NFPA 20 provides fire protection engineers with guidance on design and installation of fire pumps and related components.
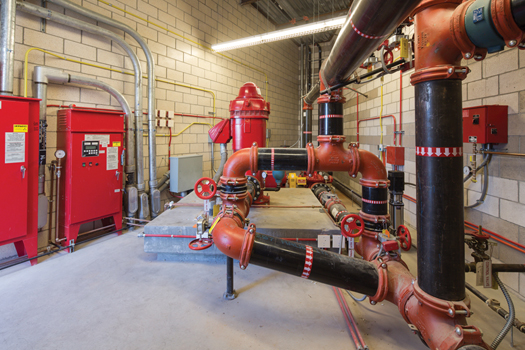
Effective fire pump installations require fire protection engineers to consider numerous components, and correctly apply a range of design and installation standards. In addition to addressing the more obvious components that comprise a fire pump installation – such as the fire pump, driver, controller, and pump room-careful attention also needs to be given to the piping leading to, from, and around the pump and the equipment associated with that piping.
While NFPA 20: Standard for the Installation of Stationary Pumps for Fire Protection serves as the principal standard addressing the sizing and installation of the associated piping, the next edition being the 2016, other codes and standards such as NFPA 13, NFPA 14, NFPA 22, NFPA 24, NFPA 25, and NFPA 291, as well as the applicable building and fire codes, also need to be reviewed and correctly applied depending on the type of fire protection systems served by the fire pump.
Suction piping
The piping connecting the water supply to the fire pump is referred to as suction piping. It comprises all piping, valves, and fittings that feed water to the pump’s suction flange. The selection and installation of such suction pipe material is addressed by NFPA 24, which specifies the use of certain types of iron, steel, concrete, plastic, and copper. In addition, NFPA 24 addresses how the pipe and fittings are to be joined together, depth of cover if the pipe is buried, protection of the pipe from freezing and other damaging events, joint restraint, and acceptance testing including flushing and hydrostatic tests.
NFPA 20 addresses the arrangement of the suction pipe and associated devices. Generally, the suction pipe and associated devices need to be arranged in such a manner so as to minimize the likelihood of turbulent and imbalanced water flow entering the pump. Such conditions decrease overall pump performance, can result in a sudden system failure and can cause premature wear of system components.
The size of the suction pipe is influenced mostly by the fire protection system’s hydraulic demand as determined in accordance with the appropriate system installation standards, such as NFPA 13 or NFPA 14, and the size of the fire pump selected. NFPA 24 provides guidance on suction pipe sizes and generally states that for any system, the pipe should be at least 6-inches in nominal diameter. Smaller pipe sizes are permitted provided hydraulic calculations verify that the pipe can supply the necessary system demand at the corresponding required pressure.
NFPA 22 provides specific guidance with regard to suction piping connecting a water tank with the fire pump. For instance, if the suction tank exceeds 100,000 gal, the size of the suction pipe must be at least 10 in. in diameter (nominal dimensions). The smaller the pipe, the faster the water flow, and therefore more turbulent flow will occur. Increasing the pipe size lowers the flow velocity and reduces the occurrence of turbulence.
NFPA 20 includes more specific provisions about suction pipe where fire pumps are installed, and specifies certain pipe sizes. The philosophy is that suction pipe be sized so that when the pump is operating at its maximum flow rate, which is 150% of its rated capacity or the maximum flow available from the water supply, the gauge pressure at the pump suction flange does not drop below -3 psi (-0.2 bar). Furthermore, the suction pipe is to be sized such that with the pump operating at 150% of its rated capacity, also referred to as pump’s overload point, the velocity in that portion of the suction pipe located within 10 pipe diameters upstream of the pump suction flange does not exceed 15 ft/sec (4.57 m/sec). Pipe flows in excess of this velocity are more prone to turbulence. Where the suction pipe differs in size from the pump suction flange, reducers or increasers are permitted to be used but must be of the eccentric tapered type and installed in such a way so as to avoid air pockets.
In addition to specifying suction pipe sizes based on the rated capacity of the fire pump, NFPA 20 also addresses other system attachments that could cause turbulent or imbalanced flow into the fire pump. Where backflow preventers or check valves are being considered, they are to be located a minimum of 10 pipe diameters from the pump suction flange. If the backflow device incorporates butterfly valves, the device is to be installed at least 50-ft from the pump’s suction flange. In fact, the 50-ft criterion applies to any valve, other than an outside screw and yoke gate valve, installed in the suction pipe.
