Several new and retrofit manufacturing building projects show trends in speed to market and energy efficiency
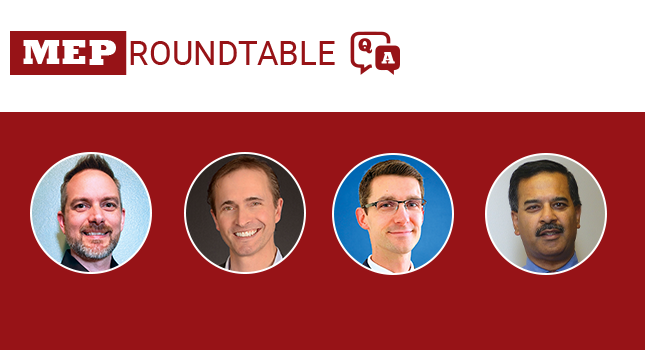
- Brian Arend, PE, LEED AP, Electrical Engineering Manager, SSOE Group, Toledo, Ohio
- Shane R. Eckman, PE, LEED AP, Vice President, Industrial & Institutional Practice Leader, Stanley Consultants Inc., Minneapolis
- Kevin LaPlante, PE, LEED AP, Mechanical Group Leader, CRB, Medford, Massachusetts
- Sunondo Roy, PE, LEED AP, Director, Design Group, Romeoville, Illinois

What’s the current trend in industrial and manufacturing facilities?
Brian Arend: The current trend is getting it done faster. We are seeing supply issues and significantly increased lead times across the board with electrical equipment. That’s pushing our clients to order sooner and squeezes the engineers to produce bid-level documents and specifications before the process is completely designed. Energy efficiency is getting a renewed focus as well. As energy prices increase, clients are taking another look at energy efficiency and how they can save on energy costs.
Shane R. Eckman: The trends that we see with our clients is toward greater energy reliability, energy efficiency and environmental stewardship. Increased energy reliability through microgrids, varied fuel sources and emergency generators to insure there are no unplanned disruptions to productivity. Energy efficiency through newer equipment and increased data-gathering (metering and sub-metering) that will give them greater information on energy/water consumption and allow them to operate their facilities more efficiently. Finally, increased sustainability through more stringent storm and process water collection and treatment and a move toward natural gas with implementation of renewal energy sources.
Kevin LaPlante: Building decarbonization and electrification have become major trends in pharmaceutical manufacturing facility design. Engineers and designers are addressing these issues in part by incorporating fully electric heating, ventilation and air conditioning and plumbing systems to serve space heating and domestic hot water needs.
The disparity between electricity and natural gas costs per unit of energy is heavily in favor of natural gas in some geographical areas. As a result, electrified buildings can have significantly higher operating costs if only traditional electric resistance heat, which has a coefficient of performance (COP) of 1.0, is employed. Many products are available that provide heating COPs far exceeding 1.0, which brings operating costs closer to parity. Dedicated heat recovery chillers, heat pump water heaters and variable refrigerant flow systems are examples of high-efficiency mechanical equipment supporting this trend.
What future trends should engineers and designers expect for such projects?
Brian Arend: A couple of things come to mind: An interconnected electrical system and modular design. Pulling in more data from the electrical system allows for fine-tuning individual pieces. That can be seen in lighting control — such as daylighting, vacancy/occupancy sensors — using smart panels and addressable fixtures. It can also be seen with power monitoring of equipment and gear. Understanding where power is being used cannot only help with targeting potential energy-saving initiatives but also with additions or changes to the process. Knowing how much load is on a substation or panel allows for construction cost savings by fully using spare capacity.
How is the growth of immediate-delivery services impacting industrial and manufacturing facility projects?
Brian Arend: The current supply change issues have tossed a monkey wrench into equipment and material lead times, impacting delivery. Clients are required to get creative to meet the process demands. Nothing is immediate anymore. We are a couple of years out before the supply chain issues resolve. We’re seeing lead times approaching a year for standard switchboard construction, with unit substations even further out. Clients are starting to relax their standards a bit to get equipment on order. We’re also seeing major delays due to the inability to secure the right equipment.
What are professionals doing to ensure such projects (both new and existing structures) meet challenges associated with emerging technologies?
Brian Arend: Historically, industrial and manufacturing clients have wanted the tried-and-true methods of design and construction to ensure a reliable system. Emerging technologies are tough to incorporate unless they are not process-related. Nonprocess related items, such as lighting and lighting control, can be easier to implement since there is no direct process impact and there can be significant energy savings.
In what ways are you working with information technology experts to meet the needs and goals of an industrial or manufacturing facility?
