Clients are asking lighting designers to help them save on energy costs. Replacing fluorescent, HID, or other lights with LEDs is in high demand.
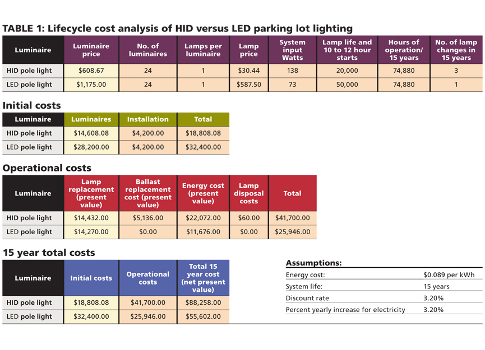
LED lighting retrofits are becoming popular due to their energy and operational savings. LED retrofits can save 40% or more energy when compared with traditional light sources such as incandescent, halogen, and high intensity discharge (HID).
Resources such as the U.S. Energy Information Administration indicate that lighting accounts for approximately 26% of the energy use in commercial buildings. It is also widely known that buildings consume more than 40% of the energy in the United States, according to the U.S. Dept. of Energy.
The U.S. Energy Independence and Security Act of 2007 marked Jan. 1, 2014, as the date when 100-, 75-, 60-, and 40-W incandescent lamps can no longer be manufactured by U.S. companies. As a result, LED light sources are an attractive alternative to the lamps that have traditionally been used to replace incandescent lamps such as halogen and fluorescent lamps.
Why use LEDs?
Why are LED retrofits popular with clients? LEDs have a reduced environmental impact compared to other light sources. This is attributable to the energy savings from using LEDs as well as the longevity of LED light sources, resulting in many fewer lamp replacements over time. LEDs also do not contain hazardous materials such as mercury, which is used in fluorescent lamps.
LEDs emit virtually no ultraviolet (UV) rays or infrared (IR) heat radiation. This makes LED light sources ideal for venues where UV and IR are undesirable, such as in museums and art galleries. UV and IR can degrade sensitive materials found in these facilities.
LED light sources work well in applications where there is frequent on-off switch cycling. The life of fluorescent lamps is decreased when used with instant start ballasts and there is frequent switching. HID lamps have a restrike time delay (usually 2 to 20 min) when they are turned off so they can cool down before turning on again. This makes HID lamps ineffective for switch cycling applications. Conversely, there are no detrimental effects with frequent on-off cycling of LEDs, making them popular in spaces that use occupancy sensors for energy savings.
When turned on, LEDs are instant-on with full light output and do not require a warm-up period to reach full light output as many compact fluorescent lamps (CFLs) and HID lamps do. LEDs also perform well in cold temperatures whereas other light sources like fluorescent lamps have lumen degradation at lower temperatures.
The rated life of most LED light sources is higher than comparable light sources including halogen, HID, and most fluorescent lamps. Also, the lifecycle cost of LEDs is favorable compared with other light sources due to their long life and their energy efficiency.
LED retrofit options
There are several retrofit options with LED light sources. Popular retrofits include a self-ballasted LED screw-in A19 lamp or a LED PAR screw-in lamp. A typical LED A19 light source uses 13 W compared to a 60 W A19 incandescent lamp with similar lumen output. This comes out to a 78% reduction in energy usage.
The A19 LED light source in the above example has a typical life of 25,000 h compared to 1,000 h for a standard A19 incandescent lamp.
When comparing lifecycle costs, the low operational and maintenance costs of LED light sources make them very attractive compared to the A19 incandescent lamp. In our example, an incandescent lamp would have to be changed out 25 times before the LED lamp would need to be changed.
Another LED retrofit option is to replace T8 and T12 tubular (typically 4-ft linear) fluorescent lamps with tubular LED lamps. T8 and T12 lamps are omnidirectional, meaning that light is emitted in all directions out of the lamp. Omnidirectional light may not be desirable; reflectors in lighting fixtures are used to help provide a more uniform distribution of light.
Many of the early linear tubular LED retrofits had narrow beam angles, which presented issues with good lighting distribution.
