Motor circuit protection involves understanding the National Electrical Code and equipment nameplate information
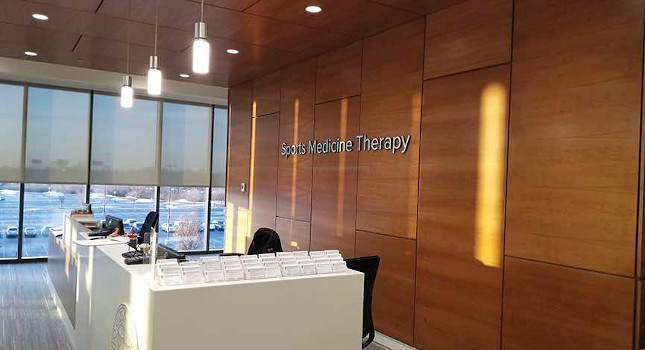
Learning Objectives
- Learn the differences between electrical overload and overcurrent.
- Know how to select a motor’s overload protective device.
- Review how to select branch short circuit and ground fault overcurrent protection device for motor circuits
- Understand how to select the correct conductor sizes for motors..
NFPA 70: National Electrical Code Article 430 covers motors including their overload protection, short-circuit and ground-fault protection, conductors, control circuits, controllers, motor control centers, disconnecting means, adjustable speed drive systems (also known as variable frequency drives) and grounding. This article is based upon the 2017 edition of NEC.
Part III of Article 430 covers overload protection for the motor and its circuit. It is important to protect motors, motor control equipment and motor branch circuit conductors from motor overloads and excessive heat. It is also critical that the motor can start and perform its intended operation.
The NEC states provisions of Article 430 Part III shall not apply to motor circuits rated over 1,000 volts, nominal. This article’s focus is on typical motors encountered below 1,000 volts.
Motor overload versus overcurrent
It is important to understand the differences between overload and overcurrent.
An overcurrent is when current exceeds the rated current of the motor or the ampacity of its conductors. This can be from an overload, short circuit or ground fault.
Overload is when operation of a motor in excess of its normal, full-load rating persists for a long enough time it would cause damage or overheating of the motor. A short-circuit or ground-fault is not considered an overload condition. Overload protection protects the motor from becoming a fire hazard.
Motor overload protection is not designed or may not be able to stop short-circuit currents or ground-fault currents. A fault is not an overload as stated in the NEC Article 100 definitions. However, an overload is considered an overcurrent.
A short circuit is the unintentional electrical connection between any two normally current-carrying conductors of an electrical circuit such as line to neutral or line to line.
A ground fault is an unintentional, electrically conducting connection between an ungrounded conductor of an electrical circuit and the normally noncurrent-carrying conductors, metallic raceways or equipment enclosures or the earth. During the period of a ground fault, dangerous voltages can be present on metal parts until the circuit overcurrent protection device such as a fuse or circuit breaker opens.
The NEC also states the provisions do not require motor overload protection where a power loss would cause a potential life-safety hazard such as with a fire pump.
Motor overload protection
A motor’s full load amps is used to size the overload protection. This FLA is found on the equipment nameplate. Examples of overload devices include fuses and circuit breakers as well as motor starters with overload relay(s) or a solid state motor controller/starter.
NEC 430.32 states for continuous duty motors with a service factor on the nameplate of 1.15 or more or with a nameplate temperature rise of 40°C shall have the overload device sized at no more than 125% of the motor nameplate current rating (FLA).
Continuous duty motors typically have continuous loads where the FLA current for is reached for three hours or more.
Typical overload protection can be fuses or circuit breakers, if applied properly. When sizing the overload device, if the calculation results in a nonstandard amp rating for a circuit breaker or fuse, the engineer is to use the next smaller size. Standard fuses and circuit breaker sizes can be found in NEC 240.6(A).
All other motors other than ones with a nameplate of 1.15 or more or with a nameplate temperature rise of 40°C shall have the overload device sized at no more than 115% of the motor’s FLA.
