As technology advances in every field, the college and university students being prepped for future careers in those fields need the tech they’re learning with to keep up. That presents unique challenges for the engineers working on such structures—specifying advanced systems that satisfy the unique needs of each institution. Here, professionals with experience in the area offer advice on how to tackle such facilities and receive top marks in regard to automation, controls, and technology.
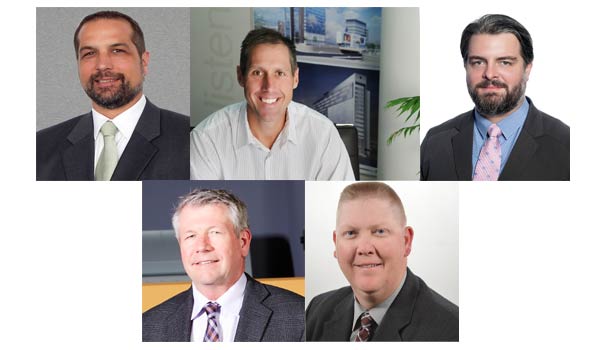
Respondents
John Holbert, PE, LEED AP Senior Principal/Client Executive, IMEG Corp., Rock Island, Ill.
Donald Horkey, PE, LEED AP Principal, DLR Group, Minneapolis
Kent Locke, PE, NCEES Associate Principal/Branch Manager, Bailey Edward, Fox River Grove, Ill.
Jason Sylvain, PE, Partner National Higher Education Practice Leader, AKF Group LLC, New York City
Matthew Wiechart, PE, CxA, LEED AP, CEM Principal/Senior Mechanical Engineer, TLC Engineering for Architecture Inc., Orlando, Fla.
CSE: From your experience, what MEP or fire protection systems within these structures require specialized automation or controls that previously might not have, or have there been specific requests for increased automation?
Wiechart: Higher ed owners are greatly concerned about the measurement and verification of energy. They want to know if their building is performing optimally, so energy meters for electrical and HVAC system are provided to properly ascertain and isolate energy issues. With those systems, robust controls and servers are required to gather and store the information.
Sylvain: We have noticed increased requests to monitor the energy-management system (EMS) for electrical equipment along with lighting controls, occupancy sensors, and vacancy sensors. By monitoring lighting control and associated devices (occupancy/vacancy sensors), we have been adding control and setpoint adjustment of the HVAC equipment serving the specific spaces. We also have noticed increased requests to provide complete automation abilities for existing chiller plants that were originally designed to be manual. The automation of these plants often requires the installation of new components, such as automatic valves and variable frequency drives (VFDs) for pumps. Additionally, we have worked on upgrading existing pneumatic controls to electronic direct digital controls (DDC) in many higher education facilities. Furthermore, our team also has designed retrofits for existing pneumatic VAV boxes where it’s not cost-effective to replace every single VAV box controller due to quantity and cost. By replacing the existing pneumatic thermostats with wireless pneumatic thermostats, which are battery-powered, setpoints for the VAV boxes can be adjusted at the BMS. Previously, setpoints had to be adjusted locally at each pneumatic thermostat.
Horkey: The integration of fault-detection and diagnostic (FDD) platforms with BAS is driven by both energy codes and sophistication of the operation and maintenance staff in higher education. We are incorporating FDD on multiple mechanical and electrical systems and subsystems to help the facilities staff maximize the performance of the building throughout the life of the systems.
CSE: What types of automation and control features are you seeing on these types of projects that you wouldn’t for other facilities?
