This New York City (NYC) building design will meet the challenge of emission reductions of 90% to 100%.
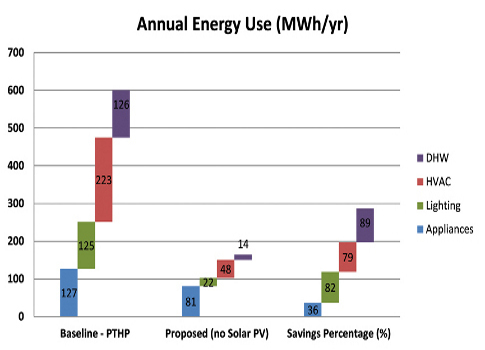
A New York City (NYC) building will meet the challenge of reducing emissions by 90% to 100%. Our engineering team assumed that a new, mid-rise multifamily building may have the highest potential for cost-effective net-zero energy building design for the following reasons: easier adoption of new technologies, lower initial incremental costs, and optimal occupant density per roof area to maximize use of renewable energy.
Using the Dept. of Energy’s eQUEST, a sample building was created that mimics energy use of a typical new NYC multifamily building. The baseline model used simulation guidelines from a state energy program for multifamily buildings, as well as ASHRAE Standard 90.1-2007, California Title 24 ACM Manual, ASHRAE Standard 62.1-2007, and the NYC Building and Mechanical Code. This model served as the reference for assessing progress toward a net-zero energy building design.
The building has 48 apartment units within a 53,000-sq-ft gross floor area, in a rectangular shape, shown in Figure 1, with four floors plus a basement and a common laundry. The model was generated so that one can incrementally change the number of floors as needed.
In the baseline, two likely scenarios are examined: heating by electricity (with packaged terminal heat pump, or PTHP) and heating by fossil fuel (with packaged terminal air-conditioner, or PTAC, and gas-fired boiler) according to ASHRAE Standard 90.1-2007. New York Central Park’s TMY3 bin weather data is used in all the simulation runs.
The approach
Although a 90% reduction in emissions by 2050 looks like an intimidating target, it is possible to overcome the challenge following a "one step at a time" approach. This means breaking the target into smaller, achievable pieces instead of considering it as an insurmountable whole.
When selecting energy-efficiency measures, priority is given to measures that are smaller, passive (fewest moving parts), cheaper (more cost-effective), and innovative.
The passive strategies studied include: highly improved wall and roof insulation, window upgrade with low-e coatings and insulated frames, shading possibilities, and substantial infiltration reduction by eliminating penetrations through building skin and through detailed air-sealing. Diminishing returns are evaluated for these envelope strategies while also taking into account the lowered installed cost for mechanical equipment that results from higher-efficiency envelope measures. In the analysis, we compare compartmentalization versus noncompartmentalization practices, along with mechanical versus natural ventilation, and determine which ventilation solution provides the best controlled intentional fresh air into the apartment spaces.
A high-performance air-source heat pump (variable refrigerant flow, or VRF) is introduced as a heating plus cooling system. One VRF outdoor condensing unit is recommended per apartment to lower transport losses and piping costs and to free up roof space for renewable energy generation. Domestic hot water (DHW) energy efficiency strategies studied include heat recovery from the drain as a preheater and recovering the waste heat from the VRF system by a heat exchanger.
VRF systems offer multiple benefits including:
- Reduced pipe energy losses
- Improved zone temperature control and substantially reduced energy usage
- Eliminating the need for a boiler room and its ventilation requirements and making the recovered space available for other uses
- Roof space freed up for other uses; eliminated room air-conditioner envelope losses (both infiltration and conduction)
- Higher-efficiency cooling/heating
- No electric resistance backup
- Heat recovery for DHW
- No structural damage from circulation water leaks
- Improved tenant comfort; potential to submeter heating, cooling, and DHW
- Resiliency (no boiler on the lower floors); and most important, dramatically lower carbon emissions.
Lighting strategies include low lighting power density (LPD) design solutions while maintaining acceptable levels of illumination. Where applicable, occupancy sensors and bi-level lighting controls are evaluated.The most efficient available appliances are considered for apartments and common areas.
Solar photovoltaic (PV) arrays can be installed in the freed-up roof space to zero out the remaining electricity use after all other improvements are implemented. Using the eQuest simulation tool, numbers of floors are iteratively varied to determine the economically viable range of floors and also the highest possible number of floors for a building to achieve net-zero energy with today’s technology.
Electrical loads
Appliances and plug-load measures were evaluated first since they are the least recognized for reducing energy and one of the hardest to achieve overall cost-effectiveness. Evaluated products were the lowest energy users among Energy Star labeled products and tabulated as follows:
- Ultra-high-efficiency refrigerators: These are expensive but offer high-value energy savings. This improvement has an incremental cost ($/kW) similar to solar PV, but is still worthwhile because it does not require roof space.
