Specification writers can play a key role in a project’s success, but the design team must use their skills effectively.
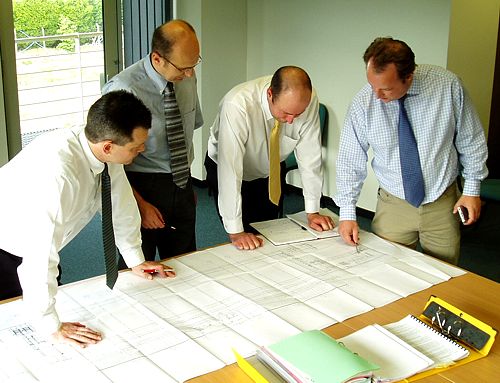
Designers delegate much of their work to specialty consultants, with one of the more common specialists being specification writers (spec writers). These specialty consultants must be integrated successfully into the design process to help achieve the desired result—a design that clearly and accurately describes the design intent and meshes with the drawings.
Spec writers typically specialize in a specific type of design document rather than a specific technical field; this sets them apart from other specialty consultants who are experts in one field. They often are required to write sections describing work for 20 or more practice areas, and few are fortunate enough to have significant practical experience in all of these fields. Qualified spec writers can be very effective when used appropriately, while improper use of these consultants can be detrimental to a project. This article presents recommendations regarding proper use of spec writers.
During a number of recent projects on which we spent tens of thousands of dollars of the owner’s money consulting on customized systems and project-specific materials, issues arose when the contractors realized that the carefully developed drawings did not match the non-projectspecific (“canned”) specs. The generic specs included various items that did not mesh with the design intent or the design drawings. Several product designations were outdated, and some materials were no longer available. In the end, the owners were forced to pay out hefty change orders to obtain only a portion of the items that the architect intended and drew.
Changing from a $7/sq ft adhered roofing system to a $15/sq ft mechanically fastened system, or changing from a $3 zinc-plated brick tie to a $6 stainless-steel adjustable anchor, can be devastating for a large project. Failing to account for such seemingly minor changes can result in major cost increases (see Figure 1).
There seem to be three main causes of the trend to specialize and delegate design responsibility for specifications. The first cause is firms’ desire to spread out design responsibility and risk. The second is their desire to allow consultants who are more experienced and competent in the specialty fields to develop specifications directly, for increased accuracy and precision (as well as risk sharing). The third cause is often-aggressive design schedules that do not allow enough time for a single firm to adequately conduct the full design process.
Recommendations
There are inherent risks with spreading design responsibility among various parties, most obviously loss of coordination and deviation from the design intent. While working through recent projects with various project delivery methods, we have found that how the design team communicates with the spec writer can play a key role in a project’s success or failure. The following are recommendations for how to use a spec writer efficiently, whether he or she is an outside consultant or a professional who is part of your own firm.
-
Allow the spec writer to participate in the design meetings and understand the basis for design decisions and product selection. Keep the spec writer in the loop, including all Friday-afternoon epiphanies and 11th-hour clarifications.
-
Perform a multi-step specification development and review process.
Step 1:
The primary designers should provide short (one- to two-page) written summaries (design narratives) of the intended content for each specification section prior to composing the actual specs. The architect can include product literature for essential components when appropriate, such as for the desired window and mechanical systems. The spec writer and the related consultants should review these narratives and provide comments. This process will encourage discovery of discrepancies early in the design process, when there is stilltime to debate and resolve the issues.
Steps 2 and 2A:
Direct your consultants and your in-house team to review the relevant specifications after the writers have made significant progress. In our experience, at least one review during both the design development phase and the construction documents phase typically is warranted. Leave enough time for revisions, discussions, and face-to-face meetings. Whether face-to-face meetings are warranted will depend on many factors, such as the complexity of the building systems and the spec writer’s experience with the systems.
Step 3:
Perform final checks of all specs prior to issuance. As noted above, leave a reasonable amount of time for revisions.
-
Perform multiple reviews of at least the general content of the specs if your budget for consultants and other specification review efforts are limited. Multiple, more cursory reviews are often more effective than a single exhaustive review. If the primary designers perform only one review, confusion regarding markups can lead directly to errors.
-
Consider instructing specialists who are skilled in a particular technical field to write the related specifications if you are designing a complex and/or customized system. Also consider doing so if the system is one of particular interest to the owner, or if the project team is simply not experienced in a high-risk discipline. This practice is already common for hardware and mechanical systems, though it is currently less customary for other specialty fields such as building envelopes and fire protection.
-
Direct bidding contractors to provide written documentation of any conflicts uncovered during their pre-bid review of the project documents. Require them to provide a letter stating that they have carefully reviewed all documents and reported any significant conflicts. Doing so will not necessarily prevent disputes, but when combined with the other procedures noted above, it will further encourage coordination and quality.
