Understand the design and application of condensing boilers and heating water systems
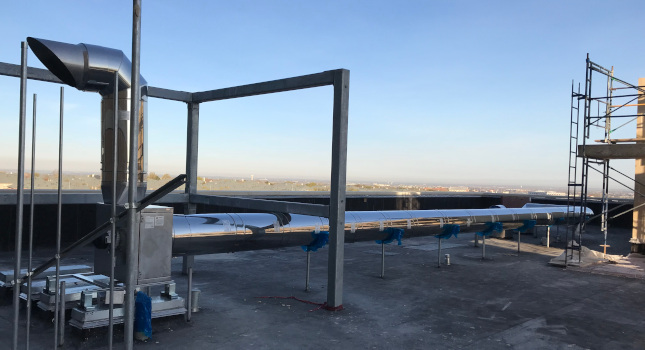
Learning Objectives
- Learn about boiler definitions and applications in building systems.
- Understand applicable codes and standards that govern heating systems and boiler design.
- Review the basic parameters that govern a heating system design, building loads and condensing type boilers.
Boilers can be thought of as encased heat exchangers with a primary goal to increase the temperature of the fluid in question a given delta above design setpoint. These robust pieces of equipment are built and constructed to The American Society of Mechanical Engineers Boiler and Pressure Vessel Code, which takes into consideration both exterior and interior construction material, size of the equipment, temperature and pressure.
This code includes several sections; in particular, section IV provides guidelines for heating water boilers and section VI focuses on care an operation of heating boilers. Inside the boiler, heat exchange occurs through combustion which is a reaction between the fuel and oxygen; a simplified stochiometric equation for combustion would look like:
Fuel + O2 → CO2 + H2O
Below are a few common fuel sources for boilers, as well as their heating values, per ASHRAE Handbook Fundamentals: Chapter 28 Combustion and Fuels:
- Natural gas HV (23,900 Btu/pound)
- Diesel HV (19,300 Btu/pound)
- Propane HV (21,669 Btu/pound)

Boiler code and design
Some boilers are specified as dual fuel, with natural gas as the primary fuel source and either diesel or propane as the secondary fuel source. Engineers specify boilers to serve various systems and/or processes, depending on the goal. Boilers specified in central plants deliver hot water for heating, ventilation and air conditioning, or domestic or process use.
Boilers are most often specified when designing new buildings such as a greenfield site, which is undeveloped land, or when retrofitting an existing central energy plant.
To begin with, the design engineer needs to know the building location and the weather design day criteria as indicated under the ASHRAE Handbook: Fundamentals, Chapter 14 Climatic Design Information. Second, the building occupancy type, which is dictated by the International Building Code and adopted by the state where the project is being designed, the central plant location with respect to the building it serves and the boiler room within the central plant.
All of the above, in addition to the floor plan layout, provides the design engineer parameters to perform the building load calculation including building envelope heat loss, building occupancy, system distribution losses and equipment load.
For example, a building of occupancy type I2 is a hospital as indicated in IBC; therefore, code requirements regarding air changes per hour for specific room types as well as room temperature and relative humidity boundaries need to be satisfied. The total load calculation is expressed in either British thermal unit per hour (Btu/hour) or 1,000 British thermal units per hour (MBH). Once calculated, the number of boiler’s are selected along with the system temperatures to meet the building demand.
Third, the central plant location affects how engineers design the optimal pumping arrangement. This may either be variable-primary where the flow varies as the differential pressure in the loop remains constant, or primary-secondary where there are two piping loops. The primary pumps serve the major equipment within the central plant and the secondary pumps serve the distribution to the building air handlers, fan coil units and variable air boxes.
To optimize the design, the engineer must weigh the benefits between pump energy consumption and a design set temperature difference; since the total building load (Q Btu/hour) = 500 (constant) * gallons/minute * temperature difference (°F).
Note that the constant considers the fluid weight, in this case water (specific gravity ~1.0), 8.34 pounds/gallon and unit conversion, 60 minutes/hour.
The International Code Council and NFPA provide codes and standards for engineers to design buildings with safety in mind.
International Building Code focuses effort on providing minimum criteria for building design and construction depending on the occupancy type.
- Section 509.1: Provides guidelines for boiler room boundaries and/or wall requirements regarding the separation to other rooms under Section 509.1 Table 509 Incidental Uses; room shall be 1-hour fire rated or provide automatic sprinkler.
- Section 1006.2.2: Regarding boilers, this code provides guidelines for means of egress based on the room usage.
NFPA 101: Life Safety Code is all about building and occupant safety.
Chapter 7, Means of Egress: Section 7.13 Mechanical Equipment rooms, boiler rooms and furnace rooms.
- Chapter 8.7, Special Hazard Protection: Provides guidelines on room boundaries and wall type construction, either 1-hour fire barrier or fully sprinklered room.
- Chapter 18, new health care occupancy section:
- Section 18.3.2: Protection from hazards.
- Section 18.3.2.1: Provide guidelines on identifying which are hazard room. Boilers, due to their combustion characteristic, follow in this path.