An example calculation to size a motor overload protection device is:
A motor nameplate has a service factor of 1.15 and an FLA of 24.5 amps.
The NEC states this overload device shall be sized at no more than 125% of the motor’s FLA for motors with a service factor of 1.15 or more.
24.5 amps x 1.25 = 30.625 amps
Use an overload protection device with a rating of 30 amps because the rating cannot exceed 125% of the FLA. This overload protection device can be a fuse or circuit breaker.
Motor overcurrent protection
Part IV of NEC Article 430 lists the requirements for motor overcurrent protection. This includes branch circuit short circuit and ground fault protection for the motor, the motor control equipment and the conductors.
Article 430.52 states the requirement that a motor branch circuit short circuit and ground fault protection device shall be capable of carrying the motor’s starting current. Typically, when voltage is first applied to an induction motor it requires a large inrush starting current. As the motor starts to reach its rated speed, the motor’s current reaches the FLA.
Table 430.52 in the NEC provides the maximum rating or setting of motor branch circuit short circuit and ground fault protective devices. The table lists the type of motor (singe-phase, alternating current polyphase motors other than wound rotor, squirrel cage — other than Design B energy-efficient, synchronous, wound-rotor and direct current/constant voltage). The table also lists for each type of motor the percentage of full load current for various branch circuit and ground fault protective devices: nontime delay fuses, dual element (time delay) fuses, instantaneous trip circuit breaker and inverse time circuit breaker.
This example calculation shows how to size the motor short circuit and ground fault protection device.
Determine the inverse circuit breaker size and conductor size for a 5-horsepower, 230-volt, single-phase motor with 75°C terminals.
First, go to Table 430.52 and find the row with “single phase motors.” Next go to the “inverse time breaker” column. There you will find “250,” which means “250% of full-load current.”
An electrical engineer may not have access to the motor nameplate during the design phase to determine the FLA for the motor. The manufacturer should be contacted to determine the FLA. If the FLA is still not available, the engineer should go to NEC Table 430.248 that lists full-load current in amps for single-phase motors. For example: 5 horsepower at 230 volts is 28 amps.
28 amps x 2.50 (this is the 250% of the full-load current from Table 430.52) = 70 amps.
A 70-amp circuit breaker is a standard size so the correct size for the maximum overcurrent protection device for this 5 horsepower motor.
If a calculation for the protective device does not match a standard circuit breaker size, then the next higher overcurrent protection device rating can be used. This explanation is found in Article 430.52(C)(1) Exception 1. Refer to this article in the NEC for further exceptions.
The minimum size conductors for the motor is determined by Article 430.22. This states conductors for a single motor are sized at no less than 125% of the table full-load current, not the nameplate amps.
From Table 430.248, use the 28 amps that were derived above.
28 amps x 1.25 (125% of the full-load amps) = 35 amps.
Use NEC Table 310.15(b)(16) to find the correct conductor size for copper, 75°C, Type THWN. For 35 amps, this is #10 AWG conductor size.
Note that the maximum overcurrent protection device is 70 amps while the conductors are sized at #10 AWG. In this example, the overcurrent protection for a motor circuit can be greater than the ampacity of the conductors required. This is something that many engineers often struggle with. The thought is that the conductor sizing should match the overcurrent protection device size. The NEC allows for the overcurrent protection device to exceed the rating of the conductors to allow for motor in-rush current.
The NEC allows for a single overcurrent protection device for motor overload, motor branch short circuit and ground faults. Article 430.55 combined overcurrent protection states that the single overcurrent protection device shall meet the overload requirements in Article 430.32.
VFDs and adjustable-speed drive systems
VFDs are a type of adjustable-speed drive system. VFDs are becoming more common in commercial and industrial facilities. VFDs can provide energy savings compared to constant speed motors.
NEC Article 430 Part X deals with adjustable-speed drive systems. Most VFDs come with their own overload and short circuit and ground fault protection device.
