The National Fire Protection Association (NFPA) revises NFPA 70E: Standards for Electrical Safety in the Workplace every three years. The latest version, the 2012 edition, was released in September 2011. Here, a group of experts explain how the current version of NFPA 70E affects how engineers specify and design electrical systems.
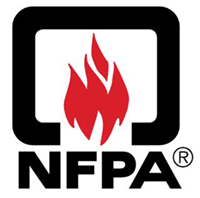
Meet our NFPA-70E roundtable participants
- H. David Chandler, PE, senior associate, Newcomb & Boyd, Atlanta
- Brian P. Martin, PE, electrical discipline lead, CH2M Hill, Portland, Ore.
- Vince Rea, PE, LEED AP BD+C, principal, senior electrical engineer, Healthcare Division, TLC Engineering for Architecture, Orlando, Fla.
- Joseph Weigel, owner, president, Electrical Safety Works, Nashville, Tenn.
Q: Describe the types of services your firm offers that relate to NFPA 70E.
Chandler: Our firm offers short-circuit protection and overcurrent protective-device coordination studies; arc-flash hazard analyses; and single-line-diagram generation, preparation, and updates.
Martin: We provide consulting and design services for both greenfield and existing facilities. These services include training, single-line generation and updates, arc-flash and shock-hazard analyses, and arc-flash and shock-mitigation recommendations.
Rea: Our firm offers electrical vulnerability and short-circuit analyses, incident arc energy (arc flash) and protective device coordination studies, and full electrical design and consulting for building systems.
Weigel: The types of services Electrical Safety Works offers include:
- Information seminars (in person and online) about NFPA 70E compliance, electrical safety, and risk management
- Expert articles on NFPA 70E for safety and engineering magazines
- Electrical safety program review and auditing
- Review of and consultation on electrical safe work practices for commercial and industrial clients
- Client review of commercial offers for arc-flash hazard analysis to establish vendor competency and best value
- “Safety by Design” technical seminars for consulting engineers.
Q: Does your firm provide arc-flash hazard studies? If so, has the number of clients requesting arc-flash studies increased, decreased, or stayed the same during the past year? The past 18 months?
Chandler: We are doing studies for an increasing number of clients. There seems to be more awareness of the need to perform these studies, although in most cases we have approached our clients with the offer of these services, as opposed to clients seeking these services without solicitation.
Martin: We have seen an increased number of clients requesting arc-flash studies, but this usually takes place during the design phase. It is rare that our clients do not request an arc-flash study at some point during the design phase, but it is still fairly uncommon to see arc-flash studies being included in the RFP for greenfield facilities. Arc flash usually becomes a topic of conversation as soon as the operations side of the facility gets involved.
Rea: TLC does perform arc-flash analysis studies. We have seen a great amount of buzz and interest in the industry from building owners, managers, and workers requesting information, presentations, and fee proposals to perform studies on their facilities in the past year. This new interest of providing gear labeling for boundaries and level of personal protective equipment (PPE) clothing for aiding workers’ safety planning when maintaining and servicing energized equipment has increased our level of studies performed. We have also had many clients who were unaware of the costs for the services and implementation place our fee proposals into their capital budgets for the upcoming cycle. We foresee further increase in arc-flash study activity when these funds become available.
Weigel: Electrical Safety Works is neither licensed nor qualified to offer engineering services such as arc-flash hazard analysis, short-circuit analysis, and time-current coordination studies. However, my previous employer does offer such services. Based on my knowledge of its past efforts and the growth of its business over the past eight years, I can reliably state that the demand for arc-flash hazard analysis and the associated studies has increased exponentially since 2003. In the past 18 months, the growth in that engineering offering has been approximately 20%. There are literally tens of millions of facilities in the commercial/industrial market that have requirements for this work, and relatively few vendors that offer an adequate level of competency and quality to provide this service. I expect this growth to continue for many years.
Q: To your knowledge, how many clients have accurate single-line diagrams/electrical documentation?
