Randall Ehret outlines an example of electrical and circuit protection using a hospital as an example.
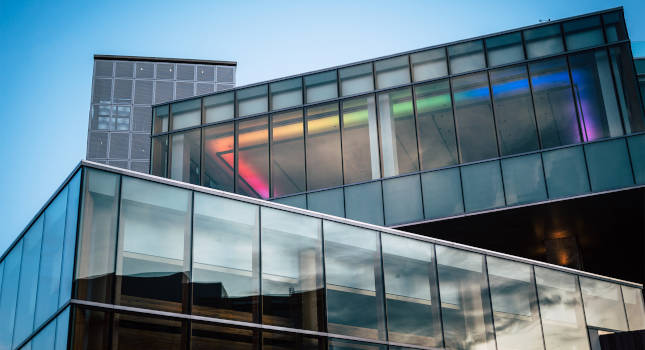
Electrical protection insights
- The electrical engineer is responsible for many different distribution systems in buildings and it is crucial to know what is needed, how much is needed and the codes and standards designed to keep people safe.
- Failing to understand can lead to serious injury or death if not properly adhered to, which makes electrical safety all the more important.
Randall Ehret, technical director for ESD, outlines a case study example using a hospital project he worked on from the Jun. 28, 2023, webcast: “Electrical: Circuit Protection.” This has been edited for clarity.
Randall Ehret: The example is going to be a 300,000 square foot suburban hospital, and our learning objectives are here on the screen. We’re going to present portions of the one-line diagram for a typical hospital. We’re going to provide insights into the concepts that were used to develop this one-line diagram. We’re going to show the different circuit protective techniques that were employed and apply them to this project, and then review possible approaches to mitigating budget constraints and value engineering impacts.
With that said, let’s provide a little context for the case study. This particular project is a hospital that is part of the larger campus. It’s a replacement hospital. There’s an existing central energy plant as part of this facility. At the beginning of this project, that plant had two small 480-volt generators and a large co-generation plant. The new hospital is going to be located on a site 300 feet away from the central energy plant. Those are the big picture basics that were provided to us at the start of this project.
Budget drives every project. What we have to do is look at how we can apply all the principles that John just talked about to maximize reliability and maintainability within the available resources.
We’ll start with the central energy plant. The central energy plant did not have a distributed normal source of power. It was distributing emergency power only. The utility service on the site was notoriously unreliable. Every time a storm potential was forecast, a hospital would come in and start a cogeneration plant and bring that online to mitigate any chances of an outage within the hospital.
To help with that, we negotiated a second utility feed from an independent substation from the utility, and we accepted service at 12 kV at a new piece of switchgear that we put in, located inside the plant. The existing campus had the switchgear located at an exterior location, and they owned all their distribution on campus. Unfortunately, that switchgear was located at the lowest point on campus and was subject to flooding, and they had issues there as well. Looking at that reliability and where to locate things becomes part of that question and part of that equation.
What we did was bring two utility sources in and tied them together with an automatic throwover switch so that if either utility source failed, the other one would pick up 100% of the load.
To go along with that, we brought the cogeneration feeder back into the same piece of gear and acted as a third source of power in case of failure. We also ran multiple normal feeds out of this gear from the central energy plant at 12 kV across the campus to the new hospital.
From there, we’re going to dig into the normal power at the hospital itself. So, this is an example of one of the unit substations that we provided for the hospital. As we previously stated, we brought multiple 12 kV feeds across; one of those feeds comes into this unit substation. Originally, we designed this as a double-ended switchboard or double-ended unit substation with two 12 kV feeds coming in and a tiebreaker in between.
The reason we looked at this was, again, just adding to that reliability. With these feeds coming a long distance underground, we wanted to make sure that there was some backup if one of those feeders failed. It could have been cut during construction. We’ve had a lot of that happen on this campus and other campuses. It could just be a bad feeder.
Each patient care floor had multiple feeders coming out of different unit substations to that floor. So, I had one feeder coming out of this unit substation that fed part of a patient floor, but I had another feeder coming out of a separate unit substation feeding the other half of that floor. That way, they would never lose normal power to an entire patient care area due to one failure.
It is also worth noting that for health care facilities, the code requires two levels of ground fault protection. John talked about ground fault protection earlier. You will see that there’s a ground fault protective device on the main here at this unit sub, but also on every feeder going out of it. And that’s, again, just to further segregate the opportunity for one failure to take out more than one portion of the system.
We also utilize draw-out circuit breakers. So, again, John talked about the different types of breakers that are available. We chose draw-out circuit breakers. This allows for a little bit more ease of maintenance and a slightly more robust breaker. What they do is, when they come in to do their annual maintenance on the breakers, rather than trying to do it in the unit substation, they swap it out with a replacement breaker, take that breaker off to a test station, and do all their testing. Then they use it to test the next breaker in the line. This helps keep things up and running and makes it a little bit easier for them to get in there and facilitate that annual maintenance that’s required on a breaker.
