Kevin Anderson, senior technical training specialist at Grundfos Pumps Corp. in Olathe, Kan. tackled unanswered questions from the Jan. 19, 2016 webcast on optimizing variable flow pumping control modes for energy savings.
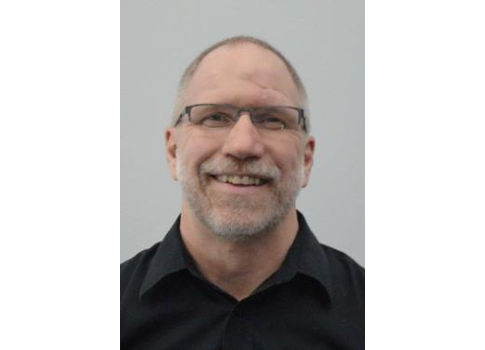
Kevin Anderson, senior technical training specialist at Grundfos Pumps Corp. in Olathe, Kan. tackled unanswered questions from the Jan. 19, 2016 webcast on optimizing variable flow pumping control modes for energy savings.
Q: What are the pros and cons of an electrically commutated motor (ECM)?
Kevin Anderson: Pros: an ECM is very efficient, especially across a wider motor load, and higher torque. Con: the purchase price is higher than that of a conventional motor.
Q: If PMGs have higher efficiency, why is it not as widely used as the induction motor (PMGs are not in common use in U.S.).
Anderson: Purchase price.
Q: Everything you’ve mentioned so far refers to ECMs. How would this be different with an induction motor?
Anderson: From a variable speed pump perspective, the main difference between an ECM controlled motor and an induction motor is efficiency. Both can be controlled the same way, but the power savings will be much higher with the ECM motor because the electrical efficiency is higher, especially at partial load—where it counts—on a variable speed pump.
Q: Somehow, I missed how the efficiencies for the zones were calculated based on the 81% motor efficiency.
Anderson: The efficiencies for the pumps were based on where the pump was operating on its efficiency curve. The efficiency for the motor was based on the efficiency of an average wet rotor motor.
Q: Why are people still using induction motors?
Anderson: The most common reason is the initial cost of an induction motor is cheaper.
Q: I question your savings. At constant speed, pump efficiency at a given point on the pump curve is unchanged. If the original motor is 81%, then at constant speed, maximum savings would be 1/0.81 = 1.23 or 23%.
Anderson: The reason for the large energy savings is due to the lower power usage overall of a permanent magnet motor, not just the motor efficiencies themselves. Also, the permanent magnet pump has a very similar flow and head profile, but has a higher hydraulic efficiency. The permanent magnet motor used for this example has a maximum load of 610 W (0.61/1.29 = 0.47). This means only 47% of the total energy of the induction motor is used by the permanent magnet motor for a total savings of 53%.
Q: What is the job of the primary pumps compared to the secondary pumps? What is the use of the green line (bypass pipe) in your diagram?
Anderson: To achieve proper variable volume pumping, we must have two-way valves, primary and secondary pumps, and a common pipe. If we leave three-way valves in the system, we will still have constant flow. The green line is the common pipe. A common pipe hydraulically "decouples" the primary part of the system (the boilers or chillers) from the secondary portion (distribution and loads) of the system. A common pipe allows independent operation of the primary and secondary pumps. Because the primary pump is only responsible for flow through the boiler and a small amount of piping, the pressure drop is relatively small, so the pump horsepower is usually small. The secondary pumps have to do more work. They have to meet maximum demand and have much more piping head loss to overcome. Fortunately, demand varies, so when demand is less, flow is less and friction loss is less—saving operating costs.
Q: It would have been really nice if you would have shown what the flow reduction was relative to, or maybe put a scale on the graphs.
Anderson: I’m sorry. I should have explained more thoroughly. The changing flow was due to zone valves opening and closing in a hydronic heating loop.
Q: By proportional differential pressure control, do you mean the pressure transmitter is out in the system as opposed to across the pump?
Anderson: The proportional differential pressure can be accomplished using differential pressure sensors either out in the system or across the pump. However, across the system is the most accurate way to design the system. A remote mounted sensor can result in optimized energy savings because "actual" head loss is accounted for versus a calculated or estimated head loss.
Q: How does the reduction in power cost compare with capital cost investment i.e. internal rate of return?
Anderson: Depending on the energy costs and the load profile for the application, we have seen as low as 18 months or even less payback on many of these applications.
Q: From your technical experience, which control mode do you think is better and why?
Anderson: I have to give the standard answer of "that depends." If it is a closed loop heating system as described in this webcast, the auto-adaptive control is best more than 85% of the time. However, high head losses at low flow, as in a coil with a high head loss close to the pump discharge, then constant differential pressure or a medium-to-high proportional differential pressure may be required.
Q: Why not try to design your example system using only primary pumps all of the time? Will that ultimately save even more money?
Anderson: Often, using single-loop systems is much less efficient for pump or boiler energy use. In a single-loop system, the pump must be sized to overcome the full head and flow of the entire system. This can cause a very large pump to run near shutoff a majority of the time depending on the load profile. In most cases, it is more energy efficient to operate smaller pumps at lower flows and heads, then adding additional pumps as needed to achieve higher flows and heads. We have a prerecorded webcast titled "Efficient Pump Selection" on our training website that gets into the efficient staging of pumps based on load profile.
