Mixed-use office buildings demand a great deal of expertise, flexibility, and complex technology, making them more challenging than one might expect. Engineers with experience handling office buildings share advice and a glimpse into the future regarding codes and standards.
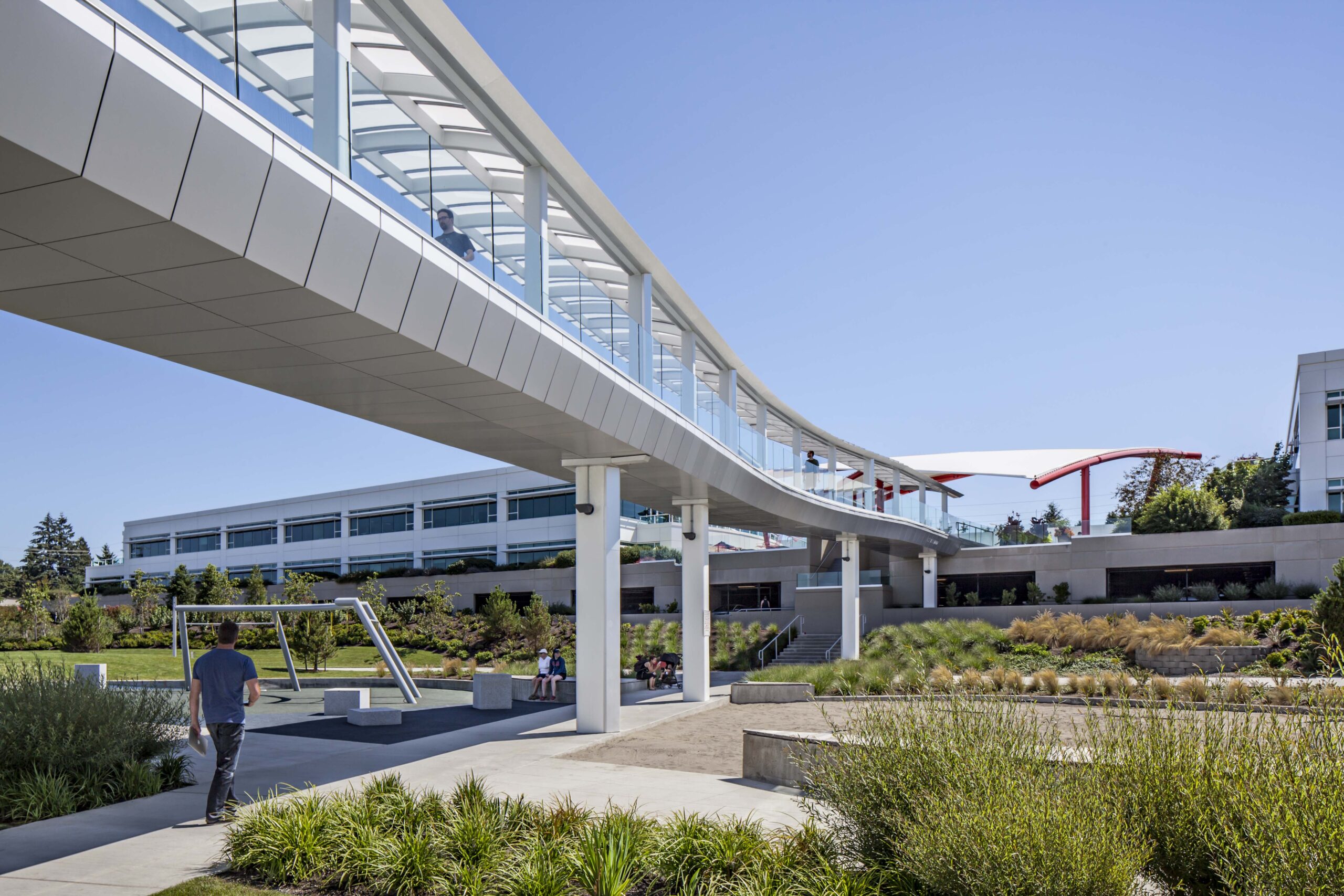
RespondentsÂ
Jason Gerke, PE, CxA, LEED AP BD+C, Mechanical & Plumbing Group Leader |, Principal, Graef, Milwaukee
Jason Majerus, PE, CEM, LEED AP, Senior Engineering Leader | Principal, DLR Group, Cleveland
Pui-Yee So, PE, LEED Green Associate, Electrical Engineer, Design Team Lead, Page, Austin, Texas
John Yoon, Lead Electrical Engineer, McGuire Engineers Inc. (MEPC), Chicago
CSE: Please explain some of the codes, standards, and guidelines you commonly use during the project’s design process for office facilities. Which codes/standards should engineers be most aware of?
