Learn how to specify systems for government and military buildings
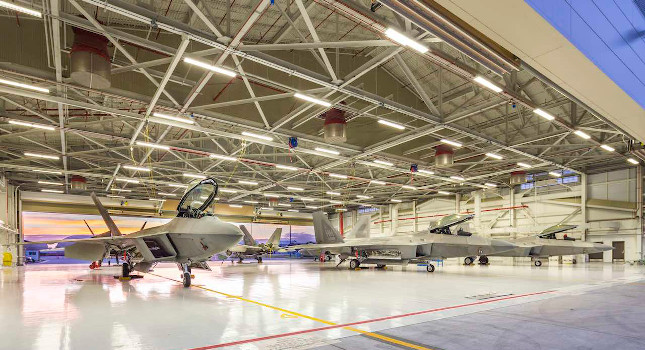
Respondents:
- Chris Ankeny, PE, LC, LEED AP BD+C, Associate/Senior Electrical Engineer, Clark Nexsen, Virginia Beach, Va.
- Mark Chrisman, PhD, PE, Health Care Practice Director/Vice President, Henderson Engineers, Kansas City, Mo.
- Randall Ehret, PE, Technical Director | Electrical, ESD, Chicago
- Todd Garing, PE, LEED AP BD+C, Vice President, Mueller Associates Inc., Linthicum, Md.
- Rob Jordan, PE, FPE, LEED AP, Mechanical Department Manager, Burns & McDonnell, Kansas City,
- Julene May, PE, PMP, Chief, F-35 Beddown Program Management Office, Stanley Consultants Inc., Eielson AFB, Alaska
- Jon Sajdak, PE, Associate Fire Protection Engineer, Page, Austin, Tex.
- Troy Windom, Automation Manager, Dewberry, Raleigh, N.C.
What’s the biggest trend in government, state, municipal, federal, correctional and military projects?
Chris Ankeny: We find increasing efficiency — both of function and related to energy usage — at the forefront with both the government and federal markets. Many projects we work on involve consolidating different functions in one centralized facility. Related to U.S. Department of Defense work, over the last few years we have seen the focus shifting from energy efficiency to energy resilience and security.
Cybersecurity is a trend that is on the rise. As mandates are set to for DOD and nonDOD facility related control systems (such as building direct digital control, utility supervisory control and data acquisition and smart metering) to be cyber secure, our clients are in turn requiring that project designers increase their sensitivity and expertise related to cybersecurity.
Whole building commissioning is a burgeoning trend that our DOD clients are more consistently requiring be provided and performed on projects. A commissioning team that is independent or the designer of record provides this and is involved before the start of the formal design process when the owner’s project requirements are being developed. The commissioning team then remains engaged with the project throughout the design and construction phases.
On the flip side, meeting the budget and codes are constants that never change with this type of work.
Mark Chrisman: On the military side, we have seen a lot of projects related to replacing or upgrading aging infrastructure or buildings. Most of the original World War II era construction is showing its age and requires major repairs or replacement. We are also seeing technology continuing to play a major role in building systems, be it through connectivity integration of building systems or apps for security or wayfinding.
Rob Jordan: The biggest trend we’ve seen in federal projects has been an increased emphasis placed on achieving high-performance and sustainable buildings, including a reduction in energy usage. Several mandates including UFC 1-200-02, ASHRAE 90.1 and ASHRAE 189.1 (which combine the minimum requirements of the Energy Policy Act of 2005, the Energy Independence and Security Act of 2007 and Guiding Principles for Sustainable Federal Buildings) require us to assess all parts of a building’s heating, ventilation and air conditioning equipment, lighting system, building envelope and mechanical or plumbing system for maximum efficiency in energy usage and water conservation from the very beginning of the project.
Julene May: During the ongoing design and construction program to beddown the Air Force’s newest F-35 aircraft, 41 major facility projects were contracted, using a balance of the traditional design-bid-build and design-build project delivery methods. The method used was selected based on several factors, including complexity, cost, the need to award rapidly to meet government fiscal requirements and most importantly the mission need date. During the design of these projects the use of building information modeling, civil site modeling and mechanical, electrical and plumbing design coordination was key to delivering projects efficiently. I would say two significant trends impacting our program are alternate project delivery methods and design automation.