- Clothes dryer: Per the Super-Efficient Dryer Initiative (SEDI), clothes washers reduced their energy use by almost 75% in the last two decades, compared to dryers with only a 20% improvement (excluding heat pump dryers). As a proven technology elsewhere in the world (over 25 models are available in the European Union), heat pump dryers have great potential in the U.S. market. The U.S. Environmental Protection Agency (EPA) gave heat pump dryers an Energy Star Emerging Technology 2012 Award.
- Television: Energy Star’s standby mode requirements have tightened over the years, which reduced consumption drastically (by 36 billion kWh/year in 2012), while 80% of televisions met the requirements by 2008. Televisions that meet today’s Energy Star requirements are on average 40% more efficient than conventional models. Since 2011, Energy Star no longer permits more energy use for larger screen TVs (larger than approximately 50 in.).
- TV set-top (cable) boxes: According to a 2011 Natural Resources Defense Council (NRDC) study, set-top boxes in the U.S. consumed about 27 billion kWh in 2010, equivalent to nine 500-MW coal-fired power plants. There are about 160 million set-top boxes in use in the country, at near-full power even when the consumer is not watching or recording TV. Potential improvements with set-top boxes include efficient multi-room solutions that schedule recordings on a central appliance and Internet protocol TVs (IPTV) boxes that draw approximately 18 W when operating and 12 W in light sleep state.
Lighting
The Lighting Field Guide: Upgrading to LEDs for Multi-Family Housing is the basis of proposed lighting design, with recommendations shown in Table 1. With these recommendations, the proposed design includes a combination of high-performing Energy Star-qualified T8 and light-emitting diode (LED) fixtures.
Precise design and fixture selections are crucial in lighting. For instance, none of the spaces have illumination levels more than 10% over what is required by the Illuminating Engineering Society (IES).
Progressive lighting design can reduce energy use between 60% and 85% compared to a conventional building. Beyond lighting design and fixture selection, lighting controls (such as occupancy sensor-based on-off and bi-level controls) have the potential to significantly lower energy use further.
In a recent study, bi-level controls in stairwells in a multifamily building produce energy savings ranging from 53% to 77% with a 5-minute off-delay at 33% and 10% light output, respectively. In another study, energy savings ranged from 40% to 60% for the same control in stairwells in four different commercial buildings with a 10-minute off-delay at 33% and 10% light output, respectively. The impact of off-delay times is analyzed for both corridors and stairwells (at 5% low-level setting) for multifamily buildings in a separate white paper
We recommended 5% low-level light output setting at 5 minutes off-delay time in this project, with savings (beyond the earlier improved LPDs) estimated at:
- 50% for corridors
- 70% for stairwells.
The lighting power reduction (10%) for the office and building operation spaces are based on ASHRAE Standard 90.1 Appendix G. Refuse/compactor, multipurpose, and mechanical room savings shown are based on a study by Rensselaer called "Lighting Research Study."
Estimated lighting power reduction for occupancy sensors and bi-level lighting controls for associated spaces is shown in Table 2.
Domestic hot water
Previously recommended efficient dishwashers in apartments and clothes washers in the common area will reduce overall hot water use by 5% and 2%, respectively. Recommended flow rates for low-flow water fixtures, such as kitchen faucets and showerheads, are 1.5 gpm, and for bathroom lavatory sinks are 1.0gpm, which are all better than ASHRAE Standard 189.1-2009. Low-flow fixtures result in substantial reductions in overall hot water use by almost 24% compared to conventional fixtures. Our proposed DHW system consists of three components:
Pre-heater: A run-around coil type heat exchanger will recover waste heat from the shower drain to preheat the cold incoming water. Apartment showers are the largest DHW user, with the water draining and demand for hot water likely to happen at the same time, also during peak hours. We estimated shower drain temperature at around 100 to 105 F; with a conservative 40% thermal effectiveness, the heat exchanger process could preheat the incoming water by about 8 F whenever the shower is in use.The mechanical designer would need to design the shower drain separately, and the additional design and installed cost is included in the analysis.
Main DHW heater: A commercial (or Energy Star qualified residential) air-to-water electric heat pump is chosen as the main hot water heater. The commercial unit has 3.9 coefficient of performance (COP) at the rated conditions and a centralized installation in a mechanical room is planned. Preheated incoming water mixes with hot recirculated water and with water heated by the pump to 110 F and is sent to the apartments. Heat pump DHW heaters have substantial savings potential in moderate climates such as NYC, which is in climate zone 4A, a mixed-humid, moderate climate per ASHRAE Standard 90.1-2007.
Secondary DHW heater: For point-of-use in apartments. This is a refrigerant-to-water heat exchanger that recovers the VRF system’s compressor waste heat to heat the DHW even further (120 F). The temperature rise provided by this unit will be 10 to 15 F. This unit will not only recover VRF waste heat, but will also make the main DHW heat pump heater operate considerably more efficiently.
The proposed design will keep the hot tap water no more than 120 F, saving at least 15% compared to typical 130 F apartment tap water.
Two final design features were considered:
- Recirculation: Because considerable energy losses occur during recirculation, the designer must give extra attention to load sizing to eliminate unnecessary recirculation flow rates or eliminate recirculation entirely. Controls are also recommended to prevent 24/7 operation of there circulation pump.
