Variable frequency drives (VFDs) have problems with application and operations; learn how to mitigate common issues.
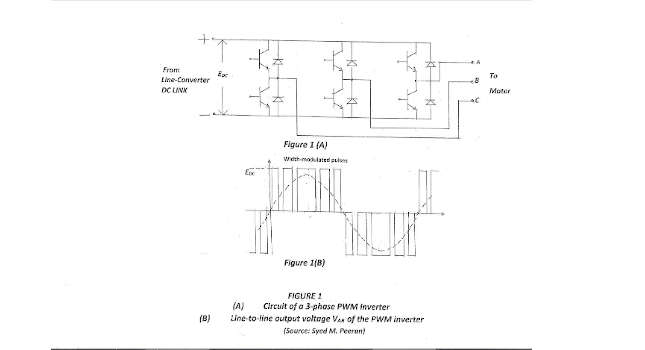
Learning Objectives
- Understand the issues involved with heating in motors and motor bearings.
- Learn about voltage stresses on motor insulation and harmonics in the input current lines.
- Know how electrical engineers can design systems to mitigate these motor problems.
From the time of their entry in the field of electric motor control in the early 1950s, variable frequency drives (VFDs) have continually evolved and been improved upon at a rapid rate. There are two primary reasons for this frenzied growth and refinement. The first is that adding variable-speed operation to most industrial apparatuses, such as pumps, fans, blowers, cranes, hoists, elevators, etc., results in considerable energy savings. The second is that VFDs offer the most efficient method of controlling the speed of ac motors.
Even though the basic technology has been in existence since the early 1950s, the HVAC industry, together with the water, wastewater, and chemical industries, did not promote widespread use of VFDs until the mid-1980s—a campaign that was initiated by a large electrical manufacturer. Since then, there has been fierce competition among VFD manufacturers to improve their products and make them more acceptable. Consumer education on the technology and the accompanying engineering issues also has risen significantly.
As with any emerging technology, several problems and issues have surfaced in the application and operation of VFDs. Four main issues are:
- Additional heating in motors.
- Motor bearing problems.
- Voltage stresses on motor insulation.
- Harmonics in the input line currents.
VFD designers and manufacturers have addressed these issues in different ways, some of them proprietary. Engineering impacts of the above four issues have been mitigated but not fully resolved. The present trend is that most of the VFD designs have now fallen into two main categories: the multipulse front-end type and the active front-end type. In other aspects, most designs offer the same features in control, instrumentation, diagnostics, protection, automation, and auxiliaries. The older current-source inverter (CSI), the line-commutated inverter (LCI), and the voltage-source inverter (VSI) designs have now faded out.
Additional motor heating
Heating, in addition to that caused by I2R losses, in the stator of the motor is due to the non-sinusoidal currents forced into the winding by the VFD inverter. In the older CSI and LCI designs, the motor currents were significantly non-sinusoidal. Motor heating due to the harmonics was an issue of concern.
Motors were often derated to allow for the increased heating. However, with the modern pulse-width-modulated (PWM) VFD-driven motors, the motor currents are very nearly sinusoidal except for a small high-frequency component. This component, whose frequency is in the range of 4 to 16 kHz, is due to the PWM switching of the power devices in the inverter. The high-frequency component of the current causes additional local heating due to the skin effect in the stator winding conductors and in the stator iron teeth due to eddy currents.
Some manufacturers offer output filters to suppress the high-frequency under the trade names of “Sine-wave” and “Matrix” filters. Such filters essentially have series-inductor shunt-capacitor configurations. Output filters are normally housed in the VFD enclosure. Separate output filters also are occasionally used. The series inductor causes additional power loss and heat in the enclosure, lowering the overall efficiency of the VFD a little bit. The benefit gained in caparison with the additional cost and loss of overall efficiency is dubious in many cases.
