Learn the nuances of a chiller energy optimization system operates contrasted with a building automation system
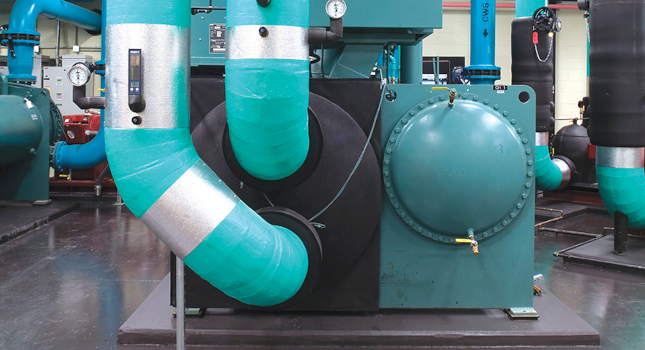
Learning Objectives
- Explain the nuances and specifics between how a chiller energy optimization system and a building automation system operates.
- Understand the relationship between a chiller energy optimization system and BAS.
- Understand when a chiller optimization system could provide value to a facility.
Chilled water systems are a significant portion of a building’s energy use, sometimes accounting for up to 40% of peak electric demand and 15% to 25% of annual electrical energy usage for a large building. As such, efforts to reduce the amount of energy used by a chilled water system are worthwhile.
Control sequences in the building automation system are written to identify and respond to variables that impact chilled water system energy. Engineers write and BAS vendors implement control sequences that are intended to meet the system demand, operate within safe parameters, protect the equipment and perform those tasks as efficiently as possible within the capability of the BAS.
Another software tool for controlling system operation is a chiller energy optimization system. Consulting engineers hear from the chiller vendors that the chiller not only meets system demand and protects the equipment, but does so more efficiently. They also hear from many BAS vendors, “We can do that.”
What’s the difference? And is a separate chiller energy optimization system worth the investment?
Typical BAS control
In a simple overview, a BAS comprises several levels:
- Management level: Makes systemwide adjustments from external input, provides user interface.
- Control level: Receives input, sends instruction to output devices based on the control loops.
- Application level: The sensors, transmitters and devices that measure input and apply output.
The sequences are written to measure an input, make a decision, then instruct the output to be implemented. Each sequence for a control loop is focused on one or a few variables and one output. For example: If the building chilled water demand exceeds 90% of operating chillers capacity or the chilled water supply temperature exceeds setpoint for five minutes, next lag chiller shall be started.
In this example, the BAS monitors two variables, chilled water system demand and supply temperature. The BAS compares the current values to the maximum operating capacity and chilled water temperature setpoints then, if either condition is true, the BAS initiates one output (start next chiller).
There are many other control loops operating simultaneously that are monitoring and controlling the chilled water pumps, the condenser water pumps, cooling tower fans, valve positions, water temperature setpoints and pressure differentials across piping mains. Each control loop is focused on a single piece of equipment; having multiple control loops trying to control the same piece of equipment often results in sending conflicting output instructions to the equipment. The sequences consider a limited number of factors, compare to a setpoint or decision value, then adjust to meet that setpoint or value.
Information flows up from the application level to the control level, where programmed responses are then sent back to the application level for implementation. The management level provides interfaces for both users and other systems (fire alarm, security, etc.).
While the sequences can be complex, they are still mainly “static” — that is, the sequences themselves don’t change. For example, they don’t consider changes in equipment operating efficiency that happen over time and don’t recognize changes to the operation of the system due to lack of maintenance, all factors affecting the overall operating performance of the system. In other words, BAS control comprises multiple control loops acting simultaneously but independently, each focused on a particular part of the chilled water system. However, the parts of a chilled water system don’t act independently; they affect each other.