Sunondo Roy: Many manufacturers understand the opportunities that exist as their facilities become digital factories. However, most are a long way from truly being able to see the savings opportunities as they do not have a good infrastructure/foundation. We work with our clients and their IT teams to architect and implement a foundation that will allow them to achieve their goals. We continue to engage with them once the foundations are established to provide analytics that will help provide actionable information to the right personnel to see a direct impact on their business.
Brian Arend: Data and metadata are the words of the day. There is a tremendous amount of data out there on both the operation of industrial facilities and design of the same. There is so much information that can be pulled that it can be hard to focus on what is needed to get the work done. There’s also the question of how to find it after the fact. Using programs like Autodesk’s Revit and BIM 360 on the design side helps. It gives us a tool to organize, pull and view data. I think the next steps on the plant side are full energy profiles for process and facilities loads. By better understanding where the energy is being used, the owners can take that data and develop plans and initiatives to become more efficient.
In what ways are you helping manufacturers and suppliers deal with supply chain issues?
Shane R. Eckman: Supply chain issues are unpredictable and can impact a project at any time, therefore the ability to plan well and remain flexible throughout the design process and into construction is key. We always approach our designs with a Plan B in mind to prepare us for unexpected disruptions. That may include an alternate type of building construction (e.g., steel versus concrete), alternate products and vendors or a different design approach to accomplish the same end goal. Equally important is that we work closely with the client and contractors to keep a pulse on the construction market and identify supply chain issues and delays ahead of time that could impact the project and schedule. That valuable insight can help us avoid or at least minimize, any disruptions to the project allowing us to be proactive instead of reactive.
Brian Arend: We are getting really creative with design and coordinating closely with delivery schedules, thinking outside the normal design process and asking questions. What temporary power options are available or could be implemented? What are the process commissioning requirements? What does the commissioning schedule look like? How much can be pulled ahead and completed while waiting for final equipment? And, how do you temporarily feed process and other large equipment on a temporary basis and still meet the requirements of code? All of these questions are part of the discussion that leads to us helping clients meet their deadlines.
Kevin LaPlante: Supply chain constraints are in contest with the importance of speed to market for mission critical manufacturing facilities. These issues require innovative solutions to deliver projects on schedule and within budget. CRB’s unique approach to project delivery addresses these challenges head-on. For example, early on-boarding of trusted trade partners helps accurately gauge market conditions, identify equipment with extended lead times and establish cost certainty. With this information brought to bear, early procurement strategies can be developed and implemented for critical path items.
Prefabrication, preassembly, modularization and off-site fabrication (PPMOF) strategies are also employed to address these challenges. Implementation of PPMOF practices allows the overall project schedule to be compressed because field construction efforts can occur in parallel. Additionally, PPMOF often yields more favorable labor rates, improved safety, better quality control and increased productivity due to controlled manufacturing conditions.
Sunondo Roy: We can’t control manufacturers and suppliers, but we are assisting clients with prepurchase specifications to allow getting into the production ques. We are seeing lead-times on custom or specialty rooftop units/air handling units anywhere from 35 to 52 weeks. These lead times are adversely affecting immediate facility improvement needs and even project construction schedules that were started last year and now going into a traditional design-bid-build project delivery’s bid and build phases. These lead times are extending to on electrical switchboards and specialty process equipment, too.
How are engineers designing these kinds of projects to keep costs down while offering appealing features, complying with relevant codes and meeting client needs?
Brian Arend: The best approach to keeping costs down is collaboration between the owner, contractor and engineer. The owner knows the vision of what the end game looks like. The contractor knows cost and construction. The engineer knows equipment, code and installation. Working together leads to the best outcome for the owner.
Shane R. Eckman: First, designers need to be very familiar with the applicable codes and the available products and systems on the market, including current trends and new developments. Designers also need to approach each project with an open mind that will allow them to consider various options to address the needs of the client to determine the best solution, which may have not been the initial consideration. The key is to work as a cooperative team to bring various perspectives, expertise and new ideas.
What technologies within the manufacturing plant are you helping design?
Kevin LaPlante: Our firm designs, specifies and implements all technologies necessary to help our clients bring their products to market. Examples include design of processes, utilities and other building infrastructure to support the development of life-saving drugs and therapies. Special environmental conditions and utilities are necessary to manufacture these products without compromising their integrity, safety or occupant comfort. Precision-controlled HVAC systems maintain space temperature, humidity, pressure and total airborne particle concentrations below specified thresholds for manufacturing spaces. Central utility systems such as steam, chilled water, purified water and specialty gas systems all support various steps in the manufacturing process that lead to the final product.