Q: Does locating the DP sensor at the most remote load provide the same energy savings as proportional differential pressure control?
Anderson: Proportional differential pressure control can be done with a remote sensor across the critical circuit, or it can be done with differential pressure sensors across the pump. It depends on having a pump and motor controls capable of operating in a proportional differential pressure control mode (many of the pumps capable or operating in this control mode can be set up with remote or across the pump sensors). Across the system is often the most accurate. However, it can also be more difficult to install the remote sensor, especially if the location of that sensor is not properly documented.
Q: What is the largest motor size available with the ECM feature?
Anderson: Currently, the wet-rotor ECM style pump as in this webcast is 3 hp.
Q: What control points in the system would you use as feedback to implement the DP setpoint reset with a proportional DP control?
Anderson: For the setpoint reset, you could use either a pump with integrated differential pressure sensors, flow meters, and integrated adaptive software to adjust to system changes. It could also be done with external differential pressure sensors, external flow meters, a control capable of operating in a proportional differential pressure mode, and software that can monitor system changes. After the proportional differential pressure has been set, the software would monitor when a higher flow and lower head has been achieved by the pump due to system changes. Then the software would need to be configured to adjust the proportional differential setting to meet this new setting.
Q: I’ve heard that selecting a pump to the "right" of the best efficiency point is best for variable speed pumping applications because you’re almost always operating at partial speed. What would be the best way to accomplish this?
Anderson: The best way to do this is to do a full load profile for the system to determine where the pump will operate the majority of the time. Then select a pump and operating mode that will operate in the higher efficiency rates most of the time. We have a free prerecorded webcast titled "Efficient Pump Selection" on the Grundfos Technical Institute training website that goes in to detail on this concept.
Q: How applicable is the auto reset for a 100 zone system, for example?
Anderson: Multiple zone systems are the best opportunity for energy savings with auto reset. However, 100 zones could prove difficult to monitor and control. If it could be done with an integrated solution, that would be the best.
Q: ECM motors are currently only small horsepower, correct? Up to what size?
Anderson: Correct. Most pump manufacturers today offering ECM technology to the HVAC market that goes up to 2 to 3 hp, but there are a few that can offer up to the 5 to 7.5 hp range. The available sizes will increase with time. In the industrial market, ECM motors have been produced in sizes up to 200 hp.
Q: What is the cost of an ECM motor compared to a standard motor?
Anderson: Smaller ones are maybe twice the price (fractional horsepower); more as they get larger. Depending on the electrical costs, control mode, and load profile for the system, the payback can be less than a year up to a few years.
Q: If I have a multi-family building with 200 TRVs, where’s the best place to put a DP sensor to determine the best setpoint for the VFD controls?
Anderson: Across the system on the critical circuit (the zone in the system with the highest head loss) is often the most accurate. However, it can also be more difficult to install the remote sensor, especially if the location of that sensor is not properly documented. In many cases, it works very well to do differential pressure across the pumps. We would just have to be sure that the setting is high enough to overcome the differential pressure across the circuit with the highest head loss.
Q: What pump efficiency did you assume for your calculations?
Anderson: For the induction motor and pump, we listed both the pump and motor efficiencies. The ECM pump and motor had a higher pump efficiency as well as motor efficiency, but I only mentioned the overall pump and motor efficiency. I could have stated that more clearly in the webcast.
Q: Is the VFD be provided with the pump, or we can use any kind of VFD?
Anderson: With the ECM pumps the drive and motor are sized exactly for that specific pump. With standard pump motors, many different motors and drives could be used. We will actually have a webcast on that topic later this year.
Q: For a domestic water system, how does energy savings compare: ECM small pump with ECM large pump both with on/off control, versus single variable speed pump with and without a compression/expansion tank?
Anderson: It depends on the flow profile and how the pump is controlled. For small domestic pump applications, the most efficient pump is off. If you have a large enough bladder tank, the larger pump may be off enough to actually use less total energy than one or two variable speed controlled pumps. But sometimes comfort is compromised. An on/off pump will have a start pressure and a stop pressure where a variable speed pump will have a constant pressure. In the domestic pump market today, there are many variable speed domestic water pumps that do not shut down effectively when there is low or no flow, which results in additional energy costs.
Q: A comment, not a question: I was once in a discussion with an engineer who did not understand that this logic does not automatically apply to open systems with a high fraction of static head versus total head. The system was water pumping in a municipal water system. You mentioned that your examples are all closed systems so I am not pointing out an error, just a limit on the applicability of the savings calculations. Thanks!
Anderson: Very true. We have a free prerecorded webcast titled "Efficient Pump Selection" on the Grundfos Technical Institute training website that goes in to detail on this.
Q: Can more energy be saved using hot water reset?
Anderson: Yes, when done properly, anytime you can modulate flow, temperature, reduce boiler output, or reduce head. All of these options can reduce additional energy use.
Q: Standard induction motor has a slip, so it runs at a speed lower than synchronous speed. Does an ECM motor run at synchronous speed?
Anderson: Yes, exactly. That is an additional advantage of the ECM motor. Also, with many ECM motors, they can be run at higher speeds than induction motors. There are some that run faster than 10,000 RPM. Also, with a soft-start capability, there is no worry of having too many starts per hour.