College and university building design is being driven by student needs, technology and new air quality demands
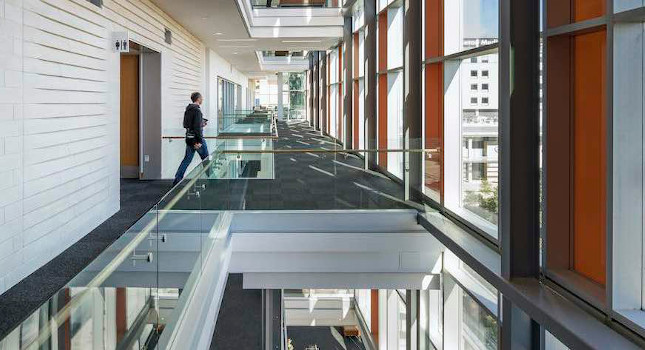
Respondents:
- Patrick McCafferty, PE, LEED AP, Associate Principal and Education Business Leader, Arup, Boston
- James Michael Parrish, PE, Associate Vice President, Department Manager Electrical, Lighting, Technology, Dewberry, Peoria, Ill.
- Tom Syvertsen, PE, LEED AP, Project Manager, Associate, Mueller Associates, Linthicum, Md.
- Kristie Tiller, PE, LEED AP, Associate, Team Leader, Lockwood Andrews & Newnam Inc. (LAN), Dallas
- Randy C. Twedt, PE, LEED AP, Associate Principal/Senior Mechanical Engineer, Page, Austin, Tex.
- Casimir Zalewski, PE, LEED AP, CPD, Principal, Stantec, Berkley, Mich.
What are some best practices to ensure that such buildings meet and exceed codes and standards?       Â
James Michael Parrish: We schedule meetings with the local AHJ and Fire Marshall on all projects. This is especially important when working in a remote state to understand nuances with local codes.
Casimir Zalewski: It is important to define the project’s code and standard requirements as early as possible. Having the expectations defined in a basis of design document and then engaging a firm’s experts to review and discuss potential implications of the project’s requirements help ensure that no expectation is missed early in the project where some of greatest low-cost impacts can be made. After this brainstorming effort, engaging the client to review the impacts of the codes and standards and receive buy in helps meet and exceed the requirements. Having technical reviews throughout the project with reference to the basis of design requirements keeps the codes and standards in focus throughout the process. For systems that require specific materials, devices or operation, the design and commissioning teams must make sure these items are clear in the construction documents. During the bidding and award process, it becomes imperative to make sure the trade professionals understand expectations. Then throughout construction, the design and construction teams need to work together to ensure the final product is constructed and operates per the original design intent.
Tom Syvertsen: It is critical to stay up to date on the latest codes and changes that occur when new codes are released and adopted. There are many industry resources including webinars and written articles that are helpful to stay current on code requirements. When possible, we gain a trusting relationship with the code reviewers. We also discuss any concerns we have on a project early and often with the owners and other project team members.
What codes or guidelines have you used to enhance the security on such a project? Â Â Â Â Â Â Â Â Â
James Michael Parrish: Our technology group is performing vulnerability assessments for clients to review any number of security issues. Many of their final recommendations can involve revisions to architecture to engineering due to the wide brush related to vulnerability.
How are codes, standards or guidelines for energy efficiency impacting the design of such projects?      Â
James Michael Parrish: The impact is the engineer needs to understand which codes are adopted for a particular job and make sure the codes are being met. We have a formal QA/QC process, which is stringent and required, which includes validating code compliance.
Kristie Tiller: Energy efficiency standards are increasing every year, which is pushing manufacturers to make more energy-efficient equipment and engineers to design more energy- efficient spaces. Such high standards, while providing long-term energy management and savings, are driving initial construction costs up. These increased costs can sometimes be offset by government incentive programs that offer rebates for high-performance buildings. This is leading to more monitoring and controls in Building Automation Systems and enhanced commissioning to verify effectiveness of energy-efficient design.
Tom Syvertsen: New versions of codes, standards and guidelines continue to raise the bar for what is considered energy efficient. What was considered an energy-efficient system 20 years ago is now a baseline system against which our new designs are compared.
Casimir Zalewski: Improved energy efficiency lends to integrated teams of design professionals focusing on early discussions of building siting, massing, materials and systems. Additionally, throughout the design process, developing clear design intent within the construction documents is paramount. There will always be a need for the trade professionals’ experience to govern the means and methods of construction, but the engineers and architects need to be clear on what is the design intent. How does the envelope system prevent infiltration? How do differing wall systems come together? How do the HVAC, lighting and plumbing systems operate at full and part loads? What are the differing control modes and integration requirements? Extremely energy efficient buildings need to minimize waste. Clear expectations for all parties are key.