Motor bearing problems
Motor bearing problems of electrical origin existed even before the advent of VFDs for motor control. It is impossible to constrain the magnetic flux to the stator and rotor iron and the air gap. There is always some flux produced by the stator winding, which links the shaft at the non-drive end (NDE) to the drive end (DE) of the shaft. Because of some magnetic dissymmetry between the NDS and the DE of the machine, there is a net 60-Hz induced voltage, which drives a small current in the axial direction in the shaft. This current finds a path through the shaft, through the two bearings, and through the stator frame. The current causes additional heat and can cause accelerated wear of the bearings. The path of the current is broken by insulating one of the two bearings, usually the NDE bearing. This insulation can be added for a small cost.
A second phenomenon caused by the VFD has been responsible for accelerated wear, minute arcing across the bearing lubricant, “fluting” of the bearings, and eventual bearing failures in many VFD-driven motors. The phenomenon is due to electrostatic induction of a high-frequency voltage between the shaft and the bearing race, causing the film of lubricant to break down electrostatically in the form of a tiny arc. The PWM inverter of the VFD impresses high-frequency pulses on the motor windings. Stray capacitances between the stator winding and the rotor and between the rotor and the stator frame, which normally have a negligible impact upon the operation of the motor, produce a high-frequency voltage across the film of bearing lubricant.
In particular, the winding-to-rotor capacitance and the total capacitance between the rotor and the grounded stator frame constitute a capacitive voltage divider that produces a voltage across the bearings. This voltage discharges in the form of a tiny arc, which causes a small current known as the electric-discharge machining (EDM) current to flow across the bearings. This discharge causes accelerated erosion of the bearing surfaces and eventual destruction of the bearing. Induced voltage, which can cause arcing, is in the range of 5 to 30 V.
One way of avoiding damage to the bearing is to provide an alternative path for the bearing voltage to discharge. Such an alternative path can be provided by a shaft-grounding brush or a ring of conductive fibers that ride on the shaft to continuously ground the shaft. The grounding brush is a copper or a carbon brush riding on a machined surface on the shaft. Because the brush is subject to vibration and wear, it is an item that requires regular maintenance. Excessive vibration and incomplete contact would defeat the purpose of providing the brush.
A ring of conductive fibers, marketed as the Aegis ring, takes care of the vibration problem and is a good solution provided it does not need replacement too often.
Another way of reducing the bearing damage is to provide a rate of change of voltage (dv/dt) filter in the output of VFD. The filter reduces the bearing’s high-frequency voltage.
Voltage stresses in the motor insulation
When driven by the VFD, there are two ways in which the motor stator winding insulation can be stressed over and above the level normal as compared with non-VFD-driven motors:
- The voltage-doubling action of the PWM pulses at the motor terminals.
- The standing-wave phenomena when the cable length approaches the critical length.
The voltage-doubling effect
ac motors are designed and operated such that the magnetic flux density in the stator and rotor iron is at an optimum value. The magnetic material of the stator and rotor is laminated silicon steel. The optimum flux density is dependent upon the grade of silicon steel and the thickness of the laminations chosen by the designer. If the flux density is more than the optimum value, the material is driven into magnetic saturation, resulting in the reduction of efficiency and distortion of the current wave shape. If the flux density is less than the optimum value the motor, it would draw a larger current to produce the same torque.
ac machine theory indicates that the flux density is proportional to the ratio (V/f) where V is the voltage applied to the motor and f is the frequency of the voltage. Therefore, when the motor is driven by a VFD, the motor voltage should be adjusted when the frequency is varied to keep the V/f (Volts per hertz) ratio constant at the design value. This adjustment is to be done by the inverter (the motor converter) of the VFD.
The input to the inverter is the dc voltage produced by the line converter. PWM is a technique used to vary the motor voltage. The power devices in each phase of the inverter are switched on and off at a certain frequency, called the carrier frequency, to generate a train of pulses of varying width such that the average voltage is sinusoidal and the magnitude is adjusted by adjusting the width of each pulse.
