A 372-bed replacement hospital required integration of a heat recovery chiller
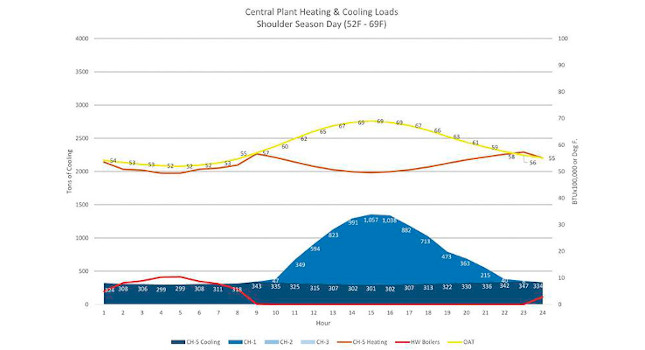
For this new 875,000-square-foot replacement hospital, a heat recovery chiller was integrated into the design of the chiller plant and sized to meet the 400-ton process cooling load. This capacity includes the operating suite air handling unit cooling coils, which allows the main chilled water plant to be taken offline during the heating season.
The heat recovery chiller is also capable of providing approximately 6,200 MBH of heating. This heating capacity exceeds the calculated hot water terminal reheat demand in the summer, which means that the boiler plant can be taken offline during the cooling season. During the shoulder months, all central plant equipment will be operating.
The goal was to maximize the loading on the heat recovery chiller due to its superior coefficient of performance relative to decoupled chilled water and hot water production. It was important to study the control strategies at different conditions throughout the year. It is critical to design the main chiller plant with a high turndown capability so the plant can slowly stage on while the heat recovery chiller maintains max cooling capacity when the total cooling load begins to exceed the capacity of the heat recovery chiller (see Figure 5).
Figure 6: This describes the interaction of the hot water heating plant, the heat recovery chiller cooling, the heat recovery chiller heating and the central chilled water plant during a typical shoulder season day. Courtesy: SmithGroup[/caption]
The integration of a heat recovery chiller into the central utility plant lowers the dependence on fossil fuels as clean electrical energy sources become more prevalent and reduces the overall energy use of the facility. Figure 6 describes the interaction of the hot water heating plant, the heat recovery chiller cooling, the heat recovery chiller heating and the central chilled water plant during a typical shoulder season day. The study of how this equipment will work together during different operating conditions helps to develop the chiller plant control strategy and helps to define the heat recovery chiller capacity.
The central utility plant for this hospital includes:
- Six 8,000 MBH hot water heating boilers.
- Three 1,200-ton centrifugal chillers.
- One 482-ton heat recovery chiller.