COVID, employee well-being and indoor air quality issues have all changed the way office building controls and automation are designed
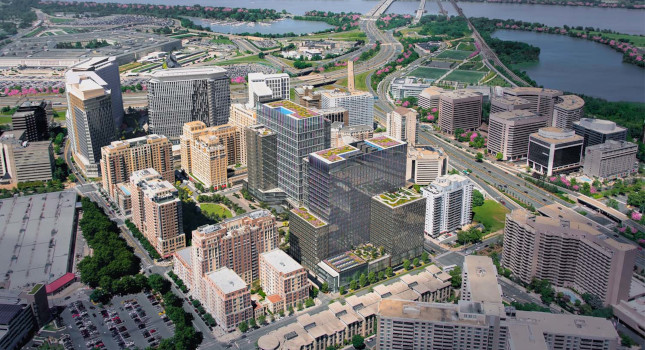
Respondents:
- Daniel Donahoe, PE, Senior Mechanical Engineer, LEO A DALY, Omaha, NE
- Tyler Jensen, PE, LEED AP, Studio Leader, ESD, Chicago, IL
- Brad McNiff, PE, LEED AP, WELL AP, Principal, GHT Limited, Arlington, VA
- Gerald Williams, PE, LEED AP, Senior Mechanical Engineer, CRB, St. Louis, MO

What mechanical, electrical, plumbing or fire protection systems within office buildings require specialized automation or controls that previously might not have?
Daniel Donahoe: The complexity of controls has certainly increased over the last decade due to updates and revisions to energy codes and standards regarding heat recovery, partial-load control and ventilation controls. In Nebraska particularly, the state just jumped from IECC 2018 to 2009 overnight. There are a variety of unique design considerations related to these codes, such as addressable lighting control systems. Nonnetworked systems were previously preferred by some clients due to cost. Almost every office building will now need an addressable lighting system to meet code requirements.
Tyler Jensen: As noted earlier, we’ve worked with a client to deploy air quality and pollutant measurement and verification system. The sensors tie into the building automation system through a bespoke intelligent building platform developed by cohesion. HVAC systems that were previously only controlling to maintain space temperature are now also optimizing and increasing ventilation rates to spaces based on air quality monitoring data.

Considering COVID-19 issues, what smart technologies are you being asked to specify to improve working conditions?
Gerald Williams: Matterport is a new technology that uses a 360-degree camera to quickly create a virtual 3-D model of rooms or entire buildings that our designers are using to verify existing conditions without the need for costly or potentially unsafe site trips. HoloLens is another smart technology we have adopted to provide remote site visits. This technology overlays Autodesk Revit models on top of a live feed, so users can see the new construction design within the existing facility. The tool uses special goggles while a local operator walks around looking at features and operating equipment at the real-time direction of remote engineers.
Many companies now require all contractors visiting their sites to have proof of vaccination, sometimes even proof of a booster shot, to be allowed on-site to observe existing conditions and attend meetings. Individuals who do not yet have those vaccination credentials can still actively participate in the design process using virtual meetings and smart technologies like Matterport, drones and 360-degree cameras. We have directly applied these technologies to our COVID response as it minimizes the number of people on-site, reducing travel and exposure.
How are cybersecurity concerns being addressed with building automation systems? What steps are you following with the building owner and operations team?
Tyler Jensen: Operational technologies like BAS create cybersecurity risks beyond traditional information technology and cloud systems that are typically thought of as the prime cybersecurity concern. Recent high-profile breaches have highlighted the potential risk as many OT systems are embedded within office buildings and are a potential vulnerability. We recently developed a cybersecurity team to consult with building owners and operators to help raise awareness and develop protocols related to both IT and OT cybersecurity.