Dedicated outdoor air systems enhance humidity control, reduce energy use, simplify ventilation design and improve efficiency in building ventilation systems
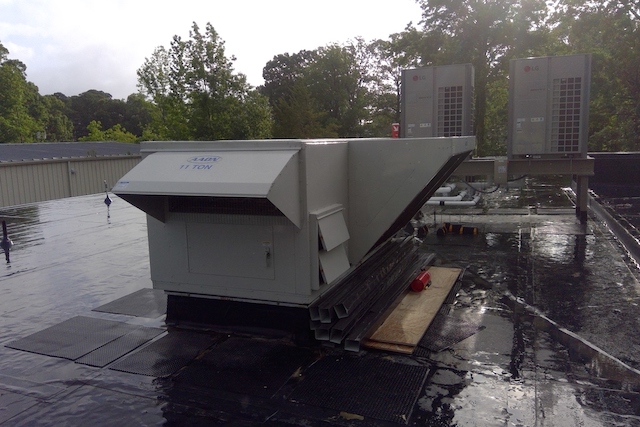
DOAS insights
- DOAS improve humidity control and reduce energy consumption by decoupling ventilation from other heating and cooling systems.
- Distributing ventilation air directly to spaces with DOAS can enhance efficiency and reduce required airflow.
Dedicated outdoor air systems (DOAS) have become common design considerations for the supply of ventilation, or outdoor air, to building spaces. As the name states, DOAS, provides dedicated outdoor ventilation air without real consideration of meeting the space cooling or heating loads. DOAS precondition the air, which relieves other space conditioning equipment of much of the latent load.
Why specify a DOAS?
The ASHRAE Design Guide for Dedicated Outdoor Air Systems states the following reasons for using DOAS:
-
Improving humidity control.
-
Reducing energy use.
-
Desire to simplify ventilation design and control.
-
Desire to use heating and cooling equipment that doesn’t provide ventilation and/or dehumidification.
-
Reducing installation cost.
Consider the first point. DOAS dehumidification is not just a byproduct of the cooling coil process, it is the primary function. The second point is accomplished by only conditioning the desired amount of ventilation air and using reclaimed condenser heat, in this case with direct expansion (DX) cooling, in lieu of other heating means that have an associated cost. The third reason considers that the DOAS is a separate system from the space cooling and heating systems, which simplifies calculations for multizone systems that can be controlled separately from the space conditioning system equipment.

Therefore, the ventilation is “decoupled” from the heating and cooling systems, and operation of one does not affect operation of the other. The fourth point is that, typically, DOAS systems use low-pressure ductwork and are only sized for outdoor air requirements. This, along with other cost benefits, explains the fifth reason.
Ventilation air distribution in DOAS
An important consideration in DOAS design is how to distribute the ventilation air in the space. Two methods are commonly used. In the first method, the DOAS preconditioned air ventilation air can be mixed with return air from the zone-level heating, ventilation and air conditioning (HVAC) system. The supply air ductwork and diffusers are then utilized to distribute both the ventilation air and air for conditioning the spaces. This eliminates the need for extra diffusers and ductwork in the space, may be less costly and may make it easier to design on a drawing. Codes do require the ventilation air to be supplied continuously, so this method needs the supply fan(s) to operate continuously while the space is occupied. Zone air distribution effectiveness (Ez) must be accounted for when utilizing this method and is discussed in more detail below.

A second method to distribute the ventilation air is to deliver the DOAS air directly to the space utilizing traditional diffusers and grilles. Both methods are common, but this method is used especially with ductless system types, such as variable refrigerant flow (VRF) cassettes and chilled beams. An advantage of the second method is that if there is an operational problem with either the DOAS or space conditioning system, it can be identified without being masked or compensated for by the other system. Another benefit comes from the possible reduced amount of required air to a space.
Most ventilation codes include an Ez for the required outside air calculations. In many traditional systems, which are responsible for providing both ventilation and space conditioning, the outside air is mixed with the return air and conditioned before being supplied to the space. When this air is designed to be supplied from a ceiling diffuser that is 15 °F warmer than the space temperature, and the return air is via the ceiling, the Ez value is 0.8. This results in a 20% increase in the required outdoor airflow provided to the space. This must also be applied to DOAS if the air from the DOAS is mixed with return air from the space and then conditioned (heated) to satisfy the heating load in the space. When ducted in this manner, the required ventilation air from the DOAS to the return air stream is effectively increased 20%.
However, if the DOAS air is supplied directly to the space at the ceiling at a temperature just cooler than space temperature, the Ez effectiveness is 1.0 and no increase in required ventilation air is needed. The extra 20% can add up across a building, and can lead to increased DOAS equipment and energy costs. Usually, the DOAS air that ducts to grilles in the spaces are easier to balance. An additional benefit of DOAS ducted directly to spaces is that the supply fans used for space conditioning do not have to operate continuously to maintain code required ventilation. They can cycle off in a deadband condition when not required for space cooling or heating. On the other hand, supplying DOAS air directly to the space does require the costs of grilles, their installation and any additional ductwork.