Troy Windom: I think cybersecurity and the “internet of things” are probably the two biggest trends in the building automation systems market. Currently, the big advances most BAS companies are making are in leveraging the information technology infrastructure that almost all buildings have in place. The issue being though that some information technology professionals aren’t necessarily keen on having additional equipment on their networks.
What trends do you think are on the horizon for such projects?
Chris Ankeny: We are seeing more advanced and more complex use of technology to manage, monitor and maintain facilities. Rapid technology innovation includes battery storage, electrification and Big Data.
When renewable energy technologies — for example battery storage coupled with solar photovoltaics — are employed, the opportunity for energy independence through electrification becomes feasible. Basically, all electric power produced and consumed by an owner/customer would be through renewable technologies allowing for the transition off fossil fuel dependence.
Big Data is a trend that will continue to challenge our clients and our industry going forward. With the growth and implementation of “smart” systems along with the continued integration of operational technology with IT, there is an abundance of data that can be monitored, collected and analyzed to support proactive and smart decision-making by owners and facility managers.
Mark Chrisman: Beyond infection control technologies and/or functional changes that are a result of designing around COVID-19, likely we will continue to see a continued push for modular construction and prefabrication that will allow us to build faster and safer. We will also continue to see a huge push in technology. Buildings and building systems continue to get smarter through the use of integration technologies making them easier to control and specialize for building occupants.
Randall Ehret: I believe the industry will begin looking at design alternatives to improve capabilities to more safely occupy facilities during infectious outbreaks.
Julene May: Greater reliance on BIM integration between design disciplines, construction contractors and facility maintainers. Also, 3-D visualization will continue to improve design and construction, as well as provide conceptual views of finished projects for owners and project sponsors.
Rob Jordan: We are seeing an increased interest in projects involving microgrids and renewable energy. As energy security and resiliency become increasingly important, these types of secure and sustainable energy sources will become more and more popular. Renewables and microgrids also support green energy initiatives, with many states such as Hawaii and California implementing 100% renewable energy goals for the not-so-distant future.
Troy Windom: Federal law requires cybersecurity on projects, and I think as we see more state and local governments getting systems hacked for ransom, they will look at cybersecurity more closely. Nowadays, there are college degree programs for this area of expertise.
Each type of project presents unique challenges — what types of challenges do you encounter for these types of projects that you might not face on “civilian” or other types of structures?
Troy Windom: I think as a controls designer, which is typically designed under mechanical, the single biggest issue is getting buy-in from the different elements of the IT world in a government agency. Oftentimes the work is completed by a contractor who may disregard BAS cybersecurity because it’s not part of their contract. Where as in the civilian world, it’s quite often just one person and that person is more willing to provide buy-in.
Mark Chrisman: Two major challenges come to mind: the amount of codes, standards and regulations that apply to building design and construction as well as the process for obtaining a permit. In the private sector, we often have a single set of criteria for design and a single review at 100% design, which often leads to a permit. While not always quick, it is often smoother than in federal work. In the federal world, we often have multiple sets of codes and criteria that are duplicative and conflicting. Even with an order of precedence set, there are challenges rectifying the differences. Additionally, we often have several reviews during design by the appropriate federal agency/agencies, often with new comments and questions arising at the final submittal. The process is often complex and approval generally takes much longer than private sector work.
Rob Jordan: With any federal project comes an added layer of security. Many of our government projects are produced for the DOD and other secure federal entities, so we design and construct with our nation’s safety and security top of mind.
On a large data center project for a confidential DOD client, the chilled water system feeding the data center was designed with redundant chilled water piping systems and chilled water equipment redundancy to satisfy the critical nature and security needs of the data center.
On a recent combined heat and power project for the Architect of the Capitol, all materials to be used on-site needed to be inspected at an off-site facility. This required significant coordination with the Capitol Police and the construction and engineering teams but was necessary to allow for an extra layer of security.
Jon Sajdak: For DOD projects, in addition to having additional design criteria based on the UFC, other challenges with these projects include meeting base installation guidelines. Most bases that Page has done projects on have a lengthy and detailed document that includes additional criteria for all disciplines to meet. This includes, but is not limited to operational, maintenance and specific material requirements. It is imperative to be diligent at the start of a project to make sure all of these criteria are met. Some design components incorporated on previous projects located on other bases may not be applicable to a project on a different installation.
