Net positive suction head (NPSH) is a key factor for plumbing engineers when specifying vertical turbine pumps. Learn more about the challenges of and solutions to NPSH issues.
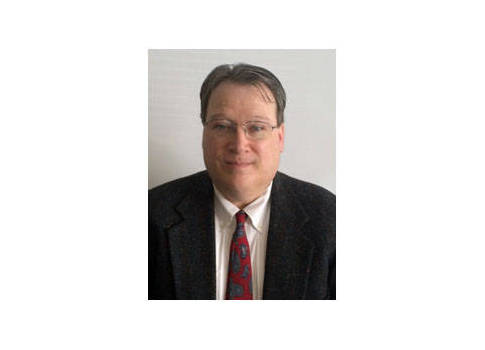
Questions not answered during the Feb. 11, 2016, webcast "Vertical Turbine NPSH" are answered here.
What water temp to use for vapor pressure in a climate that varies through the year?
I would check on a couple of things:
- What are the average highs and lows in temperature at that location through the year
- Review the 10-year, 20-year, and 50-year records. If it is acceptable to the end user or the authority having jurisdiction, plan for the worst case.
Note that hᴠᴘ for water at just above freezing is 0.089 psia or 0.2 ft and hᴠᴘ for an extreme temperature like 125°F hᴠᴘ is 1.945 psi or 4.5 ft; that is difference of 4.3 ft. In this extreme case, by adding 5 ft of hᴢ, submergence the vapor pressure issues went away.
Discuss NPSH at different elevations.
Check page 2 of the Vertical Turbine NPSH Supplement it provides the atmospheric pressure from sea level to 10,000 ft. Once you have the atmospheric pressure, add the gauge pressure (if any) to round out the há´€ absolute pressure. The rest of the NPSHa calculation follows as you would no matter what altitude.
What are some modifications or selections to improve NPSH>
As stated in the presentation, there are two ways to remedy vertical turbine NPSH: increasing NPSHa and decreasing NPSHr.
To increase NPSHa (available):
- Increase the absolute pressure (há´€)
- Enclose and pressurize an open sump
- Increase the pressure of an existing closed tank
- Increase the submergence (há´¢)
- Raise the fluid level in the sump
- Elevate the suction vessel
- Lower the pump deeper into the pumpage
- Reduce the fluid vapor pressure (há´ á´˜)
- Cool the fluid in the suction by heat exchanger or cool fluid injection
- Remove suction from a heat source (if it is in the sun – add shading)
- Reduce the suction friction losses (hÊŸ)
- Use larger suction pipe
- Add straightening vanes to inlet pipe or suction can
- Increase the straight distance from pump suction inlet to first obstruction.
To decrease NPSHr (required):
- Change to a different pump type
- Such as a double suction
- Change to a different first stage impeller
- A larger eye
- Less vanes or low capacity
- Special low NPSH first stage (check with the manufacturer)
- Change impeller material
- Some material, such as 300 series stainless will harden as it under goes cavitation
- Some material has a high foundry shrinkage rate as it cools – this produces a smaller NPSHr
- Run pumps in parallel
- Lowers NPSHr by reducing the required flow per pump
- Run at no less than 95% max impeller diameter
- Maximizing the impeller diameter increases volumetric efficiency by reducing recirculation at the impeller trailing edges
- Modify the pump (as a last resort, request the pump manufacturer make changes or risk warranty)
- Sharpen impeller leading edges
- Thin the impeller vane on the working side to open up the area (between the vanes)
- Open up the impeller eye to as large a diameter as possible
- Move all the impeller leading edges higher up inside the impeller – in a straight line from lower to upper shroud
- Neck-down the bowlshaft in impeller suction eye
Note that modification of the pump relies on increasing the suction area thus reducing the fluid velocity and NPSHr and in some cases changing the pump’s hydraulics
Effects of liquids with different specific gravities
Specific gravity (S) should have had its own table in the Vertical Turbine NPSH Supplement because of the important role it plays in NPSH. The specific gravity is a dimensionless ratio of any given fluid’s density to water density at 40°F (water’s densest point). Usually specific gravity decreases as temperature increases, for example:
- Water at 40°F has a vapor pressure of 0.122 psia and a density of 62.423 lbm/ft³
- Water at 125°F has a vapor pressure of 1.945 psia and a density of 61.631 lbm/ft³
- That means water at 125°F has a specific gravity equal to 61.631 ÷ 62.423 or 0.987 S.
Physically, specific gravity does not play a role in NPSH, so long as units are measured in feet or meters of the same fluid head. Reading 45.0 ft of NPSHr off a published pump curve, regardless if the fluid is a light hydrocarbon at 0.45 S, sea water at 1.03 S, or bromine at 3.10 S, the net positive suction head required is 100.0 ft of that fluid. However, the psi differs greatly:
- Pressure in psi = (head in ft × specific gravity) ÷ 2.31 = pressure in psi
- Light hydrocarbon = (100.0 ft × 0.45 S) ÷ 2.31 = 19.51 psi
- Seawater = (100.0 ft × 1.03 S) ÷ 2.31 = 44.65 psi
- Bromine = (100.0 ft × 3.10 S) ÷ 2.31 = 134.51 psi
Note: pump power required increases and decreases with specific gravity of the fluid
How does NPSH apply to different types of pumps (centrifugal, vertical multi-stage, etc.)? The NPSH calculations for centrifugals are virtually identical; the only thing that changes is the location and orientation of the impeller NPSH datum plane:
- For a horizontal pump
- It is the centerline of rotation for absolute pressure há´€, submergence há´¢, vapor pressure há´ á´˜; and
- The suction eye leading edges for inlet friction losses hÊŸ and velocity head há´
- For a vertical pump
- It is the plane perpendicular to the centerline of rotation at the vanes leading edges inside the impeller suction eye for all parameters
- For a vertical double suction pump
- It is the plane perpendicular to the centerline of rotation at the vanes leading edges inside the impeller top suction eye for all parameters
- For an axial (propeller) pump
- It is the suction side blade leading edges.
