Many acoustical challenges were resolved in this distribution warehouse.
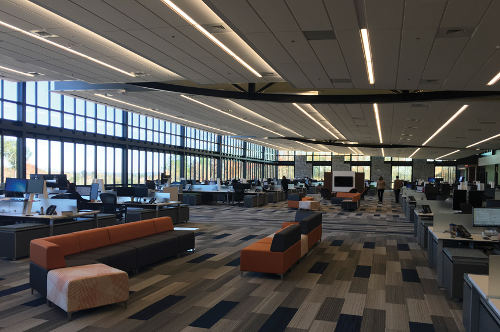
A recent project for a distribution warehouse operation included several acoustical challenges in a large, open office space that served the support staff. The space included stone and glass on three sides, with little area for sound absorbing surfaces. The interior design firm had carpeted floors and an acoustical tile ceiling in mind for the space, but there were some creative twists in the design that presented some interesting acoustical challenges.
Rooftop units
The first challenge: The space had to be heated and cooled using four large rooftop units, housed on a lightweight built-up roof deck over the office area. Adequate vibration isolation from the rooftop units was required to reduce reradiated noise into the office areas below. This would have been less of a challenge with a concrete structure; however, the facility had a metal roof deck on metal joists. This type of lightweight building structure requires careful analysis for successful vibration isolation.
Vibration isolators interact with the structure on which they rest—more flexible structures require higher static deflection isolators to be effective. If the structure is too flexible, then it can become very expensive or even impractical to isolate vibration from the units.
The key, in this case, was to work with the structural and mechanical engineers to relocate the rooftop units as close to the major joists as possible, so that we could reduce the roof deflection of each unit to less than 0.25 in. This allowed the use of a vibration-isolation curb with a relatively high, but attainable, 3-in. static deflection.
Terminal units
The next challenge was the fan-powered terminal units installed below the structure and above the ceilings. Two aspects of these were a problem: Fan noise propagating down the ducts, and noise radiated from the terminal unit housings into the spaces below.
The engineering team was able to address the potential duct-borne noise by working with the mechanical engineers to incorporate acoustically lined ductwork between the fans and the supply diffusers and return registers. In a couple of locations, duct silencers were required due to the short distances to the first supply or return openings. Rerouting ductwork in some cases allowed for the use of duct lining without a silencer, which is generally the preferred solution for both financial and static pressure budgets.
The radiated noise from the terminal units proved more challenging. The interior designers had in mind a slightly curved, more modern "floating" ceiling, meaning there were large areas on ceiling tile with gaps that were open to the structure above—and to the terminal units.
The team worked with the mechanical engineers to search for quieter terminal units, which was a challenge in itself because the way terminal units are rated acoustically for radiated noise assumes the use of a closed mineral-tile acoustical-ceiling plenum. In this case, an open-edge ceiling with fiberglass tiles that do not isolate noise as well as the denser mineral fiber tiles was used.
Engineers obtained the octave-band sound power data for various terminal units and developed detailed predictions of the office-area noise based on the ceiling conditions and the use of multiple terminal units over the space. The final solution for the radiated noise problem was a combination of selecting quieter terminal units and working with the interior designer to configure an enclosed ceiling assembly that still appeared to be floating as originally intended.
As a part of the ceiling design, the designer had to research and analyze ceiling-tile options for the large 4×8-ft tiles that were desired. The consultants found a supplier who could provide 2-in.-thick fiberglass ceiling tiles that provided the sound absorption needed to reduce reverberation the large office area. The fiberglass tiles included a sound-isolation membrane backing, which provided the sound-transmission loss required to isolate the radiated noise of the terminal units.
The results
The acoustical design was a long process that required deep coordination with the mechanical engineer, structural engineer, and interior designer. That process paid off in an acoustically comfortable and functional open-office area with a great view. When the building was occupied, the design team visited the site and made measurements in the office area. The team found the background noise to be at appropriate design levels for an open-office area, and without excessive reverberation.
The project is a great example of how cooperation between building trades with the common goal of satisfied clients can be successful, albeit with a lot of hard work.
Timothy Cape is director of acoustics at JBA Consulting Engineers. Michael Schwob is technical advisor at JBA Consulting Engineers.