Todd Garing: Most of our project types present unique challenges. For example, some government buildings also serve as public and performing arts spaces, requiring large cooling loads and strict acoustical requirements to account for vibration, air velocities and distribution restrictions.
Government buildings may also have museum spaces, which require strict temperature and humidity conditions to preserve collections. In doing so, achieving energy efficiency also requires being very creative and having a thorough understanding of fundamental engineering.
Government buildings that include laboratories have varied needs, such as occupant safety and inconsistent use of equipment that presents challenges for systems to be responsive to changing demands and able to turn down when not needed to save energy.
Many government buildings are also historic structures, which present major challenges when tasked to incorporate modern systems, minimize energy consumption, maximize sustainability and not impact the building’s historic fabric.
Overall, many institutional owners are always highly interested in sustainability but are frequently challenged by budget constraints. In these circumstances, we discuss various options and offer examples of past projects and perform life cycle cost analyses to help inform their decision-making process.
Julene May: The biggest challenge at active-duty military installations is the high turnover of users and decision makers. It is very rare that the person or group that made decisions during design will be the users when the facility is ready for occupation. This high turnover may even occur during construction and so by the time the end user is in the building, some of the decisions are no longer understood. In other words, the biggest challenge is the perceived lack of continuity with the owner.
Other challenges included Arctic engineering and construction on permafrost and in boggy or marshy conditions. Additional challenges involved construction of Secure Compartmented Information Facilities to provide secure work environments and communications infrastructure specific to the weapon system.
Chris Ankeny: The time between project development, funding, team selection, design and construction can present budget challenges. Most commonly these challenges are related to changing financial markets for materials and construction costs.
The prescriptive nature of federal and DOD work is a given. Knowledge and application of code is essential and it is ever changing. Our firm has a large team of engineers, architects and project managers with deep knowledge and experience working on federal and DOD projects and a culture of sharing knowledge with newer professionals in the firm.
The Whole Building Design Guide has the majority of the reference documents for government projects. Many agencies require their own set of standards and regulations that call for design features above and beyond established code. The challenge is primarily one of communication. The easiest way for a project to be successful is when all the stakeholders have the same level of knowledge and expectations.
What are engineers doing to ensure such projects (both new and existing structures) meet challenges associated with emerging technologies?
Julene May: Our project delivery teams, engineers and designers make every effort to incorporate proven technologies into facilities. We use the International Building Code as supplemented by the Defense Department’s Unified Facilities Criteria, Unified Facilities Guide Specifications, Engineering Technical Letters and Engineering and Construction Bulletins. Cybersecurity of Facility Related Control Systems is of particular concern and requires close coordination of users, designers and security experts to ensure compliance with DOD requirements.
Randall Ehret: Whether we are talking public or private funding, budgets are always an issue. The minimum acceptable solution is to provide adaptable, intelligent infrastructure to allow facilities to grow with technology. One of our recent projects is a 2050 Master Plan with lofty, forward-thinking goals. For this project we worked closely with the state to set stretch goals that would reside an intelligent backbone,
Mark Chrisman: While this is easier to accommodate in the private sector, often there are contractual issues in the federal world that may limit or prohibit incorporation of newer technologies. Sometimes the request for proposals are held for funding and may be several years old, referencing older standards or criteria that may not allow a newer proven technology. We can sometimes request equivalencies or waivers to help with this process. As we have all seen, technology continues to change rapidly and we do our best to be informed so the infrastructure is in place to support the technologies to the best that we can, often within budget limitations.
Jon Sajdak: There are many resources available to engineers to keep up with emerging technologies. Vendors and manufacturers typically offer webinars and virtual training sessions to introduce new products and provide examples of applications for where they can be used. In addition, case studies are made available and most manufacturers provide technical specialists that can answer questions on new systems and technologies.
Todd Garing: Designing systems with an eye on the future is a core principle and we design systems to be compatible with this philosophy.
