The most efficient mechanical system for an owner is not the one with the greatest potential to reduce energy and operational costs, but the one that is able to be easily maintained and reliably operated at its most efficient points for the life of the equipment, system and building without exceeding the capabilities of the end user.
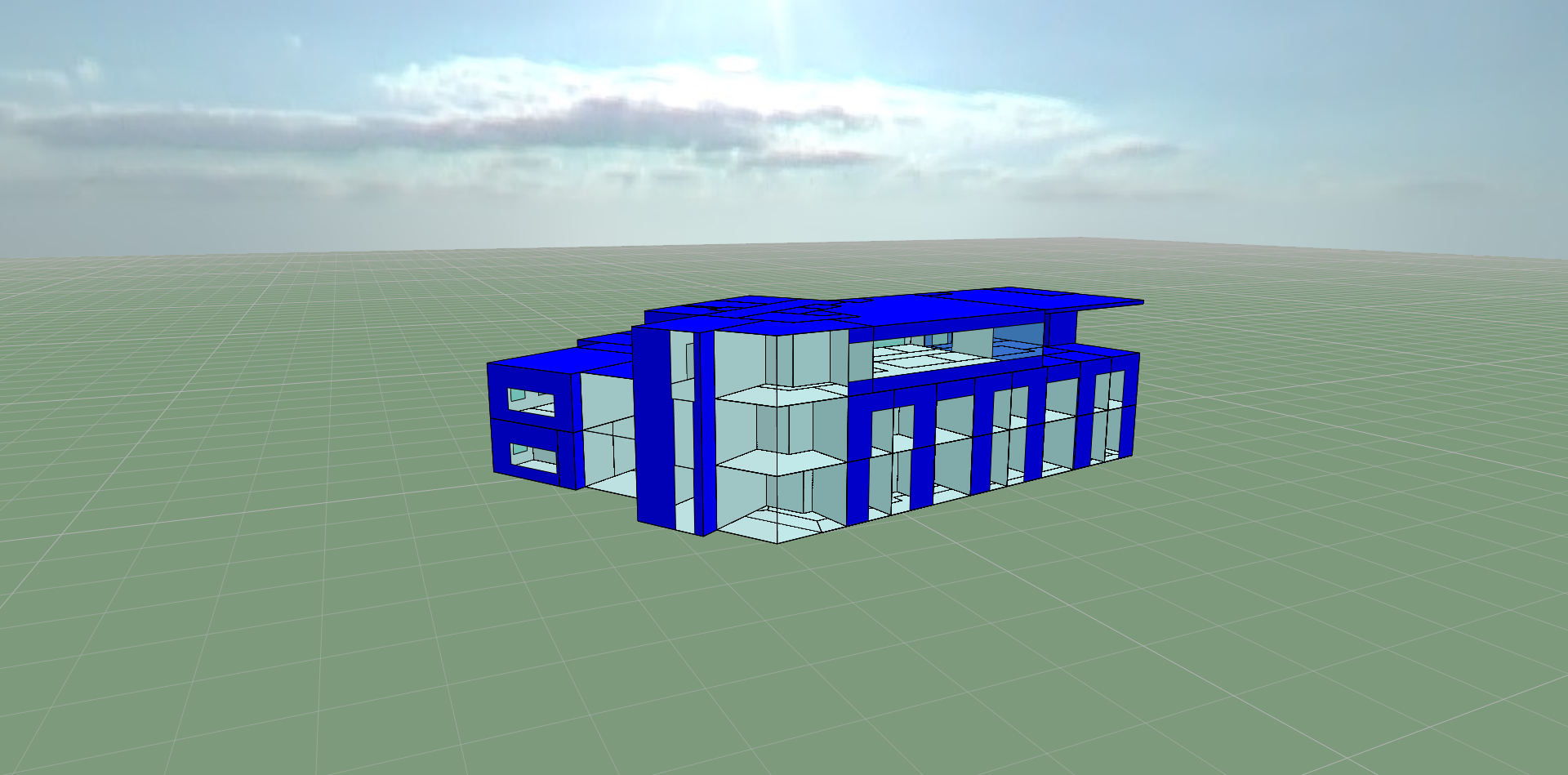
Learning objectives
- Learn the importance of setting energy conservation baselines, requirements and expectations at the beginning of a project.
- Recognize the value of communication with the owner at various personnel levels, and determining what ultimately will make a project successful.
- Know about proper owner training at the completion of the project.