How do NPSH calculations change for vertical turbine pumps with a can-style suction?
All vertical turbine pumps have atmospheric pressure há´€ and submergence há´¢ as part of their NPSHa calculation, regardless if the pump is in an open sump or in a pressurized situation. However, for a can pump; the gauge pressure as part of há´€, the friction losses hÊŸ, and the velocity head há´ gains are included in the NPSHa calculations.
In wastewater application, what could cause pump to reduce the flow at the same speed and discharge head after operated for a few hours?
That is a little off our topic and it is hard to diagnose from the confines of my office, but it sounds as if your suction and clearances are being clogged or a rather quick onset of erosion/corrosion. Check into self-clearing strainers and taking a hit in efficiency by opening up running clearances and changing materials. Look at your bearings, too; hardening the shaft with fluted elastomer bearings might help also especially if you use a water flush assembly with rifle drilled shaft to keep the bearing area clean and debris free.
There is any kind of technical information about the today´s discussed topic on the Grundfos Library?
Yes, you can visit Grundfos and Peerless websites and download information, plus Consulting-Specifying Engineer and the Grundfos Technical Institute (GTI) will have an audio archive of this webinar.
How can running pumps running in parallel help NPSH issues?
If you have a single pump and at 1000 gpm the NPSHr is 100 ft, but NPSHa is 60 ft, you will not be able to operate. But you notice that at 500 gpm the NPSHr for this pump is only 40 ft. Then two pumps operating in parallel at 500 gpm each (together 1000 gpm) will only demand 40 ft NPSHr, well below the 60 ft available. In this hypothetical situation, you are able to operate.
Can you expand on the "why" as to how using different impeller materials can help increase NPSHA?
To be honest, it does not increase NPSHa.
When you go to a special material impeller or bowl, the tooling used at the foundry (if green sand cast) is usually the same tooling used to produce the standard product. However, special material has a shrinkage rate (how much a material shrinks as it cools in the tooling or casting mold) that is different from standard material, which is standard because of its easy castability. This difference in shrinkage is usually associated with a performance de-rate. If standard material produced 104 ft of head with 60.0 ft of NPSHr (or NPSH3), and let’s say that the special metallurgy selected has a 4% performance de-rate, then the new performance would be 100 ft of head and only 57.6 ft of NPSHr. This exists because NPSHr is NPSH3, which is closely tied to a pump’s performance; a lower performance yields a smaller NPSHr.
You will need to check with the pump manufacturer on whether special alloy NPSHr de-rates will apply; some pump companies have separate tooling for special metallurgy, which is designed to accommodate the different shrinkage, sometimes the selected material may actually have a better shrinkage rate than standard, or in some cases special prework is applied to an impeller to make it meet the standard NPSHr.
How much margin is usually kept between NPSHa and NPSHr for centrifugal pump selection?
That depends on the pump manufacture, but for most part the general standard is 3% (NPSH3) between the published required curve and availability.
Please provide more information: For a VLT pump with a NPSHr at -1 ft from original equipment manufacturer (OEM) using water: If the pump is used in propane service, could the NPSHr from the OEM actually be too low for propane?
I would need much more detail to adequately answer your question. And whenever one goes from pumping water to pumping a light hydrocarbon, such as propane, there are many precautions that should be taken into account for safety and pump performance.
But strictly speaking NPSH, feet are feet, whether you are pumping propane with a vapor pressure at 124.92 psia and a specific gravity of 0.498 at 70°F or mercury, which is more than 27 times heavier than propane. The main issue with propane is the high suction pressure or the very low temperature necessary to keep propane liquefied.
What is the impact of cavitation due to NPSH on the electrical power? Do I see lower amperage or higher amperage?
At the onset of cavitation, you would generally see a lot of upward fluctuation with your current. Then as the components of the pump start to wear with cavitation and vibration, you would see a steady increase in amp draw as the pump efficiency went down.
Assuming we are operating at best efficient point (BEP) for each speed, does NPSHr increase as speed increases?
Yes, but there is much debate about how much it will actually increase. ANSI/HI allows for speed adjustment of NPSHr along the same affinity as head (a square). But most hydraulic design parameters usually show an affinity relationship around 1.5 to 1.6.
Please discuss inlet vortex protection and sump dimensions
Please register for and watch the on-demand webcast (Vertical Turbine Sump Design) that deals specifically with sump design for vertical turbines. This webinar also is archived on the Grundfos training website. I highly recommend you review it—it will thoroughly answer your question.
You discussed cavitation due to entrained air. We commonly see that in cooling tower applications where NPSHA is far above NPSHR. Is there a method to predict when this will occur?
Yes, if it is due to air-laden water; one of my Grundfos colleagues gave a lecture on entrained air not too long through Consulting-Specifying Engineer’s webcast series. If it is entrained air due to vortexing. You might want to take a hard look at your sump design or if there is any above surface discharge near your sump.
Can you generally address the geometry of vertical turbine pumps suction chambers? What are some dos and don’ts or best practices in the design of these chambers?
That is beyond the scope of this webinar. I have had a couple of inquiries on this subject; maybe we could tackle this topic in a future webinar.
Is the presenter’s contact information available?
Contact Jimmy Scroggins via e-mail at [email protected]. He is a senior technical trainer at Grundfos Pumps Corp., Lubbock, Texas.