Elbows and tees in the suction pipe also warrant special consideration. Such devices are to be located and positioned with respect to the orientation of their centerline plane. Where the centerline plane is parallel to a horizontal split-case fire pump shaft, the elbow or tee needs to be located a distance at least 10 pipe diameters from the suction flange of the fire pump. If the centerline plane is perpendicular to the horizontal split-case pump shaft, no limitations are placed on the location of the elbow or tee.
It is important to recognize that NFPA 20 only addresses the size of the suction pipe within 10 pipe diameters of the pump suction flange, while NFPA 22 addresses the size of the pipe connected to the tank. The provisions of NFPA 24 would apply where the requirements of NFPA 20 and NFPA 22 do not take precedence.
Discharge piping
NFPA 20 defines discharge pipe and equipment as the pipe, valves, and fittings that extend from the pump discharge flange to the system side of the discharge control valve. Practically, any pipe, valve or fitting downstream of the fire pump’s discharge control valve is no longer considered to be part of the discharge piping. Such pipe, valves, and fittings are considered part of the supply piping for the fire protection system being served by the fire pump. In the case of a sprinkler system riser, the requirements of NFPA 13 would apply from the point of the pump discharge control valve.
NFPA 20 addresses the size of the discharge pipe and associated fittings, and requires all of the above ground discharge piping to be composed of steel. In certain cases the discharge pipe is permitted to be smaller in diameter than the suction pipe because the water flow velocity is not of the same concern on the discharge side of the pump. The size of the discharge pipe has an effect on friction loss, but that effect can be accounted for though hydraulic analysis. As with suction pipe sizes, NFPA 20 specifies minimum discharge pipe diameters based on the capacity rating of the fire pump.
A control valve is to be installed on the discharge piping so that the pump can be isolated for service and repairs. Additional valves are discouraged to minimize the possibility that a valve will be inadvertently shut and not reopened-an ever-present concern with water-based fire protection systems. The control valve is permitted to be any type of valve listed for fire protection service, including a butterfly valve, because turbulence is not as critical on the discharge side of the pump.
A check valve is also to be installed on the discharge piping, between the fire pump and the discharge control valve. The discharge check valve traps the higher pressure in the fire protection system after the fire pump operation stops. The check valve also prevents other sources of water flow into the system, such as through a fire department connection, from flowing back into the fire pump.
NFPA 20 requires that the pressure rating of the discharge components, including all piping, fittings, and valves, be adequate for the maximum total discharge pressure with the pump operating at churn conditions at the pump’s rated speed.
Pump bypass piping
A bypass is an arrangement of piping around the fire pump that can be used to supply water to the fire protection system should the pump fail or be taken out of service. Such bypass piping is to be sized as required for the discharge pipe.
Bypass piping is required where the water supply is considered to be of “material value” to the fire protection system without the use of the fire pump. While this is a rather subjective requirement, bypass lines are usually required where the water supply is provided by a pressurized fire service main such as municipal waterworks or private fire service main. Where the water supply for the building is from a private stand-alone fixed supply such as the suction tank, a minimum pressure due to the elevation head of the stored water in the tank is available but is not usually considered to be of material value. However, this should be verified through hydraulic analysis, and needs to be confirmed with the respective authorities having jurisdiction.
A check valve needs to be installed in the bypass piping so that the flow from the pump discharge cannot recirculate back to the pump suction. Additionally, control valves need to be installed on either side of the check valve so that the check valve can be isolated for maintenance.
Pressure maintenance pump
A fire pump should operate only during fire conditions or when it is being tested. A fire pump should not be used to maintain system pressures under non-fire conditions. The activation of a fire pump provides an alarm signal as it indicates the operation of the fire protection system, and such fire pump activation under non-fire conditions would serve as a false alarm. Pressure maintenance pumps, also referred to as “jockey” pumps, are used to maintain pressures within the fire protection system under non-fire conditions.
Many water-filled fire protection systems are designed so that they are pressurized upon their installation. A system check valve serves to maintain system pressures. During a fire event, the activation of a sprinkler or the opening of a standpipe valve will cause a drop in system pressure, which will be sensed by the pressure switch in a fire pump controller. In turn, this will initiate activation of the fire pump.
Minor pressure losses can also occur downstream of the fire pump check valve under non-fire conditions. Pressure losses can occur due to water seepage across check valves or leaky fittings, or changes in system temperature. With regard to temperature, air pockets are usually trapped in the system piping. Ambient temperature changes in proximity of the fire protection system piping will cause the air pockets to fluctuate in size, thus varying the relative pressure in the system piping. A large decrease in ambient temperature in the warehouse, such as might occur in an unconditioned space over a 24-hour period, can cause a notable pressure drop, which could be sensed by the fire pump pressure switch.
