Commissioning, recommissioning, or retro-commissioning, can be a challenge—and the more complex a facility is, the more boxes an engineer has to check to get the job done right. Here, a group of expert engineers explain how to succeed on such projects.
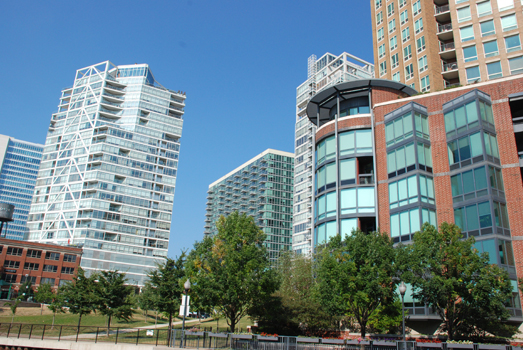
Respondents:
- Ray Dodd, PE, CxA, LEED AP , President, Total Building Commissioning Inc., Phoenix
- Kyle G. Hendricks, LEED AP, Energy and sustainability consultant, Environmental Systems Design Inc., Chicago
- Donald H. Horkey, PE, LEED AP, Principal, mechanical engineer, DLR Group, Minneapolis
- David J. LeBlanc, PE, FSFPE, Senior vice president, Rolf Jensen & Associates, Inc., Framingham, Mass.
CSE: What challenges do building commissioning projects pose that are different from other projects?
Ray Dodd: Our goal is to make the job successful for the owner, designers, and contractors alike. The role of the commissioner is a quality control agent and diplomat. Each group has a different agenda with regard to the work. In a way, they speak different languages. Many of the commissioning issues we encounter have to do with miscommunication between trades, between the designers, or between the designers and the contractors. For us, the challenge is to convince everyone we are committed to their success—not the quality police—and to communicate effectively by speaking everyone’s language so the project is successfully built.
Donald H. Horkey: A big challenge that the commissioning agent (CxA) faces on some projects is that he or she has no actual authority. Commissioning is a quality process of checks and balances for ensuring building systems are designed, constructed, and operated for peak performance; however, if the owner is not actively engaged in the commissioning process and providing influence to assist with the closure of issues, it can make life very hard for the commissioning authority. Another big challenge is not getting the commissioning authority engaged in the project early enough. The budget requirements of some projects will dictate that the owner can afford only basic functional testing. When this occurs the commissioning authority does not get brought into the project early enough to make an impact on building performance during design or early construction. Too often the commissioning authority is brought in at the end of the project for functional testing when it is much less cost-effective to make changes for operational efficiency.
David J. LeBlanc: Commissioning of fire protection and life safety systems poses different challenges than other projects, but they are mainly related to having a different viewpoint and wearing a different hat at the table. As a fire CxA you are not the engineer of record, architect, designer, or the contractor (those spots are already accounted for)—you are an independent third-party working as agent for the owner. As a fire CxA, you are an extra set of eyes and ears for the owner during the design and construction phases of the project. As a CxA you have to remember what your roles and responsibilities are. However, the CxA should bring all of his or her varied past experiences related to fire protection and life safety system for the benefit of the owner and team stakeholders.
CSE: Please describe a recent commissioning project—share challenges you encountered, how you solved them, and aspects you’re especially proud of.
Dodd: We recently completed the NuSkin Innovation Center, a complex design using chilled beams, condenser water cooling, and atrium with smoke control. It is a smart building and all the lighting, security, and HVAC interact through a common software platform. It was also completed in phases with the data center going online before the rest of the building. We helped keep the team focused by applying tracking tools to provide status, issues logs, and online communication in real time. We met all the milestones, the data center operated without interruption during pull-the-plug tests for the innovation center, and we completed the commissioning process prior to occupancy.
LeBlanc: A common challenge we face in commissioning of smoke control systems is the integrated testing of the smoke control system. The smoke control system really comprises many systems (stair pressurization fans, normal HVAC, fire alarm, sprinkler, fire pump, emergency power). What is often misunderstood is the integration of the overall smoke control system and how the various systems are intended to react in various situations (normal, fault condition, and emergency condition). We solve this problem by having the stakeholders (owner, design team, and contractors) get together to review the integration of the smoke control system in order to review the integrated testing plan of a smoke control system to make sure everyone is on the same page. I believe the fire CxA can help bring the various stakeholders together based on their unique viewpoint, qualifications, and expertise. I am especially proud of being able to pull different stakeholders with different viewpoints together for the common goal of getting the smoke control system to perform under various conditions per the agreed-upon project and owner objectives.
