TOR1 Wholesale Data Center Conversion, Vaughan, ON, Canada
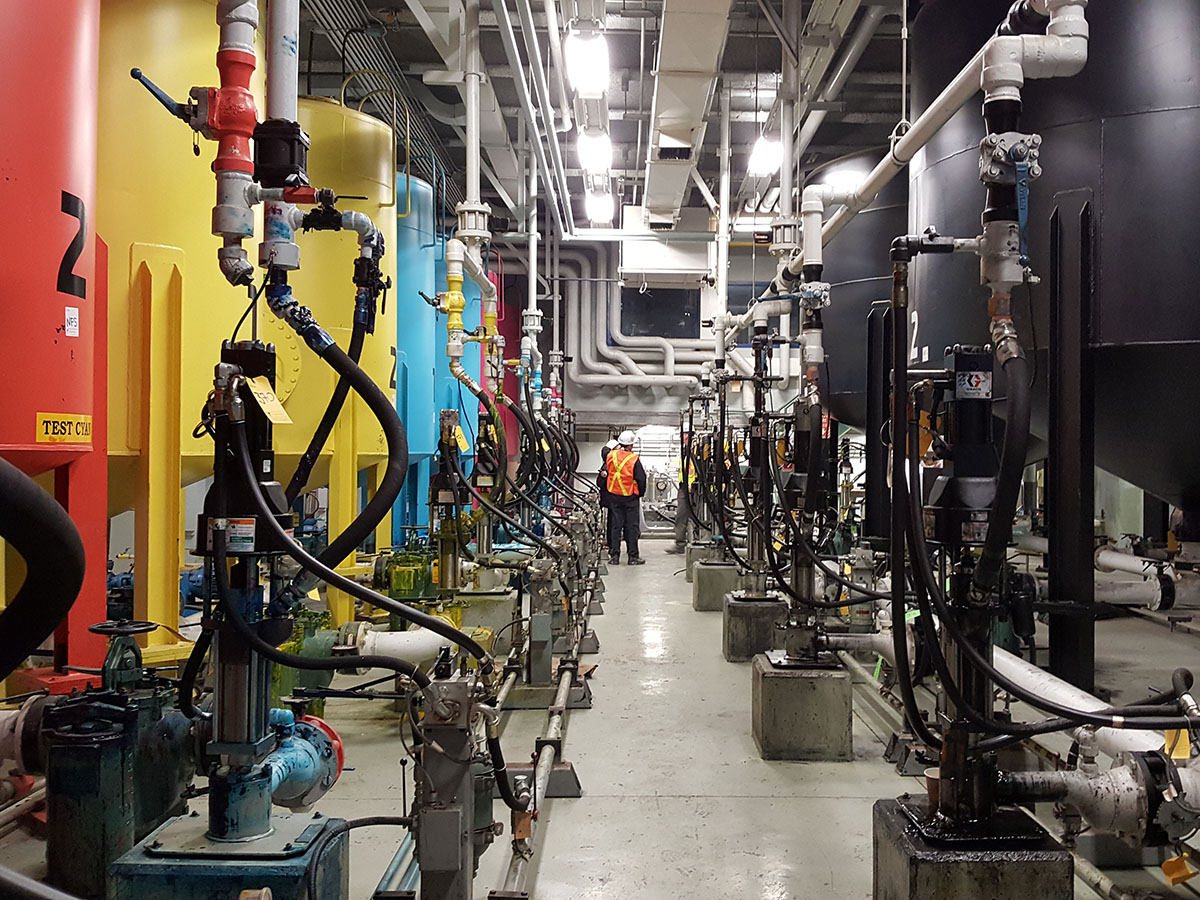
Engineering firm: Morrison Hershfield
2019 MEP Giants rank: 65
Project: TOR1 Wholesale Data Center Conversion
Location: Vaughan, ON, Canada
Building type: Data center
Project type: Existing building retrofit
Engineering services: Automation, controls; electrical, power; energy, sustainability; fire, life safety; HVAC, mechanical; lighting; plumbing, piping
Project timeline: September 2016 to July 2018
MEP/FP budget: $2,800,000
Commissioning budget: $1,000,000
Challenges
Morrison Hershfield assisted Digital Realty with repurposing the iconic Toronto Star newspaper printing facility into “TOR1,” the first mega-scale wholesale data center in Canada. The facility delivers top efficiency and reliability to the globe’s largest companies, essential for meeting the increasing demand for wholesale data center capacity in Toronto,. TOR1 includes 23 computer rooms spread across 21,000 m2 (226,000 SF) with a critical power capacity of up to 46 MW and is engineered to achieve an annualized Power Usage Effectiveness of 1.25. Phase 1, completed in May 2018, consists of 12 computer rooms and provides for 24 MW of critical load capacity, expandable to 60MW.
The TOR1 conversion project involved aggressive efficiency, flexibility and schedule targets. The inherent challenge was to design and construct a data center with an aggressive PUE target, without sacrificing flexibility or reliability, in an existing building that was originally constructed for a much different operating purpose — all in 24 months with a $200 million budget.
Efficient processes and superior technical solutions were designed and implemented to meet the expedited schedule and repurpose the existing facility without compromising any aspects of design or function.
Load bank and transformers at southwest corner of TOR1.[/caption]
Solutions
To maximize speed to market, the team designed based on critical path (for material and equipment). The project plan divided work into logical segments to facilitate parallel design and delivery efforts, enabling the team to work around
delays caused by a more lengthy approvals process for “outside” equipment by moving ahead with the “inside” work, like demolition, cleaning and reinforcing steel. The design team worked closely with the constructor and produced drawings to be sequentially tendered for work that was permitted, in an order that allowed base building long lead items to be released, e.g., base building structural re-enforcement drawings were advanced in the critical path to allow for early shop drawing review, constructor coordination and field install.
Corridor with overhead services, servicing multiple computer rooms.[/caption]