Three engineers discuss current trends, common challenges and important codes when designing industrial facilities.
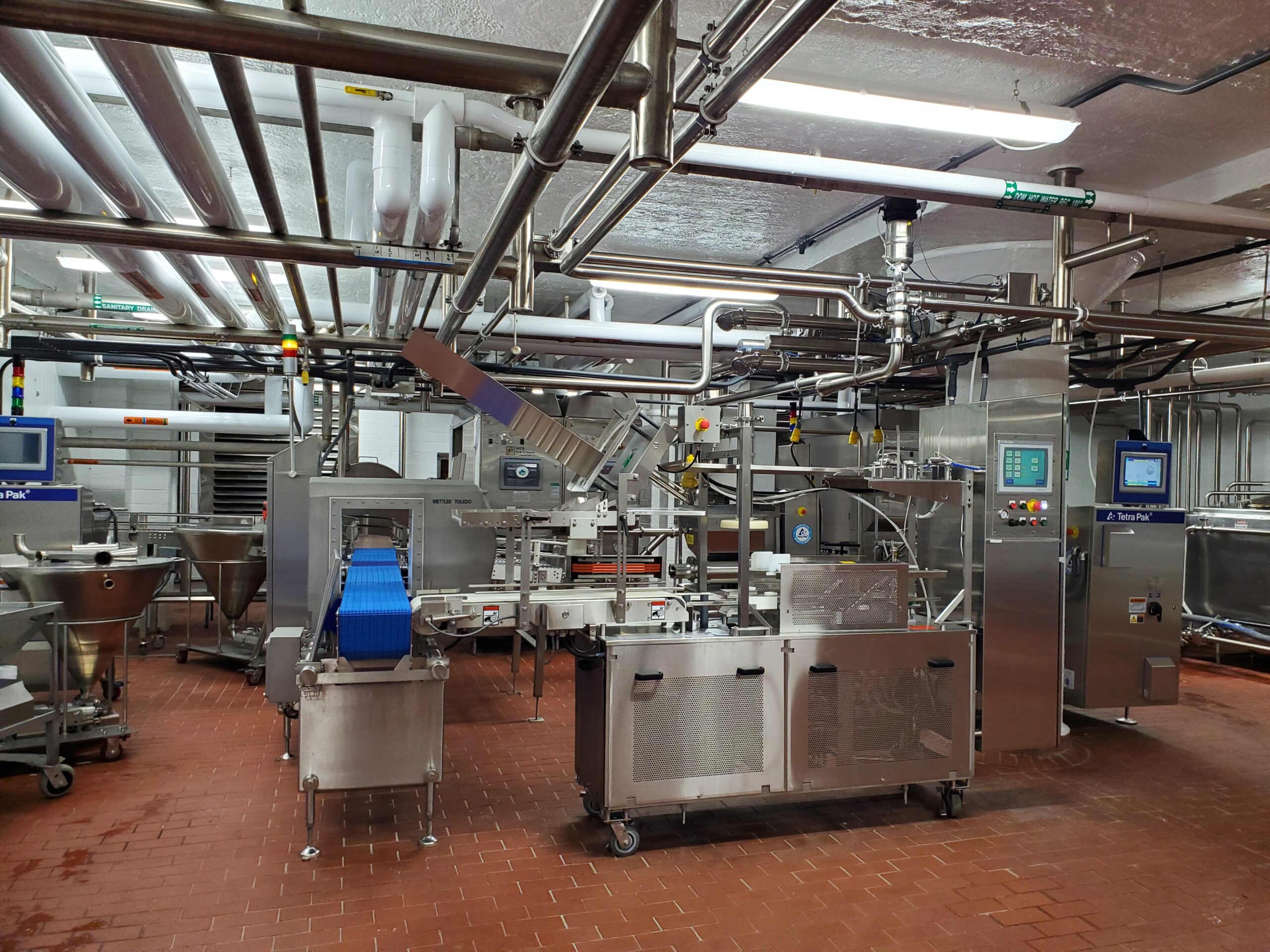
Learning objectives:
- Identify current trends driving industrial and manufacturing facility design.
- Understand how new technology like AI is changing manufacturing processes.
