A water-cooled chiller plant can be more efficient over the life span of the system and will be less costly than an air-cooled chiller plant
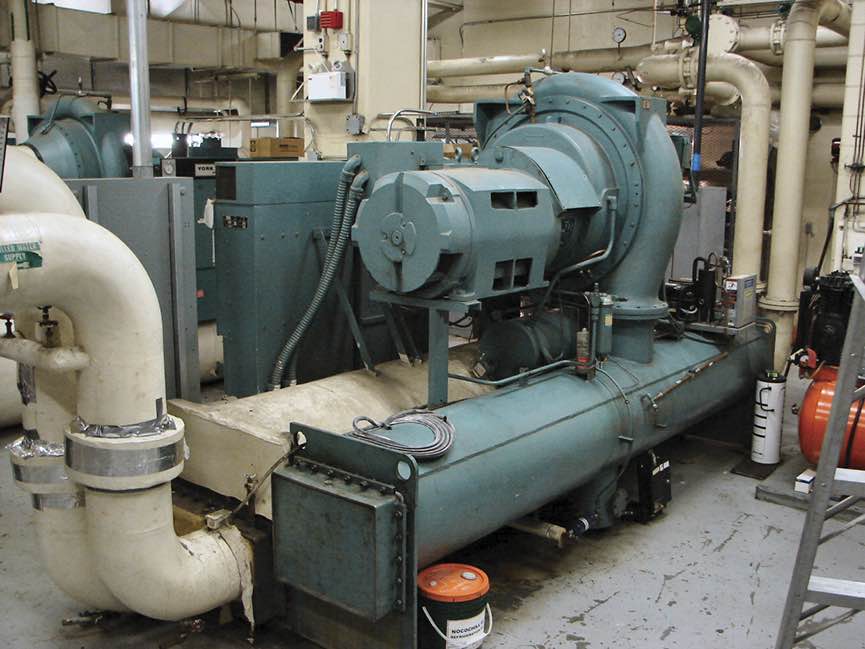
Learning Objectives
- Discuss the key differences between an air- and a water-cooled chiller plant, detailing efficiencies, initial cost and life cycle analysis.
- Understand the key components to each plant type and operations and maintenance needs.
- Determine when to choose an air- versus a water-cooled chiller plant.
As a consulting engineer, knowing when to design an air-cooled chilled water plant or a water-cooled chilled water plant can be a challenge. While the systems are similar, they have fundamental differences that will address unique project goals.
This article will explain the components of each plant and present clear guidelines for optimized use of both plants, depending on the building type, size and client goals. This article will review the advantages and disadvantages of each system bases on size, noise control, cost and efficiencies. The primary argument is that in most cases water-cooled chilled water plants provide the most long-term benefits in terms of energy and cost savings, despite the higher upfront costs.
Plant components
It is important to understand the components of each plant type.
An air-cooled chilled water plant consists of an air-cooled chiller, located outside of the building; primary and secondary pumps; expansion tank; air separator; and some form of chemical treatment. The pumps are arranged in a primary/secondary arrangement or in a variable primary pump arrangement. See figures 1-3 for images of air-cooled chiller plant diagrams and an installed air-cooled chiller.
A water-cooled chilled water plant consists of a water-cooled chiller, typically located inside the building. They also can be placed outside the building and include chilled water pumps, an expansion tank, an air separator, chemical treatment, cooling towers located outside of the building, condenser water pumps, makeup water to accommodate evaporation of the condenser-water and chemical treatment.
The chilled water pumps are arranged in a primary/secondary arrangement (more common in a campus or multiple building arrangement) or in a variable/primary pump arrangement, which is the most common arrangement for individual building system designs. See Figure 2 for an example of an installed water-cooled chiller.
Comparing the options
For illustrative purposes, a 200-ton air-cooled chiller plant will be compared to a 200-ton water-cooled chiller plant. A primary-secondary pumping arrangement consists of a primary loop in which the water is pumped through the chiller constantly (mostly used in the past) or variably (more common today) to produce the desired chilled water temperature. The secondary loop consists of a pump (or pumps) that pulls the chilled water from the primary loop and pumps it through the building loop to the air handling units, fan coil units or to whatever piece of equipment is being used in the building to deliver conditioned air.
The secondary pump(s) can either operate in constant speed or variable speed, depending on the type of controls for the system. If the secondary pump(s) operate in variable speed, the pump speed will vary based upon the pressure in the building loop piping system. The chilled water flow through the respective coils at the AHUs and FCUs is controlled by either a two- or three-way control valve. Commonly, three-way valves are used to maintain flow through a section of pipe, typically at the end of a long run or to maintain a minimum flow through a coil or piping system.
A differential pressure sensor typically located two-thirds of the way downstream in the longest pipe run in the building loop; it will control the speed of the secondary pump(s). When the control valves at the coils begin to close, the pressure in the building loop will increase, which slows down the speed of the secondary pump(s) to counter the building’s decreased cooling demand.
In the same manner, when the control valves begin to open to allow more chilled water flow, the pressure in the building loop will decrease, which will increase the speed of the secondary pump(s) to keep up with the building demand. There also should be a decoupler between the primary and secondary loop. See Figure 3 for a typical primary/secondary loop piping arrangement.
See Figure 4, which shows the different components between a water-cooled chiller system and an air-cooled chiller system.
Selecting a chilled water plant
There are five key considerations of each plant type.
1. An air-cooled chiller plant occupies less square footage in a building than the water-cooled chiller plant, typically because only the pumps, expansion tank, air separator, etc. are located inside the building and the chiller itself is located outside the building.