Figure 1(A) shows the circuit of a 3-phase PWM inverter. The power devices used are insulated-gate bipolar transistors (IGBTs) shunted by silicon diodes, which help in switching off the IGBTs. Switching on and off is accomplished by a circuit, controlled by a microprocessor, which feeds the gates of the six IGBTs.
Figure 1(B) shows one line-to-line voltage (VAB ) of the output of the inverter. The voltage wave shape consists of positive and negative pulses of magnitude equal to the dc link voltage EDC , whose width is adjusted such that the average voltage is sinusoidal (as shown by the dashed line). Its frequency depends upon the speed demand by the driven equipment. For example, if the load is to be driven at 50%-rated speed, the frequency of the average voltage is adjusted to 30 Hz. Note that Figure 1(B) is not to scale, and the numbers of pulses shown in each half cycle of the average voltage are arbitrarily selected to illustrate the action of the PWM inverter. Actually, for a 30-Hz base frequency and a carrier frequency of 4 kHz, the number of pulses in each half cycle of the average voltage will be 66.
The PWM inverter sends a train of nearly rectangular pulses of the carrier frequency (4 to 16 kHz, typically) to the motor via the motor cable. These pulses travel at a velocity of approximately 100 m/microsecond (329 ft/microsecond). For a career frequency of 16 kHz, the average width of each pulse is approximately 62 microseconds. When the leading edge of the pulse reaches the motor, the pulse doubles in magnitude because the motor’s winding-surge impedance is much more than that of the cable.
A reflected wave is created, which will travel back to the VFD. Therefore, if the cable length is 100 m (329 ft), there will be 62 multiple reflections and doubling of the voltage at the motor terminals in the duration of one PWM pulse. The incident and the reflected waves are attenuated by the cable resistance. Therefore, the motor winding insulation is subjected to pulses of twice the dc link voltage and a high-frequency ringing at the leading edge of each PWM pulse.
The dc link voltage of a 480 V VFD is approximately 648 V in a 6-pulse line converter and very nearly equal to 678 V for the 18-pulse line converters and higher pulse line converters. In 208 V VFDs, the maximum dc link voltage is 294 V. The motor sees pulses of approximately twice the dc link voltage, followed by a high-frequency ringing of which the frequency depends upon the length of the cable.
Recognizing this fact, the National Electrical Manufacturers Association’s Standard MG-1, Section IV Part 31, requires that the inverter-fed motors rated for 600 V or less be designed to withstand a peak voltage of 1,600 V with a rise time of 0.1 microsecond. Motors rated at more than 600 V must be designed to withstand a peak voltage of 2.5 per unit with a rise time of 1.0 microsecond.
The standing wave phenomenon
This phenomenon depends upon the rate of rise of the leading edge of the PWM pulse. The PWM pulses are not rectangular but have a trapezoidal shape having a finite rise time. The rise time depends upon the inherent inductance of the current path in the inverter and the characteristics of the switching devices. Circuit theory indicates that the receiving-end voltage—i.e., the motor terminal voltage—is inversely proportional to COS (2πs/λ), where:
- COS(X) is the trigonometric function cosine of the argument X.
- λ = the wavelength = (the velocity of propagation) x (the time for one cycle), m.
- s = length of the cable from the VFD to the motor, m.
When the ratio (s/λ) approaches ¼, the motor terminal voltage approaches infinity. This length is called the critical length of the cable and depends upon the rise time of the leading edge of the PWM pulse. The critical length is given by the following equation:
s = ϑ * t/2
where
s = critical length, m.
ϑ = velocity of prorogation in the motor cable, m/microsecond.
t = rise time of the PWM pulse, microsecond.
The rise time is typically 0.2 to 0.8 microsecond. It can be increased to approximately 10 microsecond by the addition of a dv/dt filter in the output of the VFD, thus increasing the critical length to approximately 500 m (1,645 ft). The heavier sine wave filter would increase the critical length even more.