Sylvain: In many higher education projects, we have received requests to add flexibility for teachers to adjust setpoints for the HVAC equipment serving their specific classrooms. The system is programmed such that the setpoint then returns to the default setpoint at the next occupied time. Additionally, there have been requests to add the ability to enable after-hours cooling for evening classes. These features allow teachers to customize the comfort cooling and heating of their classrooms to the needs of the students in the classroom. The controls team also has been involved with troubleshooting many different issues specific to higher education facilities. For example, we were asked to analyze the humidity issues in a university’s anatomy lab, which was causing the cadavers in the labs to grow mold. By evaluating the existing mechanical system and control strategies, our team developed a strategy to mitigate the issues while keeping the client’s budget restrictions in mind. The strategy resulted in adding spot dehumidifiers in the lab and also adjusting the controls of the existing HVAC in the facility to a customized controls sequence to maintain dewpoint temperature in the space.
Wiechart: The type of automation isn’t special. However, the devices to properly automate and alarm are more robust. An example of this would be to alarm filter loading. Typical projects would have differential sensors across both prefilters and final filters to alarm. University projects typically have differential sensors across the prefilter and final filter to alarm separately. Typically, university projects have 25% more control sensors and devices to control than other project types.
CSE: Are the internet of things (IoT) technologies and increased connectivity with these projects being talked about and implemented? If so, please give an example.
Holbert: IoT definitely is being talked about. There’s a general awareness of the phenomenon on many projects, but I wouldn’t say that it has fundamentally changed the technical solutions on projects yet. The most common thing it has done is shifted the responsibility for Ethernet cabling for devices that haven’t traditionally been IT systems to the IT scope of work.
Horkey: We are seeing an increase in interest from our clients on how to implement IoT technologies in their buildings. There is tremendous potential in transitioning from current technologies to a more connected IoT cloud-based connectivity. The ability to collect and analyze data to maximize performance in a true smart building will have a great impact on energy and comfort of facilities. We have started to specify control valves that have onboard control systems that are uploaded to the cloud for analytics. This technology allows the valve to be continuously optimized to eliminate waste energy, resulting in a significant reduction in energy and improved occupant comfort.
Sylvain: Many projects have discussed the use of converged networks as one way of implementing IoT. The converged networks allow for the facilities’ lighting control, BMS, security, IT/AV, elevator, EMS, and fire alarm systems to communicate using one network, which also provides potential savings for the client. Another benefit is that data can be shared more easily between systems. For example, as an employee uses a security badge to enter the office building, the lighting control system can be triggered to turn on the lights in his/her office and the BMS system can be signaled to enable the VAV box serving the office with the preferred setpoint.
CSE: For new and existing structures, have you experienced building owners requesting equipment and systems to be updated with asset management or automation tools?
Wiechart: These discussions are starting regarding the implementation of systems into a building management system to maintain and understand capital assets and improvement. I believe that universities are doing these tasks internally (if they are implementing) to keep internal costs down.
Sylvain: Owners in some facilities have requested that the BMS communicate directly with their asset management and automation, and AKF has specified this on many projects. Prescriptive Data is one such software package that can be integrated into many types of facilities and is used to collect data from various systems in a building (BMS, lighting control, elevator systems, supervisory control and data acquisition [SCADA], security, IoT sensors, etc.). The software is able to analyze the data inputs and provide feedback to improve the efficiency of systems in the facility. Feedback can range from recommending adjusting setpoints of supply-fan VFDs to reducing the number of operating elevator cars during nonpeak hours. There are many similar software packages on the market today.
CSE: How have your engineers worked with building owners and facility managers to implement integrated technology in these structures?
Locke: The universities have been proactive in upgrading their infrastructure to meet growing user needs. We have worked with their teams to understand where this infrastructure is and extend it per their campus standards and for systems used in these user spaces.
Holbert: We’ve developed a consulting approach that’s specific to integrated IoT systems. The architecture and engineering industry can’t deliver the same process that we’ve always delivered when the technology has converged the way it has in recent years. These converged technology systems require a paradigm shift in our consulting process so that clients can afford to implement these systems successfully.
Sylvain: At present, implementing IoT and integrated technology is a very new concept to our industry. It has been implemented in very few facilities and can be quite costly to implement due to the added coordination and programming required. However, we continue to discuss the possibility of using integrated networks with clients who are interested in pursuing this for upcoming facilities.