Industrial facility insights:
- Increased automation is driving the efficiency of manufacturing processes, changing the focus of the building’s design.
- Concerns with supply chain, tariffs and emerging technologies are speeding up the design process.
Respondents:
- Jason R. Gerke, PE, LEED AP BD+C, BCxP, Senior Design Phase Manage, JP Cullen, Milwaukee
- Jarron Gass, PE, CFPS, Fire Protection Discipline Leader, CDM Smith, Pittsburgh
- Matt Merli, PE, Principal / Client Services Director, Fitzemeyer & Tocci Associates, Inc., Woburn, Mass.
What are current trends in industrial and manufacturing facilities that engineers should be aware of?
Jarron Gass: Overall, I see a lot of effort being expended to increase efficiency, not only in the process being performed or the item being manufactured, but also in the energy efficiency of the structure. This can manifest in various ways, but increased automation is the primary method that tends to have the greatest impact on fire protection specifically. Often, automated processes introduce additional challenges for fire protection due to obstructions caused by conveyance systems or other platforms. Additionally, these facilities are growing in size beyond what the prescriptive solutions current codes offer.
Matt Merli: Certainly, the biggest trend we’re seeing right now is the advancement in robotics and automation within industrial and manufacturing facilities. For example, a client of ours that does advanced technical manufacturing has recently created a completely automated line for its process. We completed a similar line for them six or seven years ago with stations for people, whereas now it’s fully robotics with a single person monitoring at a front-end computer. For the architecture/engineering industry, this means much more electrical, compressed air and piping engineering for robotics and automation as opposed to workbench (or person-based stations).
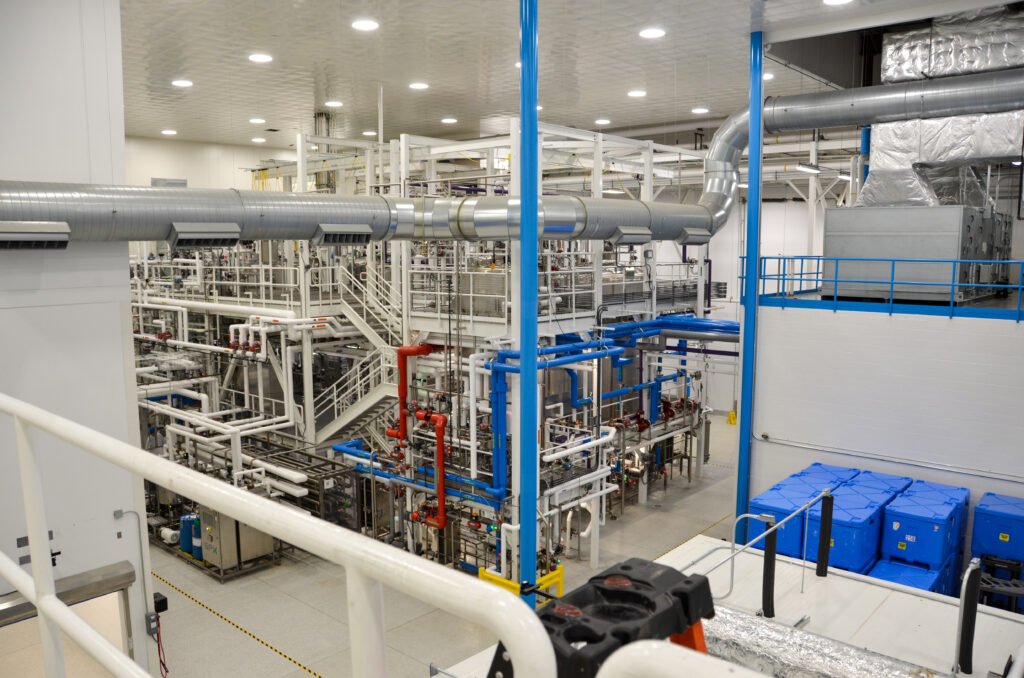
What future trends should engineers and designers expect for such projects?