Multi-pulse VFDs
Multi-pulse VFDs are those VFDs whose line converters (rectifiers converting the ac input voltage to dc to feed the inverter) are configured with the input phase-shifting transformer to produce a smoother dc link voltage. The pulse number relates to the number of ripples in the dc link voltage in one cycle of the ac input voltage. Multi-pulse operation is possible entirely due to the phase-shifting transformer. The power electronic devices in the converter are uncontrolled silicon diodes.
A single-phase, full-wave rectifier that rectifies in both positive and negative half cycles of the ac voltage is a 2-pulse device. A 3-phase, full-wave rectifier is a 6-pulse device. The phase angle between successive secondary voltages is 120 deg. In a 12-pulse converter, the phase-shifting transformer converts the 3-phase input to 6-phase voltages, which when rectified, produce 12 ripples in the dc output voltage. The phase angle between successive secondary voltages is 60 deg. Similarly, the phase-shifting transformer produces a 3-phase to 9-phase conversion in the case of the 18-pulse converter. The secondary voltages are mutually displaced by 40 deg. Incidentally, the number of power electronic devices is equal to the pulse number.
Figures 2, 3, and 4 show the connections of the input transformer and the power devices for 3-phase line converters with 6, 12, and 18 pulses. In Figure 3, each limb of the transformer core carries two secondary windings in addition to one primary winding. For example, the red-colored windings (Pa, Sa1, and Sa2) are wound on one limb of the transformer core.
In Figure 4, the transformer for the 18-pulse line converter has five secondary windings and one primary winding in each phase. Like-colored windings shown in Figure 4 are wound on the same limb of the transformer.
See Table 1 to understand the operation of multi-pulse converters. For the 2- and 6-pulse converters, the input transformers are the normal single-phase and 3-phase transformers. In the case of the 12-pulse converter, the transformer performs 3- to 6-phase conversion. In other words, two sets of 3-phase voltages are created, mutually displaced by 60-deg electrical. Each set is fed to a 3-phase bridge rectifier. The dc outputs of each rectifier are connected either in series or in parallel.
Similarly, the transformers perform 3- to 9-phase conversion in the case of the 18-pulse converter. Three sets of 3-phase voltages are created, mutually displaced by 40-deg electrical (see Figure 5). The transformer has five secondary windings and one primary winding on each limb. Like colored phasors shown in Figure 5, the voltages are produced by the secondary windings of the same phase. The three sets of 3-phase voltages are A1B1C1, A2B2C2, and A3B3C3. Therefore, there are nine voltages of equal magnitude mutually displaced by 40 deg.
It can be shown that if the winding Sa1 has 100 turns, the windings Sa2 and Sa3 should have 39.49 turns and the windings Sa4 and Sa5 should have 74.22 turns each to produce a set of balanced 9-phase voltages. The three sets of 3-phase voltages (A1B1C1, A2B2C2, A3B3C3) are fed to three 6-pulse converters. The dc outputs are connected either in series or in parallel.
A similar phasor diagram can be drawn for the 24-pulse converter. In this case, the transformer performs a 3- to 12-phase conversion. Each limb of the transformer must carry nine secondary windings in addition to one primary winding.
Table 1 shows that the number of power electronic devices required for multi-pulse conversion is equal to the pulse number except in the case of the single-phase, 2-pulse converter. The peak-to-peak ripple voltage progressively reduces as the pulse number increases.
