Many hospitals and health care facilities struggle to maintain temperature and humidity in operating rooms, especially as doctors are asking for lower temperature options. Three kinds of dedicated outdoor air systems can solve this challenge
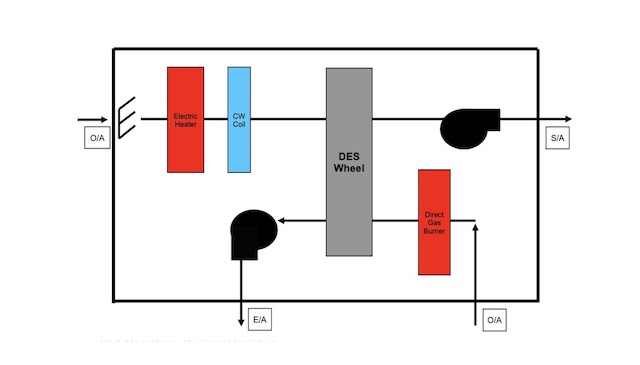
Learning Objectives
- Identify the concerns with existing systems and low-temperature operating rooms.
- Learn the different types of dedicated outdoor air system units.
- Understand how an engineer implements a dedicated outdoor air systems unit in an existing system.
Operating room insights
- The three system options when retrofitting low-temperature operating rooms are direct expansion, glycol chilled water and desiccant.
- Precise control of environmental conditions, such as maintaining a specific dewpoint, is crucial in retrofitting operating rooms.
In the realm of surgical precision and patient care, every detail within the operating room environment plays a pivotal role in ensuring successful outcomes. Temperature and humidity within the operating room stand as critical determinants of both patient safety and surgical efficacy. Surgeons and medical professionals alike understand that the delicate balance between surgical team comfort, patient safety and optimal surgical conditions hinges upon careful control of environmental variables, of which temperature is no exception.
ASHRAE Standard 170: Ventilation of Health Care Facilities dictates that the temperature range in an operating room should fall between 68 F and 75 F, but also allows for temperatures to be outside of this range for surgeon preference or surgical procedure requirements. More and more surgeons are requesting temperatures as low as 62 F in operating rooms for personal comfort reasons. This becomes difficult for existing facilities that don’t have additional measures beyond a typical heating, ventilation and air conditioning (HVAC) system required to achieve these lower temperatures.
How to create a low-temperature operating room
With the volume of air that operating rooms are normally provided, it seems simple enough to achieve temperatures lower than 68 F. However, issues often arise from the second environmental condition — relative humidity.
Space relative humidity affects multiple functions that are crucial to successful procedures in an operating room. Low relative humidity (below 20% as required by ASHRAE 170, or 30% in some jurisdictions) can lead to static electricity or desiccation of tissues, causing them to become brittle and more prone to damage during surgical manipulation. Humidifiers are required in most climates to maintain the minimum relative humidity with the high quantity of outside air provided in operating rooms. Various strategies can be used to maintain a relative humidity below the maximum of 60% allowed by ASHRAE 170.

Controlling humidity helps mitigate the risk of microbial growth and transmission within the operating room. High humidity levels can create conditions conducive to the proliferation of bacteria, viruses and fungi, which pose a significant risk of surgical site infections. By keeping humidity within recommended ranges, health care facilities can reduce the likelihood of airborne and surface-borne pathogens spreading during surgical procedures. Many medical devices and equipment used in surgical procedures are sensitive to environmental conditions, including humidity levels. Excessive humidity can damage electronic components and lead to equipment malfunction, compromising patient safety and surgical efficiency. High humidity levels may compromise the sterility of surgical instruments and supplies, increasing the risk of contamination and surgical complications.
AHRAE 170 indicates relative humidity for operating rooms must remain between 20% to 60%. These humidity requirements mean that the dewpoint of the discharge air supplied to the operating rooms must be evaluated to maintain both the room temperature setpoint and the room relative humidity setpoint.
The standard setpoint for an operating room at code recommended minimum is 68 F at 50% relative humidity. The dewpoint of this room condition is 49 F at sea level, which means that the supply air to the operating room must be at or below 49 F dewpoint.
Keeping the same dewpoint with a 62 F space, what happens to the relative humidity? At those conditions, the operating room would have a relative humidity of 62%, above the maximum allowed conditions by AHRAE 170 and most applicable codes. This is that supplemental or special systems are required to provide low-temperature operating rooms for surgeons. To achieve a 62 F temperature setpoint and 50% relative humidity, the dewpoint of the supply air to the space must be a maximum of 43° F. Typical HVAC systems deliver supply air from 49 to 52 F dewpoint and are therefore unable to meet the demand.
DOAS options for operating rooms
To aid existing systems in achieving lower space temperatures, dedicated outside air systems (DOAS) can be installed to condition and dehumidify outside air. By pretreating the outside air to below the required dewpoint, the existing mixed air system only needs to handle the sensible space load.
Three DOAS system types are generally used to pre-treat the outside air before being introduced into an existing system:
-
Direct expansion (DX).
-
Glycol chilled water.
-
Desiccant.
All three options have the capability to be placed in series in the outside air path to dehumidify outside air before being supplied to an existing HVAC unit.
DX DOAS units: These units cool outside air through the refrigeration cycle and can come as packaged units with all components integral or with the evaporator coil located in the DOAS with a separate condensing unit. It is worth mentioning here that care must be taken in selecting DX systems to achieve low leaving air temperatures. DX desiccant systems utilizing hot gas for regeneration were popular for a time, but hot gas required for regeneration may not be available in low sensible load conditions.
Glycol chilled water: Standard chilled water plants provide 42 F chilled water to air handling unit (AHU) cooling coils. This delivery temperature creates problems when attempting to cool air down to lower dewpoint temperatures. The heat transfer through the coil is unable to cool the air down to lower temperatures with standard chilled water plant supply temperatures.
Glycol can be provided with chilled water then to create a mixture that reduces the freezing point of the water to supply lower temperatures as low as 28 F. Lower temperatures achieve better efficiency for the coil, but engineers must pay attention to manufacturers’ recommendations that water temperatures below freezing can cause ice to form from condensate on the cooling coil. For this reason, 34 F is a common glycol-chilled water supply temperature with 20%-30% propylene glycol. Glycol chilled water systems require the same equipment and components as a standard chilled water system to provide glycol chilled water to AHU cooling coils.
Typically, an air-cooled chiller is provided and then pumped through a closed circuit. Based on loop length, a buffer tank may be required to maintain the manufacturer’s recommended time lag so that the glycol chilled water can provide constant water temperature back to the chiller. Glycol makeup units can also be provided to monitor and release glycol into the system to maintain a constant mixture.

