Several new and retrofit manufacturing building projects show trends in codes and standards changing
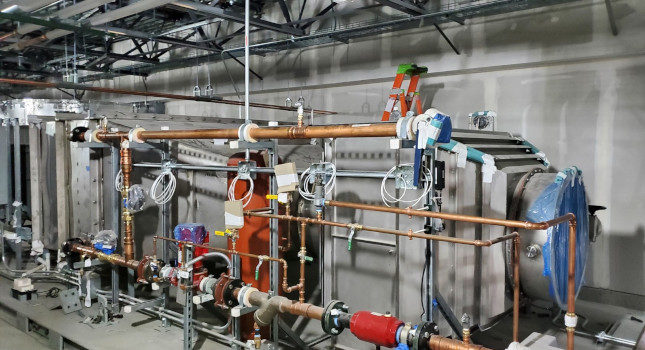
- Brian Arend, PE, LEED AP, Electrical Engineering Manager, SSOE Group, Toledo, Ohio
- Shane R. Eckman, PE, LEED AP, Vice President, Industrial & Institutional Practice Leader, Stanley Consultants Inc., Minneapolis
- Kevin LaPlante, PE, LEED AP, Mechanical Group Leader, CRB, Medford, Massachusetts
- Sunondo Roy, PE, LEED AP, Director, Design Group, Romeoville, Illinois

Which codes/standards should engineers be most aware of?
Brian Arend: On the electrical side, the NFPA 70: National Electrical Code, is by far the most used. We also routinely use NFPA 101: Life Safety Code, NFPA 70E, NESC, ASHRAE Standard 90.1: Energy Standard for Buildings Except Low-Rise Residential Buildings and IEEE color books.
Shane R. Eckman: IBC, IFC, IEBC, IECC, NFPA, Occupational Safety and Health Administration, ASHRAE, UL, state and local codes and the owners established requirements.
Sunondo Roy: NFPA 70, National Electrical Code, is obviously one of the most crucial codes with regard to electrical design in all facilities. However, for industrial and manufacturing facilities, Articles 500 through 504 are especially critical for determining Hazardous (Classified) Locations, Classes I, II and III, Divisions 1 and 2. These articles cover the requirements for electrical and electronic equipment and wiring for all voltages in locations where fire or explosion hazards may exist due to flammable gases, flammable liquid–produced vapors, combustible liquid–produced vapors, combustible dusts or ignitable fibers/flyings. Additionally, designers should be familiar with NFPA 497, Recommended Practice for the Classification of Flammable Liquids, Gases or Vapors and of Hazardous (Classified) Locations for Electrical Installations in Chemical Process Areas and NFPA 499, Recommended Practice for the Classification of Combustible Dusts and of Hazardous (Classified) Locations for Electrical Installation in Chemical Process Areas.
What are some best practices to ensure that such buildings meet and exceed codes and standards?
Shane R. Eckman: The design team must understand which codes are applicable and have a thorough understanding of those codes, including the requirements and intent of each provision, as the codes sometimes need to be interpreted. The team must also understand how the space is being used (manufacturing, storage, shipping, laboratory, etc.), layout of equipment and utilities, material and traffic flow, chemicals being used or stored, occupancy and electrical classifications, fire requirements, etc. The code requirements need to be addressed at the beginning of the project and then confirmed at the end of the design process, to ensure compliance as the requirements may have changed during the design process. Equally important is to engage the local code official early, to keep them informed of the project, identify their concerns and confirm that their interpretations of the code requirements match the design team’s.
Brian Arend: A couple come to mind, like peer reviews and quality checks. Engaging a senior engineer in a peer review in the 20% to 30% complete range cannot only validate the original design intent, but also allow for outside input and provides a mechanism for a different perspective. Quality checks before major postings is another useful tool. Having a senior engineer do a line-by-line check of the contract documents allows for a code, best practices and constructability review before the set is released for bids or permits. A side benefit of both is the lead on the project has an avenue for continuous learning.
Sunondo Roy: It is critical to understand the actual extent of the hazardous environment to ensure the special design precautions in the National Electrical Code (NEC), Articles 500 – 504, are applied correctly to the areas of hazard and not applied to areas beyond the area of the specific hazard. It is important to establish hazard boundary(ies) and create a matrix of mitigation measures to ensure the installing contractor knows that not only equipment specifically noted on the drawings, but any additional equipment, devices and wiring that may be installed in the course of construction phase adjustments comply with the applicable sections of NEC Articles 500 – 504 and the NFPA 497 and 499. Typically, it is advisable to engage a specialty firm to perform a dust hazard analysis for all locations with processes where potentially combustible dust is generated or can settle and collect.
What new or updated code, standard, guideline organization or association do you feel will change the way such projects are designed, bid out or built?
Shane R. Eckman: Sustainable design (U.S. Green Building Council/LEED) and WELL building design
What are some of the biggest challenges when considering code compliance and designing or working with existing buildings?
Shane R. Eckman: The codes are written in a way that they can be ambiguous and may require some interpretation to identify the intent. As different people have varying backgrounds, expertise and perspectives, getting everyone to agree on the intent can sometimes be a challenge. The key to addressing this challenge is to approach the code discussions with an open mind, realizing that there may be more than one correct interpretation.
Brian Arend: The loading of existing equipment needs to be carefully reviewed. NEC Article 220 requires the designer to understand the existing load before adding new load. As design professionals, we need to either calculate what that starting load is or work with the client and get metered data.