Jarron Gass: I am continuing to see new challenges in safely protecting the manufacturing and storage of lithium-ion batteries. The protection of electric vehicles, personal vehicles and battery-electric buses has introduced heightened fire safety concerns, particularly within structures. At the same time, industrial chemical facilities are navigating the complexities of addressing environmental concerns related to perfluoroalkyl and polyfluoroalkyl substances. Specifically, their presence in traditional firefighting foam and the implications of modifying fire protection systems to accommodate alternative suppression solutions are large concerns.
Matt Merli: The growth of robotics, AI and automation is here to stay and only going to grow. This will also cause considerable growth in the server room and data center infrastructure. The amount of power and energy needed to support the data center growth will be immense (at the local building and grid level), which will take a lot of creative thinking and coordination with the utility.
How is the growth of immediate-delivery services impacting industrial and manufacturing facility projects?
Jarron Gass: Supply chain logistics is continually pushing the envelope to balance the cost and environmental impact of manufacturing, aiming to minimize the time and distance between each link in the chain until the product reaches the end user. This is frequently driving infrastructure to its current limits, or requiring increased capacity or the development of private infrastructure. This “last mile” focus is stretching existing systems and contributing to the creation of more mixed-use zones.
What are professionals doing to ensure such projects (both new and existing structures) meet challenges associated with emerging technologies?
Jarron Gass: While this has likely always been true, it’s especially important now to stay current with emerging technologies. One of the best ways to do this is through trade associations, engineering societies and other professional industry groups that provide opportunities to collaborate with peers. Understanding the challenges others are facing and how they’re addressed is essential for driving positive outcomes. The learning never stops, and competent engineers will continue their education through CEUs or other available means.
Matt Merli: It’s crucial to design for growth and flexibility. These companies may start with a single manufacturing line or stage, but they’re always looking to grow fast. From an infrastructure perspective, it’s important to understand the one-year, five-year and 10-year plans for the client and weigh those against upfront infrastructure cost to support that growth. Designing things like a building’s electrical service entrance, chilled water capacity and other major infrastructure for future expansion is important to these clients.
In what ways are you working with information technology experts to meet the needs and goals of an industrial or manufacturing facility?
Jarron Gass: In some of the sectors I’ve had the opportunity to work in, older plants that are upgrading and expanding their capacities are increasingly looking to integrate and network systems across multiple buildings onto a single operating platform. The goal is to unify building management systems, fire alarm, HVAC, SCADA and other automation processes. When these systems can communicate and automate functions between each other, where permitted by code, end users can increase efficiency by reducing redundancy. These types of upgrades also enable more remote control capabilities, allowing for a reduced footprint at each facility or at various stages of a given process.
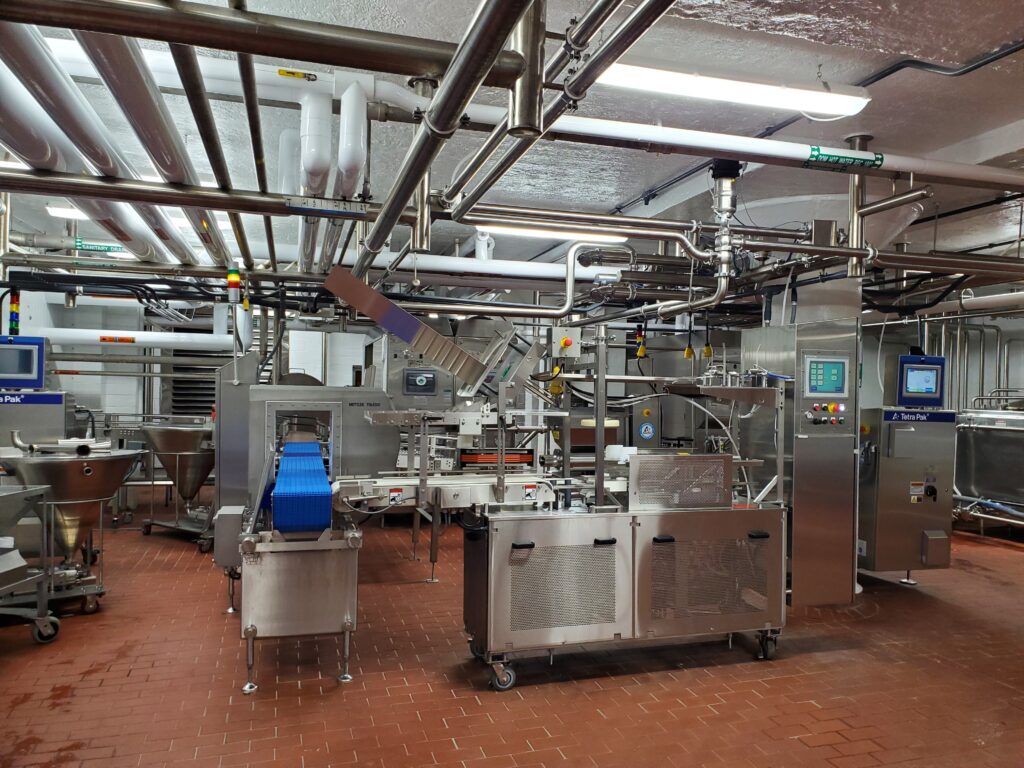
In what ways have supply chain issues impacted the industrial and manufacturing sector and how do you work with building owners to address any issues?