Chandler: Very few commercial, institutional, or healthcare owners have accurate or up-to-date documentation of their systems.
Martin: Many have single lines that are accurate, but it is very rare that they are sufficiently complete for the purposes of an arc-flash study. It is uncommon that you will find an up-to-date single line and coordination study that includes line lengths and updates that include changes to protective devices, and indicates the type of construction (panelboard, switchboard, switchgear). However, if the arc-flash study is scoped at the beginning of a design project, it is pretty straightforward to make sure that all of these data are modeled for the coordination study.
Rea: In my experience most of the existing older facilities have very little when it comes to one-line diagrams, short-circuit analysis, coordination studies, and documentation of their electrical systems. We typically find partial and incomplete documentation from the additions and modifications that have occurred over many years since the inception of the building or campus. Many facilities rely on in-house electricians who have worked at the facility most of their lives and have all the information in their heads. I have seen this become a detriment to a facility when these key people retire, pass away, or leave the company.
Weigel: I have personally surveyed thousands of people who have attended my arc-flash information seminars since June of 2003. Based on their responses, I can state that fewer than 5% of employees in existing customer facilities consider their single-line drawings and other electrical distribution system documentation to be accurate and up-to-date. The lack of accurate documentation presents an elevated safety risk to electrical system workers. This lack of accurate system documentation is not generally the case if the facility is very new (less than two or three years old).
Q: Do you see a trend in the industry where manufacturers are starting to “get it”?
Chandler: We’ve seen only the earliest movements by manufacturers. They have a huge opportunity for improvement, starting with updating the more than 50-year-old design of molded case circuit breakers. There have been some improvements, such as a more extensive use of barriers, arc-flash reduction modules, and optical arc detection.
Martin: Absolutely. Major equipment manufacturers have really stepped up and offered more intelligent trip units that include maintenance settings, more barrier options in equipment, and better remote racking options. Some manufacturers have started to isolate the line side of main circuit breakers within panelboards based on our recommendations and recommendations from our clients.
Rea: Yes, a few manufacturers pioneered introductory features to help prevent injuries from electric shock, arc-flash burns, and arc blasts as long ago as four years. Today, most gear manufacturers provide equipment with safety features. OSHA’s enforcement tends to punish employers for unsafe working conditions and unsafe working environments by imposing staggering fines for violations. Word of these fines and today’s need to attract and keep experienced employees by providing safe working environments have prompted building owners’ requests/queries in providing equipment containing these safety features in our new electrical distribution designs.
Weigel: Yes, there is a lot of evidence that manufacturers of electrical distribution and control equipment are now considering arc-flash and shock hazards when designing their products. Arc fault propagation is a well-established phenomenon, and worker access into equipment that has hazardous voltage levels should also be an equipment design consideration. So consequently, I have seen newer equipment designs that incorporate barriers and other design choices to prevent upstream fault propagation. Even machine control panel builders are beginning to isolate and barrier voltage levels inside the control cabinets so that one could access, for example, a PLC inside the cabinet to reset it without being exposed to the higher voltage levels that operate the machinery. Door-mounted reset devices for interior devices like PLCs are also now becoming more common on control panels. Often, the workers who open these cabinets to reset a device are machine operators, not qualified persons, and these design improvements will help to reduce the hazard to these workers.
Q: For new building/facility construction, who is responsible (financially or physically) for ensuring an arc-flash analysis is done?
Chandler: Ultimately, it is the owner. We would love to see arc-flash analysis done on all projects, but we find that facility owners are often not willing to make a study a priority. We try to educate owners and encourage them to fund an analysis, but often we do not get an audience with the appropriate people.
Martin: The consultant should discuss arc-flash mitigation with the client at the beginning of the project, including determining if the arc-flash study is included in the scope of the design, as well as educating the client why this is an important safety precaution. There are many ways to reduce arc-flash energies before an arc-flash study is performed. When this discussion takes place early in the design phase, many of the solutions are affordable and allow for significantly reduced arc-flash energies. That being said, the responsibility of meeting the OSHA general-duty clause lies with the owner. Owners can choose to hire the firm that designs the facility, hire another firm, or perform the study internally.