Gerke: Office buildings require a number of codes and standards to be followed in the design of these spaces, specifically depending on the location of the facility. Most locations throughout the United States use the International Code Council (ICC) codes, many using the latest or second most up-to-date version of these codes. This near standard adoption of the ICC codes can make the code review of the design phase process much faster as compared with years ago when municipalities adopted a variety of codes. Besides the actual building codes, ASHRAE standards are important references. These standards may include ASHRAE 62.1: Ventilation for Acceptable Indoor Air Quality and ASHRAE 90.1: Energy Standard for Buildings Except Low-Rise Residential Buildings. While there are other ASHRAE standards that are important to reference throughout the design phase, these two for ventilation and energy are the primary system design drivers.
CSE: What are some best practices to ensure that such buildings meet and exceed codes and standards?
Gerke: A variety of software may be used to ensure a design meets the minimum code requirements, ranging from online programs that confirm building envelope compliance to multiple programs designed to model the energy consumption of a proposed building. These software programs are able to create a level of confidence that the design intent meets the requirements and provides quantitative metrics, but there are other items that are interpretations of the words written in codes and standards. This portion of the quality review phase requires using a critical thinking process that is only available through human interaction.
CSE: How are codes, standards, or guidelines for energy efficiency impacting the design of such buildings?
Gerke: The most recent version of the International Energy Conservation Code (IECC) is pushing HVAC design to a higher level. Old standby solutions that could get a system designer around some of the requirements are going away. Control system calibration and feedback in the specifications, commissioning of systems, and more strict efficiency requirements for equipment are pushing beyond what may be considered industry-standard solutions. These requirements will result in new system configurations and additional time required for control system designs, and functional testing of many systems may add time to the design and construction close-out phase of projects.
Yoon: In our experience, the greatest code-related challenges are in regard to compliance with the prevailing energy-conservation code. While those codes are often adopted on a statewide basis, the level of enforcement at a local jurisdictional level is wildly inconsistent. The downsizing trend has also hit many municipal building-inspection departments, which means that they frequently have their hands full just trying to enforce basic health and safety codes. As a result, review for energy code compliance is often perceived as an inconvenience that can be ignored. This may mean that although you are required to design to that prevailing energy code, the standard practice in a particular jurisdiction may be something considerably less due to lack of enforcement.
CSE: What new or updated code or standard do you feel will change the way such projects are designed, bid out, or built?
Gerke: The biggest driver that will affect our current design practices is related to energy efficiency and the requirements in the IECC. This code will have an impact on decisions in the design phase as well as in the commissioning that is required on many/most projects. In the past, commissioning has been an option, but the latest versions of the codes are making it a standard requirement.
CSE: What are some of the biggest challenges when considering code compliance and designing or working with existing office facilities?Â
Yoon: To control construction costs, we are often directed to salvage as much of the existing MEP infrastructure as possible. While that infrastructure might still be perfectly serviceable, it may not be able to meet a current code—and usually, that code is the energy code. For example, how do you cost-effectively perform demand-control ventilation in high-density rooms when the building only has pneumatic controls? Or, how do you convince a client to replace several floors of three-lamp, T8 troffers because you crossed the 10% grandfathering threshold and the installation exceeds the allowable power density?
Gerke: Challenges in existing buildings may be extensive, especially when there is a significant modification planned in the building that does not change the use of the building. Remodeling or renovation projects are often judged on the level of complexity and total area affected to determine the level of alteration according to the International Existing Building Code (IEBC). While it is important that system designs comply with the IEBC, another major complication working in these buildings is the need to comply with codes and not necessitate major modifications to existing envelope systems. We have seen situations where additional energy modeling or higher levels of efficiency are required in HVAC systems to avoid more costly changes to building façade systems.
CSE: What are some of the unique challenges regarding fire/life safety system design that you’ve encountered for such projects? How have you overcome these challenges?
Yoon: One life safety design issue relates to the integration of newer BAS technologies with fire alarm systems for smoke management in high-rise office buildings. BAS devices that are directly associated with smoke management are required to be UL 864/UUKL-certified. This listing extends to other required devices, which may include Ethernet switches, surge suppression, and other devices associated with the supervision and control of the smoke-management equipment. Compliance is relatively straightforward with more traditional, proprietary BAS topologies. However, this can be a significant hurdle when using cutting-edge technologies, such as devices communicating using wireless mesh networks, IoT devices, etc. The solution usually ends up being less than ideal: a hybrid system. While emerging technologies may seem to offer endless flexibility as compared with traditional solutions, be aware that life safety requirements can significantly limit their application.