Jarron Gass: Supply chain issues have made planning more critical than ever, and they have driven an increased emphasis on the early identification of procurement items for projects. It’s essential to identify long-lead items that need to be designed, selected, specified or otherwise flagged as early as possible in the design process to facilitate timely procurement. On the manufacturing side, striking a balance between maintaining adequate resources or stock without running out or overstocking, which increases storage needs and costs, relies heavily on data analytics. The rise of AI is also contributing to this process, providing real-time input and forecasting. Understanding the impact these items can have on a project schedule forces earlier decisions, and often commits engineers and clients to specific choices sooner than was historically required.
Jason R. Gerke: On the construction side, we work with owners to establish allowances and contingencies for every project, whether there is a concern about tariffs or not. The primary tariff risks we are addressing on projects include steel, electrical wiring/devices and specialized equipment. We see the greatest risk for cost escalation or tariffs on any products that are manufactured outside the United States.
Matt Merli: The biggest challenge from an architecture, engineering and construction perspective is that these buildings require large infrastructure (switchgear, generators, air handling units, etc.) that are all affected by supply chain concerns. It’s important to consider this equipment as part of early procurement design packages.
Tell us about a recent project you’ve worked on that’s innovative, large-scale or otherwise noteworthy. Please tell us about the location, systems your team engineered, key players, interesting challenges or solutions and other significant details. If one is available, please link to or attach a case study or portfolio description of the project.
Matt Merli: A recent project example is a client in the advanced tech market located in New England. They have manufacturing ‘lines’ on their campus that historically had more ‘people-based’ assembly, so we’d design flexible work and cooling stations for employee comfort. The design essentially enabled people to be part of the process. They’ve now moved to robotic assembly with one person at the front-end computer monitoring the process, changing the focus of the design.
How are engineers designing these kinds of projects to keep costs down while offering appealing features, complying with relevant codes and meeting client needs?
Jarron Gass: Incorporating a value engineering process into the overall design can help analyze building features, systems and material selections to achieve greater efficiency, increase cost savings, reduce life-cycle costs or meet other predefined objectives. This approach can lead to more managed and predictable costs and processes, while still maintaining key design goals. Additionally, these efforts can guide builders to enhance efficiency and cost-effectiveness further down the line. For example, in fire suppression, a value engineering item might involve using alternative fire protection methods that eliminate the need for in-rack sprinklers or proposing alternative suppression systems in challenging environments. These alternatives can be evaluated by weighing effectiveness, component intrusion and cost, while still delivering a high-quality solution that meets or exceeds expected safety standards.
Jason R. Gerke: Our work focuses on design-build projects. It is important that design teams allow for options on materials and products. It is also important to ensure each of the trade contractors is involved in the design phase of the project. This involvement will not only allow for input on constructability, coordination and local preferences, but also on the materials and products specified. The trade contractors can give immediate information on design attributes that may increase project costs and offer suggestions on ways to reduce or control the cost to more closely align with the project budget.
What are plant owners and managers requesting from consulting engineers to make the facility more prepared for the future?