Jockey pumps mitigate false alarms by compensating for small pressure fluctuations in system piping and return the system to its normal static pressure range under non-fire conditions. As with a fire pump, the jockey pump installation will include a controller with a pressure switch. The jockey pump pressure switch is normally set at a higher pressure so that the jockey pump starts before the fire pump. Note that each controller, the one for the jockey pump and the one for the fire pump, must have its own independent pressure sensing line that connects the fire protection system with the pressure switches in each controller.
Jockey pumps are high-pressure, low-flow pumps that typically cannot sustain system pressures after the activation of a single sprinkler. When a sprinkler operates or a standpipe outlet is opened, the jockey pump operates but cannot maintain adequate system pressure due to the relative high volume of water flow from an operating sprinkler or opened outlet as compared to that of a leaky fitting. The pressure within the system continues to fall until the fire pump starts and produces the required flow and pressure for the operating system.
Jockey pumps are not required as part of fire pump installation. However some means of maintaining system pressure under non-fire conditions without relying upon the fire pump as a pressure maintenance pump is needed. Jockey pumps do not require a listing as fire protection equipment. Any pump that can produce the necessary pressure is acceptable. In general, jockey pumps are sized so that their flow is lower than that expected from the smallest orifice sprinkler on the system, allowing for system pressure to fall and the fire pump to properly activate. Although jockey pumps and their controllers do not require a listing, NFPA 20 includes a number of requirements addressing their installation. As noted above, it needs to be confirmed that the jockey pump controller has a pressure-sensing line independent from that of the fire pump.
Test header and flow meter
Every fire pump installation needs to be provided with a testing means to ensure proper operation. At a minimum, arrangements must be provided to evaluate the pump at its rated condition as well as at its overload (150% of its rated capacity) condition. The means of testing must allow for the flow and discharge of significant quantities of water. NFPA 20 includes provisions for sizing the pipe used for testing. Such testing is conducted during the initial acceptance and/or commissioning of the fire pump installation, and on an annual basis in accordance with NFPA 25.
NFPA 20 allows for three different types of testing arrangements. These arrangements include the use of a discharge outlet such as a test header where water is discharged to atmosphere through connected hoses and nozzles with appropriate pressure and flow readings taken. The other two methods involve a metering device that is used to measure the flow produced by the fire pump. The metering device is installed on a pipe loop that is arranged so that the pump discharge is circulated back to the water supply tank, or arranged so that the pump discharge is circulated directly back to the suction line feeding the fire pump. This latter arrangement is referred to as closed-loop metering.
For closed-loop metering arrangements, NFPA 20 requires that an alternate means of measuring flow, such as through a test header, be provided. It is important to recognize that the alternate means of measuring flow must be installed downstream of and in series with the flow meter. NFPA 25 includes provisions that fire pump metering devices be recalibrated every 3 years. Locating the alternate means of measuring flow (test header) in the manner required by NFPA 20 facilitates this calibration activity and better ensures an accurate assessment of fire pump performance.
As noted above, a test header can be installed without the use of a metering device and loop. Located on the discharge side of the pump, the test header must be installed on an exterior wall of the pump room or pump house, or in another location outside the pump room so as to allow for adequate water discharge during testing. Hoses are connected to the test header during testing to allow for proper discharge and measurement of the water flow. Flow from the test header is usually measured by using a pitot gauge or other flow-measuring device placed in the flow stream. See NFPA 291 for further discussion on flow testing procedures. The pitot gauge registers a velocity pressure from the flow discharge, which can then be converted to a flow rate using a conversion formula or table.
The connection for the test header should be between the discharge check valve and the discharge control valve for the pump assembly. This allows the pump to be tested even when the control valve is closed, isolating the pump from the rest of the system.
The size of the pipe leading to the test header and the number of hose connections depends on the size of the pump. This is specifically addressed by NFPA 20. In the case of a 1250-gpm pump, a pipe at least 8-in. in diameter is required. The test header itself is to consist of six 2.5-in. hose valves and outlets. Where the length of pipe leading to the hose valve test header is more than 15-ft in length, the next larger pipe size as indicated in NFPA 20 is to be used.
Additionally, the pipe can be sized through the use of hydraulic calculations based on a total flow of 150% of the rated pump capacity. This hydraulic calculation is to include the friction loss for the total length of pipe plus any equivalent lengths of fittings, control valves, and hose valves, and elevation losses between the pump discharge flange and the hose valve outlets. This hydraulic calculation then needs to be verified by a flow test.