Multipulse line converters
Pulse number | Input transformer phase conversion | Phase angle (deg) between consecutive phase voltages | Line converter configuration | Number of rectifying devices | dc link voltage | dc peak-to-peak ripple | ac line current harmonics |
2 | 1- to 1-phase | 180 | 1-phase full-wave bridge | 4 | 0.9 E
(Note 1) |
1.414 E | 1, 2, 3, 4, …
|
6 | 3- to 3-phase | 120 | 3-phase full-wave bridge | 6 | 1.35 EL
(Note 2) |
0.189 EL | 1,5, 7, 11, 13, 17, 19, … |
12 | 3- to 6-phase | 60 | Two 3-phase full-wave bridges in series or parallel | 12 | 2.78 EL for series
1.39 EL for parallel |
0.096 EL for series
0.048 EL for parallel |
1,11, 13, 23, 25, 35, 37, … |
18 | 3- to 9-phase | 40 | Three 3-phase full-wave bridges in series or parallel | 18 | 7.31 ES for series
2.436 ES for parallel (Note 3) |
0.111 ES for series
0.0372 ES for series |
1, 17, 19 35, 37, … |
24 | 3- to 12-phase | 30 | Four 3-phase full-wave bridges in series or parallel | 24 | 9.77 ES for series
2.44 ES for parallel |
0.083 ES for series
0.02 ES for parallel |
1, 23, 25, 47, 49, … |
Table 1: For the 12-, 18-, and 24-pulse converters, the input transformer performs 3- to 6-phase, 3- to 9-phase, and 3- to 12-phase conversions. As the pulse number increases, the ripple in the dc link voltage reduces and the lower harmonics in the ac line current are suppressed. Courtesy: Syed M. Peeran
Notes:
1. E = Transformer secondary voltage, V rms.
2. EL = 3-phase line-to-line voltage, V rms.
3. ES = Transformer secondary voltage, V rms (see Figure 4).
An obvious question is, “How is the pulse number related to the harmonics of the input line currents?” Consider the 6-pulse converter. There are six devices in the converter. The devices conduct in pairs. Each device conducts for a period of one-third of a cycle (120-deg electrical). The pulse number indicates the number of times the devices are switched in one cycle. The currents in the transformer’s primary windings consist of positive and negative pulses of 120-deg duration each. The transformer input line currents are stepped waves that have six steps in each cycle. The currents are non-sinusoidal because the converter, together with the dc link capacitor and inductor, is basically a nonlinear device that draws non-sinusoidal current even though the input voltages are sinusoidal.
Therefore, the currents have the fundamental (60 Hz) and harmonic components. Now, the VFD is a 3-wire device. There is no path for a neutral current to flow. Therefore, the input line currents do not have the third harmonics and multiples of the third (the triplen) harmonics. In addition, because the conduction of the devices in the positive and negative half cycles is identical (ideally), there is no dc component and there are no even-ordered harmonics. Therefore, the input line currents contain only odd-ordered harmonics in pairs, such as 1, 5, and 7; 11 and 13; 17 and 19; etc. The lowest-frequency harmonic is p-1, where p is the pulse number. A general equation for the harmonics is as follows:
h = n * (p +/- 1)
Where
h = harmonic order
p = pulse number
n = 1, 2, 3, 4, …
An 18-pulse converter would, theoretically, produce only 17th-, 19th-, 35th-, 37th-, 53rd-, and 55th order harmonics. The magnitude of the current decreases as the harmonic order increases. This is because the circuit impedance increases with the harmonic frequency, thus permitting a smaller current. What this means is that the 18-pulse converter draws a “cleaner” current than a 6- or a 12-pulse converter. This is the reason for the increasing use of 18- and higher pulse converters.
The harmonic orders given by the above equation are the characteristic harmonics for a specific pulse number. However, because of slight irregularities in the conduction of the devices, unequal impedances in the three phases, and imbalances in the input voltages, small amounts of non-characteristic harmonics are also created. For example, it is not unusual to find an 18-pulse converter producing small amounts of 5th, 7th, 11th, 13th, etc. harmonics in addition to its characteristic harmonics.
Practically, unbalance in the input voltages is the primary cause of the production of the non-characteristic harmonics. This fact constitutes a weakness in the multi-pulse design. Consider the 18-pulse design: A balanced set of 9-phase voltages can be produced only if the turns ratios of the windings in the phase-shifting transformer are 100: 74.22 and 100: 39.49. Because the number of turns in a transformer winding can only be integers (74 or 75, not 74.22), it is very difficult to produce a set of balanced 9-phase voltages.