Note the nominal capacity of a DX cooling coil, such as what you’d find in a zone-level packaged or split system, is listed in product catalogs at Air Conditioning Heating and Refrigeration Institute (AHRI) Standard Rating Conditions. The engineer is advised to account for different entering air conditions when DOAS are used in conjunction with the space cooling and heating equipment. Capacities of the space conditioning equipment and other parameters differ from the nominal AHRI published conditions for the space equipment based on entering air condition. Nominal capacity values, or capacities listed at AHRI conditions, do not apply and a manufacturer’s selection is recommended to ensure space loads are met. The HVAC engineer should consider these strategies and determine which is best for the project before detailed design begins.
DOAS energy recovery considerations
Exhaust air energy recovery is often considered when designing a DOAS to potentially reduce equipment sizing and energy usage. Energy codes require energy recovery for systems with high percentages of outside air. The percentage where energy recovery is required has steadily decreased with new code updates. The applicability of this requirement varies based on climate zone, supply fan airflow rate, percentage of outside air and ventilation system operating hours per year. When required by codes, energy recovery devices, such as enthalpy wheels and fixed membrane heat exchangers, must have a minimum enthalpy recovery ratio of 50%.
Additionally, a bypass damper or some other control must be included to disable the device when outside air conditions are not conducive for energy recovery, such as when air economizers would normally be active.
There are exceptions to the energy recovery requirements, so verify specific code requirements enforced for each project. It is considered best practice to utilize energy recovery where possible, even if there is an exception that applies. At times, the exhaust flow from the spaces may need to be increased from minimum requirements to meet the efficiency standard for the energy recovery device. The engineer should design the DOAS ventilation airflow and the exhaust airflow to provide overall positive building pressure and meet the code required minimum energy recovery enthalpy recovery ratio.

When including energy recovery in a DOAS, engineers must decide whether to account for the capacity of the energy recovery device when sizing cooling and heating coils. If cooling and heating capacities are reduced, energy recovery can appear more cost-effective, but risk increases. However, if capacities are not reduced, the ventilation load is met even if the energy recovery device fails or is later removed. Either way, maintenance of the energy recovery device is just as critical as any other portion of the DOAS.
Supply temperatures for DOAS
To dehumidify the raw outdoor air in summer, the DOAS cools the supply air down below saturation or dewpoint, and moisture is removed from the air as condensate. Many engineers will use the ASHRAE dehumidification design condition and heat recovery temperatures to assure they have accounted for the full dehumidification load. A leaving coil temperature of 52 °F or lower is typically used for the design. In cooling season, the air can be sent to the spaces at this temperature, but there is a risk of overcooling some spaces. At times, the saturated air is reheated to avoid over cooling.
However, energy codes limit the reheat in cooling season to no more than 60 °F if the majority of zone-level HVAC systems served by the DOAS require cooling. In this way, not only is no ventilation load added for the space conditioning systems, but the DOAS helps to reduce the load on the space cooling system.
Additionally, engineers need to be mindful of the supply location of the DOAS airflow in the space, and that the air needs to be cooler than the space temperature to utilize the zone effectiveness ratio of one for the required airflow calculations mentioned above. Therefore, many engineers specify duct insulation on the DOAS air even when the duct is exposed in a conditioned space.
Demand control ventilation
Demand control ventilation (DCV) can be accomplished with a DOAS design. Typically, variable air volume (VAV) cooling only terminals are used to provide DOAS supply air to a space requiring DCV. In this scenario, the DOAS maintains a duct static pressure setpoint in the supply duct and the supply fan speed varies to maintain the static pressure. The VAV terminal can be set to a minimum unoccupied flow. As carbon dioxide (CO2) levels rise when spaces become occupied, the VAV terminal opens and supplies more ventilation air – requiring the DOAS supply fan to increase until the CO2 setpoint level is obtained.