Desiccant: This technology utilizes a wheel impregnated with a chemical media, typically silica, to drive moisture from one airstream to another. A desiccant wheel uses the difference in relative humidity between two airstreams to absorb moisture from a saturated airstream and move the moisture to a dry air stream. This process allows the saturated airstream to be dehumidified below the required dewpoint.
Type 2 active desiccant systems heat the incoming reactivation air to dry it out before entering the wheel, which allows the maximum absorption of moisture from the saturated air stream. This is the most common type of desiccant for retrofit applications, as it is typically a packaged unit using heating water, electric, steam or natural gas to heat the process airstream for regeneration of the media.
Type 3 desiccant systems can dehumidify the using return air, but the process may be difficult to implement in existing systems. This type is excellent when used for greenfield and expansions where return ductwork can be planned with a new unit.
Pros and cons for different DOAS types
With these three options, how does one make the decision of which to use to help an existing system? Each option has benefits and drawbacks that need to be evaluated by the engineer and facility staff to make the best decision for the facility.
DX: This system type is generally the lowest upfront cost option and simplest from a maintenance standpoint. Most facilities have staff trained in these types of units, and fewer total components need to be serviced and maintained by facility staff. While DX is typically the lowest first cost, it is also the least efficient option, with higher operating costs for the cooling provided. Attention to the existing electrical infrastructure is required to see the impact of adding the large electrical load to existing switchgear. The designer must balance the lower first cost from a mechanical side to the potential increase in electrical equipment.
There are also a few limitations with DX when cooling outside air down to the required dewpoint for lower-temperature operating rooms. Suction temperature becomes a concern when the cooling down to lower temperatures, and DX systems may not be able to achieve dewpoints around 42 F for colder rooms. As it gets cold, the coil can become frosted and iced over. Minimal loads are difficult on the compressor where the turn down of the variable speed drive is unable to maintain the low load. Hot gas bypass can be provided to help impose load on the compressor in these moments.
Glycol chilled water: This system comes in at a higher first cost than DX solutions, but has better controllability. Electronically actuated control valves modulate to maintain a specific discharge air temperature off the coil and deliver within a +/-0.5 F deadband. This type of system can easily maintain the necessary discharge air temperature for the space setpoints as low as necessary. Maintenance can become a burden as there are more components needed for glycol chilled water systems. Glycol chilled water systems with air-cooled chillers can run into similar problems at low loads. Variable speed drives on the compressors and hot gas bypass can be provided on the chiller keep load on the compressor in low load situations.
Desiccant: These systems can be very energy efficient, but may have a higher upfront cost than other DOAS options, and come with a complexity that requires special training for operators. Desiccant DOAS units can use either a variable frequency drive to modulate the desiccant wheel or maintain a constant wheel speed with bypass dampers to modulate and maintain a specific design dewpoint delivered by the unit. A desiccant DOAS unit’s energy efficiency will be dictated by the heat source used for the reactivation air. Heating water, natural gas, steam or electric can all be used to heat the air. The heating water temperature may not be high enough for reactivation temperatures if low temperature heating water is used for condensing appliances at the facility. Natural gas may not be available at the site, and pipe routing can be difficult if it must be run through occupied spaces. Central steam systems are less common in hospitals, so steam may not be readily available. Electric heat is always an option, but the amount needs to be coordinated at the electrical distribution level to see if it is feasible.
Applying DOAS units to existing systems
Now that the engineer has looked through the options and worked with the facility to decide which one is best for the facility based on upfront cost, maintainability and energy efficiency, how do they implement the DOAS into the existing system? Install the DOAS in the outside air path before it is introduced to the existing air handling unit to pretreat the outside air. The minimum outside air must flow through the DOAS system to achieve the desired dewpoint and then be supplied to the existing AHU. Pre-treated outside air can be ducted to an existing outside air duct routed to an indoor AHU or directly to the outside air louver on an exterior unit. In both situations, care should be taken if economizer cycles are provided for existing AHUs. Normal economizer operation begins at 65 F dry bulb, which will introduce humid outside air to the unit and be unable to maintain the required dewpoint mixed with the pre-treated outside air. Economizer cycles either need to be disabled, or additional programming for the economizer cycle should to be enabled once the dry bulb is below 65 F and the dewpoint is below the required for the space setpoint.

As health care engineers, the health and safety of patients must guide our recommendations and decisions. At the same time, we need to be good financial stewards for our clients.
In evaluating requested low space temperature operating rooms, especially in retrofit applications, multiple options must be evaluated based on existing utilities available, maintenance staff availability and total cost of ownership versus simplicity and upfront cost.
There is not a “one size fits all” solution to this challenge. The key is for the engineer to understand all factors and to lead the discussion with key stakeholders to help develop the right solution to what is actually a very complex engineering problem.