Designing a resilient building requires understanding of both the built environment and operations for critical facilities
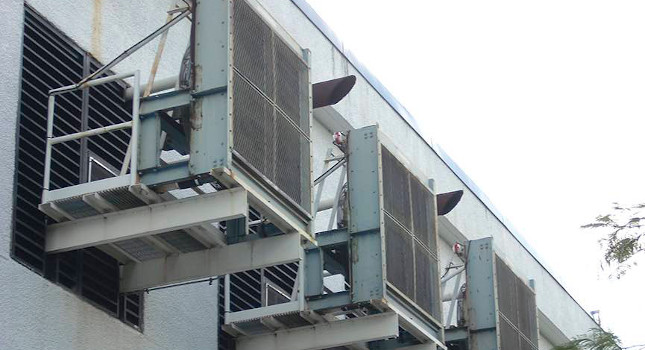
Learning Objectives
- Evaluate and understand design parameters for facilities.
- Learn about risk analysis and why it is important in designing for resilience.
- Know the considerations for design for envelope, structure, fuel and emergency power.
Resiliency is defined as “the capacity to recover quickly from difficulties; toughness,” or “an ability to recover from or adjust easily to adversity or change.” Resiliency in design and the built environment can be taken to mean many different topics, but, in general, it’s that the building continues to function as it was planned and intended. This requires operational understanding, proper risk analysis and finally design execution.
Unfortunately, risks are everywhere and engineers and building owners can’t truly prepare for every contingency. For each risk, the designer should consider how likely it is to occur, what the impact occupant safety and security and what the potential solution is to mitigate the risk. What is a built environment risk and what is something that can be accomplished via an operational plan in the event that risk does come to pass?
It seems silly at this point to write about why resiliency is important with COVID-19 challenging our lives and our buildings. Unfortunately, COVID-19 is only the latest and most devastating of events that have occurred over the past decade around the world and the United States, both from the aspect lives lost and the cost.
When evaluating each facility, approach it with the following three questions:
- How would the owner want to operate during and/or after an event?
- What are the possible failure points and the risk?
- What can be done about it?
Operational considerations
How a facility operates becomes an answer that informs the rest of the analysis. Engineers need to have this basic understanding even before doing a risk analysis. Some risks can also be mitigated by the operational plan for any facility. If the goal is for a building to operate as intended, then this step comes before risks are identified that will cause a deviation from that operation. Commercial buildings, theaters or restaurants, for example, most likely shut down during an event, but want to start up afterward.
To demonstrate the importance of operational awareness consider this cause and effect analysis for a commercial restaurant:
- Does the owner plan to be present at this facility for an outage? If no, the facility will need to operate without human intervention. The owner may also want to know status of the building from afar — this means alarm points, monitoring and possibly remote controls. The internet connection is a critical service that needs to be protected.
- How soon after an event will the facility be open? If operations will begin immediately after an event, the owner needs to ensure that structural damage, debris or flooding would not affect the interior of the restaurant. This would impact what kind of glass is used or how the envelope of the facility is designed. It also would affect the locations of utilities and necessitate enhancement of protection of equipment.
- How will food storage be handled in a power outage? Different owners have different tolerances for risk. When power goes, food stored on-site starts to go bad. Does an owner have those refrigerators on emergency power, or do they accept the risk of that loss? If the owner accepts the risk of this loss or has an operational plan to use it up before an event, then power outages become a less critical failure point.
- What maintenance contracts does the owner have? Consider the generator above for food. Who is doing the testing for that equipment and making sure it will run when needed?
- What equipment is most critical to the function as a restaurant? Operational requirements such as a grill or a cash register would lead to design considerations for the exhaust over the grill, review of the gas service supply and knowing the power and internet connection for the cash register/card swipe is of elevated importance.
- How long of an event does the owner want the engineering team to consider? This is a big question, especially when it comes to fuel. If there was an outage, how long do the refrigerators have to run?
Mission critical facilities
Hospitals, fire stations, police stations, news facilities and data centers will all want to remain fully functional during any event, elevating the need for operational understanding. To demonstrate the impact of this understanding, let us consider it through the eyes of a hospital facility director.
During an event, which might last minutes or a day, a facility director will focus on the most important items at that time, items that can have an impact to safety of the occupants. Patient care is highest priority at all times, but during a storm or emergency event, elective surgeries and outpatient procedures may be stopped. This is the first operational question, and that answer will impact how much fuel electrical engineers plan for if there will be redundancy in the generators and equipment serving operating rooms.