Brian Arend: We are engaged in a lot of electric vehicle and battery production plants as the electric vehicle market steadily ramps up. A lot of very large auto manufacturers have been working toward this for a while, but recently we’ve seen an unprecedented increase in work in this specific market. The process and facilities designs we’re working with haven’t been done on this scale before and project teams are blazing the trail to design facilities and systems that match the owner requirements and local code. In some cases, we’re working with local officials because they don’t have any codes or standards available to them that address how these designs should perform.
Sunondo Roy: Our teams focus on general automation of manufacturing facilities from receiving, process, packaging to storage and distribution. This typically involves the latest in automation technologies with programmable logic control equipment and software designed for the plant floor. In support of these systems, we are also engaged in implementing plant floor networking, virtualization and manufacturing execution systems to provide the infrastructure to manage these systems securely and effectively.
What types of cloud, edge or fog computing requests are you getting and how do you help the owner achieve these goals?
Sunondo Roy: We are heavily involved in pulling data up to the cloud for data migration and analytics. This often includes edge-based computing to ensure data integrity and security. This comes from the plants need to transition large amounts of data/information into actionable information to more efficiently run their processes. Additionally, there is a need to pull information out to equipment suppliers so they can assist are clients with better maintenance of their equipment.
Brian Arend: We have gone all-in with Autodesk BIM 360, a cloud-based collaboration tool. While still in its infancy, it has proved to be a very powerful collaboration tool that can easily communicate the design-to-design partners whether that be the owner, a contractor or an engineering partner.
How has COVID-19 changed your work in these facility types? Has the coronavirus affected these projects, by either increasing or decreasing some aspect of them?
Brian Arend: While worker safety is always at the forefront of any operation, there seemed to be a major focus on keeping the plant personnel safe and free from COVID. This leads to more remote meetings and getting creative with design reviews and site visits. In many cases, site visits weren’t permitted. To get around that, we increased the 3D scans of the facilities we were working in. Using a program called Cintoo, we can take the scans and do a virtual walkthrough of the facilities. It’s pretty close to actually being there with the added benefit of it only taking a couple of minutes to travel there. As long as you have a good contact on-site that can chase down the occasional circuit for you, it can be a real time saver and keeps everyone safe.
What are plant owners and managers requesting from consulting engineers to make the facility more prepared for the future?
Shane R. Eckman: Clients are demanding flexibility in space programming and a responsive design team. In a dynamic economy that can have unexpected fluctuations in supply and demand, having the flexibility to increase/reduce capacity on short notice is key. That could mean being able to quickly modify an existing space to accommodate increased demand of an existing product or quickly modifying that same space to accommodate the manufacture of a new or different product. Being able to make the conversions quickly to capitalize on market opportunities requires an efficient, reliable design team that is familiar with the client and that particular facility.
Brian Arend: The main one is probably the least flashy. They want a system designed to be expandable and maintainable. As production changes, they need the ability to add new feeders, breakers, panels or other items to feed the new process equipment. Designing the equipment with spares or expandable options helps with that.
Does your firm anticipate more industrial or manufacturing building projects, considering the supply chain issues with non-U.S. facilities?
Brian Arend: We really didn’t slow down during the pandemic. Now that things have opened a bit, we’re seeing record levels of business. The supply chain issues are certainly impacting our clients’ ability to meet market demands in a way we’ve never seen before. We’re seeing a quadrupling of lead times for basic electrical gear. A lot of material that was previously a simple order-and-ship now has lead times. We’re working with our clients to help them meet production quotas and deadlines by getting creative with how we power their systems. Used or refurbished equipment used to be a no-go, but it’s now being approached from a new perspective and has a place at the table for consideration.
Shane R. Eckman: We expect more industrial and manufacturing building projects in both the near-term and foreseeable future. Regarding reshoring, the business decision to bring back manufacturing to the U.S. is up to our clients. Our job is how to work with them to address the challenges of modifying an existing plant to accommodate the relocated process. Merely adding onto the building is normally straightforward, but often the decision is made to move the process into an existing space within an existing building, a space not originally designed to accommodate that particular process.
We start by gaining a better understanding of the sister plant and the process to be replicated in the U.S.-based plant. Then we work as a team to address the challenges of fitting the process into the existing space while considering product flow, operations, utilities distribution and any physical challenges or constraints. The design process is often dynamic and involves changes throughout the design process as more information is gained and the pieces come together, reinforcing the necessity of a familiar and intuitive team developed from long-term relationships with that client.