One example is using low-temperature heating water, which may not be required if, for instance, the building is connected to a central steam plant, but the low-temperature water is compatible with efficient systems such as heat recovery chillers, water source heat pumps, geothermal, solar thermal and condensing boilers. We also try to minimize roof-mounted equipment and provide electrical pathways to maximize photovoltaic arrays, even if they are not included in the initial scope of the project, but are available for the future.
Chris Ankeny: Our firm culture promotes innovation and we work to stay on top of emerging technologies in our industry. We feel it is important to educate project stakeholders about new options that they might not be aware of so they can make the most informed project decisions. If the budget does not allow for all the desired components, an infrastructure can be put into place to accommodate upgrades in the future.
Troy Windom: This requires careful coordination. As previously mentioned, typically BAS are under the mechanical design. Most mechanical engineers understand what they want the system to do and can right clear mechanical specifications. The issue then becomes how do other systems integrate and what protocols are necessary. This is usually where a programmer gets involved: they help identify how to get information across the network. At this point, information technology gets involved. Good firms have learned they need to coordinate how they want the building systems to work. It takes more than one discipline working together to be successful.
Tell us about a recent project you’ve worked on that’s innovative, large-scale or otherwise noteworthy.
Todd Garing: The Smithsonian National Air and Space Museum on the Washington, D.C., National Mall is undergoing a full-scale renovation. At the beginning of the project, we performed several studies to evaluate numerous options for every envelope component, heating and cooling plants, HVAC distribution systems, lighting, power, water and renewable energy. We performed numerous energy model runs to evaluate all the options and then evaluated various combinations. We then performed life cycle cost analyses to help inform the decision-making process.
The systems selected for NASM include a dedicated heat recovery chiller providing chilled water and heating water at the same time; dedicated outside air systems to pretreat the outside air and reduce the need for reheat (a major energy driver in many museums); adiabatic humidification, condensing boilers, a robust control system that responds to the drastic load fluctuations driven by weather and the sporadic attendance of the 7 million visitors a year; digital addressable LED lighting incorporating dimming, daylighting and vacancy controls; and metering of all branch circuits and rainwater and air conditioning condensate collection for reuse flushing toilets and urinals, cooling tower makeup and irrigation.
The two biggest impacts to energy savings were allowing different summer and winter gallery setpoints for temperature and humidity and the LED lighting — these two measures alone will result in savings of 40% energy consumption.
Jon Sajdak: One major project is the Rhine Ordnance Barracks — Medical Center Replacement (ROB-MCR) in Germany. The nearly 1 million square foot hospital will replace the existing medical center in Landstuhl. Our firm has been part of the independent technical review team over the past few years. This project has involved many design teams and reviewers from the U.S. and Germany. We have dealt with many challenges on this project to achieve compliance with U.S., German and DOD criteria. As part of the review team, we were responsible for highlighting portions of the design that did not comply with the applicable codes and standards. One challenge was aligning the code requirements between each country. For instance, wall and doors are rated with different classifications between the two countries so an equivalency analysis was required. It was interesting to observe how the German fire protection approach incorporates more passive fire protection requirements than the U.S., which relies more on active fire protection systems.
Rob Jordan: Burns & McDonnell is designing and building the Pacific Energy Assurance and Renewables Laboratory (PEARL). Located at Joint Base Pearl Harbor-Hickam in Hawaii, PEARL is a state-of-the-art renewable energy microgrid developed in coordination with the Hawaii Center for Advanced Transportation Technologies, the Air Force Research Laboratory, National Guard Bureau, Hawaii Air National Guard and the Naval Facilities Command. The initial stage of PEARL is the first of six planned microgrids to provide energy assurance and security for the entire 154th Wing F-22 campus while also helping make strides toward Hawaii’s renewable energy goals.
These microgrids will play a critical role in reducing Hawaii’s dependence on fossil fuels, boosting the transition to renewable energy and creating a multitude of new jobs in the state. Planning for the project began in 2016, with construction slated for completion in August 2020. Once complete, PEARL’s technical capabilities include solar PV integration, battery energy storage and the ability to restore power to the F-22 mission instantaneously. To read more about this project, click here.