The other thing you might notice as you look at this one-line diagram is the size of all the feeders. We’ve tried to keep those to 800 amps or less. It’s a more expensive way of doing the design, but what it allows is for no one feeder to pick up a large percentage of the hospital’s load. Again, a feeder failure impacts a smaller area.
The other thing we will note here is the LSIG on these draw-out power circuit breakers is used to provide the protective relaying on the curves that John was showing, and we’ll give an example of that in a little bit to make sure that we’ve got selective coordination. The code does not require selective coordination on the normal power system, but for a facility such as a hospital, it’s important to try to achieve that. Again, we want reliability for patient care for both the safety of the staff and the patients.
The next component of the electrical distribution system was the emergency power system. This is going to be located in the central plant. We put in new generators. The 480-volt generators we didn’t feel were adequately sized for the new hospital, but also we wanted to go to 12 kV to kind of match what we were doing with the normal power distribution. Our chillers were at 12 kV, and now we can extend across to our hospital without any real concerns about voltage drop.
We brought those generators and connected them to a piece of paralleling gear. A paralleling gear basically allows the first generator that comes up to speed to come online and pick up all the loads on the gear. In this case, however, we selectively decided which pieces of which load would be picked up first. Code requires that all life safety and critical power loads within a hospital be picked up in 10 seconds or less. That first generator was sized to be able to accommodate a hundred percent of the life safety and critical loads. The second generator would then come up to speed, parallel sync with the first generator, and come online, and then we start to pick up all the equipment loads.
Code also requires that, again from a circuit protective standpoint, feeders for life safety and critical loads be separated from equipment loads and other feeders within the building. So, you can see that separate feeders were extended from this paralleling gear to the hospital for life safety. There were multiple ones that were extended across for critical loads and multiple that were extended across for equipment.
When you start paralleling generators, you’ve got to look closely at the grounding to protect the generators and the rest of the system. So, there are a lot of different ways that can be accomplished. In this instance, we elected to go with a low impedance ground system at each generator, and that will help mitigate issues related to ground faults. The drawback to it is it can cause damage to the generator if that ground fault is actually in the windings of the generator.
Once we brought that power across to the hospital, this is an example of the critical power unit substation. So, we had a separate unit sub for life safety, we had multiple separate unit subs for critical loads, and we had multiple unit subs for equipment branches.
We elected to go with a cascading transfer switch design in this instance. What that basically does is I’ve got a normal feed from one unit sub coming into the first transfer switch, a second normal feed from a second unit sub coming into that first transfer switch. Either one of those fails, it transfers to the other side. So, we’ve got two sources of normal power. That feeds into the second transfer switch, which is then fed from the emergency power source so that if both normal sources fail, the emergency source then picks up and feeds all the critical loads in the hospital. Again, each patient floor was fed from at least two-unit substations so that we never had a loss of all the critical power on a floor due to the failure of one substation or one feeder.
Additionally, it’s important to note that, for the life safety, critical, and equipment branches, the code only requires a single level of ground fault protection. So, in fact, it does not allow for the second level of ground fault protection. We don’t use that in this particular instance.
This is an example of the time current curves for this project. Code only requires that the system coordinate down to 0.1 seconds for health care. That is very specific to health care. There is no such allowance for emergency systems and other types of buildings. So, you can see John was talking about this funny-looking L down here at the bottom. You can see the overlap there. So, in the instantaneous range, you’ve got a little less selectivity than you have in other areas, but as you can see, the breakers never overlap until they get into that instantaneous range. So, the smallest feeder size breaker will always trip before the largest.
One thing that you might consider when you get into projects such as this, these are all LSI breakers both at the gear and at the distribution panel. Sometimes you might want to use just an LS breaker rather than an LSI breaker. Those sometimes will coordinate better than the LSIs. There’s a lot of software out there that you can use to develop these time current curves. That’s the way that most of these studies are done.
One thing that I do recommend is during the early stages as you’re putting together your one-line and trying to make sure that you can accommodate all the code requirements, there are some really nice charts that all the manufacturers publish that show at different fault levels what breakers will coordinate. And rather than just using rules of thumb, this will allow you to go in and kind of get a good feel early on whether the system you’re designing will selectively coordinate in the end.
The last piece I wanted to talk about was a typical IT for an uninterruptible power supply (UPS). IT in a hospital is critical to patient care. All the electronic medical records are kept on the internet, and there’s very little charting that’s done anymore. So, everything has to be available. We usually put in a dedicated UPS for all the IT equipment.
In this particular hospital, we also put in a dedicated imaging UPS because if you lose power during a procedure, you’ve got to start that procedure over again, and this allowed for them to continue on through if they so choose. The time current curve you see here is an example of a time current curve as it relates to a transformer and making sure that we don’t damage the transformer due to a fault condition.