From high-tech automation to energy-saving lighting and HVAC systems, there is more than meets the eye when it comes to warehouses and factories
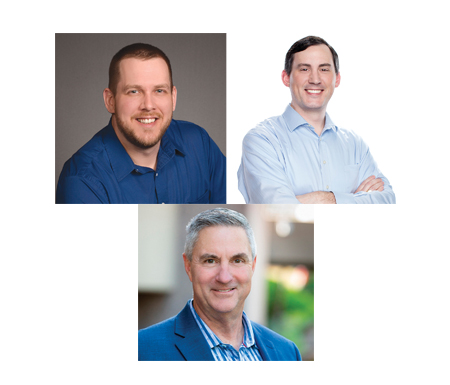
Respondents
Jason DanielsonÂ
Stanley ConsultantsÂ
As an electrical specialist, Danielson has worked on low-voltage electrical design and special systems for industrial facilities, municipal government and federal government projects. His experience encompasses designing LED lighting and lighting control systems, low-voltage power, security, communication, surveillance, access control and fire alarm systems.Â
Justin M. Harvey, PE, LEED AP BD+CÂ
Henderson EngineersÂ
As Associate/Warehouse and Distribution Practice Director, Harvey leads the company’s team on large-scale facility design to maximize supply chains for high-profile retailers. As a teenager, he was encouraged by a teacher who told him he had the skills to become a talented architectural engineer.Â
Doug Sandridge, PEÂ
RTM EngineeringÂ
Sandridge, principal, comes to RTM from Concord West, an engineering firm specializing in design, construction and management services that the firm acquired in June. His portfolio includes a number of liquor distilleries and international projects.Â
CSE: What’s the biggest trend in industrial/manufacturing facility and warehouse projects?Â
Justin M. Harvey: One of the biggest trends in the industrial/manufacturing facility and warehouse projects is the push to provide smaller warehouses in more locations closer the end users. There is such a push in many industries right now for immediate delivery of goods that companies are having to re-evaluate their position on large distribution centers and think more about regional and local hubs to serve their communities. Â
Doug Sandridge: For warehouses, it’s faster turnover resulting in lower inventory. Also, we’re seeing increased ventilation and temperature control for cold production facilities.Â
CSE: What trends do you think are on the horizon for such projects?Â
Sandridge: Technology includes auto storage and retrieval systems and energy-efficient building systems for lighting, heating, ventilation, air conditioning and refrigeration. Â
Harvey: We’re seeing more and more interest from clients on the height of their storage systems, the effects that has on the fire protection systems in their buildings. There’s also a growing focus on how evolving automated storage and retrieval systems are interacting with the ever-changing infrastructure.Â
CSE: What types of challenges do you encounter for these types of projects that you might not face on other types of structures?Â
Harvey: We are constantly coordinating lighting controls and owner-requested light levels across warehouses with the latest adopted energy codes, including the use of daylighting within these spaces. We’re helping our clients be on the forefront of this industry, investigating new methods of material handling, code review to meet the latest requirements of the owner’s insurance carriers and maximizing the owner’s budgets within the construction of their buildings through more efficient use of their required mechanical, electrical, plumbing and fire protection systems. Â
Sandridge: We see moisture control in cold storage and production facilities.Â
CSE: How are industrial/manufacturing facility and warehouse buildings being designed to be more energy efficient? Â
Jason Danielson: One of the easiest ways to reduce energy usage in a renovation is to replace the older technology light fixtures with LED and incorporate automatic lighting controls. It’s possible to reduce the total light fixture count and cut energy usage by 30% to 60% or more. With inclusion of automatic lighting controls, the energy usage can drop even further. Â
For a new design, it’s best to start with LED and a lighting control system with occupancy and daylight sensors. Many of our projects conform to ASHRAE Standard 90.1-2013, which includes requirements for separately monitoring energy usage of HVAC, interior lighting, exterior lighting and receptacle circuits. With an advanced metering system and programmable controls these energy systems can be tweaked by the end user to locate and resolve energy use issues.Â
Sandridge: We’re using destratification fans, tighter seals around loading docks and better control of overhead doors to refrigerated areas.Â
CSE: What are engineers doing to ensure such projects (both new and existing structures) meet challenges associated with emerging technologies?Â
Sandridge: They’re keeping up with regulations and new innovations is equipment and systems.Â
Harvey: Our company strives to be a part of the design team early on to help with the space planning of each building and to assist with the location and sizes of the critical systems for each project. By joining the conversation early, engineers can help the owners understand the intricacies of the adopted codes within their jurisdiction, as amendments and omissions vary from jurisdiction to jurisdiction. Having open and communicative relationships with the authorities having jurisdiction creates pathways for discussion that streamline the design and review processes and help maintain the project’s timeline. Â
CSE: Tell us about a recent project you’ve worked on that’s innovative, large-scale or otherwise noteworthy. Â
Sandridge: We used high heat makeup air equipment instead of standard gas fired makeup air units. Higher efficiency paid off the higher first cost quickly. Also, we used increased air changes to de-stratify the warehouse air.Â
CSE: How are engineers designing these kinds of projects to keep costs down while offering appealing features, complying with relevant codes and meeting client needs?Â
Harvey: As is the case with most projects, these require collaboration among the design team as well as a shared understanding of the owner’s needs and project goals. Open communication is the biggest factor that helps keep the cost of these projects down. Understanding the implications of a decision not just for the system being discussed, but how that system interacts with the other disciplines, is key to delivering a project on budget. Â
Sandridge: They’re truly understanding the owner’s criteria and vetting it in some cases (custom design versus industry norms).Â
CSE: What is the biggest challenge you come across when designing such projects? Â
Harvey: Typically, it’s the cost of the project. The engineer is rarely involved when the owner and architect are discussing the initial pricing effort on warehouse or industrial/manufacturing projects. Assumptions are made for the mechanical, electrical, plumbing and fire protection systems that typically do not consider utility or AHJ requirements and these tend to have negative effects on the budgets after the fact. It’s important for engineers to be a part of the pricing discussions early on to provide feedback on the designs. Â
Sandridge: It’s the owner’s low budget.Â
CSE: What is the typical project delivery method your firm uses when designing these a facility? Â
Sandridge: We use several methods. Design-build with our team as the lead works the best.Â
Harvey: Design-bid-build is the most common project delivery method at Henderson, with design-build a distant second. The design-bid-build approach allows Henderson to be a part of the decisions early in the design process, which helps the owner understand how their project will physically operate and what to expect during the permit process. It also allows us to provide valuable input during construction for the contractors installing the systems we designed.Â