The situation is further aggravated if the input 3-phase voltages from the utility are unbalanced. Imbalance of 2% to 3% is not unusual in the utility input voltages. Yet, despite the creation of the uncharacteristic harmonics, 18- or higher pulse VFDs are preferable to the 6-pulse VFDs from the harmonics point of view. The additional cost and possibly a larger footprint is often justifiable because no other means of harmonic mitigation is required.
Table 2 shows the harmonics produced by a typical 6-pulse PWM VFD and a typical 18-pulse PWM VFD.
Harmonics produced by typical 6- and 18-pulse VFDs
Harmonic order | Frequency, Hz | Typical 6-pulse VFD
harmonic current, % |
Typical 18-pulse VFD
harmonic current, % |
1 | 60 | 100.00 | 100.00 |
5 | 300 | 31.3 | 2.6* |
7 | 420 | 9.3 | 1.6* |
11 | 660 | 6.4 | 0.7* |
13 | 780 | 3.4 | 0.4* |
17 | 1,020 | 2.4 | 1.5 |
19 | 1,140 | 1.9 | 1.0 |
23 | 1,380 | 1.1 | 0.1* |
25 | 1,500 | 1.1 | 0.1* |
29 | 1,620 | 0.7 | 0 |
31 | 1,860 | 0.6 | 0 |
35 | 2,100 | 0.5 | 0 |
37 | 2,220 | 0.4 | 0 |
41 | 2,460 | 0.4 | 0 |
43 | 2,580 | 0.4 | 0 |
Total harmonic distortion % | 33.64 | 3.64 |
Note: * indicates non-characteristic harmonics.
Table 2: The numbers are taken from the author’s experience in field testing of VFDs. These numbers vary with the VFD make and model. It is best to obtain the harmonic spectrum from the VFD manufacturer
Active front-end VFDs
Active front-end (AFE) VFDs have come into use only recently and are gaining rapid acceptance. Figure 6 shows the configuration of the line and the motor converters. AFE VFDs are basically 6-pulse VFDs, with the exception that the line converter is not the uncontrolled diode bridge rectifier as in other 6-pulse VFDs but uses controllable power devices, such as IGBTs. The configuration of the line converter is the same as that of the motor converter.
Operation and control are, however, different. The line converter operates at a base frequency of 60 Hz while the motor converter operates at a variable frequency (typically 6 to 66 Hz) depending upon the desired speed of the driven motor. The line converter also is provided with PWM switching of the IGBTs, but the switching logic is such that that the converter draws nearly sinusoidal current. In the case of the motor converter, the PWM-switching logic is such that the motor’s root mean square (rms) voltage is proportional to the inverter base frequency to keep the ratio V/f (Volts per Hertz) nearly constant. The PWM carrier frequency is generally not the same as in the motor converter.
Because the IGBTs are switched at a high frequency, the AFE VFD requires a large inductor-capacitor filter at the line end. The filter is provided integral to the VFD. It increases the footprint of the VFD, but not as much as the phase-shifting transformer of the 18-pulse VFD. Therefore, in general, the AFE VFD has a smaller footprint than an equivalent multi-pulse VFD.
Because of the PWM switching of the devices in the line converter, the AFE VFD draws nearly sinusoidal currents from the line. The harmonic performance of the AFE VFD is about the same as that of an 18-pulse VFD. However, the AFE VFD is not as sensitive to unbalanced voltages as the 18-pulse VFD.
Because the line converter is configured with IGBTs, the converter is bidirectional. An AFE VFD can provide regenerative braking of the motor, which is a feature that is not available with other 6-pulse and multi-pulse VFDs. The roles of the line converter and the motor converter can be easily reversed when the motor is braked, thus recovering the kinetic energy of the rotating motor. There is no need to provide dynamic braking resistors. This is a desirable feature in some drives requiring repeated reversals.