Horkey: DLR Group recently retro-commissioned a high-rise hotel. We immediately discovered a constant volume pumping system that was oversized on both the hot water and chilled water sides. The system was pumping through hot water and chilled water valves throughout the building, forcing simultaneous heating and cooling to occur. By installing variable frequency drives (VFDs) on the pumps, adding differential pressure sensors, and adding a bypass line to the chilled water system, we were able to reduce the building’s energy consumption by around 40%.
CSE: Testing methods/procedures can be complex. What tips can you offer engineers working on commissioning projects?
Horkey: It’s essential to keep design sequence of operations as simple as possible. Design engineers should help with writing and witnessing testing procedures; this is a great way for the design engineer to close the loop between real-world conditions and design on paper. Closing this loop is critical for design engineers and CxAs to better understand the entire building process. Additionally, it is a very good learning experience for the design engineer to assist with the training of the operating staff. Similarly, it is important not to overcomplicate prefunctional checklists and functional test procedures. Prefunctional checklists with overly laborious or repetitive tasks can lead to contractors skipping over or “pencil-whipping” checklists. A well-structured checklist is needed, with clear and concise instructions, for the contractors that deal specifically with the piece of equipment being assessed.
Dodd: It’s critical that the mechanical and electrical engineers have detailed specifications regarding construction integrity testing (duct pressure testing, hydrostatic testing, megger testing, etc.) during the project. Also, because the functional testing phase during commissioning relies heavily on the sequence of operations, we suggest that when the controls submittal is being reviewed, the design engineer, commissioning authority, and controls contractor meet to discuss the final sequence of operations. Finally, engineers shouldn’t take the commissioning comments made during design personally. Instead, use them as a way to improve the quality of the product. Commissioning is a no-cost (to the engineers) quality-control process designed to help make sure that the building functions as the designers intended.
LeBlanc: The best tips for any fire protection life safety systems are to have a great test plan that incorporates the various test scenarios you will want to eventually be testing, a thorough sequence of operations, and a specific integrated test plan for integrated fire protection and life safety systems.
CSE: What are some of the tools and systems you rely on to commission projects?
Dodd: We use online issues (punch list) tracking systems, databases, spreadsheets, and fault detection diagnostic software.
Horkey: DLR Group has used a nonproprietary cloud-based commissioning system for the past few years with great success. A cloud-based commissioning platform allows real-time data synchronization, which in turn allows on-site deficiencies discovered during site visits or functional testing to be documented, synced, issued, and resolved on a real-time basis. Contractor checklists can be completed and synced in the field. Issues can be identified in real time, which reduces coordination time for the entire team and the overall impact on the schedule.
-
Project administration is reduced due to the elimination of the time spent handling documents multiple times. Once a checklist is filled out electronically in the field and synced, it is complete. Using digital prefunctional checklists and functional performance tests also allows multiple trades to access and complete checklists for systems and equipment simultaneously.
-
Contractors can complete checklists and other commissioning responsibilities on their own schedule without having to wait for the CxA or other trades to complete their sections first, reducing the impact on their schedule.
-
Contractors can sync all completed checklists electronically via the cloud, eliminating administrative time spent coordinating other methods of printing and transmitting completed documents, for example, scanning, faxing, e-mailing, and so on.
-
Daily and weekly resolution tracking reports are easily generated, which increases project team visibility and accountability. This allows for quicker resolution of commissioning issues and minimizes the impact on the project schedule.
-
The owner has real-time visibility on open issues and can coordinate pay requests based on the resolution tracking form.
-
Taking a traditionally paper-heavy process to a fully digital and paperless process reduces time for all team members transmitting, coordinating, filing, and storing commissioning process documentation and eliminates project printing costs for the commissioning process.
CSE: When re- or retro-commissioning structures, what challenges do you encounter, and how do you overcome these challenges?