Julene May: Eielson Air Force Base is located in the interior of Alaska and has patches of discontinuous permafrost around base. During the beddown of the F-35, three projects were required to implement large scale deep thawing techniques in ice-rich soils to a depth of 35 feet before construction. Once the thawing was complete deep dynamic compaction was employed to improve the loosely compacted soils. The decision to implement the large-scale ground thawing and deep dynamic compaction was coordinated with designers and end users to prevent ground thawing and settling of facilities, potentially impacting sensitive aircraft maintenance operations.
Randall Ehret: One recent project is the Illinois Department of Corrections Inpatient Treatment Center. For this project, we were challenged with building a hallmark patient hospital for incarcerated patients. The mantra for this project is the need to have a facility to care for both behavioral health and Category 3 patients (a Category 3 patient is defined as a basic care room in which the failure of equipment or a system is not likely to cause injury to the patient or caregiver, but can cause patient discomfort).
The facility needed to be built as a healing environment, not a prison, but yet secure and safe for both staff and patients. Selecting materials that struck the appropriate balance of looking like a modern healing environment but were also safe and effective in a prison environment became very challenging. The project is a design-build effort for the Illinois Capital Development Board. There are multiple stakeholders including the design-build team, the team that developed the turn-over package, the Capital Development Board, the Illinois Department of Corrections, the facility engineers for the site, medical team and commissioning agent. Everyone worked well together and respected the needs of interested parties to allow the proper balance to be achieved.
Troy Windom: Dewberry recently finished a building upgrade project for a courthouse and federal building in Puerto Rico. There were several different systems being tied into the BAS. They included electrical metering; PV power monitoring; air monitoring system; different HVAC manufacturers; and even the hot water mixing valve was smart. Almost every system had different communication protocols. In the end, the only system not permitted was the air monitoring system because it could not get a certificate of networthiness.
How has COVID-19 changed your work in these facility types? Has the coronavirus affected these projects, by either increasing or decreasing some aspect of them?
Randall Ehret: I was part of the dedicated team charged with converting Chicago’s McCormick Place Convention Center into a COVID-19 alternative patient care facility. The project entailed converting three halls within McCormick Place to facilitate 2,250 Category 3 patient beds and 750 Category 2 patient beds. The project had to be completed on an extremely tight timeline and work to maximize the functionality of the existing convention center infrastructure to satisfy the patient care requirements.
For the Category 3 patients, the existing ventilation system was adapted to operate in negative pressure mode and still meet temperature requirements (no easy feat for a mechanical system designed for significantly larger occupancy and equipment load factors). Plumbing and electrical systems were able to be distributed from the convention hook-ups to provide power to patient beds and meet the additional plumbing needs. The 750-bed Category 2 patient beds required a much more comprehensive and creative approach.
Patient beds were set up in tents. Scaffolding was installed around the perimeter of the tents to be used for HVAC, electrical and medical gas infrastructure distribution. Each tent had an individual negative pressure high-efficiency particulate air filter fan. Duct work was routed around the perimeter of the tents collected and exhausted directly to the outside. New exhaust fans were purchased through a COVID-19 quick ship program. An oxygen tank farm, medical vacuum compressor and medical vacuum system were provided and copper piping extended along the scaffolding to the patient beds in the tents. A portable diesel generator was brought in for patient care, critical power. Outlets were provided at each patient bed from the generator.
The process, while fast, was extremely exciting with all the interested parties involved: U.S. Army Corps of Engineers, City of Chicago, McCormick Place facilities team, the contractors and the caregivers to name a few.
Troy Windom: I think the single biggest issue is access to the project. Reviews seem to be taking longer because some of the clients don’t have access to what they need. It’s not possible to take work home. Has the coronavirus affected these projects, by either increasing or decreasing some aspect of them? As previously mentioned, we’ve seen an increase time in review time. I think over time because of COVID-19, you will find some changes in design that will impact systems to be more adaptable to changing situations.
Rob Jordan: Our federal projects are all critical infrastructure projects that continue to move forward throughout the COVID-19 disruption. We expect increased requests for developing and implementing advanced air filtration HVAC systems and building water management systems with enhanced sanitation. Burns & McDonnell goes the extra mile to put safety first for our clients and partners and safety and health during the COVID-19 disruption is no different. We already have teams actively working to develop a strategy for HVAC system programming, filtration, ventilation during periods of unoccupancy, ultraviolet disinfection and water management plans. Modifications to the HVAC systems can help facility owners control exposure from airborne viruses such as coronavirus.
