The flow rate, pressure losses, best efficiency point compared to the duty point, and the operating cost are all important factors when selecting a pump for HVAC applications.
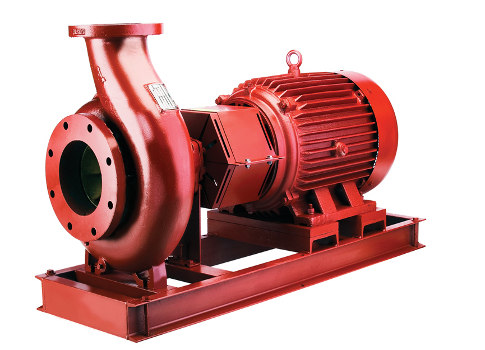
Learning Objectives
- Understand the various pumps available for HVAC systems.
- Learn about pump system configurations.
- Know how to calculate HVAC loads in order to select the correct pump.
There are several types of pumps used in fluid transfer, but the most common used in today’s HVAC systems is the centrifugal pump. Types of centrifugal pumps include volute or axial flow pumps. The volute takes water from the impeller and discharges the water perpendicular to the shaft. A centrifugal pump with a diffuser casing (axial flow pump) discharges the water parallel to the pump shaft.
Centrifugal pumps are available in many types including circulator, single- and multi-stage end-suction, single- and multi-stage split-case, and vertical in-line pumps.
Circulating pumps are typically used in low pressure, low-capacity systems. The size of this system is typically under 150 gpm and not rated for more than 125 psig operating pressure. This type of pump is typically mounted directly in and supported by the piping system and is available with the motor in either the vertical or horizontal position. See Figure 1 for a standard circulating pump.
End-suction pumps are single-suction and can either be close- or flexible-coupled. A close-coupled pump has the impeller directly mounted to the motor shaft. A flexible-coupled end-suction pump has the impeller and the motor shaft separated by a flexible coupling. The benefit of using a close-coupled pump is that alignment of the motor shaft to the impeller is fixed. A flexible-coupled pump can become misaligned during maintenance. This can create issues if not properly reassembled by trained personnel. End-suction pumps are designed such that the incoming water enters the pump through the end in a horizontal manner. The water then changes direction and is discharged vertically, perpendicular to the suction. These pumps are typically installed on a solid base on the floor. An end-suction pump is capable of being used in HVAC systems with capacities up to 4000 gpm and 150 ft of head.
The advantage to using a close-coupled pump is that it requires less floor space within a plant room for installation. One of the disadvantages of using a close-coupled pump in an HVAC system is the motor type. The motor is typically specially matched to the type of shaft and the seals for the pump. Flexible coupled pumps typically use standard motors. See Figure 2 for a typical flexible coupled end-suction pump.
Split-case pumps are similar to end-suction pumps in that they are flexible coupled between the motor and the pump. The assembly, including the motor and pump, is rigidly mounted to a common base-plate. Pump suction and discharge are arranged in the horizontal direction and are perpendicular to the shaft.
Split-case pumps are available either in single- or double-suction. To be a single-suction pump, the water enters the impeller from only one side. For double-suction, the fluid enters the impeller from both sides. Using double-suction reduces the risk of hydraulic imbalance. The reduction of hydraulic imbalance is one of the reasons why double-suction split-case pumps are preferred over single-suction.
Split-case also may have multiple impellers for multi-stage operation. Multiple impellers provide increased available head within a single pump.
Split-case pumps are available as horizontal or vertical split-case. For horizontal split-case pumps, the impeller casing is split in the horizontal plane. For vertical split-case pumps, the impeller casing is split in the vertical plane. To have the casing split allows full access to the impeller for maintenance.
Split-case pumps are used mostly in fire protection systems but also have been used in the HVAC industry for large capacity systems. Their capacity range is up to 6500 gpm and 600 ft of head. These pumps are also available with increased operating pressures up to 400 psig. See Figure 3 for a typical horizontal split-case pump.
