From high-tech automation to energy-saving lighting and HVAC systems, there is more than meets the eye when it comes to warehouses and factories
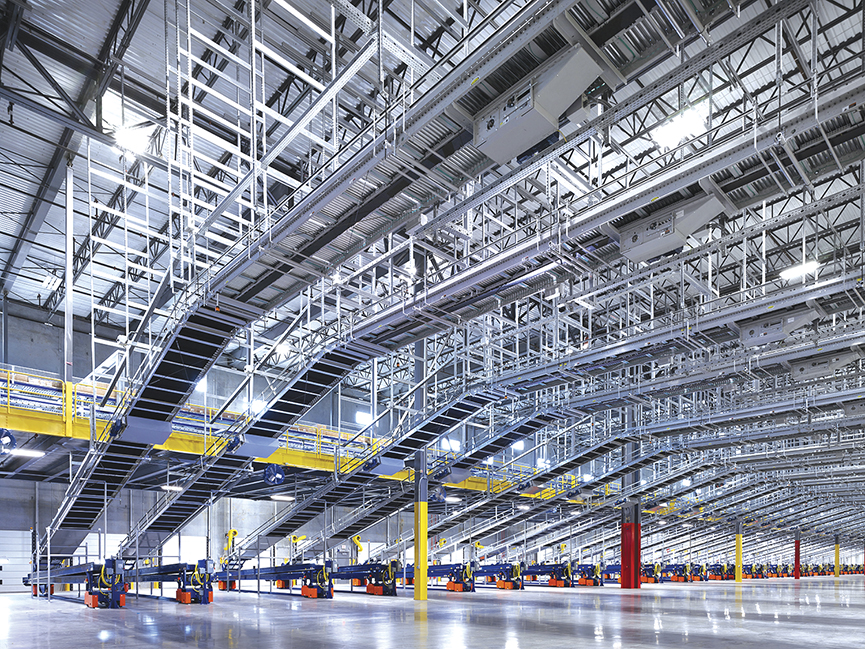
Respondents
Jason Danielson
Stanley Consultants
As an electrical specialist, Danielson has worked on low-voltage electrical design and special systems for industrial facilities, municipal government and federal government projects. His experience encompasses designing LED lighting and lighting control systems, low-voltage power, security, communication, surveillance, access control and fire alarm systems.
Justin M. Harvey, PE, LEED AP BD+C
Henderson Engineers
As Associate/Warehouse and Distribution Practice Director, Harvey leads the company’s team on large-scale facility design to maximize supply chains for high-profile retailers. As a teenager, he was encouraged by a teacher who told him he had the skills to become a talented architectural engineer.
Doug Sandridge, PE
RTM Engineering
Sandridge, principal, comes to RTM from Concord West, an engineering firm specializing in design, construction and management services that the firm acquired in June. His portfolio includes a number of liquor distilleries and international projects.
CSE: From your experience, what systems within an industrial/manufacturing facility and warehouse project are benefiting from automation that previously might not have been?
Sandridge: All will at some point. Auto storage and retrieval becoming standard now. Robotics are just around the corner. Human machine interface is always a key to efficiency.
CSE: What types of system integration and/or interoperability issues have you overcome for these projects and how did you do so?
Sandridge: Machine suppliers do not fully understand the constraints and restrictions of today’s buildings.
CSE: Is your team using building information modeling in conjunction with the architects, trades and owner to design a project?
Danielson: We’ve been using Autodesk Revit central models in conjunction with mechanical, structural and architectural disciplines for many years now. We’re seeing more BIM as a requirement from clients for the design. When engineers of different disciplines can design and see changes reflected immediately in a central model, it really helps with coordination and confirming constructability.
CSE: Has the “internet of things” come up in discussion or been implemented on such projects? How has this integration impacted the project?
Sandridge: It has — it’s caused less coordination of trades due to all not understanding the complexity of the other trades.
CSE: Cybersecurity and vulnerability are increasing concerns. Are you encountering worry/resistance around wireless technology and IoT as the prevalence of such features increases? How are you responding to these concerns?
Danielson: We’re hearing concerns from clients regarding cybersecurity for anything that is on a network and not just typical computer networks that most of us think of when we think the internet. We address lighting control systems, HVAC control systems and security or access control networks, among others. These systems are not always connected to the facility internet and many times are even air-gapped to remain unconnected to the main computer network.
However, malicious code can still infect these networks and cause damage. An attacker could gain access through a networked HVAC control system and access other sensitive networks, as we saw in late 2013 with the Target department store hack, which happened this way.
While we can’t control everything during commissioning, something to consider is specifying that commissioning agents must have the most up-to-date operating system with all new security patches installed before plugging any computer into a network to program a system. Another recommendation is to require they change the default passwords that may come pre-installed on a networked smart device immediately.
CSE: How has your technology team worked with facility managers to implement security technology (biometrics, card-scan, etc.) in industrial/manufacturing facility and warehouse projects?
Danielson: In my experience, access control and closed-circuit TV requirements come in the form of rooms and doors the client wants protected. We don’t always know what activities are taking place in certain spaces during design. We may make some recommendations on camera types or alternative access control schemes, but it’s generally client driven on what areas they want to protect. We would determine the camera specs required at each location. We would then design the system as a whole that may tie back to the communications room and a security desk where monitoring occurs.