Todd Garing: Every building is different. We review the guidelines provided by organizations such as ASHRAE and discuss options and impacts with our clients. We do believe there will be more emphasis moving forward on items such as filtration, disinfection, humidification and epidemic control modes, to name a few.
Mark Chrisman: To date, most of the federal projects we were previously awarded are moving forward as originally planned. I would expect that we will start to see some changes sooner than later as we look to modify building system design and functional layouts to accommodate measures recommended by the World Health Organization, Centers for Disease Control and Prevention and applicable health departments in response to the COVID-19 pandemic.
We have also spent a lot of time researching infection control technologies for building systems, which are being discussed with the private sector currently. We expect that we will be having similar discussions within the federal sector as projects continue to be approved/funded. Our federal sector work has remained strong and projects in construction have continued to move forward with minimal impacts to date. The duration and severity of the COVID-19 pandemic will likely determine further impacts to the federal sector.
Jon Sajdak: COVID-19 has changed the way some of our work is done. For projects that are currently in the design phase, there has been minimal changes to the process. Our team has increased the frequency of coordination meetings, but production has been shifted to remote work and most deliverable milestone dates have remained the same. The larger change has been to projects currently under construction. Site visits have been limited or prohibited due to travel restrictions and social distance guidelines. As a result, team members that are on-site or near the project location have provided virtual site visits and walk-throughs. There has been greater communication with contractors, especially with videos and photos to supplement discussions.
Chris Ankeny: We anticipate there may be increased requirements related to indoor air quality and factors like filtration and UV lights in air handlers, which we already specify for some clients. An existing municipal client has asked us to provide design costs to expand the current design to include UVC lamps for a coil cleaning only setup to airborne virus inactivation setup.
Julene May: The COVID-19 pandemic has required our team to adjust operations to work remotely as much as possible and use virtual means for design reviews and coordination meetings. Our field work has largely continued without interruption due to the program’s critical infrastructure designation. Work was performed in compliance with DOD directives and local guidance from the contracting officer.
How are engineers designing these kinds of projects to keep costs down while offering appealing features, complying with relevant codes and meeting client needs?
Rob Jordan: Our clients require high-performance systems, sometimes with a limited budget. Through detailed studies and processes such as commissioning, our team can help federal clients find the best solution to their needs and comply with all regulations while being mindful of cost. For example, our combined heat and power project for the Architect of the Capitol was originally envisioned as a new plant structure with a much larger system. After performing an hourly dispatch analysis and economic study, it was determined that a smaller system was better, which could be designed and constructed within the existing plant structure. This saved the client money both upfront and provided a long-term economic benefit.
Mark Chrisman: Most of our military projects use design-build project delivery and cost/best value represents a major aspect of successfully landing and completing these types of projects. The major design and cost discussions usually start early in the proposal stage and continue as we perform an initial site observation and review as-builts. Trade partners are engaged early, as we are often designing the building systems as the project is being developed by the architects. Because we have a consistent team of folks actively engaged in these projects, we have a good handle on the codes and criteria and their challenges. Through MATOC or IDIQ contracts, we also develop a good relationship with contracting officers, facility users and U.S. Army Corps of Engineers personnel, which helps with understanding needs.
Todd Garing: We implement strategies that solve multiple problems at once. For instance, a small heat recovery chiller can improve energy efficiency, provide night and winter cooling and be backed up on the generator to serve critical cooling loads.
Randall Ehret: Every project has its distinct parameters and cost must be approached uniquely. It is a matter of trying to implement the appropriate application of the most suitable product. An example from our McCormick Place COVID-19 alternative care project was the strategic use of scaffolding to serve as a distribution support for the HVAC, medical gas and electrical systems. The temporary nature of the facility, combined with the need for extremely fast installation, the large volume space and the high ceilings, drove the use of scaffolding as an effective, efficient solution. With our department of correction’s inpatient care facility, it was more a matter of the balance between form and function. One example was the need for correctional grade plumbing fixtures versus creating a healing environment. The solution: correctional fixtures with a white enamel finish. Another example was working through logistics and care parameters with the users. Where less-restrictive patient environments were acceptable due to less-mobile or more heavily monitored patients, a less “correctional grade” product was implemented.