These pumps typically have a reduced footprint within a plant space and do not require inertia bases. Inertia bases are generally installed to reduce vibration from the rotating parts within the pump. discharge piping are arranged in the horizontal plane. Vertical in-line pumps are available as single- or double-suction.Vertical in-line pumps are close-coupled. The pump and motor are directly mounted on the pump casing. The pump is typically mounted and supported by the piping system in which it is installed. For larger capacity vertical in-line pumps, the pump assembly may be provided with a base for floor mounting. The pump suction and
Vertical in-line pumps have a capacity of up to 25,000 gpm and 300 ft of head. See Figure 4 for a typical vertical in-line pump.
Types of pumping systems
There are two types of systems in which pumps can be installed: closed-loop systems and open-loop systems. In the HVAC industry, closed loops are systems in which the static elevation is not accounted for in head pressure calculations. Chilled water and heating hot water systems are typically closed-loop systems. An open-loop system is defined by the system having a pipe that is open to the atmosphere. Pumping systems associated with cooling towers are considered to be open-loop systems in that the spray nozzles at the top of the tower are open to the atmosphere. See Figure 5 for closed-loop and open-loop general configurations.
When selecting a pump for closed-loop systems, several factors are to be considered, such as pressure losses associated with the total horizontal and vertical length of piping, the piping elbows and tees (fittings), the valves in the system, miscellaneous piping accessories, the equipment coils, the minimum system pressure to be maintained, and net positive suction head required (if applicable).
Each pipe size has an associated pressure drop depending on the velocity at which the fluid is being circulated. The fittings have a specific pressure drop associated with them as well. Each valve in the system, such as shut-off valves, check valves, balancing valves, strainers, etc., have published manufacturer’s literature for pressure drop for the listed size and flow rate. Each piece of equipment in the system, including cooling coils, heating coils, and chillers, also has manufacturer’s literature for pressure drop at a given flow rate. Table 1 is a sample of how to sum the pressure losses in a closed-loop system.
As demonstrated in Table 1, a pressure drop for the system equates to approximately 81 ft. The required pump for the system indicated in Table 1 would need to provide a minimum of 81 ft of head to properly distribute the fluid to the system.
For open-loop systems, in addition to the pressure loss associated with a closed-loop system, the static elevation must also be considered.
In Table 2, we have replaced the air handling equipment (coils) and the system pressure with a cooling tower and the static elevation, respectively. The static elevation of the system is the difference in the height of the inlet of the cooling tower to the discharge of the cooling tower.
In selecting a pump for an open system, the net positive suction head required (NPSHr) and net positive suction head available (NPSHa) must also be considered. NPSH is defined as the pressure at the inlet of the pump. If the pressure at the pump inlet is less than the vapor pressure of the fluid at the local temperature, the liquid will boil at the impeller, creating vapor bubbles. The creation of the vapor bubbles is defined as cavitation. Cavitation in a pump can lead to premature failure due to erosion of the impeller, and fatigue of the shaft bearings and seals.
The calculation to determine NPSHa is:
NPSHa = Patm + Ps – Pvp – Pf
Patm: Atmospheric pressure (ft)
Ps: Static height of water above the pump impeller (ft)
Pvp: Vapor pressure of water (ft)
Pf: Friction losses in piping (ft)
As indicated in Figure 6, the NPSHa equates to 45.9 ft (34.2 ft + 15 ft – 1.3 ft – 2 ft = 45.9 ft).
The NPSHr is typically provided by the manufacturer of the pump being used in the system. The NPSHa must be greater than the NPSHr to prevent cavitation. A margin of safety is recommended to be applied to the NSPH to ensure that cavitation does not occur in the system. A typical margin of safety is 3 ft when determining the NPSH of a system. If the NPSHa is 45.9 ft, a pump with a maximum NPSHr of 40 ft should be used.
Pump system configurations
Several configurations can be used in pumping systems. Pumps can be arranged in parallel, series, and also in a primary/secondary pumping configuration. Pumps that are installed in a parallel configuration are used when additional flow is required at the same system pressure and a single pump is not capable of meeting the system requirements (see Figure 7). Pumps that are installed in a series configuration are used when additional pressure at a set maximum flow rate is required and a single pump is not capable of meeting the system requirements (see Figure 8).
