Labs and research facilities house sensitive equipment and must maintain very rigid standards. Ventilation, air quality, and HVAC systems are discussed here.
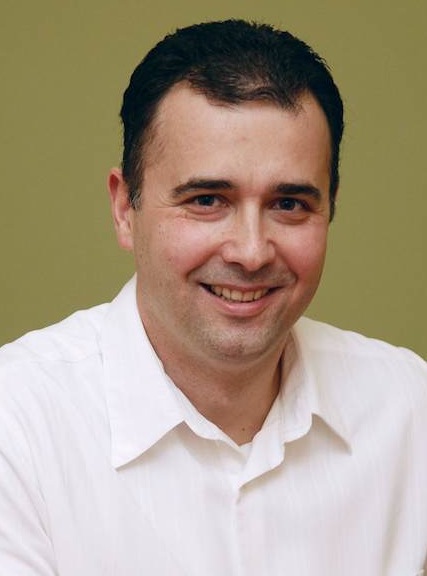
Participants:
Nedzib Biberic, PE, LEED BD+C, Mechanical Engineer, PAE Consulting Engineers, Portland, Ore.
Michael Chow, PE, CxA, LEED AP BD+C, Member/Owner, Metro CD Engineering LLC, Powell, Ohio
David S. Crutchfield, PE, LEED AP, Division Manager, RMF Engineering, Baltimore
Dave Linamen, PE, LEED AP, CEM, Vice President, Stantec, Edmonton, Alberta
Jay Ramirez, Senior Vice President, ESD Global, Chicago
CSE: What unique requirements do laboratory HVAC systems have that you wouldn’t encounter on other structures?
Biberic: The following:
- Handling of harmful chemicals.
- Requirements to maintain building spaces at different pressure with respect to each other
- Additional control systems
- Location of laboratory exhaust system (minimum equipment separation, plume height, recirculation of lab exhaust)
- Energy hog
- Redundancy of the equipment; more equipment on e-power
- Unique code and standard requirements need to be followed that some owners or even local code officials may not be very familiar with (not the same as the last project they just did).
Linamen: The primary difference with regard to HVAC is the increased requirement for makeup and exhaust air. Also, reheat energy. These requirements cascade into larger central heating and cooling requirements, as well as into increased sizes for fan systems and ductwork.
Crutchfield: The obvious is the need for single pass air, which is often confused as 100% outside air. We’ve seen that certain lab types lend themselves to single pass air that is not necessarily 100% outside air. Excess air from non-lab spaces is used to offset some of the outside makeup air and routed through labs. It is not recirculated, but rather a portion of the air to the labs is made up of return air from spaces such as offices that may have an excess of supply air.
CSE: Test facilities often dictate that a laboratory’s ventilation system contain advanced capabilities to preserve integrity of samples and keep a stable environment. How do you maintain this delicate balance?
Biberic: There are two ways: Sizing the HVAC system based on a clear understanding of the current, and by providing dedicated HVAC systems for building areas with significantly different load profiles or environment requirements; humidity, level of filtration, and tight temperature control maybe required only in few building areas, and there is no need to design the entire building system with this options.
CSE: When working in labs, how has ASHRAE Standard 62.1, Ventilation for Acceptable Indoor Air Quality, helped guide you? What challenging projects have you worked on?
Linamen: Actually, the ASHRAE ventilation standard does not provide much guidance in the design of HVAC air systems for labs. If we follow the letter of the standard, the requirement for ventilation in a science lab is approximately 2.5 ACH. There are a number of other codes, standards, and guidelines that take precedent.
Biberic: We referred to ASHRAE Standard 62.1 for prescriptive requirements on minimum separation between different types of building exhausts and minimum ventilation requirements in different general building areas. In the Whitworth Science Building, the same laboratories are used as both teaching and research spaces, each having significant differences in airflow requirements depending on the occupancy. We used the AIRCUITY monitoring system to reduce airflow rates when space air quality allows it.
CSE: Describe a challenging indoor air quality system you worked on recently. What were the challenges and solutions?
Crutchfield: We did another smoke lab where there was no place to exhaust the smoke room. We provided a special air filtration system that filters the smoke within the room. It was an interesting research project for us to design a system that will properly filter cigarette smoke.
Linamen: This isn’t necessarily related to IAQ, but we have developed an evolution of designs to eliminate snow from outdoor air intakes for lab buildings and other buildings where high percentages of outdoor air must be brought in through intakes in winter. The design involves bringing the snow in from the side of a plenum or down into an areaway, and then changing the direction of the airflow so that the last direction into the intake is vertically up. We have found that the change in direction in the upward vertical direction causes the snow to drop out. This saves saturating the filters in the air handling systems with snow in a driving snow storm. No additional energy is used to melt the snow in the intake.