Here is some guidance on how to implement paralleling strategies for generators, plus how to lay out a proper control scheme to achieve it.
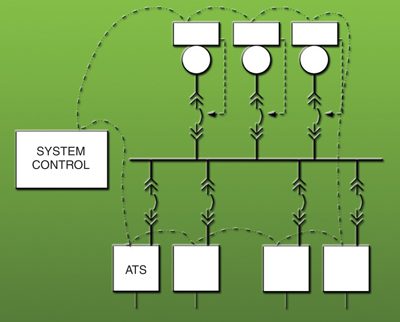
Contrary to conventional wisdom, paralleling systems are not completely customized control and power distribution systems, but rather a combination of common control functions for each major function in the facility power system. Consequently, with a basic understanding of these common functions, it’s possible to get a good understanding of nearly any system design.
The common major control groups in an on-site power system include:
- Individual genset/paralleling controls
- Power transfer control systems
- System level controls.
Every on-site power system with paralleled gensets uses some or all of these major functional control blocks. Not all facilities need all functions, and some systems may need a handful of other supervisory functions, but the use of common functionality whenever possible leads to more reliable designs, better documentation, easier training, and better capability to support the product over the life of the facility.
Basic generator functions
All alternating current (ac) gensets, whether paralleled or not, require several active control subsystems: engine control and protection, governing, and alternator control and protection.
The functions in an engine control and protection system include controls to start and stop the engine; protection for common failure conditions, such as low oil pressure and high engine temperature; failure to start; and an operator interface to allow manual control of the genset and visibility of the genset’s condition and status.
Governing functions are provided to allow the engine to maintain constant speed at any steady-state load from no load to fully rated load. Governing functions are very similar to the cruise control in a typical car: as load changes, the system monitors speed and corrects the fuel rate to maintain or recover to a preset speed level.
Emission-controlled engines all have integrated governing and engine protection systems that incorporate all the functions noted here, except for an operator interface panel. Emission-controlled engines often have many other protective functions in addition to those noted here. Each engine manufacturer has slightly different protection and control systems, but the overall functions are common.
The major function of the alternator control system is to control voltage by sensing voltage level and managing the excitation level to maintain as close to constant voltage as is possible.
Alternator protection is, at a minimum, thermal over current protection, which is commonly provided by either a circuit breaker or a protective relay. Minimizing ac protection in a genset improves reliability of service by minimizing the risk of nuisance trips at minimal risk because the system are normally de-energized and operate under load only a very limited number of hours relative to other facility power distribution equipment.
It is worth noting that any control issue on a genset is resolved by manipulation of the fuel rate, excitation level, or simply turning the genset on or off.
Paralleling Functions
When generators are connected together on a common bus, one generator is first selected and closed to the bus, which proves a synchronizing reference to the other generators, and all the others synchronize to the bus. As they reach synchronous conditions and close to the bus via electrically operating paralleling breakers their load sharing controls begin operation, with each machine carrying an equal percentage of the total load on the bus. Most paralleling control systems also include additional necessary protective functions, which include reverse power (kW) and reverse kVAR functions. The control systems also include manual back-up for the synchronizing function.
When generators are to be paralleled with the utility grid, they must also include var/power factor controls and kW import/export functions.
Since these functions are common to all systems, many manufacturers have integrated all paralleling functions into a single board control for improved reliability and space-saving.
Power Transfer Functions
All systems that must have the ability to be served by both a utility service and generators must incorporate power transfer controls and power switching equipment. These devices are commonly integrated together into automatic transfer switches (ATS), but the functions can also be provided by independent controllers and circuit breaker pairs.
Power transfer functions that are done with paralleling gensets often have an additional function, which is a master synchronizer, which rather than driving a single specific generator, is designed to drive multiple generators simultaneously. The master synchronizer allows the generator system to be safely paralleled to the utility. Utility service providers usually require specific protective relays to protect their system when the generators are paralleled to it.
Power transfer controls for each switch or breaker pair incorporate voltage sensing to determine the suitability of power available from the utility or generator bus, logic to operate switch mechanisms or circuit breakers, an operator interface that allows supervision of all functions, and manual control. Use of independent controls for each switching point helps to eliminate single points of failure and improve system reliability.
System-Level Functions
The capacity of a paralleled generator system increases and decreases as generators connect and disconnect from the bus, so automatic load management equipment is necessary to control load devices. This provides assurance that the most important loads will always be served with highest priority, and that system reliability will be maintained.
Some systems also incorporate capacity management functions, which control the number of generators operating based on connected load. This is primarily done to minimize fuel consumption.
Finally, each supervisory system will generally include an operator panel to allow careful supervision and manual control of the system when that is desired.
System Architecture
There are many different system architectures available, but–perhaps surprisingly–most systems in service are selected from only a handful of designs.
In general, it is always desirable to provide a means to isolate the generator bus from the utility so that the system can be serviced without disrupting service to the load. Breaker pairs are also often used in utility paralleling applications and to achieve higher levels of selective coordination without costly 30-cycle rated ATS.
Power transfer equipment is necessary to allow prioritization of service to the most critical loads. This tends to be done with ATS equipment in low-voltage systems, especially at lower current levels (<1,600 amps). At higher current levels and in medium-voltage applications, breaker pairs are often used. Feeder breaker control can also be used for this function.
Tie breakers are sometimes used to allow loads to be fed from multiple buses, but it is desirable to do these functions with transfer pairs in most cases. They are particularly useful when they are manually operated.
System Implementation
This article has spent little time in discussing switchboard and switchgear equipment for paralleling applications because this equipment is typically well-understood by design engineers, and there is nothing different in how it is selected, specified, or applied as compared to utility-fed equipment.
Using the major building blocks, generator/paralleling equipment, power transfer pair equipment, and supervisory controls, nearly any system design can be developed. See Figure 1 for an example of control functions in a basic paralleling system.
Clearly, nearly all control functions can be performed by independent controls that provide better overall reliability relative to a system using central controls, even when the central controls use redundant control functions, because of the difficulty in eliminating single points of failure in any discrete system. Independent, dedicated purpose components in a system also have a major advantage in terms of serviceability over the life of a facility because they are often produced in large volumes resulting in better availability and familiarity by a larger number of technicians.
— Olson is a graduate mechanical engineer with an MBA who has been in the on-site power industry for more than 33 years, chiefly working with application engineering of complex systems and equipment, including paralleling systems.