Constant volume VAV terminals are also needed to maintain the proper ventilation air for other spaces that do not need DCV. Without constant volume VAV control, the required ventilation airflow can fluctuate and become too little or too much. Likewise, there needs to be control for the exhaust amounts and supply, while maintaining overall building pressure. Energy codes are less likely to require DCV if energy recovery requirements are met. The requirement depends on which code or standard is used, and which year version is enforced. To minimize complications, the engineer is advised to check the DCV code section that applies to the project early in the design process.
Manufacturer provided versus designed controls
Packaged equipment manufacturers provide almost all components necessary for the operation of a DOAS, but there are a few others the engineer may want to consider.
Outside air measuring stations: DOAS units do not necessarily include an outdoor air measuring station. Information from the station can be valuable in trouble shooting, and can be used to vary the supply speed based on filter loading so that the airflow rate through the unit remains constant. The outside air measurement provides one of the most crucial pieces of information available for why a DOAS was chosen in the first place. You can’t control what you don’t measure, so the outside air measurement should be considered for each DOAS. There are multiple ways to accomplish reading the airflow values, including piezo rings and thermal dispersion instruments. For similar reasons, exhaust airflow measurement is desired and the engineer can choose what might be the best method for their project.

Condensate overflow sensors: While these are not required for most applications, many DOAS units are roof mounted and ducted through to the spaces below. Eventually, condensate drains get clogged and need to be cleaned out. Even though the condensate is at the roof level and may not pose an immediate nuisance threat to occupants below, chances are high that the overflow will get into the duct and leak into the ceiling space. An overflow alarm sensor prevents this from becoming a problem. It can de-activate the unit and keep it from becoming a larger issue. The building automation system (BAS) or local alarm should be signaled. The DOAS is the main way ventilation air is supplied, so its continued operation is crucial to the indoor air quality.
Filter gauges: These should be provided, and control alarms signaled, when the filter pressure drop indicates it requires changing. It is not uncommon for the filters to need changing more often than most facility operators may be expecting. DOAS, with 100% outside air, have the capability of introducing much more air particulates than other air systems, making monthly filter changes common. The particulate quantity depends on the local environment and what might be circulating in the air at the project site. There are many variables, so a good filter alarm is crucial. It is also best practice to filter the exhaust before it flows through the enthalpy wheel, and place a filter gauge and alarm there as well.
With packaged DOAS equipment, most temperature and humidity sensor status indicators are included. The usual monitoring points include:
-
Temperature points include exhaust, outside air, mixed air (outside air downstream of enthalpy wheel), cooling coil leaving air, hot gas reheat leaving air and supply air to spaces.
-
Humidity points include exhaust before the enthalpy wheel (or space humidity), outside air and supply air to spaces.
-
Other status points: supply fan on/off status and speed, exhaust fan on/off status and speed, enthalpy wheel on/off status, filter differential pressures, supply and exhaust airflows and heating percentage.
-
Any sensors not provided by the DOAS manufacturer can be added to the BAS as separate control points.
Package units usually come programmed for five modes of operation.
-
Cooling: In cooling mode, supply air temperature set point can be 60 F and the compressors modulate to maintain the supply air setpoint.
-
Heating: In heating mode, the supply air setpoint can be 68 F, or 2 degrees lower than the space temperature, and the heat input is modulated to maintain the supply air setpoint.
-
Vent: Vent mode is when neither cooling nor heating is required. The enthalpy wheel can be turned off or bypassed.
-
Dehumidification: Dehumidification is a special case of the cooling mode, and is initiated when the exhaust or space humidity level reaches a setpoint of 60% relative humidity. The compressors only modulate to maintain a low suction temperature and the hot gas reheat is modulated to maintain the supply air temperature.
-
Off: Off is for when no ventilation air is required or unoccupied periods.
It is best practice to use the packaged unit manufacturer’s programmed algorithms for these functions and only monitor the sensors and devices mentioned above. Actual control points for user input are usually unit start/stop, supply air temperature setpoint, cooling season setpoint and heating season setpoint. This keeps the controls simple for operating personnel.