- Redundancy: The main heat-pump water heater capacity is sized to meet the full DHW load when needed by apartments.
Building envelope
Twelve different scenarios are evaluated for the exterior walls, roof, and fenestration. The resulting peakload reduction (heating) for each scenario is shown in Figure 2.
Savings-to-investment ratios (SIRs) were reviewed for varying insulation levels in exterior walls and roof,and for different fenestration scenarios. Analyses reflect two different methodologies: The blue curve is based on incremental installation cost that accounts for the lower HVAC load and lower equipment sizing requirements; the red curve does not take this into account.
In this sample building, the window-to-wall ratio is 28%, a range not penalized under ASHRAE Standard 90.1. Multifamily buildings often have lower window-to-wall ratios, as low as 10% to 15%, which would result in even lower overall energy use.
Additionally, 4-in. extruded polystyrene (XPS) is introduced to below-grade vertical walls, an additional 2.5 in. of insulation compared to the baseline case.
Last, we calculated that infiltration of about 13 cfm occurs per PTAC unit in the baseline. Because the VRF system requires no exterior wall penetrations, the result is approximately 0.1 air changes/hour (ACH) infiltration reductions compared to the reference building.
HVAC systems
The engineering team specified VRF systems to provide heating/cooling/ventilation for each apartment, with inverter-driven compressors. Compressor speed modulation can vary to 10%. The outdoor unit and branch circuit controller will be connected to each indoor unit by a two-pipe refrigerant system. VRF units will be installed for each apartment, either on a balcony or, as is common in other countries, in a mechanical room for each apartment, open to the outside.
VRF units will have a heat recovery option where waste heat from the compressor can be used to heat the DHW loop. A closet in each apartment will house VRF hydronic heat exchangers (closed-circuit water heater transfers heat from refrigerant to water).
We studied 20 different ventilation scenarios, including compartmentalization versus central exhaust, overventilating, underventilating, continuous versus intermittent exhaust flows with acceptable amounts, energy recovery ventilation, and exhaust air sourced from infiltration, balanced, or air handling units. Compartmentalized continuous exhaust and outside air (per apartment) provided by the air handler was found to be the best option; it had relatively low energy consumption and also eliminated unintentional infiltration. Continuous exhaust totaled 45 cfm per apartment, and continuous outside air at the rate of 10% higher than exhaust flow (which results in about 15 to 25 cfm per person that complies with local code) is incorporated into the design.
Results and successes
After implementing the aforementioned measures, the annual energy use and savings percentage by end use are presented for the baseline and proposed cases as in Figure 3.
For ASHRAE-regulated measures, including HVAC, DHW, and lighting, the savings are around 80% compared to the baseline as shown in Figure 3. However, the 36% savings from appliances is relatively low and has a longer path to achieve higher energy efficiency. In the proposed model, half of the building electricity use is appliances, compared to only one-fifth in the baseline. For net-zero projects, the appliance improvement cost-effectiveness is compared to the solar PV system, as the savings is mostly in electricity and has the advantage of not requiring roof space.
The baseline (with PTHP and baseline with hydronic) and proposed overall annual energy use and cost and greenhouse gas (GHG) impact were calculated. The proposed design saves 68% to 72% in source energy use and 70% to 73% in energy cost compared to the baseline. As a result, electricity generated by solar PV on the building roof would need to offset the remaining 30% of energy use.
Lifecycle cost analysis of all energy-efficiency measures based on end uses is shown in Table 3. Lighting-related measures yield the best SIR by far. DHW-related measures are economical as well; SIR is almost 1.0. The lowest possible SIR is for HVAC because of the costly VRF system. Consequently, the SIR for the incremental installation cost for implementing all measures (without solar PV) is very close to 1.0, which is in the cost-effective range. Considering potential federal or state incentives, the investment looks even better.
The final step before the finish line is solar PV. Per our model, 60% of the roof would be sufficient for a solar PV installation. High-end equipment is chosen for this solar PV system: monocrystalline silicone solar cells with 20% efficiency and micro-inverters with 91% conversion efficiency.
The engineering team calculated the building’s electricity use versus solar PV generation (per gross floor area in sq ft or gsf) if the same roof area and solar PV equipment are used for all other floors as the four-floor building.
Although solar PV production matches building consumption in the four-floor building, energy use per gsf opens the gap as the number of floors increases.
Can we overcome the roof area issue, especially when buildings are taller, as in NYC? Cell type and PV module efficiency, or inverter technology and conversion efficiency, or permissible roof area ratio could be improved for solar PV systems to sustain net-zero energy even for taller buildings.
A net-zero building design is feasible in NYC, up to four stories. Taller buildings would be possible with higher-efficiency solar PV systems or a larger permissible roof area. The package of energy efficiency improvements is shown to be cost effective, on a lifecycle basis.
Umit Sirt is a partner and senior engineer at Taitem Engineering where he manages the energy consulting services department, providing services relating to building and industrial energy efficiency including benchmarking, general feasibility studies, advanced energy models, and investment-grade energy audits; net-zero design and consulting; and technical reviews, energy master planning, and outreach.