By contrast, a chiller energy optimization system takes a global view of the chilled water system. It not only monitors all of the various control loops for each particular device or piece of equipment as the BAS does, but it also has the capability to understand how the various loops affect each other and can make adjustments to the control loops based on that understanding. This capability to make changes automatically to control loops — to make a control sequence “dynamic” — is what differentiates a chiller energy optimization system from a BAS. In fact, it can be argued that a chiller energy optimization system is a low-level form of “internet of things” in which one system controls and makes dynamic changes to another system without direct human evaluation or intervention.
Factors that impact system operation
In a chilled water system, there are four major equipment types that consume electrical energy: the chillers, chilled water pumps, condenser water pumps and cooling tower fans. As noted above, there are control loops and sequences that control the operation of each piece of equipment. In doing so, the control sequences directly affect the resultant power consumed by operation of that equipment.
With the installation of electrical energy usage meters for real time data collection, the chiller energy optimization system can monitor the individual power consumption for every separate piece of equipment and can attempt to tune or trim the power used for a specific piece of equipment. The total amount of electrical energy used by all of the equipment, the overall chiller plant kilowatt/ton, is the sum of the simultaneous demands of all of the equipment. This is the purpose of a chiller — to minimize overall chiller plant kilowatt/ton in real time.
Figure 2 illustrates how various inputs and variables affect not only the intended piece of equipment, but how the resultant action affects other pieces of equipment.
Direct inputs from external sources:
- Building load affects number of chillers and individual chiller loading to maintain enough capacity online to meet cooling demand.
- Space temperature and relative humidity affect chilled water supply temperature setpoint to obtain chilled water sufficiently cold enough to provide required sensible cooling and dehumidification.
- Chilled water delta P across the mains affects chilled water pump speed to maintain sufficient flow to all chilled water-cooling coils.
- Outside air wet-bulb temperature affects condenser water temperature setpoint that can be produced by the cooling towers. It also affects cooling tower fan speed needed to meet the CWST setpoint.
Control sequences are written to take the input above and stage chillers on and off to match cooling demand, change CHST setpoints if space temperature or relative humidity is too high, increase or decrease chilled water pump speed to maintain sufficient flow as chilled water control valves modulate open or closed to maintain required supply air temperature and change CWST setpoint to obtain lower CWST when possible.
These individual actions, however, affect each other and become indirect inputs to other equipment:
- CHST affects chiller efficiency. Chillers are more efficient at higher CHST but require more energy per ton of cooling at lower CHST (lower CHST require more compressor work for a larger “lift” from evaporator temperature and pressure to condenser temperature and pressure).
- CHST also affects chilled water pump operation. Lower CHST can result in less chilled water needed, which reduces pumping energy; in contrast, higher CHST may require more chilled water flow and, therefore, more chilled water pump energy.
- CWST affects chiller efficiency. Higher CWST increases compressor lift (between evaporator and condenser), which increases chiller work and energy required.
- CWST also affects CWP operation. Higher CWST can result in more condenser water needed, which increases CWP energy.
- CWST also affects CTF operation. Lower CWST requires more evaporative cooling, which requires more airflow through the cooling tower and, therefore, more CTF energy.
Common control loops for equipment operation in a chilled water system include:
- Chiller staging based on load; sometimes monitoring CHST is also included in chiller staging.
- Chilled water pump speed to maintain delta P across the coil and control valve at an AHU.
- Cooling tower fan speed to maintain CWST setpoint.
- Sometimes a control loop to vary condenser water flow and CWP speed is used as the first stage of CWST setpoint; at part load, condenser water from one chiller might flow through two cooling towers to take advantage of available heat transfer area. In addition, condenser water flow might vary from 50% to 100% before starting fans.
There are also control loops that seek to optimize setpoints to minimize energy:
- CHST setpoints can be increased slowly until space relative humidity exceeds setpoint.
- CHST setpoints can also be lowered to try and increase the chilled water system delta T, which reduces chilled water flow and pump energy.
- chilled water pump delta P setpoint can be decreased until some chilled water air handling unit control valves are open past 95%.
