The use of BIM in plumbing projects creates deeper project knowledge, delivers a more robust product, and can reduce total project costs.
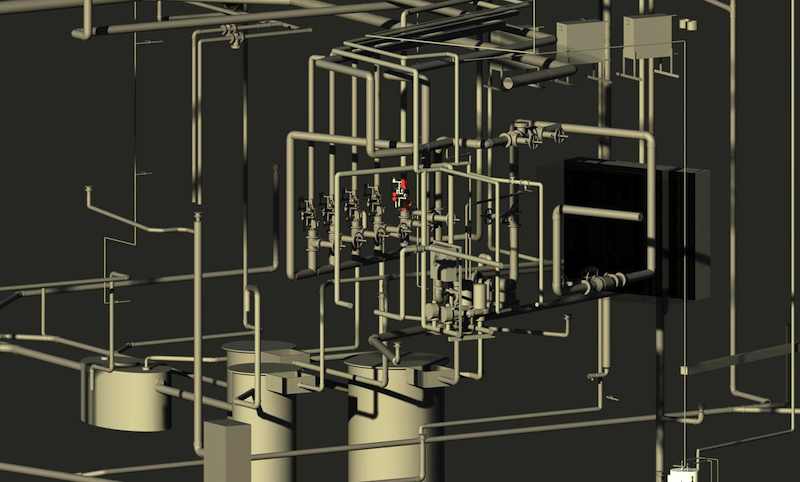
Learning objectives
- Understand the basics of how BIM can be used in plumbing and piping projects.
- Learn the advantages of Autodesk Revit MEP software.
- Anticipate some of the challenges faced by plumbing designers using Revit, and gain knowledge of potential solutions.
Building information modeling (BIM) is a powerful tool that is transforming the design and construction industry. As more building owners become familiar with the technology and even mandate its use, successful architecture, engineering, and construction (AEC) firms understand that they must embrace the BIM revolution if they want to stay competitive and keep pace with industry trends. Consulting engineers need vision and commitment to integrate BIM into their practice as it matures for mechanical, electrical, plumbing (MEP), and fire protection design.
Across the MEP disciplines, designers voice common challenges related to BIM. MEP software is typically a generation or two behind software for structural engineering, and further behind that for architects. Designers need intensive training to start using it, and the skills they develop are of the “use it or lose it” variety. Breakdowns in project team communication can jeopardize drawing quality and project schedules. However, with upfront planning and a focus on collaboration, there are solutions. The plumbing discipline has the farthest to go in terms of software development, but there are a few simple shifts that designers can make to dramatically increase productivity.
Don’t let the learning curve of implementing BIM distract you from the bigger picture. The use of 3-D modeling software creates deeper project knowledge, delivers a more robust product, and can reduce total project costs.
Big-picture guidelines
GHT Limited, Arlington, Va., uses Autodesk Revit MEP software. It’s important for designers to understand that Revit functions very differently from AutoCAD—it’s not just a 3-D version of the drafting software. In addition to the X and Y coordinates, you have the Z coordinate and material data collection information, as well as the potential to integrate time, cost, and lifecycle management data. Designers must show the plan view of X and Y; the Z coordinate will be decided by the cut plan view set by the user.
One of Revit’s unique features is the Families function. Families are divided into three groups. The first group is the System Families, which are pre-existing within the software. The second group is the Loadable Families. This group is customized by the user, based on the project needs. The third group is the In-Place Families, which are loadable but can’t be exported out of the project in which they were made. All families have one thing in common: They are 3-D parametric objects.
Traditionally designers draw a rectangle, square, circle, or other type of shape to represent an object for 2-D AutoCAD drafting. Some of these objects are available in Revit format from the material or equipment manufacturer, but not always—design teams should check availability at the beginning of the project and plan to create them in-house if they don’t exist yet. Be aware that when an object is provided by the manufacturer, it may contain much more information than what you require, which may slow down productivity due to the files’ large size. As software development is progressing, firms should plan to allow design teams research and development time for creating efficiencies for their Revit projects, which will cut costs in the long run.