LeBlanc: We see four main challenges related to fire protection and life safety systems, which generally pertain to design intent. First, oftentimes there is a lack of documentation from the owner, including previous commissioning records and the intended performance or sequencing of the various fire protection and life safety systems. These existing systems need to be integrated properly to meet the intended performance or goal, and it is often a challenge to determine the actual intended operational sequencing without benefit of original design documentation. Second, there must be an understanding of the owner/project goals and objectives, beyond meeting code minimum requirements. Third, many times there are existing fire protection and life safety systems that have not been properly inspected, tested, and maintained by the owners as required per code. Fourth, existing occupied buildings, and in some cases—like for a hospital, nursing home, or hotel—those that are occupied 24 hours a day, 7 days a week, bring another set of challenges for both retrofitting of systems into existing building and commissioning and testing of these systems. We overcome these challenges by conducting functional testing to confirm the actual system operation, and working with the stakeholders and using our expertise and experiences for the benefit of the overall commissioning effort.
Kyle G. Hendricks: Often the most challenging aspect of a retro-commissioning project is getting buy-in from the building operators, whether it be to start the project or to implement controls modifications and energy conservation measures (ECMs). The key to success is the real “commissioning” aspect of the project; it is important to stay actively engaged with the operations team until they fully understand and embrace the implemented ECMs. Recommendations that end with reports usually get left in the drawer.
Horkey: While a lot of the functional testing of systems and general approach to existing building commissioning is the same as new construction commissioning, there are a few key differences. The most notable difference is the difference in skill sets required for retro-commissioning. There is a much larger emphasis on accurately calculating energy and cost savings to make the business case to management teams for implementation. This is not typical in new construction commissioning where optimizing the design is the primary objective.
Another challenge with retro-commissioning and existing buildings is we often find unique HVAC systems using older products that have been discontinued. We have to dig a bit deeper into the equipment’s design intent and define optimal operation going forward than with a new building where everyone is familiar with the equipment. In these instances we work with the manufacturers and the building engineers to put together a plan to improve the equipment’s efficiency.
Dodd: Often on re- or retro-commissioning, the original contractors are not available to be interviewed. To commission the building we need to understand the design intent, track down original and renovation drawings so we understand the as-built conditions, and identify how the building is being controlled today. We can’t move forward without it. Overcoming that challenge requires detective work, interviewing the occupants and service people involved with the building, and putting together a history with the help of energy bills, service tickets, and anecdotes so that we can put together a cohesive plan.
CSE: Does your firm offer third-party commissioning services, and if so, what benefits do you provide as a third-party commissioning agent?
Horkey: DLR Group does offer third-party commissioning, which is a significant portion of our building optimization services. The most important thing is to ensure that a third-party commissioning professional is from a major commissioning certification program through ASHRAE, AABC Commissioning Group, Building Commissioning Association, or National Environmental Balancing Bureau. Also, it is important for the commissioning professional to be engaged in a comprehensive continuing education program to stay in front of HVAC system design and industry trends.
LeBlanc: Yes, RJA does perform third-party commissioning services. The largest benefit is to the owner. As a third-party CxA you are an owner’s representative and the owner benefits from an unbiased viewpoint during the design phase and during construction with an extra set of eyes and ears looking out for its best interest. As a company the benefits we provide are our extensive experience with fire and life safety codes, designing of fire and life safety systems, our experience with the NFPA process/requirements, and lots of field experience dealing with various designs and configurations.
Dodd: Yes, we offer third-party commissioning services. The benefits are: no conflict of interest, an independent review, and transparency to the owner during the commissioning process.
Hendricks: We do, and our third-party commissioning teams nicely complement our design services. We usually don’t commission projects designed by our company, which allows us to lean on the expertise of our design professionals during design reviews and functional performance tests. Likewise, our commissioning teams bring real-life operations experience to our design projects, which ensures they will be both functional and buildable.
CSE: ASHRAE Standard 202: Commissioning Process for Buildings and Systems, identifies the minimum acceptable commissioning process for buildings and systems as described in ASHRAE’s Guideline 0: The Commissioning Process. How have you applied this standard in a recent project, and what challenges did you overcome?
Horkey: Most of our projects follow the guidelines set forth in the standard. However, it is common to have some of the predesign and postcompletion items not included in a scope of work such as owner project requirements, basis of design document, a full report for design review, and warranty commissioning reports. Including these items in the commissioning process is not an issue.