Sensors, VFDs and enclosures ensured reliable motor performance
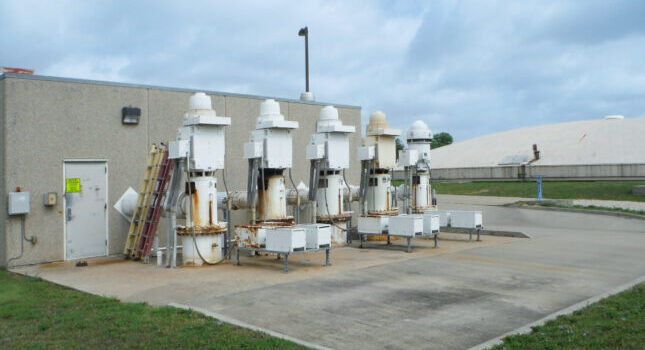
Lockwood Andrews & Newnam Inc. (LAN) recently completed a design project for a large municipal water authority in Texas. The project involved moving treated drinking water from a large ground storage tank to its water distribution system. This facility accepted finished water from the water district and pumped it out to the city’s distribution piping that serves the customer base. In a typical installation, water is provided at various points in the system and used by many customers throughout the city and surrounding areas. The distribution is very much like the electrical grid.
The basic installation and site requirements dictated that the nine motors deemed necessary for this operation had to be 400 horsepower, 480-volt, 1,800 revolutions per minute motors. Working with the client, the LAN team defined the important factors for installation. The first was motor protection. LAN wanted vibration and temperature sensors to monitor the large motors, considering their use case and importance in the system.

The loss of any of the client pumps could mean long lead times if any of the motors had to be replaced and hamper the system. This would have operational impacts on their distribution system and most significantly, on customers throughout the city.
Now, with the remote monitoring of these sensors, the city is alerted if any one motor is showing any signs of distress or premature failure so corrective actions can be taken before there is a full malfunction.

LAN also recommended that each motor management unit include a variable frequency drive (VFD) that could also monitor temperatures and vibrations. By keeping the control and monitoring elements integrated within the VFD, it keeps the responsibility for driving and protecting the motor within the realm of a single manufacturer. This is critical when services are required for routine maintenance or repair.
Another key requirement was satisfying the regulations of the local electric provider. In this case, the VFD had to maintain acceptable total harmonic distortion in accordance with the standard set for electrical power systems by the Institute of Electrical and Electronics Engineers (IEEE 159). To achieve this, LAN selected 18-pulse drives for this project.

Finally, to protect the VFDs and motors from the elements, LAN constructed a simple metal building over the existing pump cans to accommodate the new pumps and motors. The pump room is ventilated, while the electrical room is air conditioned to prolong the life of all the equipment, as well as provide a sheltered location for maintenance and repair.