Owners are understandably excited about BIM software, though they are not always aware of how its use will affect the project budget and scope, leading to challenges later in the job. Engineering consultants can make the process more successful by educating their clients about the impacts of using BIM during the proposal and negotiation stage. Help them understand the benefits they will gain to offset their concerns that it might add a premium. To support this effort, designers must vocalize how the use of BIM impacts their workflow to their firm’s executives.
Revit is a collaborative tool, so allocate time for collaboration. The use of Revit typically requires more team coordination than do projects in AutoCAD, and this should be reflected in project planning and cost estimating for design. On a Revit project, getting consultants on board and involved earlier in the project, potentially in the concepts or schematics phase instead of the design-development phase, should lead to a better coordinated finished model, resulting in fewer problems during construction.
Revit design tips for plumbing design
Plumbing design can be more complicated in Revit than HVAC or electrical design because it deals with sloped piping, a sanitary drain vent, storm drain lines, and so on. The latest versions of Revit have improved the ability to design sloped piping, though it can be time consuming if you need to connect multiple sloped pipes together and retain the slope with the correct fittings. The plumbing design also requires lots of piping in small spaces. In addition, plumbing design in AutoCAD is typically schematic in nature, so it requires a shift in mind-set for designers to start thinking of their components as real-life objects and how they will be installed during construction.
Here is some advice on common situations plumbing designers face in Revit.
Time savers: Designers transitioning to Revit often comment that it takes more time to accomplish a task in Revit than it does in AutoCAD. Consider the following to shave time from your workflow:
- Revit is a graphical database. Plumbing involves repetitive design components, so if you save common designs in groups you can reuse them on future projects—similar to blocks in AutoCAD. In Revit, it can be faster to reconfigure the design than to start from scratch. GHT Limited’s team designed a standard pump room with all the components and piping in Revit, and created a group. Copying this standard into new projects and reconfiguring it has saved us many billable hours when the building types are similar. As we all know, no two buildings are exactly alike when it comes to the layout and utility connections, though in many cases you should be able to use similar types of pumps, fittings, and accessories.
- If you’re under deadline pressure and have to delegate plumbing work to colleagues who are not proficient in Revit, they can draw in CAD and the files can be linked to a drafting view, and later incorporated into Revit. Any changes required on the CAD file can be made in the CAD file, and you can manage the link to Revit for automatic updates. This is most helpful if you are new to using Revit and are under pressure to get your portion completed on time. Once you become more efficient in Revit, we would recommend avoiding this practice, as it can decrease the operational speed of the overall Revit model and reduce productivity. In addition, we have found difficulties with plotting sheets linked in from CAD with respect to fonts and other items that are not necessarily compatible with Revit.
- Drafting views create a view showing details that are not directly associated with the building model, like riser diagrams and detail sheets. This approach works well for supporting information, like riser diagrams, cover sheets, and details.
- Revit lets you design pipe placeholders. This is especially helpful for large buildings; you can simply touch a button and they update throughout the model. However, many users have found it more useful to complete the work within standard Revit piping systems and change pipe sizes as required by selecting individual sections or whole systems in place of this element. In addition, we recommend using placeholders only during the schematic design phase.
- If you have a pipe that runs above and below the floor, the program has tools that make it easy to tap into pipes at the same and different elevations. It also has a visibility that shows when piping is below the view range; this is discussed in more detail in the section on visibility
- Typically you won’t know all pipe sizes until the layout is finished, but that doesn’t mean you should wait to get started until the end of the design process. Tag each pipe with an estimated size before you exit your drawing; when you go back, you can quickly update the information if necessary
- Practice every day whether you’re working on a Revit job or not. Even spending 10 minutes a day using Revit can help you maintain your skills, and reduce retraining time in the future.