Troy Windom: When it comes to BAS, IoT by nature helps keep costs down by using the information technology network that will have to be there anyway as the communication platform. This significantly reduces installation costs. Additionally, you can now use common machines for servers. In the end, you’ll be reducing first costs and life cycle costs.
Chris Ankeny: Keeping costs down is an intrinsic part of meeting client needs. We accomplish this by keeping a continuous watch on our cost models. At every project phase we have a cost estimate that we analyze to see how it is tracking with the project design. If it’s not in range we look at cost saving measures and make design or other adjustments as needed.
Jon Sajdak: From a fire protection aspect, air-aspirating smoke detection systems have become more widely used throughout government, state and federal projects. The upfront cost of air aspirating smoke detection systems is equal to or slightly greater than a spot-type smoke detection system. However, the long-term cost savings to test and maintain these systems are far less for the air-aspirating smoke detection systems. They are also considered more reliable given the fact that they are easier to maintain and multiple levels of alarm/sensitivity settings can be programmed. These particularly appeal to clients in health care and correctional facilities because the systems can be tested remotely from each panel location.
How has your team incorporated integrated project delivery or virtual design and construction into a project? Define the owner’s project requirements and how the entire team fulfilled them using these methods.
Mark Chrisman: We have been using a form of VDC for many of our design-build military projects.
How are these types of buildings being designed to be more energy efficient?
Chris Ankeny: We focus on having conversations early — right from kick-off charettes — where we talk to the users and owner’s reps to hear what they are looking for. But we also come to the table with ideas and hope to get buy-in. Otherwise, it is easy for this part of the project to get lost in the design criteria, codes and standards.
Rob Jordan: To comply with UFC 1-200-02, we perform a whole building energy analysis to show the proposed building design has an energy savings of 30% over the ASHRAE Standard 90.1 Appendix G baseline. We also perform a 40-year life cycle analysis, which compares our design to at least three systems to prove which system is the most economical. Several strategies are used to meet these baselines, including high-efficiency chillers, efficient pumping systems, occupancy sensors, demand control ventilation, high-efficiency condensing boilers and solar domestic water heating.
Todd Garing: Energy efficiency starts with the reduction of the loads on the building. We have seen much more attention paid to the building envelope at the earliest stages with preliminary energy modeling to test ideas. For new buildings, the shape orientation, quantity and location of windows and skylights, floor plate depth, perimeter-to-square footage ratio and floor-to-roof ratio, can have a drastic effect on energy consumption, including daylighting and photovoltaics. For all buildings, the envelope material choices for glazing, wall and roof insulation and especially window shading play a role in energy consumption.
Inside the building, close attention should be paid to the lighting systems and miscellaneous equipment. Depending on the building type and systems installed, the miscellaneous equipment loads can account for 50% of the building energy, so anything that can be done to reduce these loads should be evaluated — examples include laptops instead of desktops, sleep mode for computers and monitors, shared copier/printers, smaller/fewer coffee machines and banning personal electric heaters.
Mark Chrisman: Our military work has continued to see an emphasis on implementing high-performance and energy-efficient building systems where practical (new greenfield buildings or additions for example). In new buildings or building additions the conversations are easier as we have more control over building features such as insulation, windows and other items that can help play an important role in HVAC and lighting design, which are the two big energy users. In renovation projects, there is at least a discussion about what could be done to increase energy efficiency. Often it comes down to the scope of the project, concerns if the building is historical and budgetary or space constraints.
Randall Ehret: It was interesting establishing the sustainability now and looking ahead to 2050 as part of the 2050 master-plan project for the State of Illinois. There wasn’t a dedicated person to talk to about sustainability for the state and the capitol, so ESD and the sustainability consultants had a lot of influence over setting these goals. As a master plan tends to be rather aggressive, the sustainability goals followed suit with a goal of having the campus be carbon free by 2050. Having the state building itself strive for this aggressive goal is a great way for setting an example for the rest of the buildings.
What is the biggest challenge you come across when designing government, state, federal, correctional and military projects?