Construction managers often base their bid packages primarily on the specification sections rather than the drawings. Therefore, certain materials shown on the design drawings may be difficult to obtain from the successful subcontractor unless the specifications accurately complement the drawings. Construction managers may be reluctant to absorb the costs related to bid package omissions and conflicts, regardless of whether or not their bid package organization was a factor. Careful coordination of specifications and other design documents will result in a more efficient process and ultimately save the owner money.
Case studies
The following case studies illustrate some recent successes and failures regarding the development of architectural specifications for building envelope systems.
Case Study 1—
During a recent schedule driven project in Massachusetts, the design team discussed the plan for the design process with the architect prior to the schematic design phase. The team elected to organize several day-long meetings among various consultants (e.g., the structural engineer and building envelope consultant) and several members of the architectural staff (e.g., designers, drafters, and managers). After discussing some of the more complex and costly portions of the work, the architect directed us and other consultants to write certain specifications. The architect reviewed our specs, and then we discussed his comments and revisions face to face. The schedule, though aggressive, provided adequate time for all parties to review, comment on, and make the necessary revisions to the specifications. Later, after we modified portions of the design, the relevant parties updated and proofed the specs again. The primary design team also reviewed and proofed other specifications written by the spec writer, who wrote the remainder of the specification sections for the project. While unable to attend in person, the spec writer was electronically connected to all meetings, helping to assure that he would receive the correct information.
We are currently partway through the preconstruction phase (all significant subcontractors are on board, and the architect has reviewed most of the submittals), and to date, the contractor has not proposed any significant change orders. In fact, the architect has been able to resolve the few requests for information (RFIs) by directing the subcontractors to the appropriate line items in the design documents.
Case Study 2—
A recent project saw complications because the spec writer, who was a member of the architectural staff, was not familiar with the design intent or drawings. The design team performed significant research to determine a compatible membrane flashing product that would adhere well to the job site substrates. Unfortunately, the spec writer was not privy to this research, and he specified incorrect information about the type of membrane flashing product required at several hundred window openings. An inappropriate product that was used on a previous unrelated project found its way into the project specification. The error was likely due in part to a particularly aggressive design schedule that did not allow time for multiple reviews of the specifications. Ultimately, the owner and design team had to choose between accepting the lesser product that was listed in the specification (and thereby an increased risk of water penetration) and approving a $50,000 change order for the “cost increase” related to the desired flashing product.
Case Study 3—
The owner and architect were forced to accept an inferior window system instead of the quality system intended for a school in northern Massachusetts. Because the architect’s window specification was vague and poorly written, the team was required to accept a field-assembled (“knock-down”) window system rather than the prefabricated punched window units that were desired. The installers’ poor execution combined with the low-quality components led to serious problems with the windows. Eventually, the team dismissed the original window subcontractor. The team is currently considering removing and replacing all of the new aluminum windows, and the project’s completion date is at risk. If the spec writer had been involved in the design process, he or she could have drafted accurate specifications that would have prevented this problem.
Case Study 4—
Two buildings constructed in southern New England have substantial water damage due to the substitution of a substandard through-wall flashing material. The problem was compounded by confusion among the various contractors about who was responsible for the materials required at the transitions between wall systems. Carefully written specifications probably could have prevented such confusion and performance problems. The specifications on this project were extremely vague and provided little direction to the subcontractors (and to the architect’s construction administration team) about what was required and what might constitute an acceptable substitute. Modest additional design effort likely would have prevented a $250,000 to $500,000 repair cost, not including any replacement of water-damaged interior finishes, or legal fees.
Summary
Limiting the scope of the spec writers may save a few thousand dollars during the design phase, but it can result in expensive conflicts after construction contracts are awarded. The results will likely be negative regardless of which project delivery system is used. In our experience, a diligent, experienced spec writer can be a valuable member of the design team if his or her skills are used properly, as summarized below:
-
Keep spec writers in the loop throughout the design process, including all appropriate meetings and last-minute changes.
-
Prepare preliminary design narratives for the spec writer to follow as a roadmap in preparing project-specific specifications.
-
Allow the project architect and related consultants to perform multiple reviews of the specifications, leaving adequate time for discussion and revision.
-
Consider directing consultants who are skilled in a specific technical discipline to write specification sections that describe systems that are complex or high risk, and direct the architect and other design stakeholders to perform review efforts similar to those noted above.
-
Bear in mind that “canned” specifications cannot embody the breadth of design intentions that most modern projects require.
-
Remember that a project is only as successful as the least accurate aspect of its design; poorly written specifications, or specs that do not complement the drawings, often cost the client money and diminish performance
About the author
McCowan has eight years of service investigating building envelope problems and providing construction administration services as well as design consulting services. He also is a published author and has presented on the topic of building envelope engineering.