Manufacturing and industrial facilities can be particularly complex projects, involving large facilities containing behemoth machinery, hazardous chemicals, and a range of other concerns. Fire and life safety systems are at the forefront in these buildings.
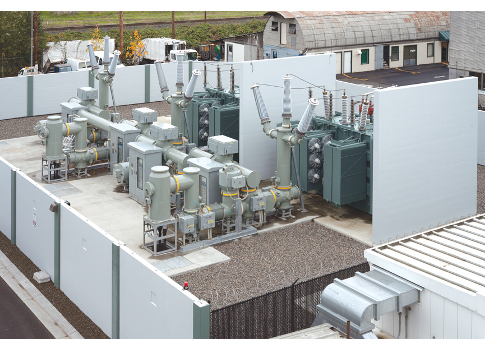
- C. Erik Larson, PE, LEED AP BD+C, Principal, Industrial Systems, Wood Harbinger, Bellevue, Wash.
- Ronald R. Regan, PE, Principal, Triad Consulting Engineers, Morris Plains, N.J.
- John Schlagetter, NCARB, PMP, CSI, CCS, CCCA, LEED Green Associate, Senior Architect, Process Plus, Cincinnati
- Wallace Sims, SET, NICET Fire Alarm Level IV, Lead Life Safety Engineer, CH2M Hill, Portland, Ore.
CSE: What unique fire suppression systems have you specified or designed in a manufacturing/industrial facility?
Schlagetter: We have specified dry chemicals for hazardous storage, deluge systems for flammable gas-using laboratory fume hoods, dry pipe preaction for controlled environment rooms, and early suppression fast response (ESFR) systems for warehouses. Piping fire suppression water to industrial equipment, such as baghouses and dryers, always poses a challenge and increased risk of accidental discharge.
Larson: Some of the most interesting fire suppression systems are associated with airplane hangars. Most hangars have a low-level aqueous film forming foam (AFFF) fire suppression system that automatically discharges foam over the entire hangar floor area. Non-water-based fire suppression systems, such as FM-200 or Inergen, are also common where very expensive equipment could be damaged if water from a sprinkler system were to come in contact.
CSE: How have the costs and complexity of fire protection systems changed in recent years?
Larson: Things are relatively constant, but there are more opportunities to design facilities that perform at least as well as a code-compliant system. Performance-based design is a concept that is really catching on—especially in industrial facilities. For example, if you have a 100-ft roof height, do you really need sprinklers at the roof? What kind of fire would it take to get that kind of heat to the ceiling? Is that even possible given the fuel loading in the building? These are all questions that need to be asked in this kind of a facility. For example, in this case, it would be better to have a VESDA that could alert a fire response team that there could be trouble. Consider what kind of trade-offs (like reduced spacing for fire hoses) might make it easier for your AHJ to accept not installing overhead sprinklers.
CSE: What type of unique smoke control solutions have you designed in these buildings? What were the challenges/solutions?
Larson: Most of the manufacturing and industrial space we design doesn’t have engineered smoke control systems, mainly because the majority of occupancy occurs well below the roof structure, and there is typically plenty of room for smoke above any occupied level. When this isn’t the case, the biggest challenge is to get everyone to agree on the design fire size. If this is off, smoke control systems can be drastically oversized because our tendency is to err on the side of caution and assume it’s going to be a big fire. Make sure you look at the real fire potential and design accordingly. New tools that are now becoming mainstream, such as computational fluid dynamics (CFD), allow the design engineer a lot more opportunity to right-size the smoke control systems, but if you don’t get the design fire size right, you’re not spending your client’s money wisely.
Sims: There has been an increasing emphasis on smoke control systems. This is a result of the need to provide a safe egress for occupants of increasingly larger facilities. Area of refuge and pressurized stairwells were a good jumping off point, but when travel distances become too great, then alternate methods need to be employed. We have employed rated tunnels with independent makeup air supply to shorten egress distances, smoke exhaust designs, and additional firewalls to segregate the smoke into smaller defined areas.
CSE: Describe a recent project in which a mass notification system (MNS) or emergency communication system (ECS) was specified. Describe the challenges and solutions.
Larson: Most of the facilities we design include some kind of MNS that is integrated with the building fire alarm system. As is the case with most of the MEP systems that building occupants will interface with, it’s critical to understand the what and where of their operation. Make sure that the interface is in the right location, and that the people who need to use it know how to. Don’t wait until the end of the project to explain how things are supposed to work. Ask your clients what their concerns are and how they’d like to see the system work before assuming you know better than they do.
Sims: I recently designed a fire alarm system that protected a tank repair facility. This client mandates that any new system incorporate MNS and further mandates which technologies to use that are compatible with the existing infrastructure. This was not as restrictive as it may sound. I still had free license to design the system of detection; it just had to employ voice evacuation and transmit two-way radio signals for alarm transmittal and notification instructions over the base-wide emergency system to the proprietarily monitoring station. In the event of an emergency situation that was not initiated by the fire alarm, the MNS signals would alert occupants with the necessary instructions that fit the situation. It was a relatively simple task to integrate the voice evacuation system and the two-way ECS because the manufacturer had provided compatibility schedules for all listed fire alarm equipment.