Rea: I believe the facility owner is financially responsible, and the facility director should be encouraging and ask the facility owner to ensure that the analysis occurs.
Weigel: Generally, the owner of the facility and the equipment is responsible for making sure that the arc-flash analysis is contracted and completed, and the equipment is labeled for the hazards.
Q: For new building/facility construction, when should an arc-flash hazard analysis be done?
Chandler: Although there may be some benefit to performing an analysis during design, the best time is after the overcurrent protective devices (OCPDs) have been submitted and approved, so either late in construction or during commissioning.
Martin: An initial study can be performed during the design phase as a sanity check, but the reality is that the model will be incomplete. On most projects we’re involved with, the electrical distribution equipment is bid, so it is unlikely that we know the manufacturer and won’t have submittals with complete breaker information. Also, the conductor lengths may not be determined, and in some cases, we may not have been able to speak to the utility yet. On our projects, the sweet spot for doing the complete arc-flash study is usually during construction but before commissioning. This gives the contractor time to incorporate the settings before any start-up is performed. During the commissioning phase there are a lot of people working fast to get the job complete. They need to wear the appropriate PPE and apply as many of the recommendations of the arc-flash study as possible.
Rea: The initial arc-flash analysis should occur during design with the short-circuit analysis and protective-device coordination study. Due to the typical changes of gear locations and sizes during the construction process, the study can be updated and finalized after the majority of construction is completed and the final gear locations and conductor lengths are determined.
Weigel: For new construction, the ideal time to conduct the arc-flash analysis is before the electrical equipment is actually built and delivered. However, equipment manufacturers will generally not include the cost of the arc-flash analysis into a new construction equipment bid unless the consulting engineer/designer has incorporated this requirement into the new construction specifications. The cost to provide the arc-flash analysis after the equipment is in place is substantially higher than it would be if the preconstruction analysis was performed (usually more than double). Additionally, after the equipment is built and shipped, the opportunity to make minor changes in the design to reduce arc-flash hazard levels is lost. It is not uncommon to see new equipment installed in new construction that is found in a subsequent analysis to have a very high arc-flash hazard potential simply because of design choices that were made, and it could have been changed to make the equipment less hazardous.
Q: Who is responsible for ensuring NFPA 70E compliance when a building/facility is leased?
Chandler: The party responsible for the maintenance and operation of the facility.
Martin: Interesting question. I’m not qualified to answer that from a legal standpoint. However, it’s pretty unlikely that the owner of a leased facility would be able to provide the lessee with an arc-flash study that keeps up-to-date with utility changes and potential power-system changes internal to the building. In addition, I can’t make a reasonable argument that leasing a building absolves an employer from providing a safe workplace.
Rea: OSHA will regulate and the owner may want to require compliance by the lessee by adding it as part of the leasing contract.
Weigel: The owner of the facility (lessor) would normally be responsible for the cost of compliance.
Q: How can engineers design and specify electrical equipment to improve safety for maintenance workers?
Chandler: We can strive to design the system to minimize arc flash, but that oftentimes comes at the expense of selective coordination. With selective coordination being required for emergency and legally required standby systems by NFPA 70-2008 and 2011, we may have higher incident energy levels at some points in the system. We can specify breaker-maintenance overrides, vented-gear enclosures, dedicated compartments for main breakers, arc-flash reduction modules, current-limiting breakers, and limiting the maximum size of transformers.
Martin: There are almost too many options to list. They range from the less common (arc-resistant switchgear, zone-selective interlocking, remote racking, high-resistance grounding) to the more typical (specifying equipment with maintenance settings, remote operators, electronic trip units, allowing for greater working distance), and finally to the basics (providing a coordination study/protection scheme with reduced clearing times, educating the client about arc-flash and shock hazards). Additional options include reducing the equipment-rated ampacities and increasing the working clearances beyond the minimums of the National Electrical Code (NEC).