Figure 2: It’s important to consider appropriate louvers and risks to building envelope when designing resilient buildings. This louver was designed structurally with an extra 10-inch cantilever to support new remote radiators for the same site. Courtesy: TLC Engineering Solutions[/caption]
Failure points and risk analysis
A review of the facility planning is the first item that should be on any risk analysis. A lack of documentation on how a facility would prepare for an event or function in an event is a major risk item. Many of the concerns outlined in the operational section are items that can be planned around, but not if they are a surprise during an event.
The engineering team should help clients plan for:
- Evacuation plan: Define the criteria for deciding that a facility should be closed.
- Proactive testing and maintenance: Determine whether preventive maintenance on the essential generators must be performed, among other tasks.
- Event simulations: Conducted before any event, a simulation would test how its occupants function in event and after of an event.
The next step would be to go through a facility and identify the possible failure points, how likely they are to fail and what the impact would be. Common failure points include:
- Many older cities have power lines overhead, creating risk in snow or storm events.
- Flooding is the most common source of damage. Roofs and the building envelope should be reviewed.
- Failure based upon age of equipment: Many facilities operate with equipment that was made more than 40 years ago, with no available replacement parts for that equipment. It creates a situation that is an elevated risk due the duration that they could be out while they find obsolete parts.
- Lack of proper maintenance on equipment.
- Limited awareness of how systems interconnect.
- No documentation for redundancies put in place or directions on how to implement.
The amount of emergency power is a big question for any facility, and what is connected to it is just as important. The biggest load in most facilities is the heating, ventilation and air conditioning system, in particular the cooling system. These are not code required to be on emergency power for many facilities, but lack of backup to these systems have caused deaths in several events. Nursing homes, for example, frequently have emergency-powered HVAC for all spaces or emergency-powered HVAC for common spaces and an operational plan to relocate residents in a power outage to that space.
COVID-19 has brought a new element to the risk analysis for all building types. One common element of resiliency is to continue to function while protecting the occupants. Every facility has some risk in the spread of the virus in how air is distributed, what is done to filter air and much fresh air is brought in. There is no question: COVID-19 and viral transmission within facilities will be an item of concern for owners everywhere.
Design considerations
The most important systems to get right the first time are the building envelope and structure. These are very costly to fix and upgrade to meet high levels of reliability and redundancy. It’s important to consider every opening within the building as potential failure point — the types of windows, doors and louvers should be reviewed.
There are many manufacturers that create louvers that are designed to withstand the impact of a 2×4 hitting it at hurricane speeds. All openings should be protected; how to maintain those openings to the desired level should be considered. An example of this would be a facility that has hurricane shutters, and needs to annually install and uninstall all shutters to ensure they fit and the right bolts and attachments are still functional. It can be a significant maintenance item to opt in to shutters over higher cost/higher quality windows.
Emergency system gets a lot of focus, but what really is on emergency power? Too many facilities are only backing up code-minimum elements. The simplest thing a facility can do is to have an electrician install meters on the facility. With metering on key loads, the owner will get a great understanding of how much capacity it would take to add that to the backup system. Generally, it’s recommended that all HVAC and critical functions be on emergency power if the owner intends to operate through an event.
Some things, such as kitchen equipment, need to coincide with food preparation plans to remain open. If the plan says to serve nothing but peanut butter and jelly sandwiches, storage is required for all of that, but not a lot of power. If the plan says the menu will remain the same, then the owner will have to provide emergency power for each type of cooking equipment at minimum.
Fuel systems often are an extreme source of stress. The proper calculation for available fuel in the tank is to consider the volume between the maximum fill level of the tank and the bottom of the usable fuel. Both items are available from the manufacturer and should be used in understanding how much fuel is truly available. For example, a 5,000-gallon tank might only have around 4,200 gallons of usable fuel. The size and shape of the tank matters as well. But once an owner has fuel, having some extra is good, but having too much can be just as much a problem as having bad fuel. Fuel quality is equally important; poor-quality fuel can cause an emergency system to fail. Many facilities either opt to have a standing fuel polishing program or install an automatic fuel polisher to maintain high-quality fuel.
A simple, but often overlooked element is landscaping and site grading. Location of cooling towers adjacent to trees that aesthetically block them becomes the reason they fail during a hurricane. The debris from the trees cause blockages within the cooling tower basins and also get5s into the pumps. In cases where generator louvers located where snow drifts will accumulate, the generator doesn’t get the air it needs, so it won’t work. Again, many of these become operational plans for trimming trees and clearing snow, but could they have been designed differently to not require those operational plans?
With the pace of events over the past decade and continuing into 2020, resilient design is going to become more important. Engineers need to design facilities that are functional, can survive weather events, consider health of its occupants and not need to be replaced over the next 20 or 30 years.