to ensure air is getting to where it is needed, not washing areas with too much air, and ensuring critical areas of a space receive appropriate airflow. This process will allow the design team to design for the actual load of the space instead of oversizing 10% or more “just to be safe.”
Describe an industrial or manufacturing project in which process piping was required. What were the challenges and solutions?
Jason R. Gerke: Process piping can quickly add cost to the construction phase of a project. The design team must ensure utility needs are carefully analyzed, documented and signed off by the owner or process engineers. This step will ensure the system is properly sized, not only for day one, but for future process expansions, future building expansions or potential increases in demand for the current processes. Beyond the sizing of the process piping systems, materials of construction need to be evaluated early in the project. The gas or liquid systems may require specific pipe materials that have a wide range of costs to balance against the performance of the piping systems. Finally, the routing of process piping systems needs to be carefully evaluated in the design phase to ensure the most efficient path is selected. Many times, these systems are banks of piping, so saving one foot in actual distribution distance could be multiplied by the many pipes in the gallery.
What best practices should be followed to ensure an efficient HVAC system is designed for this kind of building?
Jason R. Gerke: There are many options when selecting an HVAC system for an industrial building. These options range from heat/vent to cooling to dehumidification. It is important that the design team works with the owner to establish their minimum project requirements at the beginning of the project. This step to establish written requirements will allow the entire project team to use that information in later decisions to ensure the requirements are being met and no extraneous systems or equipment are being included.
Matt Merli: Deciding which type of energy recovery is important to evaluate during the design process. These buildings are unique facilities, so there’s not one common solution to all of these types of buildings. Understanding if there are hazardous exhaust systems or outdoor air requirements to help facilitate an efficient and safe energy recovery approach is important.
What are some of the challenges or issues when designing for water use in such facilities?
Jason R. Gerke: Depending on the specific manufacturing processes, water demands can be extreme in an industrial facility. This demand can stress existing infrastructure in a large industrial complex, as well as municipal systems serving the facility. The flow rates must be established early in the design phase for the project team, municipal or regional authorities to contribute to a solution to meet the water consumption needs. It is important that the demand values presented by owners and process engineers are challenged to ensure the values provided are real and not gross overestimations. It is equally important that the design team evaluates opportunities for water recycling and reuse as well as storage to reduce instantaneous demand on infrastructure.
Matt Merli: Working with the local utility, particularly on the wastewater side of things, is important. Some of these facilities have hazardous, or at least atypical, waste to consider and vet. There typically are two or more sanitary waste systems from these facilities, such as normal sanitary and a process, acid or other waste system.
What level of performance are you being asked to achieve, such as WELL Building Standards, U.S. Green Building Council LEED certification, net zero energy, Passive House or other guidelines? Describe a project and its goals, identifying the geographic location of the building.
Jarron Gass: Architects and engineers are increasingly expected to meet high-performance standards that promote sustainability, energy efficiency, and occupant health. Common benchmarks include LEED, which focuses on green building strategies; the WELL Building Standard, which emphasizes wellness through air, light and comfort; Net Zero Energy, where buildings produce as much energy as they use; and Passive House, which requires ultra-low energy consumption through airtight, insulated design. The Living Building Challenge is one of the most rigorous, demanding net positive energy, water and materials. These guidelines reflect a growing push for buildings that are not only efficient but also healthy and environmentally regenerative.
What types of sustainable features or concerns might you encounter for these buildings that you wouldn’t on other projects?
Jason R. Gerke: An important quality review task on highly sustainable projects is to review the HVAC system of operations. In addition to the HVAC sequences, other control systems in the building, whether connected or standalone, must be evaluated for the level of complexity. This complexity includes both operational and initial setup. It is easy to design and specify a perfect building with really sophisticated controls, but it is another situation to actually construct, commission and operate the building. The design team often wants to add several complexities to a project that are well-intended but may make the construction process and facility operations very complicated.
Matt Merli: Energy recovery for these facilities is a common design discussion for the architecture/engineering team. These buildings may have large outdoor air requirements and are physically quite large as well. This leads to an enormous amount of air, where energy recovery is not only a code requirement, but also has payback opportunities.
Describe energy storage systems at an industrial or manufacturing facility. What have you designed recently?
Jason R. Gerke: Ice storage continues to be a very useful solution when designing chilled water systems for an industrial building that requires chilled water for the process systems. Ice tanks can be used to reduce chiller runtime during peak hours and installed chiller capacity to meet instantaneous process loads. These types of buildings provide a great opportunity for synergies between comfort cooling and process systems to achieve a lower first cost, energy-efficient operation and long-term flexibility in system capacity and plant expansion.