- CWST setpoint can be decreased slowly based on the projected available CWST from the cooling towers as outside air wet bulb temperature drops.
Each of these reset control loops, which are intended to save energy, can also have unintended consequences:
- Increasing CHST setpoint increases chiller efficiency. However, it may also result in more chilled water needed at the cooling coils to obtain required cooling, which would increase pumping energy, so there’s a trade between increased chiller efficiency (decreased chiller energy) and increased chilled water pump energy. The increase in required flow at the coils will also result in more chilled water control valves opening, which will cause the chilled water pump delta P setpoint to be reset to a higher value.
- Lowering the CHST setpoint may reduce chilled water pump flow and energy but increases chiller energy per ton because the chiller works against a higher compressor lift.
- Lowering the CWST increases chiller efficiency. It also may require more CTF energy, which is a trade-off against the lower chiller energy. The sequence could also affect CWP energy if varying the condenser water flow is part of controlling the CWST setpoint.
The big question is, how do you control the chilled water plant equipment to operate as efficiently as possible and ultimately consume the least amount of energy, while meeting the building needs?
What an optimization system chiller offers
A chiller energy optimization system continuously looks at all of the operating equipment and seeks to minimize the overall chiller plant electric demand. It may adjust the CHST and CWST setpoints up or down. It may reduce CWP speed while increasing CTF speed or do the opposite. It constantly monitors and adjusts setpoints and equipment speeds to respond to changes in the chilled water system demand. It is this readjusting of established control loops that a chiller acts as a low-level smart device — one system working in conjunction with the BAS to optimize the operation of the chiller plant without human intervention. The system can be installed and operate on local servers for security, if desired.
How does it do that? Different chiller vendors use their own software and proprietary algorithms to reach the goal of minimizing real-time kilowatt/ton, but one common aspect is that they all build a “library” or type of database that reflects project-specific equipment performance data. The operating characteristics for all equipment in the chiller system and the resultant electric demand are cataloged for comparison. This collection of empirical data becomes the basis for the chiller to know the best combination of equipment and settings for a particular load.
As an example, a common BAS control sequence might be: “When lead chilled water pump reaches 90% rated speed for five minutes, start lag chilled water pump.” A chiller energy optimization system will look at the operating curves of the pumps and sequence two pumps online where traditionally there may only be one. This would happen because two pumps operating at a lower frequency may use less energy than one pump operating at 60 hertz.
Another example would be where the chiller knows the part-load operational characteristics of each chiller in a system and uses that information to determine the best combination of chillers for the real-time demand.
One factor that is inherent in this method is that the part-load efficiencies of the specific equipment installed becomes a factor in the analysis. Power is the cube of flow for both water and air, so the energy used by pumps and tower fans during part load conditions becomes a major input to the overall plant energy usage. Chiller efficiencies, as well, are not linear but are functions of the installed equipment and change over time due to wear.
In effect, the chiller energy optimization system “learns” about the installed system then uses that data to select the most energy-efficient combination of equipment and settings. The chiller uses predictive methods at first to determine equipment operation, observes the resulting energy usage then adapts to tune the settings. (This process is similar to when a patient goes for an eye exam for corrective lenses. As the patient looks through the lens device, the eye doctor will select then reselect the proper lens, asking, “Is this better or worse?” until the patient sees no difference, at which point the doctor has found the right prescription.)
Because the chiller energy optimization system incorporates specific equipment efficiency data, building the database takes time. It will use various combinations of equipment and it may take several months to optimize the most effective plant operating scenarios. As it continues to run, the database continues to grow, with more accumulated history of operating combinations and associated energy usage.
Relationship of optimization system and BAS
It is important to recognize that a chiller energy optimization system does not replace a BAS. Rather, it complements and enhances overall chiller plant operation. The chiller energy optimization system is an optimization of chilled water system control. It takes the available inputs and outputs of the BAS and optimizes their use.