Rea: In equipment selection, the engineer can suggest to the building owner his options to use gear with arc-flash safety features, remote racking devices, and maintenance switches that adjust protective devices to a faster trip setting, and to lower incident energy and PPE requirements during maintenance and troubleshooting activities. It is typically an economic decision at the time of design whether the enhanced safety items are chosen to be incorporated into the design or as an add-on alternative. Within the coordination study, engineers, when appropriate, can tighten the instantaneous region while still maintaining coordination, thus aiding to limit the buildup of energy before an upstream breaker can clear the fault, which also lowers the PPE level requirement at that location.
Weigel: There are many design choices for electrical equipment that were once considered adequate—and even best practice—that should no longer be used because of arc-flash hazard potential. An example of this is called the “six main rule” or “six disconnect rule” (see NEC 230.71(A)). Whenever this is used in a design on the service entrance equipment, the arc-flash hazard levels in that service equipment are almost always very high—commonly more than 40 cal/cm2—for a 480-V service. The reason for this is that the upstream OCPD is now on the electric utility system. Those utility devices are never designed for fast interruption under arcing conditions. Simply adding a single main OCPD into the service entrance equipment will significantly reduce the arc-flash hazard potential on the service entrance equipment bus. There are many other examples of incorporating “safety by design” into a new construction project. Awareness of arc-flash hazards is beginning to be recognized by electrical system designers.
Q: Should unqualified personnel be trained in electrical safety? Are consulting engineers or electrical engineers considered unqualified personnel?
Chandler: Some consulting firms send their employees to safety classes and then deem them qualified, but we have reservations with that approach. Our firm has made the decision that we are not qualified personnel when it comes to entering potentially dangerous situations. There still is merit to being trained in safety, but not with the goal of declaring ourselves qualified.
Martin: I would always recommend that workers be trained to recognize the electrical hazards in the workplace, but that does not mean that they could be considered qualified. Engineers can be either qualified or unqualified workers, depending upon their training, and their familiarity with the equipment and facility.
Rea: I believe all workers involved with maintaining and servicing electrical equipment should be trained in electrical safety. Engineers and electrical engineers with no physical safety training and only theory knowledge may be considered unqualified to service and maintain electrical equipment.
Weigel: Unqualified personnel should at least be given a short basic training about electrical hazards and safety. Unqualified personnel such as office workers might encounter a situation in the facility where electrical work is being done, or a panel cover has been left off, and, in that case, it is worthwhile for them to be educated on how to avoid the potentially hazardous areas. Consulting and other engineers would not be considered as “qualified persons” under the definition unless they have had the specific required training. Even a noncontact inspection of electrical equipment can be potentially hazardous, so any time electrical equipment is energized and has energized conductors or circuit parts exposed, the hazard is present even if no intentional physical contact is being made.
Q: Are dc systems such as UPS batteries and switchgear station batteries covered by NFPA 70E?
Chandler: Absolutely. Not only does Article 90 of NFPA 70E not exclude these systems, but we know that dc installations can be very dangerous as well as ac, and a high level of care should be exercised when working on or around dc equipment.
Martin: Yes, the sections exist in NFPA 70E. NFPA 70E has been evolving to give better guidance for dc systems, and both the changes in the body of the standard and in Appendix D.8 in NFPA 70E-2012 are a good start. Several of the major software manufacturers have released, or are working on, software releases that include dc arc-flash calculations based on the 2012 version of NFPA 70E. A corollary question would be, “Is there anything that says the general-duty clause does not apply to dc systems?”
Weigel: Yes. DC voltage potentials can be very hazardous, depending on the configuration of the batteries or dc sources. Other dc sources such as solar arrays, crane controls, and other equipment that operates on or produces direct current can also be hazardous and are covered in NFPA 70E. At this time, not very much is known about how to calculate arc-flash hazards in these dc systems. Work is currently underway to develop a wider understanding of dc hazard potentials. The current NFPA 70E-2012 also has more information on dc hazard potentials in Article 130.7(C)(15)(b).
