Warehouse, manufacturing and logistics facilities need engineering experts to specify various systems that meet codes and standards
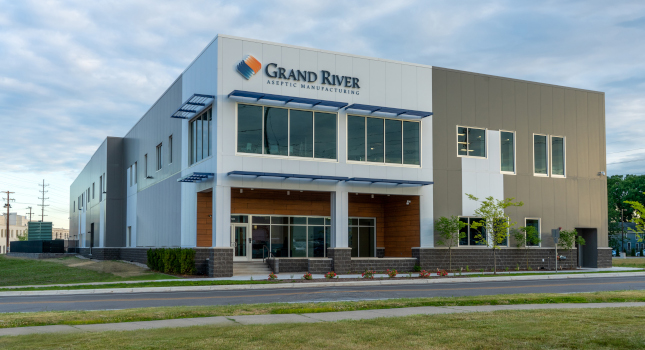
Respondents:
- Jarron Gass, PE, CFPS, Fire Protection Discipline Leader, CDM Smith, Pittsburgh
- Mike Morder, PE, CPD, Design Engineer II, Southland Industries, Dulles, Va.
- Bryce Vandas, PE, Mechanical Group Lead, CRB, St. Louis
- John Gregory Williams, PE, CEng, Vice President – Design Studio, Harris, Oakland, Calif.
Please explain some of the codes, standards and guidelines you commonly use during the project’s design process. Which codes/standards should engineers be most aware of?
Mike Morder: From an HVAC and plumbing engineering perspective, manufacturing facilities follow local codes approved in that jurisdiction. One particular item to be aware of is which version of energy guidelines/codes are applicable for your project. First cost is a large driver, so understanding the baseline energy code requirements as a starting point is critical. Also common, most large manufacturing/industrial owners have developed documents aligning to good manufacturing practices. Refer to these guidelines to make sure you are incorporating all owner requirements and meeting or exceeding the requirements for their facilities to meet a variety of performance indicators. Some of these practices may also feed into Food and Drug Administration validation or other approval processes external to the specific client. For HVAC, these practices typically include filtration requirements, air change rates and pressurization needs.
Jarron Gass: With a focus on fire protection and high piled storage requirements, typically I find myself in either the International Fire Code or NFPA 1 as the fire code and then into the various editions of NFPA 13, 20, 24 and 72 for the various types of systems required between fire suppression and alarm.
Bryce Vandas: All of the international building codes (building, mechanical, plumbing, Electrical, etc.), as well as ASHRAE 90.1. These codes and standards are used in almost every jurisdiction and are the etc. basis of most projects. NFPA is used a lot in the manufacturing industry where different ventilation requirements, safety features, fire suppression needs, etc. can be a big issue. Getting that solved upfront can dictate not only what needs to be done, but in many cases where processes can even take place or products/ingredients can be stored. It can shape your facility from the very beginning and it’s important not to get caught by them later.
What are some best practices to ensure that such buildings meet and exceed codes and standards?
Bryce Vandas: Read the codes for every project like it is the first time you read them. You may have read the codes before and consider yourself very familiar. But there is inevitably a line or section that didn’t apply to your last project that will be applicable this time around. Also, they do change. Spending the time to understand them up front can save a lot of money down the line.
Jarron Gass: For me, conducting a stakeholder meeting before commencing design to discuss project specifics and how the locally adopted codes and standards and documenting the meeting allows for all to be on the correct page.
Mike Morder: For confirming energy code compliance, you can either run an energy model simulation or use other tools such as the Department of Energy’s COMCheck to verify minimum performance is obtained. For specific owner GMP requirements, its best to have periodic reviews with the owner’s engineering team to verify all performance metrics and requirements are met. It’s also a best practice to have the owner’s subject matter experts review major equipment specifications and details for compliance.
How are codes, standards or guidelines for energy efficiency impacting the design of warehouse, manufacturing and logistics facilities?
Bryce Vandas: Energy efficiency codes, standards and guidelines have been a hot topic around manufacturing. Because the codes are written more for commercial buildings but applied to industrial facilities. A lot of the metrics and acceptance criteria specified can be very tough to meet in a straightforward manner. In many cases it pushes you to separate your manufacturing utility/HVAC systems from the rest of the building. Separate chiller systems for process and HVAC to allow for temperature reset instead of running a single system at a low temperature all year-round because a user in your process required it. You have to be willing to look at a building as a sum of its parts and get creative in making the codes work in energy heavy processes.
What new or updated code, standard, guideline organization or association do you feel will change the way such projects are designed, bid out or built?
Jarron Gass: The struggle continues to be the lag between what is being built and the ability of the codes and standards to keep up with the constantly evolving technology and building styles, particularly as builders continue to push the envelope of building taller warehouses and how we can properly protect them from a fire protection perspective.
Bryce Vandas: Energy initiatives by the owners more than any other standard or code drive how these projects are performed. There is often a lot of discussion on what needs to be done or how a standard can be met with least impact financially, spatially, maintenance, etc. However, the second a client states that they have a metric they want to meet or a corporate standard, the approach to those topics changes completely into a what is the best for us and how can we make it happen rather than a minimum standard to achieve compliance approach.
What are some of the biggest challenges when considering code compliance and designing or working with existing buildings?
Jarron Gass: Reverse engineering older buildings and construction styles from a different use group to a new use group can present a challenge for providing adequate fire protection due to various issues such as unprotected structural elements, inadequate infrastructure for fire suppression or lack of appropriately developed criteria for fire protection (sloped roofs in a high piled storage environment).
Mike Morder: Manufacturing facilities commonly expand to add more production lines and infrastructure based on market demands. Occasionally these expansions occur over multiyear projects and new scopes of work may fall under updated codes. It’s important to identify these items early and communicate them back to the team to understand the impacts associated with the change. If you have an approach that may impact typical or modularized equipment, previous specifications may no longer apply and additional infrastructure may be required.
Bryce Vandas: Understanding the effect of code compliance and how far it reaches when working in and existing building is a large portion of the issue. If I reroute a duct, does that mean that I need to update the unit? If I install a new air handling unit, do I need to update the utilities connecting to it? Once you understand the scope of what needs to be updated during a retrofit project is the biggest hurdle to getting your project and your client focused and talking about the true scope of a project.