Mark Chrisman: I think the biggest challenge is related to the large number of codes, standards and criteria that are often applicable on these types of projects. We often run into conflicting and duplicative requirements during design, which require some level of discussion or remediation with all involved parties. This can impact projects and schedules.
Jon Sajdak: The greatest challenge for these projects includes aligning host nation requirements with U.S. requirements for projects that are built in other countries. These projects require extensive code comparison analysis across all disciplines and applying the most restrictive criteria in most cases. Many times, there are code conflicts between the host nation and U.S. standards and solutions or equivalencies need to be derived for authority having jurisdiction approval.
Chris Ankeny: The biggest challenge is not unique to just these types of buildings. We work to deliver a successful project outcome that balances the desire for energy efficiency and sustainable features with all the mission, security and performance requirements. We also sometimes navigate conflicting requirements. And again, like most projects, accomplishing high standards for energy efficiency and technology while staying in the cost range is a challenge. Especially considering that the project budget is approved long before the project is designed.
Troy Windom: Getting buy-in from all the stakeholders. We often encounter many differing opinions depending on what is important to each stakeholder. Of course, each one has a different goal to meet.
Rob Jordan: Burns & McDonnell works on government, federal and military projects for every branch of government and every branch of the United States military. Our work spans across the country and around the world, including unique locations like Guam, Guantanamo Bay and Kwajalein Atoll. Every installation is different and each project has its own unique challenges. System preferences, corrosion issues, design guidelines, security requirements, maintenance requirements, cost factors and climate conditions all vary project to project. Our first step is to assign a highly specialized and knowledgeable team that can navigate the challenges of each site. This builds client confidence that the project execution will run smoothly and efficiently to deliver a successful outcome.
Julene May: We encounter significant challenges in designing federal projects, with the most significant being a lack of continuity with the owner’s personnel. That can result in changing requirements and delayed decision making, which puts schedules and budgets at elevated risk.
Randall Ehret: There isn’t only one thing. It is understanding the chain of command; what codes and standards to follow and to use the proper process/paperwork.
What is the typical project delivery method your firm uses when designing these facilities?
Mark Chrisman: For military projects, our most common delivery method is design-build. We are still seeing design-bid-build on state/local projects and in the General Services Administration sector, but design-build is gaining traction. At any given moment we have several design-build projects going on throughout our firm. It’s an effective and efficient method for all parties, including the owner, when you have a good team in place. We have been working with most of our design-build partners for many years and our teams are very collaborative. In this setup, everyone goes the extra mile to make sure things are done correctly the first time as the team succeeds and fails together — and failure is not an option in the federal sector. While integrated project delivery is a great idea in concept, we have seen very few true IPD projects move forward, most end up being some version of design-build or a modified version of IPD.
Rob Jordan: Burns & McDonnell works to find the best project delivery method for each individual client, which is often a design-build delivery method. Design-build can provide major cost savings on projects and deliver them in a more efficient manner, often ahead of schedule and under budget.
Burns & McDonnell recently completed the addition of combined heat and power to the Architect of the Capitol’s capital power plant. This project was executed using a design-build delivery method. The replacement of steam previously generated by coal-fueled boilers with the CHP system resulted in a reduction of campus greenhouse gas, as well as added redundancy and resiliency. Similarly, significant redundancy was designed into the replacement steam plant in our project for an army ammunitions plant in Tennessee.
Jon Sajdak: For these types of projects, our firm uses design-build most frequently. This project delivery method allows for coordination between the design team and contractors throughout both the design and construction administration process. Our firm has had success on projects where subcontractors are brought on early to coordinate project requirements and design intent.
One recent project that our team is part of is the Schofield Barracks Behavioral Health and Dental Clinic in Honolulu, Hawaii. The facility will provide additional space for medical services on the Schofield Barracks and reduce the need for patients to travel to Triple Army Medical Center for care. Construction is currently underway and is targeting an opening date of later this year.
Julene May: During the beddown at Eielson AFB, the project delivery method varied between design-bid-build and design-build, depending on timing of need to award the project and projected issues such as environmental and specialty designs, such as a facility having extra secure spaces that may be outside of a normal construction project. Although our firm performs design using all delivery methods, the most typical is design-bid-build, which generally affords more time and control to designers resulting in reduced project risk.