Wiechart: Working with the commissioning team and the university’s energy/building controls manager is a must. Clients want completed projects that work seamlessly. Verification that the system operates as designed and the manager can easily access the alarm and information gives the university the simplicity that they need to manage multiple buildings/assets on a daily basis. However, if systems are not set up to deliver the information from the onset of the project, issues go undetected for months, wasting money and potentially harming building equipment. Universities do not typically have the personnel to review buildings onsite routinely, so remote access and verification is extremely valuable.
CSE: When incorporating IoT, what are some of the most pressing challenges or concerns?
Horkey: Since IoT is still in its relative infancy, operation and maintenance staff are not completely up to speed or comfortable with the potential benefits. They are very comfortable with traditional building automation systems that are on an Ethernet network. It will take additional time and information for the facility decision-makers to understand the power that all the potential data mining, maintenance, analysis, and ultimately, building optimization will have on occupant comfort and building performance.
Sylvain: Security of the communication network is the most pressing concern. In recent years, the hacks on various high-profile companies, such as Experian and Target, have put a spotlight on network security options. Additionally, IoT can involve integrating the BMS network with other IT systems in the facility or using the facility’s existing IT network in lieu of the BMS network. This can create a challenging environment because the BMS vendors have to work within the constraints of the network requirements from other vendors, which may not conform with the requirements of the BMS software.
Wiechart: Hands down, network security.
Holbert: Despite these systems being converged from a technology architecture perspective, in many cases they’re still very separate in terms of how the clients support and manage them. So, the overriding concern is security-how you develop a single approach to system security.
CSE: What types of system integration and/or interoperability issues have you overcome in such specialty projects, and how did you do so?
Wiechart: The amount of information transmitted over a single network at any one time can bog down a network, so understanding how much information and when the information is transmitted is valuable. Also, if wireless devices are used, the building construction, wireless access points, and transmittance rates are crucial pieces of information. Integration of special systems in this day of digital controls can be difficult at times depending on the language of the systems being integrated.
Sylvain: The most common system-integration issues that our company has been involved with are due to the compatibility (or lack thereof) of dissimilar protocols of the different software packages. We have overcome that by working with the vendors to ensure that proper gateways are specified and sufficient scope is included in the project for programming and coordination between the vendors. Another issue that has come up on some projects is when the building management system has to use a network and server that is provided by others, such as the facility IT department. In one instance, our team designed a new BMS, which was to use the client’s IT network and the client-provided server and front-end workstation. The client’s IT-management program required the installation of Windows software updates as they are released. However, the BMS software programming has to be updated each time a new patch is released and cannot function on a server if the patch is installed prior to the update of the BMS software. This issue was resolved by communicating the BMS software requirements to the client’s IT department and working with them to develop a schedule for updates.
CSE: Is your team using BIM in conjunction with the architects, trades, and owners to design a project? Describe an instance in which you’ve turned over the BIM model to the owner for long-term operations and maintenance (O&M) or measurement and verification (M&V).
Locke: We are incorporating Revit modeling in all the projects that require this level of coordination. The main purpose is to understand all the building restraints through an interference check and adjust the design accordingly. One client, Electronic Theater Controls, required that AutoCAD design drawings be developed into a Revit model because all the systems were exposed and this model helped them visualize the final product and make changes prior to construction. We also have engineering support services to assist some contractors in developing shop drawings through CADmep, running clash detection through Navisworks in teleconference coordination meetings, and continually adjusting the model until the area/project is complete.
Wiechart: BIM using Revit from a modeling standpoint has been a staple for our firm for many years now. We turn the model over to the owner and contractor for informational use only. While there are discussions with owners about using the model for O&M and/or M&V, we haven’t seen it implemented. Owners typically don’t have the access to hardware and software or trained Revit users to make this a reality yet.