Passive harmonic filters
Passive harmonic filters provide an inexpensive way to mitigate the harmonics created by VFDs and other harmonic sources. Passive filters are best used as individual filters for each small 6-pulse VFD or as common filters connected to a motor control center (MCC) supplying several VFDs. Basically, the passive filter is a series inductor-capacitor resonant circuit that is tuned to a specific frequency and connected in parallel with the VFD. The filter consists of a 3-phase iron-cored inductor in series with a wye-connected or a delta-connected 3-phase capacitor. While specifying the filter, one must be aware of the following electrical properties of the passive filter:
- At the resonant frequency, the filter offers a low impedance (mostly resistive). Therefore, when connected in parallel with the VFD, it bypasses to ground that harmonic to which it is tuned. For example, if the filter is tuned to the 5th harmonic (300 Hz), it will bypass the 5th harmonic to ground and negligible 5th harmonic current will flow in the electrical system.
- At frequencies above the resonant frequency, the filter will act as an inductor.
- At frequencies below the resonant frequency, the filter will act as a capacitor. Therefore, for the power frequency 60 Hz, the filter capacitor will provide power factor correction.
Passive filters are rated in terms of the reactive kilovolt amperes (kVAR) provided by the filter capacitor at the power frequency. For example, a 60 kVAR 5th harmonic filter will provide 60 kVAR of reactive power at 60 Hz for power factor correction while the inductor is such that the resonant frequency is 300 Hz. When a passive filter is connected, the overall efficiency of the distribution system is increased because of the increase in power factor.
How should the engineer specify the passive filter for a particular VFD? Most harmonic-analysis programs can model the passive filters. To begin with, the kVAR rating of the filter is assumed to be approximately on-third of the VFD kilovolt ampere (kVA) rating. Then the harmonic analysis is rerun. The kVAR rating is then adjusted and harmonic analysis is repeated until satisfactory results obtained.
Under conditions of light load, the 60-Hz reactive power supplied by the passive harmonic filter can cause the system to have a leading power factor. System voltage would then increase above the nominal voltage. To avoid this situation, the passive filter consists of two or three parallel filters, which can be switched depending upon the load in the system.
Active harmonic filters
Active harmonic filters (AHFs) are now being made and marketed by several companies. The filters generally are not tailored for a specific situation or system, as the passive filters are, but they can adjust dynamically to the demand for harmonic correction. AHFs are available for low-voltage (480- and 208-V, 3-phase) and medium-voltage (4,160 V, 3-phase) applications. AHFs operate as a combination of multiple passive filters (to bypass currents of different frequencies) and different magnitudes (to reduce the harmonics in the monitored circuit below a desired level).
To perform dynamically, the AHF senses the magnitude of the harmonics in the circuit. Such sensing is done by current transformers and an internal microprocessor that performs fast Fourier transform (FFT) of the input waveform. The AHFs contain active elements, such as IGBTs, and combinations of inductors and capacitors. The exact circuitry of AHFs appears to be a closely guarded secret by manufacturers, but as with passive harmonic filters, their basic function is to absorb harmonic currents dynamically.
AHFs are best suited as common filters connected either to a switchgear or an MCC bus supplying many VFDs. AHFs are rated in terms of the maximum root mean square of the total harmonic current absorbed by the filter. Ratings of 50 to 300 amps are available. Multiple AHFs can be connected in parallel to obtain higher ratings. AHFs also can provide variable power factor correction. However, unlike passive harmonic filters, they will not create a leading power factor situation at times of light load on the VFDs. They are also not likely to adversely interact with existing filters, active or passive, in the system.
How does one select an active harmonic filter for a particular system? AHF manufacturers provide simple spreadsheet-based programs to determine the rms current rating of the filter if the total kVA rating of the VFD is known. Alternatively, system-analysis software, such as SKM, PowerTools, or ETAP programs, can be used to determine the rating even though these programs are not presently capable of modeling active harmonic filters.
Syed M. Peeran was formerly with CDM Smith, Boston. He is an emeritus member of the Consulting-Specifying Engineer editorial advisory board.