Please explain some of the codes, standards and guidelines you commonly use during the project’s design process. Which codes/standards should engineers be most aware of?
James Michael Parrish: Much of our work is code driven. Even lighting design has more rules and regulations than in the past, which create restrictions, mostly with regards to energy and controls. In addition to all the NFPA codes, there are jurisdictional codes and there are design standards that every federal agency has, which must be followed.
Kristie Tiller: In addition to standard local and regional building codes, most universities also have their own Technical Design Guidelines to maintain consistency across their campuses.
Casimir Zalewski: As a global practice, one of the first steps in any project is to understand the applicable codes and standards. Building, mechanical, electrical and plumbing codes provide a typical baseline for project needs. Understanding any sustainability goals is typically part of the same discussion. Sustainable rating systems have additional requirements such as compliance with specific international ventilation and energy standards (ASHRAE 62.1 and 90.1 for example). So, whether the project is designed under base municipal codes or additional standards, it is paramount to understand all of the other referenced codes and standards such as NFPA, NEC, SMACNA, IES, ASHRAE, ANSI, ASTM for potential requirements for system quality and performance and compliance. Additionally, having a deep working knowledge of the governing energy codes/standard helps guide the project from the envelope to specifying equipment and operational requirements.
Tom Syvertsen: We start with the applicable building codes for the project’s jurisdiction–typically the International codes or the local jurisdiction’s adapted version. ASHRAE standards are supplemental to the building codes as well. It is also very important to determine at the beginning of the project whether the college or university client has their own published design standards. For example, in the Commonwealth of Virginia, its projects falling under the Division of Engineering and Buildings (DEB) umbrella and the Construction and Professional Services Manual (CPSM) is the LAW. Along with the obvious life safety concerns addressed in the CPSM, the designer’s avenue of gaining compliance with the Virginia Energy Conservation Code (VECC) is paramount. Not only is the design team expected to comply with the VECC, but they are required to explain the path they are using for compliance early in the design phase.
What new or updated code or standard do you feel will change the way such projects are designed, bid out or built? Â Â Â Â Â Â
Casimir Zalewski: Compliance with energy codes will continue to drive the design, procurement and construction process. As energy metrics will continue to become more stringent, how buildings and building systems are designed and constructed will be directly affected. The energy metrics drive where construction dollars are spent. This can be on the quantity or type of materials, how components come together or on the infrastructure required to meet performance criteria and building operations. The existing energy codes and standards already require a high level of integrated design demanding coordination in envelope development balancing cost with translation or opaqueness. While some technologies have come down in price, such as LED lighting, the increased need for energy recovery in HVAC systems still carries cost premiums. Current energy codes dictate specific automation and modes of operation again putting pressure on design and construction teams to developed cost effective strategies to meet code provisions. Current codes already require commissioning to modify the construction process. With each cycle, additional requirements from both the design and construction have been required. As design has had to move to a more integrated approach, it may only be a matter of time before design and construction are required to be more integrated.
Tom Syvertsen: There will be a greater resilience and familiarity with the International Green Construction Code (IgCC) on higher education projects moving forward.
What are some of the biggest challenges when considering code compliance and designing or working with existing buildings?
Tom Syvertsen: Sometimes it is difficult to determine which portions of code apply to an existing building renovation, depending on the project’s type and size. It is critical to make this determination early on by consulting with a code expert or the applicable code official can help avoid big issues late in the design or during the construction process. Sometimes it is difficult to incorporate code-mandated features into existing buildings because the architecture and structure were not designed to anticipate the need to accommodate particular mechanical code requirements that could come years later. For example, existing duct shafts may not have the necessary size to accommodate the addition of combination fire/smoke dampers required for a building to comply with current codes. Or when an existing AHU is replaced, the space available for new equipment and ductwork may be inadequate to accommodate energy recovery systems required by current code. The same challenge may apply to the addition of an air side economizer. The existing duct path to the outside might be sized only for minimum ventilation air, rather than for 100% outside air (much larger duct required) and there may not be space for a relief fan and a relief duct path to the outdoors. The installation could prove difficult unless major architectural and structural modifications are made to accommodate the HVAC components.
James Michael Parrish: Complying with certain codes impacts costs.
Casimir Zalewski: The buildings and systems are existing. A wall was designed and constructed a certain way, as was each element in building. There is a cost associated with each duct, pipe, conduit that must be moved or modified. Municipal and fire safety codes have changed a great deal over the years as have many of the industry design standards. The challenge that typically arises in work in existing buildings is addressing the elements from past projects. There are hidden costs of modifying these elements, such as adding firestopping to an existing wall, reinforcing structure, addressing exposed wiring, leaky ductwork, antiquated controls or fire alarm systems and even aged pipe systems. Larger challenges arise with bringing larger systems or regions of the building up to current codes especially in regards to egress, ADA or ventilation standards.