If a VFD does not have its own protective device(s), then NEC 430.32 and 430.52 shall be used to determine the rating of these devices.
Circuit protection for lighting
Lighting is considered a continuous load by the NEC. This is a load where the maximum current is expected to be three hours or more.
NEC Article 410 addresses lighting. However, Article 210.19 addresses the sizing of lighting conductors as most lighting fixtures are left on three hours or more continuously. 210.9(A)(1) is for lighting branch circuit not greater than 600 volts. 210.19(A)(1)(a) states when a branch circuit supplies a continuous load, the minimum branch circuit conductor size shall be sized at not less than 125% of the continuous load.
For example, an electrical engineer is designing lighting for a new sports medicine facility. The engineer is determining the number of recessed LED can lighting fixtures in the reception and waiting area that can be on a 120-volt, 20-amp circuit breaker that is not 100% fully rated.
A 100% fully rated circuit breaker can handle the current listed on its rating for continuous loads. A typical circuit breaker is rated for 80% of the current listed on the breaker for continuous loads. For example, a typical 20-amp circuit breaker (not 100% fully rated) can handle 16 amps of continuous loads, which is 80% of 20 amps.
The decorative lighting fixtures are to be controlled on a separate circuit (see Figure 1). The lighting fixtures are to be left on continuously for approximately 16 hours each day. Each recessed can lighting fixture in the open office area is 28 watts.
NEC Article 210.19(A)(1)(a) states continuous loads must have branch circuit conductor sizes at not less than 125% of the continuous load. If a branch circuit has continuous loads or any combination of continuous and noncontinuous loads, the minimum branch-circuit conductor size shall have an ampacity not less than the noncontinuous load plus 125% of the continuous load.
Calculation: A typical 20-amp circuit breaker is rated for 16 amps. With a continuous lighting load, 16 amps/1.25 (125%) = 12.8 amps. This means there are 12.8 amps available for lighting loads on this circuit.
28 watts needs to be converted to volt-amps for this calculation. LED light sources have a power factor value usually between 0.65 and 0.95. We will use a 0.85 power factor for this calculation.
28 watts/0.85 = 32.9 volt-amps; this means each recessed LED lighting fixture uses 32.9 volt-amps.
To determine the maximum number of these LED lighting fixtures allowed on the circuit:
120 volts x 12.8 amps = 1,536 volt-amps; this is the maximum volt-amps allowed on the circuit.
1,536 volt-amps/32.9 volt-amps = 46.7 LED lighting fixtures; 46 lighting fixtures is the maximum number of recessed LED can lighting fixtures on this circuit.
One issue electrical engineers may not be aware of is inrush current for LED light sources. When LED light sources are turned on, a large inrush current may occur. This large inrush current may trip a circuit breaker or blow a fuse. The engineer should determine if the inrush current and its duration could trip a circuit breaker.
An LED light source’s specification sheet may state something akin to this “to address inrush current, slow blow fuse or type C/D breaker should be used.” A typical Type C circuit breaker has a minimum trip setting of 5 to 10 times its rated current. A typical Type D circuit breaker has a minimum trip setting of 10 to 20 times its rated current.
NEC Article 411 contains low-voltage lighting systems. This is for lighting systems operating at no more than 30 volts AC or 60 volts DC. Common low-voltage systems include some track lighting and are common in commercial buildings, museums, landscaping, etc.
Low-voltage lighting systems typically have a power supply, lighting fixtures and other associated equipment such as a track for track lighting.
NEC Article 411.7 states that low-voltage lighting systems can be supplied from a maximum 20-amp branch circuit.
Circuit protection for motors and lighting systems are covered by the NEC. Motors may be used for life-safety systems such as elevators, smoke evacuation systems, etc. Lighting systems may include emergency lighting for egress for building occupants.
NEC Article 430 covers motors. An electrical engineer needs to properly size the overload device and the short circuit and ground fault protection device for a motor.
NEC Article 410 addresses lighting. Lighting is considered a continuous load and this must be considered in designing circuit prot