Jarron Gass: With rapidly developing and advancing technologies becoming available nearly every day, the front-end due diligence process is expanding significantly. This requires more thought, discussion and preparation for future expansions and the potential implementation of emerging technologies. Coordination and input from the design team, owners, operators and other key stakeholders are essential to developing a strategic and comprehensive plan. This plan should address the current process, potential future expansions or upgrades, optimization initiatives and sustainability goals in order to determine the full extent of impacts. For instance, should you build the entire building now and only develop a portion of the manufacturing process, adding more equipment later into the existing space, or should you build only what is currently needed and expand both the building and the process in the future?
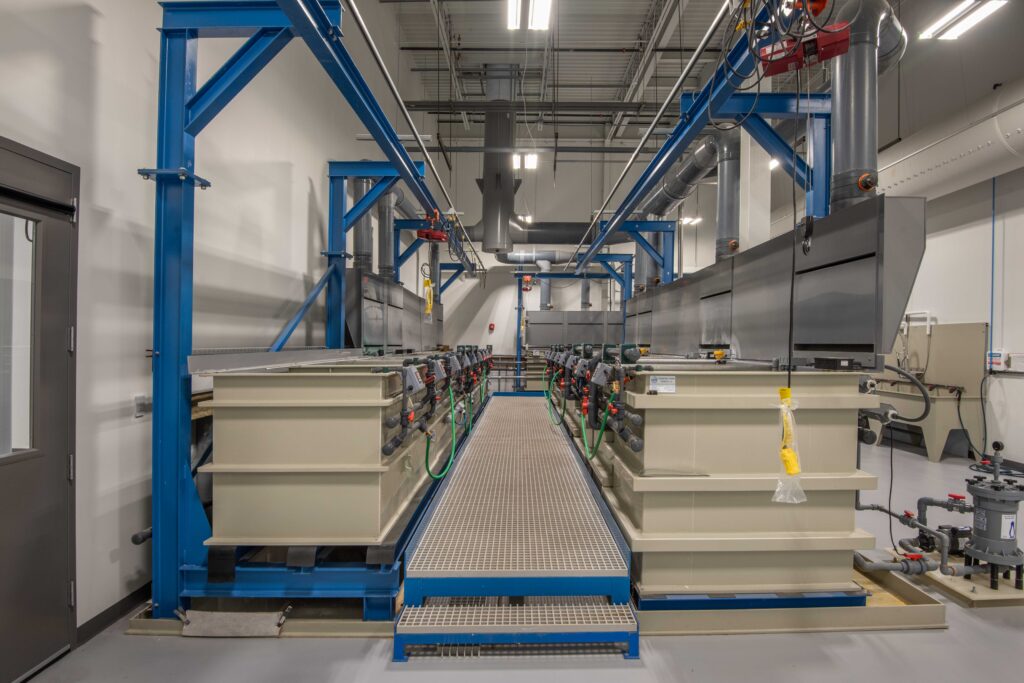
Jason R. Gerke: It is very difficult to look into the future and make an accurate prediction of building or process needs. It is important that the design team works together with the owner team and process engineers to establish the requirements for utilities early in the design phase. Estimates, assumptions and guesses must be well documented to ensure everyone is aligned with the requirements and can defend design decisions as construction progresses and process systems are started. Focused conversation around process expansions, redundancy, reliability and cost will create a future-proof facility.
Does your firm anticipate more industrial or manufacturing building projects, considering the supply chain issues with non-U.S. facilities? Describe the business development process for these clients and the re-shoring of industrial and manufacturing buildings.
Jarron Gass: Yes, there seems to be a growing push to bring manufacturing back to the U.S., particularly in the tech sector and renewable industries. The U.S. government is supporting this effort through favorable financing, expanded access to capital and increased investment in research and development. Providing greater access to funding, especially for small businesses, is crucial to developing and building the necessary infrastructure to support these new or expanded industrial and manufacturing facilities. It also enables the modernization of older facilities to meet the demands of a technology-driven economy. Domestic production can have a domino effect on the supply chain, increasing demand in various sectors, which further stimulates activity downstream. Communities with the foresight to prepare for this influx will be well-positioned to accommodate these needs and capitalize on the benefits that industry brings to the local tax base.