Several manufacturers provide an LED retrofit kit complete with the LED driver and the tubular LED lamps. The conversion would involve removing the existing magnetic ballast, the fluorescent lamps’ lamp holders, and the fluorescent lamps themselves. Another option is a retrofit kit that is complete with LEDs and driver that come as an assembly and mount directly into the existing luminaire housing. One advantage of this style of retrofit kit is photometry is available for analysis.
Tubular LEDs can reduce energy usage by about 40% compared with standard 32 W T8 lamps with a normal ballast factor (0.88) while producing similar light level at the target area. However, most new tubular LED lamps have a wide beam angle (such as 160 deg) that has rectified this problem.
Another popular LED retrofit application is with street lighting and parking lot lighting. Many existing lighting fixtures in these applications use HID lamps such as high pressure sodium (HPS) and metal halide (MH).
Using LED lighting for streets and parking lots over HID lighting has many significant benefits. These include reduced energy usage and longevity, resulting in fewer lamp change-outs (saving high maintenance costs with tall light poles). LEDs also reduce risk from inadequately lit spaces when HID lamps are burned out (due to their shorter rated life) and areas become unsafe. LEDs also are flexible when it comes to controllability such as dimming or occupancy sensing, saving energy and helping comply with energy codes.
Code considerations
What are some of the code related considerations when retrofitting existing lighting fixtures with LED light sources? In most cases an existing lighting fixture is UL listed based on a particular lamp type (such as T8s). Most likely, the fixture that is being retrofitted does not have a UL listing with a retrofit LED light source.
It is important to check with the authority having jurisdiction (AHJ) to determine if luminaire retrofit kits require inspection and how compliance is established. In an online document, UL implies that modifying a fixture by replacing the existing lamps and ballasts in the field might negate the UL listing. AHJs may require that a LED retrofit kit be UL classified under the product category “Luminaire Conversions, Retrofit (IEUQ).” According to UL, “these products have been investigated to determine that, when used in accordance with the manufacturer’s instructions, they do not adversely affect the operation of the complete unit.”
A luminaire that is modified so it can no longer accept the original lamp should have a label affixed (provided by the retrofit kit manufacturer) indicating the luminaire has been modified and can no longer operate the originally intended lamp(s). The label is an easy way for the AHJ to identify whether a conversion retrofit kit meets the UL Classified Mark.
Some of these tubular LED linear light sources are able to use the existing T8 lamps’ electronic ballasts. This makes it easy to change out the linear T8 lamps without having to remove the existing ballast and installing a new LED driver.
Design considerations
There are other items lighting designers should consider when evaluating LED retrofits. The designer should study the LED’s specifications to verify if the lamp will work in a specific application. If lighting photometry analysis is to be performed, it is important to remember that the luminaire photometry information was originally developed using omnidirectional lamps. If the retrofit is a lamp replacement, the luminaire photometry cannot be used if the new LED lamp is not omnidirectional such as the tubular T8 replacements. Some retrofit kits that come as an assembly that inserts into the existing house do have photometric information available.
Self-ballasted LED lamps may not be suitable for totally enclosed lighting fixtures due to heat dissipation.
LED light sources that are marked “suitable for use in open luminaires” can be used to replace lamps in applications where the luminaire is open and does not require an additional lamp containment barrier.
Another consideration is the luminaire system efficacy. An LED light source does not necessarily need to have the same lumens as the lamp it is replacing. This may be acceptable in some instances such as an LED retrofit of an outdoor lighting pole-mounted fixture used for street lighting and/or parking lot lighting. Most LED retrofits involve replacing the entire luminaire while reusing the existing pole.
For outdoor lighting, one reason that lower LED lumens is acceptable is that the uniformity of the light delivered by LED sources is often drastically improved. Energy is not spent creating hot spots on the ground. Outdoor lighting design requires that lighting provide the minimum allowable light level in the illuminated area and not the average. Thus, with improved lighting uniformity, the LED fixture can operate with lower overall lumen levels.