Pressure-relief device
A pressure-relief valve is a device on the discharge side of the fire pump that can be used to prevent overpressurization of the system. The pressure-relief valve operates when the pressure in the system reaches an unacceptably high level, such as may occur during an engine overspeed condition. Operation of the pressure-relief valve causes the pressure in the system to drop. One type of pressure-relief valve employs an adjustable spring-loaded mechanism. When the pressure in the system reaches a predetermined level, the system pressure overcomes the force of the spring and forces the valve open. Another type of pressure-relief valve uses a pilot operated diaphragm which forces open the valve when the pressure in the system reaches a predetermined level. With either one of these types of valves, a substantial discharge flow is expected and needs to be appropriately accounted for.
NFPA 20 allows the use of pressure-relief valves only under two conditions. The first pertains to installations involving a diesel engine pump driver. The second addresses installations involving variable speed pressure-limiting controllers for either electric motors or diesel engines. Note that if pressure-relief valves are installed, NFPA 20 places a number of restrictions on the arrangement and sizing of the relief valve discharge depending on where the discharge is piped back to. In summary, NFPA 20 does not permit the use of pressure-relief valves as a means of limiting system pressure under normal system operation conditions, that is, as a substitute for higher pressure-rated system components.
For their broad range of applications, diesel engines are designed and built to operate over a range of speeds. For the purposes of driving a fire pump, a diesel engine should run at or near its rated speed so that the fire pump produces the desired flows and pressures. However, situation scan occur in which the diesel engine operates faster than its rated speed, creating an overspeed condition that produces excessive system pressures that could cause a catastrophic system failure or shortened life of system components.
From a hydraulics theory standpoint (pump affinity laws), a small increase in fire pump or driver speed creates a substantially greater increase in system pressures, that is, the pressure developed is proportional to the square of the pumps’ rotational speed. Therefore, pumps operating at speeds in excess of their rated speed can be a cause for concern. NFPA 20 includes a number of provisions that address engine overspeed and system overpressurization.
Where the possibility for an overspeed condition of a diesel engine drive exists, and such an overspeed condition results in system pressure in excess of the pressure rating of the system components, which is typically 175 psi. Specifically, NFPA 20 requires a pressure-relief valve in the discharge piping where a total of 121% of the net rated shutoff (churn) pressure plus the maximum static suction pressure, adjusted for elevation, exceeds the pressure for which the system components are rated.
To facilitate avoidance of an engine overspeed and overpressure situation, NFPA 20 also requires the installation of an engine governor to regulate engine speed. The governor is required to be capable of limiting the maximum engine speed to 110% of its rated speed, resulting in a maximum system pressure of 121% of the fire pump churn pressure. However, failure of the governor would result in a more critical overspeed condition. As such, an overspeed shutdown device that senses the speed of the engine and shuts down the engine when it operates at a speed greater than 20% over its rated speed is also required. When the overspeed shutdown device operates, it sends a signal to the fire pump controller preventing automatic restarting of the engine until the situation is investigated. However, the pump can be manually restarted through the controller.
Another means of regulating engine speed and system overpressurization is through the use of a controller equipped with a variable speed pressure-limiting control. Such a device limits the total discharge pressure produced by the fire pump by reducing the pump driver speed, be it an electric motor or diesel engine. Prevention of overpressurization is therefore accomplished by altering the speed of the driver. However, where a variable speed pressure-limiting controller is used, and the maximum total discharge head adjusted for elevation with the pump operating at shutoff and rated speed exceeds the pressure rating of the system components, NFPA 20 requires the installation of a pressure-relief valve.
Fire pump installations are often complex and require the coordination of various pieces of mechanical and electrical equipment, as well as the correct application of several installation standards and local regulations. Proper attention must be given to not just the sizing and connection of the more obvious components such as the fire pump, controller, and driver, but also the arrangement of the associated piping and attached devices. Without a well-coordinated effort addressing all the associated aspects of the installation, the life span of the fire pump equipment can be severely reduced and, more importantly, the fire pump cannot be expected to effectively operate during its most critical time-when a fire occurs.
Milosh Puchovsky, PE, FSFPE, is professor of practice in the department of fire protection engineering at Worcester Polytechnic Institute. He is president-elect of the Society of Fire Protection Engineers, and serves on a number of NFPA Technical Committees including fire pumps and sprinkler system discharge criteria.