The baselines, requirements and expectations for minimum energy conservation and increased efficiency within new construction and renovation/addition projects are always increasing, and design teams and engineers are constantly being challenged to surpass these efficiency expectations.
Though energy conservation can be achieved through the design and construction of the exterior envelope, lighting, water heating and power usage systems, the design and operation of a facility’s overall mechanical system is looked upon to achieve the bulk of the efficiency gains. Ultimately it is the collective design, installation, maintenance and operation of this mechanical system that determines its true efficiency, and a failure in any of these factors will result in long-term inefficiency.
The energy conservation baselines, requirements and expectations for a project are often determined from the most stringent of a variety of applicable sources, which, depending on the goals and even geographic location of the project, can be quite aggressive.
With every newly adopted edition of the International Energy Conservation Code(IECC), projects are required to comply with the increasingly rigid baseline efficiency requirements of ASHRAE Standard 90.1: Energy Standard for Buildings Except Low-Rise Residential Buildings. With the adoption of IECC 2018, projects will need to comply with the 2016 edition of ASHRAE 90.1.
Section 109 of the Energy Policy Act of 2005and Energy Independence and Security Act of 2007 requires new federal buildings to be designed 30% more efficiently than what was required by ASHRAE 90.1 standards or the IECC.
Certifying sustainability
To attain sustainable design certification, such as U.S. Green Building Council’s LEEDor Green Globes, projects must achieve credits or points based on efficiency levels.
Certain states, such as South Carolina with its South Carolina Energy Efficiency Act, Code of Laws Section 48-52-830, mandate minimum efficiency optimization requirements for new major facility projects, which include state-funded new construction building projects larger than 10,000 gross square feet and state-funded renovation projects involving more than 50% of the replacement value of the facility or a change in occupancy. South Carolina requires a major facility project earn at least 20% of the available Green Globes points for energy performance under “C.1.1 Energy Consumption” or at least 40% of the available LEED points for energy performance under “EA Credit: Optimize Energy Performance.”
Architects and agencies signing up for the Architecture 2030initiative, will be required to design new buildings and major renovations that meet a fossil fuel, greenhouse gas emitting, energy consumption performance standard of 50% of the regional (or country) average for that specific building type and be carbon-neutral by 2030.
In addition to code, law or initiative efficiency requirements, real-world capacity limitations of an owner’s distributed central energy facility can place an upper limit on a project’s demand energy usage, indirectly defining the efficiency requirements by working toward a maximum cooling or heating load.
Too often, these baselines, requirements, expectations and/or constraints force engineers to maximize system efficiency at the expense of the agency or owner by implementing overly innovative and technical designs and control strategies that ultimately become too complex or burdensome for longtime optimization over the useful life of the building. In theory, a high-performance energy model may show a mechanical design that achieves all the required or desired efficiency goals, and upon calculation a life cycle cost analysis may show a specific payback period that offsets the associated increased first capital costs, justifying its use and implementation.
However, over time, if the requirements, operation and maintenance of the system exceed the capabilities of the agency or facility personnel in charge of the building, the once highly efficient system will operate inefficiently, waste considerable energy and reduce its useful life.
Understand the owner’s needs
For instance, what if an established agency, campus or district wants to add a new 100,000 gross square feet technology building, but their existing building mechanical systems consist of dual temperature hydronic fan coils, or single zone mixed air recirculating air handling units or even a few multizone variable air volume systems with terminal reheat?
The sustainable efficiency requirements of the project mandate a 26% improvement in the proposed building performance compared to the equivalent baseline building system described in Appendix G of ASHRAE Standard 90.1. As such, the design team will need to provide a highly energy-efficient design using high-performance equipment with integral controllers, complex air-to-air and heat recovery systems and an elaborate array of internal and external automatic temperature control sensors. If the model shows the changes and additions produce a 28% improvement in performance, and the life cycle cost analysis shows a five-year payback, the efficiency goals will have been met.
However, after the building is turned over to the owner, a single unknown system operational error that requires a specific corrective action could reverse any projected gains. Because of the system’s complicated diagnostic process, the facility personnel’s unfamiliarity and/or lack of time to research or find the operation and maintenance manuals may end up performing the wrong corrective actions or, worse yet, ignore the malfunction completely. The result would be a system that no longer performs or operates as designed, becoming inefficient and negatively impacting any intended gains.
As a result, the most efficient mechanical system for an owner is not the one with the greatest potential to reduce energy and operational costs, but the one that is able to be easily maintained and reliably operated at its most efficient points for the life of the equipment, system and building without exceeding the capabilities of the end user.