Visibility: Some plumbing designers express difficulty with graphics and visibility, especially in regard to printing, with Revit. Part of the solution lies in your view and workset:
- Elements can be hidden or misplaced outside the floor plans. Adjusting visibility graphics allows you to cut the view depth lower than the floor plan. For example, the standard view will not show a drain in the slab. To make it show up, set the visibility view depth lower. You can extend the view into “beyond” mode, which changes line work—a dashed line means it’s not on that level, but it does exist. This may also result in structural or architectural elements showing up along with the below-slab piping. Be aware that this may cause plotting and clarity issues with the drawings when submitted to the authority having jurisdiction (AHJ) or the owner. An alternate solution would be to modify the hidden object by extending it above the floor in order to achieve the visibility.
- Make sure you are in the correct workset. Use filters to display plumbing equipment and pipes in the plumbing views, add all of your components to the plumbing workset, and complete all design in that space. This will enable you to print only the components you want to see and filter out what you don’t want to see.
- Using the underlay option in the properties dialogue box while in a floor plan allows you to see a phantom view of piping or equipment below the floor level you are working in. This is helpful for coordination and layout of pipe runs and riser locations, as well as avoiding conflicts.
Connections: In Revit, plumbing connections are typically shown on the MEP model, not the architect’s model. When an architect updates the model and moves a restroom or deletes a wall, the MEP model assumes the plumbing host is still there. As a result, Revit won’t allow the modification. You can’t just “grab and rotate” the plumbing when an architectural change happens; you have to redo the connections. To speed this process:
- Create a Group and keep it in general relationships; don’t connect directly to fixtures until the architect tells you that no more changes will be made, to avoid having to disconnect and reconnect all piping. We consider it a best practice to not host plumbing piping on objects, as it can save significant time when the architectural background model changes.
- Remember to pay attention to deliverables. It’s not always cost-effective to show every single plumbing connection in Revit, especially for projects where you anticipate a lot of last-minute changes. Waiting to make final connections until floor plan decisions are reasonably complete adds order and flexibility.
Document coordination versus full documentation: There are times when it is appropriate to use Revit for document coordination rather than full documentation. The most important factor in success with this approach is making that decision at the beginning of the job. The cost to fix plumbing mistakes later is comparably high, because water goes through the entire building and can’t be modified in sections. The project team and owner must be on the same page from day one; they must agree on the approach and stick with it.
- Before beginning the design, ask what level of detail is required and clarify the deliverable. Can modeling stop below 2-in. diameter pipe? Can it be performance based? The plumbing only needs to be defined as far as the subcontractor will need it to install, some of which can be done in AutoCAD.
- In our experience, full Revit documentation has worked best on complicated projects where many changes are expected. When using Revit for document coordination only, be strategic in identifying the areas that typically present clash problems. The MEP can’t be fully responsible for all areas due to the lack of exact materials, lack of control over the installation sequence that occurs in the field, and level of contractor experience
- Either way, the use of Revit allows contractor questions to be answered more quickly, because there is more information about the design. The model allows you to visualize the final product on the screen before it’s constructed in the field. And as the level of detail in Revit increases, the speed follows suit. Theoretically, the use of BIM should result in a much better coordinated set of plans which, in turn, should minimize requests for information (RFI) during construction and help keep the project on time and budget.
- Revit also provides a benefit in coordinating with other disciplines. Sloping pipes take up a lot of room in the ceiling plenum, where everyone’s fighting for space. Revit can make collaboration easier for plumbing designers, as they can see the ductwork, cable trays, etc., that are already there, and help the architect set the final ceiling height throughout the building. Ceiling plenum coordination is a significant benefit in areas like Washington, D.C., where height limits put ceiling space at a premium.
Juncheng (James) Yang is a Senior Associate and Plumbing Section Head at GHT Limited. He has more than 15 years of experience delivering highly creative, technically exceptional plumbing designs for commercial, governmental, and institutional projects.