HID lamps such as HPS and MH appear to be very efficient (100 lumens/W or higher) when one focuses solely on source efficacy. However, source efficacy does not accurately reflect how much light is actually delivered from the light source to the target area, such as onto a street or a parking lot.
Luminaires with LED light sources typically have a higher system efficacy compared to other light sources. System efficiency is based on how many lumens actually reach the target area. It is not the same as the number of lumens emitted from the lamp (source efficacy).
HID lamps are omnidirectional and require reflectors inside a luminaire to reflect light to the target area. However, not all light can be effectively redirected. Typically 40% of more of the light from HID lamps does not reach the target area.
LED light sources are typically directional, meaning the lumens reach the target area without needing to be reflected or redirected.
A typical luminaire with an LED light source (with a source efficacy around 100 lumens/W) has a system efficacy of 50 to 75 lumens/W. A typical luminaire with an HID lamp has a system efficacy of 30 to 35 lumens/W. LED drivers are generally more energy efficient than HID ballasts.
Color temperature and color rendering index (CRI) are also important factors to consider when selecting LED light sources. Most LEDs have increased efficacy as the color temperature increases with a cooler light output.
LEDs are available with CRIs in the 80s and 90s. The current CRI is a measure of the first eight (R1 to R8) color reference samples, which are pastel colored. However, the current CRI metric does not include saturated colors such as strong reds (R9). Other than halogen, most typical light sources do not render the R9 metric very well. Many LED manufacturers are now offering products with enhanced saturated color rendering and specifying R9 CRI values.
Lighting designers should also verify that specified LEDs have their IES LM-79, LM-80, and TM-21 documentation readily available. See the “Use the right resources to specify LEDs” article in the August 2012 issue of Consulting-Specifying Engineer.
Additional excellent resources include the Design Lights Consortium and Energy Star Qualified LED Lighting. These resources ensure products meet high quality and performance standards. The U.S. Dept. of Energy’s CALiPER (Commercially Available LED Product Evaluation and Reporting) program tests and evaluates off-the-shelf LED products to see if they actually perform as rated.
O&M savings
Lumen depreciation is important when evaluating lifecycle costs. Metal halide lamps in particular suffer from substantial lumen depreciation over relatively short time periods.
LEDs’ useful life is usually defined as the operating time prior to 30% lumen depreciation, or 70% lumen maintenance (L70). This level of lumen depreciation has been widely adopted as the standard for useful life. A 30% decline in lumen levels is usually not detectable by most people.
Many LEDs have an L70 life of 50,000 to 100,000 h, making them attractive compared to most other light sources.
Lifecycle cost analyses for LEDs typically show that the 15-year total costs make them attractive in most scenarios. Lifecycle cost comparisons should include the number of years for the analysis; the number of luminaires; the initial cost of the luminaire (including the lamp type); the initial installation costs; the yearly hours of operation; the cost of electricity per kWh; the lamp replacement costs during the time of comparison (e.g., 15 years); the ballast/driver replacement costs during the time of comparison; the cost to change out the lamp/ballast during the time of comparison; and the lamp disposal costs.
Table 1 lists a lifecycle cost analysis of a study performed by the Dept. of Veterans Affairs’ Office of Construction and Facilities Management in October 2011. The analysis compares HID against LED in a parking lot application.
Additional considerations include the controllability of LED light sources compared to sources such as HID that have limited control due to the warm-up time of the HID lamps. This is especially important with increased lighting control requirements in ASHRAE Standard 90.1-2010 for exterior lighting and parking garages. LED light sources do not have a warm-up time and their life is not shortened by frequent cycling, making them ideal for effective schedule and occupancy control compared to several other light sources (e.g., HID).
LED retrofits provide energy as well as operational and maintenance cost savings over traditional light sources. LEDs provide lighting designers and clients with benefits and options that were not possible in the past.
Michael Chow is the founder and owner of Metro CD Engineering. He holds a BSEE from Ohio Northern University and is a member of the Consulting-Specifying Engineer editorial advisory board and a 2009 40 Under 40 winner.