Mechanical system success
In addition to right-sizing the mechanical equipment based on actual demand and selecting equipment that can suitably handle part-load conditions, the engineer and design team should consider these five actions to design and deliver a truly efficient mechanical system for the owner:
- Determine efficiency design goals
Far too often, the design team begins a project without discussing, determining or documenting the actual energy efficiency goals or target energy use intensity. The result is that the energy consumption and energy cost of the mechanical system and the building become passive byproducts of the project, secondary to many other active design goals like reduced first capital cost, reduced spatial impact, increased reliability, aesthetics or reduced maintenance.
It is critical that the team (architect, engineer and owner) analyze efficiency measures during the programming and schematic design phase of the project and define the project’s energy goals. That way, decisions about the size, shape and cost of a mechanical system that’s capable of achieving the defined goals can be incorporated into the project from the start.
A system capable of satisfying ASHRAE 90.1 will be much different from one required to achieve 40% of the LEED v4 new construction energy optimization credits (20% improvement over ASHRAE 90.1-2010). If it is determined that the costs necessary to achieve the energy targets exceeds the budget of the project, it is typically early enough to either re-examine the energy performance target or modify the budget.
- Communicate with the owner and owner’s facilities staff
Involving the owner’s facilities staff in the design process from the onset of the project is one of the most overlooked ways to avoid future complications. The owner’s decisionmaker or representative may be the one involved in determining the target energy performance, but the facilities staff will be the ones charged with operating and maintaining the new building and mechanical system. Meeting with them to discuss everything that could and should impact the mechanical system selection and design can save considerable stress later.
Items to discuss include, but are not limited to, the size and workload of the current facility staff, the various mechanical system types within existing on-site buildings, staff experience, continuing education opportunities, system/equipment preferences and familiarity with different heating, ventilation and air conditioning system types. If the staff is shorthanded or inexperienced, the result is typically a reactive approach to mechanical system maintenance rather than a proactive approach.
A reactive approach would be better suited for a more reliable, less technical system or equipment that requires less maintenance and opportunity for repairs, whereas a proactive approach might be able to handle a more complicated system or piece of equipment capable of higher efficiency gains. If a building system design is too complex for those responsible for its operation and maintenance, over time the actual EUI and costs can often be higher than a simpler system design (see Table 1).
- Incorporate an integrated design approach
It is essential for the design team to understand that energy efficiency and optimization is not the sole responsibility of the mechanical engineer, but of everyone involved. To optimize the integration of efficiency strategies across all aspects of building design, construction and operations, assign a design charrette with as many of the major team members as possible during the initial programming and pre-design phase. This will allow you to draw on the expertise of all participants during the important decision-making process.
Continue to encourage communication within the team as decisions or changes are made. A building with an energy-efficient building envelope, integrated with an efficient, right-sized mechanical system and high-efficient lighting and control system often will have a lower first cost and require less to operate and maintain, compared to a building where the components and systems were designed independent of one another.
- Perform energy modeling early in design
Don’t make the performance and energy efficiency of a building an accident. Whole-building energy simulation to check compliance, after the orientation, massing, envelope and fenestration, lighting and mechanical systems has little to no value when used late in (or after) the design process. Perform a preliminary block energy modeling analysis early in the schematic design that explores how to reduce energy loads in the proposed building.
Continue its use throughout the design to experiment with systems and architecture. This will assist in decision-making and identify the most cost-effective energy efficiency measures. The decisions derived from the results of early modeling can help keep you from missing the efficiency targets and costs associated with redesign time and/or incorporating late design strategies, providing the building owner with a more valuable final product (see Figure 1).
- Include training and O&M manuals in the contract
O&M represents one of the largest costs of operating a facility over its life span, yet it is often overlooked during the design, construction and post-construction phases. Not only is it the responsibility of the design team to design systems that will perform efficiently at the level of operation and maintenance that the owner is able to provide, it is also the responsibility of the design team to provide the necessary support for the owner’s facility staff. They need to deliver the proper system and equipment training and include the proper O&M manuals so the staff is familiar with the different components of the mechanical system and different maintenance procedures so the system performs properly.
With an increasing focus on energy costs, a greater responsibility is being placed on the design team to achieve higher levels of energy efficiency and improvement, often at the expense of the long-term life cycle of the building. By defining the energy goals at the beginning of the project, communicating with the owner’s facility staff, using an integrated design approach with energy modeling and providing the training and O&M materials necessary to maintain the long-term operation of the building, the result will be a building that is truly efficient throughout its life span.