However, the placement of the air-cooled chiller on the exterior of the building introduces a lot of environmental noise and it is much louder than the cooling tower (90 to 100 db compared to 80 to 90 db, respectively) that is located on the building’s exterior in a water-cooled chiller plant system. A sound level increase of 10 db is the equivalent to double the noise.
An air-cooled chiller consists of a compressor and a fan, which both produce environmental noise. The water-cooled chiller plant’s cooling tower only consists of a fan. A compressor generates more noise than a fan, thus cooling towers are quieter during operation.
There are many options or strategic designs that could dampen the noise generated by an air-cooled chiller plant. For example, most air-cooled chillers have an option of a sound blanket, which is an additional cost. Sound barrier walls are also alternatives to dampen the compressor noise to the surrounding environment. Another example would be a steel barrier wall.
2. In terms of costs, there are fewer components in an air-cooled chiller plant, reducing the initial costs of the plant. Depending on the usage of the building and the building owner type, this cost savings could be a game changer.
For example, let’s assume the project is a small office building and the owner plans to resell the building within a few years, an air-cooled chiller is often the most desirable in this scenario. However, if the building is a large high school that will be used by the school district for many years, then a water-cooled chiller plant would be the choice to make.
3. The efficiencies of the two plant types puts the air-cooled chiller plant at a disadvantage when comparing the two. Depending on the size of chiller and type of chiller, the efficiency (kilowatts/ton) at full load varies. The requirements for chillers have become more stringent under newer versions of the International Energy Conservation Code (2015).
For example, if we compare a 200-ton air-cooled chiller with a 200-ton water-cooled chiller, as per the required IECC, their required efficiencies are 1.18 kW/ton and 0.54 kW/ton, respectively. Additional factors that determine the plant’s efficiency include, but are not limited to, the type of pumps and their efficiencies and the overall pumping arrangement, use of variable frequency drives, chilled water delta T, condenser water delta T, location of the plant and sequence of operations.
The equation below shows the relationship between water flow in a system with the system water temperature change.
Btu/hour = 500 x gpm x delta T
Where:
Btu is the cooling or heating load; 1 ton of cooling is equal to 12,000 Btu.
Gallons per minute is the water flow.
Delta T is the change in temperature of the water in the system.
Let us compare the 200-ton plant as described before. As stated above, 1 ton of cooling is equal to 12,000 Btu, so a 200-ton chilled water plant has 2.4 million Btu. The most common chilled water delta T is 12°F; in the equation, the system requires a chilled water flow of 400 gpm, which equates to 2 gpm per ton.
However, if the system has a 16°F delta T, the gpm would be 300 and equates to 1.5 gpm per ton. The higher the delta T in the system, the lower the gpm requirements are to achieve the same heat exchange in the system. If the system requires less gpm then the pump will reduce in size, meaning less pump energy is used throughout the year.
This same concept applies to condenser water and hot water systems. The use of VFDs also reduces the energy consumption of the pumps greatly. For example, a pump that operates at constant speed will use the same power consumption of the pump all the time, whether the building demand is at 100% capacity or at 50% capacity. VFDs turn down the speed of the pump to match the demand in the building, which reduces the power consumption.
In this case, we will consider the chiller and pumps for an air-cooled chiller plant and the chiller, cooling tower and pumps for a water-cooled chiller plant. An average air-cooled chiller plant has an efficiency of roughly 1.5 kW/ton, while the efficiency of a water-cooled chiller plant is approximately 0.85 kW/ton. Obviously, a water-cooled chiller plant is more efficient, but that is not the only factor to consider.
4. It is important to consider the cost of each type of plant. Once again, there are many factors that can impact the cost including labor rates where the plant is being installed, manufacturer of chiller and location where the chiller is being manufactured, the time of year during installation, as well as any site obstacles to overcome. At a quick glance or base comparison of size and cost, the air-cooled chiller plant is more cost-effective. The average cost of an air-cooled chiller plant is roughly $1,300/ton while the water-cooled chiller plant is approximately $1,700/ton. For the same 200-ton chiller plant, the cost of the air-cooled chiller plant would be roughly $260,000 compared to the $340,000 to $400,000 water-cooled chiller plant.
The first cost of the two plants was achieved by using the cost values from RSMeans from Gordian and using a 3% price increase per year for inflation. The following components were used in determining the initial cost of the air-cooled chiller plant; a 200-ton air-cooled chiller, 100 feet of 6-inch black steel pipe, a 5 horsepower pump for the primary pump, a 15 hp pump for the secondary pump, controls and heating, ventilation and air conditioning accessories (expansion tank, air separator, valves, etc.).
Table 1: The table shows the installed price per ton comparison of a typical air-cooled chiller versus a water-cooled chiller plant. Courtesy: Page[/caption]
5. The life cycle analysis of the two types of plants is also important to consider. Many factors contribute to the life cycle of a plant including location of the plant (wear and tear due to weather conditions is fundamental to consider), electricity charge from the energy company, size of the building being serviced and maintenance personnel training and retention. There is also a limitation on the size of an air-cooled chiller, typically the maximum size is 500 tons.
In this example, we will assume a charge of $0.10/kWh. The office building that operates 16 hours per day at 85% load of the plan for 300 days per year. Per Tables 2 and 3, the air-cooled chiller plant would cost roughly $122,400 per year to operate compared to the $69,360 per year for the water-cooled plant.
Table 3: In this case, the average first cost and yearly operating costs of various air-cooled chiller plant sizes are compared. Courtesy: Page[/caption]
As a consulting engineer, knowing when to design an air-cooled chilled water plant or a water-cooled chilled water plant can be challenging. Client goals and site constraints will often serve as reliable guides for the best choices. When thinking of long-term aspects of a building, an owner will see higher cost savings in regard to efficiency with a water-cooled chiller plant.