International Mechanical Code: Chapter 10, Boilers, Water Heaters and Pressure Vessels provides guidelines, which are required for boiler construction under ASME Boiler and Pressure Vessel Code as well as controls and safety devices depending on boiler rated MBH. The break line is < 12.5 million Btu/hour. If the boiler is larger than the value indicated above it must comply with NFPA 85: Boiler and Combustion Systems Hazards Code.
- Maintenance must be kept in mind and the manufacturer recommendations must be verified before installation.
- Provide safety relief valves, refer to detail.
- Provide a low water cutoff.
- Heating water systems must be provided with an expansion tank either open or closed type.
- Boiler shall be provided with a temperature and pressure gauges.
- Condensing boiler flue or stack is typically specified of noncorrosive material such as stainless steel, due to the acidity of the water.
- The design engineer must consider boiler location within the room to ensure compliance with IMC for required distances to outside air intakes.
- For safety and equipment functionality boilers come with lower water cut off and are provided with safety valves.
NFPA 85: Boiler and Combustion Systems Hazards Code provides guidelines for gas and oil fuel startup. This code is also applicable to boilers exceeding 12.5 million Btu/hour as referenced above.
State boiler code: The design engineer should verify if the state of the project in question provides any additional guidelines that may exceed the current International Code Council adopted. The Texas Boiler Code has included requirements for carbon monoxide monitor and controls for boiler room design.

Boiler ventilation
IFG 2018: International Fuel Gas Code is probably the most important code for the design engineer because it involves combustion air. The boiler produces heat due to a reaction therefore, the need to introduce outside by either natural or mechanical means is necessary to complete the process of combustion. One focus of this code is to provide guidance for preventing either flue gases or fuel leakage into the building.
There are various ways to design a boiler room:
Natural ventilation
Indoor air: May be achieved provided the cubic feet of air as indicated in Section 304 of the International Fuel Gas Code is met. This option allows to introduce the air either from the same level adjacent spaces or from higher levels provided there is a duct that introduces the volume of air to the space.
Outdoor air: May be brought either through horizontal or vertical openings or vertical opening under Section 304 from the International Fuel Gas Code.
Combination: May be brought portion from outdoor and portion room indoor.

Mechanical (force draft)
Rates are indicated under the same section, and the engineer must consider all equipment inside the room to calculate the volume of air required. Makeup air should also be considered as well as interlock of the equipment and the fan. See Figures 2 and 3 for each option for schematic purposes.
Condensing type boilers
Condensing type boilers have become more popular in the past 15 years. The combustion reaction within the boiler has a byproduct, CO2 + H2O. This means that water must develop somewhere and water condenses in the boiler stack or flue due to the dew point temperature in the stack. This is latent heat of vaporization.
This water is very corrosive in nature with a pH of 3 to 4, therefore, condensing boilers are typically stainless steel or another noncorrosive material. In addition, a condensing boiler is always specified with a “neutralization kit.” The neutralization kit includes limestone media, which raises the pH level of the condensate. The kit is installed inline to the drainpipe from the boiler and before the discharge to the floor drain. Discharging condensate directly to the floor drain will deteriorate and corrode the floor drain in a short time and it is not compliant with code in most jurisdictions.
Condensing boilers are designed with lower return water temperatures to the boilers. Typically, with return water temperature below (<130°F). Condensation will start developing in the exhaust stack. This condensate contributes to the systems higher efficiency by recovering the latent heat of vaporization and reducing waste heat. The lower the return water temperature, the more efficiency will be obtained from the boiler system because more heat is extracted from the flue gases.
Condensing boilers provide other advantages such as smaller compact footprints when compared to the noncondensing larger steel boilers. In addition, new technology includes smaller and more efficient heat exchangers within the boiler that make the heat transfer optimal. Another benefit is the turn-down ratio. Some boilers may provide a 25:5 turn-down ratio. The points mentioned above may vary per manufacturer; therefore, always consult with the basis of design manufacturer

Design parameters
Design parameters for heating water systems vary per project. For example, a system design with 130°F,maximum leaving system hot water design, and 100°F,minimum return water system design, most often includes a heat pump chiller. In summary, these lower water design temperatures take advantage of free heat from the condenser side on the heat pump chiller; with the lower heating water return temperatures.
Other systems focus mostly on a design of 150°F/120°F; in addition, these systems can take advantage of the return water temperature to preheat the domestic incoming water with a heat exchanger to the domestic side. Consequently, the lower return water temperature to the boiler assists with boiler efficiency operation.
When designing new hospitals or data centers, it is important for the engineer to discuss with the owner about equipment redundancy, which is typically provided for these types of facilities. This is often referred to as N+1. Redundancy may be specified at the equipment level for both water and air side.
The peak building load that must be satisfied on design day is the load if the building were to peak at the same time. However, in reality, load varies during the day therefore, the design engineer takes into account the building load profile throughout the entire year to optimize the equipment size and selection.
Boiler controls
Most boiler manufacturers include integrated controls and a master panel that can set boiler sequencing and designate a lead boiler. The lead boiler may rotate every month, for example, or at a preset time frame. This evens out wear and tear of the equipment. There are several strategies for boiler operation when the central energy plant includes more than one boiler. For example, one boiler may fire and carry a larger percent of the building load or two boilers may run at a lower firing rate to meet the building demand.
In summary, when designing and specifying boilers for heating water systems it is very important to research and study the codes and standards. In the United Sates, each county, municipality and state have authorities having jurisdiction that implement building codes. Some states may have amendments to current codes adopted that may exceed the minimum requirements.