The chiller energy optimization system does not directly command a pump on or off, nor does it directly change a temperature setpoint. It tells the BAS to start or stop a pump or to change a temperature setpoint. The BAS retains direct control of sensors, transmitters and actuated devices and equipment at the application level.
Because they communicate so closely, the BAS and the optimization system must “speak the same language.” They must use the same protocol (BACnet, Modbus, etc.). The BAS and chiller energy optimization system are communicating constantly; they need to have compatible network speeds. There need to be sufficient interfaces in the management level of the BAS with which the chiller can communicate.
Just because there is an optimization system, the engineer should not abdicate design and intended operation of the chilled water system. There is always the chance that communication will be lost between the chiller and the BAS; if that happens, how is the chiller system supposed to work? There need to be sufficient control sequences for the system to operate properly without an optimization system.
As mentioned earlier, some BAS vendors may not agree with the advertised benefits of a chiller energy optimization system. The optimization system and BAS installer need to coordinate details of “tuning” the systems, such as valve closing speeds and time durations to ramp up or slow down pump speeds. It’s important that both system installers work closely together to bring their best products and installation practices to a successful project for the owner.
When does energy optimization make sense?
A chiller energy optimization system is an added expense and is not crucial to the operation of a chilled water system. There is a practical lower boundary of when an optimization system adds value above its cost. Therefore, it “needs to pay for itself.” For a custom written specification with site-specific installed equipment, some general guidelines are:
- There are at least three chillers in the plant, totaling at least 1,500 tons.
- Electricity costs are above national norms, either in energy or demand charges.
- A chiller energy optimization system is more likely to prove its worth when the chiller system operates year-round, as opposed to a system that does not run in the winter because the air handling units have airside economizer and do not use chilled water when the outside air temperature is below 50°F.
Recently, some chiller vendors developed standardized systems applicable to chilled water plants smaller than 1,500 tons with three chillers.
Asking “How much does it cost?” is akin to asking, “How long is a rope?” because systems differ in size, number of chillers, characteristics of the BAS, location of the project, etc. For example, a chiller for a chiller plant with three 500-ton chillers and variable primary flow costs in the range of $90,000 to $140,000 to install and start up. (These costs would be for a new installation with a new BAS that is prepared to interface with a chiller. Cost to add a chiller as retrofit may be higher if modifications to the existing BAS are needed to interface with the chiller.) Additionally, annual maintenance costs average 15%, depending on vendor, to provide continuing services, such as software updates or implementation on other host equipment.
When comparing systems and selecting a chiller energy optimization system, a presentation in person or in print is helpful to understand the scope of what will be provided. Important points to consider include:
- Features and advantages of the system. Ask what the system does that a BAS won’t do. They won’t tell you their proprietary algorithms but they should provide enough information that shows they are making real-time decisions based on-site specific equipment operating characteristics. Ask for an example, such as the pump or chiller examples above.
- A sample report or screen shot. See if they show a dynamic, real-time “dashboard” or something similar that shows current chiller plant kilowatt/ton.
- A list of equipment and control points that are monitored and adjusted.
- First cost and what is included in that scope. What requirements must already be on-site (such as BAS interface) for them to communicate? What else will be needed outside of the scope included in the first cost?
- Are there any annual system maintenance or upkeep costs? If so, how much and what is included?
- References for systems in buildings of similar size and occupancy.
A chiller energy optimization system is appropriate when the owner prioritizes long-term operational cost savings over first cost of installation. For the three 500-ton chillers example, the simple payback would range from three to four years assuming year-round operation and electricity costs 10% above national norms.
There are many successful optimization system installations with which owners are very satisfied. There are also installations that have not been successful. The consulting engineer needs to evaluate the owner’s priorities, plant capacity, expected time of plant operation and electric utility rates to advise the owner accordingly. The engineer should also enlist the owner’s influence with the BAS and chiller energy optimization system installers to work together.