Q: What can be done to reduce the arc-flash hazard potential at a substation transformer secondary, upstream of the main OCPD?
Chandler: The transformer primary protection can be selected to minimize incident energy, but the main protection involves the construction of the switchgear on the secondary. Switchgear construction obviously doesn’t help you if there is a flash in the transformer compartment, but most faults occur within the switchgear. Most manufacturers seem to be paying more attention to arc flash in the design of their gear, and incorporating arc-resistant design features.
Martin: The first solution should always be to perform the work de-energized. When that can’t be done, the answer depends mainly on the results of the arc-flash study. Reduction of the incident energy may be possible by opening upstream or downstream tie breakers, differential protection, lowering or applying the instantaneous-settings group on the upstream breaker, or installing current transformers (CTs) at the transformer secondary that trip the OCPD at the transformer primary.
Weigel: Optical arc detection could be used in the transformer secondary compartment in combination with CTs to detect a forming arc and then signal the OCPD on the medium-voltage (MV) side to interrupt (if the MV OCPD is a fault-interrupting device such as a vacuum circuit breaker). If the MV primary device is a fused load-break switch, not much can be done. Relaying in the transformer secondary compartment can also be used to interrupt the primary OCPD. But large vacuum circuit breakers have a fairly long opening time, so significantly restricting the arc-flash hazard is often not feasible.
Q: Does the flash hazard at a substation transformer secondary apply to all substation distribution sections? Does the answer to this question depend on whether the low-voltage (LV) distribution sections are switchboard vs. switchgear construction?
Chandler: Yes, but to a different extent. As soon as you are within the distribution sections, you are on the load side of the main circuit breaker, which can be selected and set to minimize arc flash. Obviously, there is still a great deal of danger of arc flash, but to the extent that it can be minimized by proper device selection and gear design, it should be. The answer does depend on whether you have switchgear or switchboard construction. Typically, switchgear construction will have barriers separating all breakers. Switchboards may or may not have these barriers.
Martin: I default to including line-side arc-flash energy at the beginning. If it is switchgear, or other methods have been used to segregate the main, then I will allow the main to be the upstream (interrupting) device. Including the line-side arc flash does result in higher levels of PPE, which also is problematic and has a clear downside. This topic is pretty widely debated; I’m not convinced that there is a one-size-fits-all answer.
Rea: You could have different PPE labeling requirements on a unit substation switchgear lineup—especially if you have an isolated and barrier-protected main breaker. The high-voltage switch, LV section main and transformer, and the LV bus and feeder distribution sections can have different levels of arc energy/PPE. A word of caution is multiple labels on one lineup will give workers multiple options. They could elect to select the lower PPE/labeling of their choice, which could quite be a recipe for disaster when working on multiple sections of the lineup with differing PPE requirements. A method to avoid this, if the facility owner agrees, would be to provide the worst-case scenario of PPE for the lineup. This worst-case scenario procedure on a lineup can reduce training requirements, confusion, and liability.
Weigel: Consideration should be given to the likelihood of arc fault propagation when performing arc-flash hazard analysis. Most (more than 90%) arcing faults originate as a single-phase to ground fault, and immediately escalate to all three phases and ground if they are not interrupted very quickly. Once the 3-phase arc is established, it tends to propagate upstream if the construction of the equipment does not hinder that propagation. If the fault originates in a switchboard, panelboard, or motor control center, it is very likely to propagate upstream and even into the main section, thus disabling the main OCPD. In that condition, the next upstream device has to clear and those often have longer fault-clearing characteristics. In substation construction, the next upstream device is typically at the MV level and, in many cases, is a fuse in a metal-enclosed load-interrupter switch. These fuses are not effective at interrupting an arcing fault in the sub-cycle range, and that results in some very high incident energy levels on the LV bus. Generally, if the MV primary OCPD is a vacuum circuit breaker, there are more effective ways to control the incident energy on the LV bus by using relaying to interrupt the MV breaker.