Primary/secondary pumping is used when the volumetric flow rate varies between the equipment and the system. As technology advances on the equipment used in fluid systems, a reduction in the use of primary/secondary systems has been noticed.
Chilled water and heating water systems were typically designed as primary/secondary. The reason for using a primary/secondary pumping configuration was due to the chillers and boilers requiring a constant flow rate at all times. The primary circuit is constant flow 100% of the operating time. The secondary circuit uses variable flow. The pump ramps up and down on the variable frequency drive (VFD) to match the flow rate to the system requirements.
The use of two-way valves in the system allowed the flow rate at the equipment to be reduced to match the coil loads. The increase in pressure in the system by closing the valves sends a signal back to the pump to reduce the flow. This is accomplished by installing differential pressure sensors in the piping system. The differential pressure is kept constant. As the valves close, the system pressure increases. This tells the pump to slow down and reduce flow to maintain the constant pressure.
Before the technological advances of the VFD, chilled and heating water systems were operated with constant flow pumps and three-way valves. The three-way valve allowed the water to either go through the coil or be diverted through a bypass back into the system. This system was constant volume 100% of the time. That means that regardless of the load requirements of the system, the pump was operating at 100% of its design capacity. To operate a system in this manner is a massive waste of energy. With the introduction of VFDs, the building loop was capable of being operated at a point consistent with the load. As the load in the building reduced, the pump was able to reduce its pumping capacity. An example of primary/secondary pumping is illustrated in Figure 9.
Selecting a pump
When selecting a pump, several factors must be considered. Once the building HVAC loads have been determined, the flow rate can be established. Then the pressure losses of the system are to be calculated. Consider the following example:
A chilled water system is to be designed for a building. The system will include an air-cooled chiller, air handling units, and piping distribution. The peak heat loss for the building is calculated to be 2,400 MBH with a minimum heat loss of 840 MBH. This was determined by the HVAC loads performed on the building. By using a 12 F delta for the entering and leaving water temperatures at the chiller, a maximum flow rate of 400 gpm and a minimum flow rate of 140 gpm are required. The distribution system has a total developed length (TDL) of 350 ft of piping including fittings. As stated previously, the pressure losses need to be calculated. See Table 3 for a summary of pressure losses in the system.
To calculate the pressure losses associated with the piping, the rule of thumb is to use 2 to 3 ft per 100 ft of piping as a pressure loss and also maintain a maximum velocity of 8 to 10 ft/second (fps). Erosion of the piping can occur if the velocity is too high. In the above calculation, 2.5 ft per 100 ft of piping was used for pressure losses.
Based on the above calculations, the pump selection will be at a design condition of 400 gpm and 85 ft of total dynamic head (TDH).
Now that the flow rate and pressure loss are known for the system, the selection of the pumps can begin. At this point in the selection process, a pump curve will be required. Before we pull out the manufacturer catalogs or research it online, first we have to determine the best type of pump for this application. The way that this is determined is by reviewing the manufacturer’s literature to determine the operating range of each type of pump. Circulator pumps are typically used for low-flow applications, so this type of pump would be too small. End-suction pumps are typically used for small- to medium-sized systems.
As this system is a medium-sized system, the end-suction pump is a potential option. Vertical in-line pumps are typically used in small- to large-scale projects, so these pumps are another option. Split-case pumps are typically used for large hydronic systems. This type of pump would be too large to meet the requirements of the system described above.
Based on the pump uses and system requirements, end-suction pumps and vertical in-line pumps have the capabilities to operate within the design parameters.
There are online calculators provided by the manufacturers that can assist with the selection of the pump, or the manufacturer’s catalog can be used. For the system in the above example, we need to review if a single pump can achieve both the maximum flow rate and the minimum flow rate. This is determined by plotting the points on potential pump curves. If a single pump is not capable of achieving the maximum and minimum flow rates, a second pump will be required and piped in a parallel configuration (see Figure 7).
As indicated in the pump curves in Figure 5, a single pump can be used to meet the maximum and minimum flow rates of the system.
As depicted in Figures 5 and 6, the vertical in-line pump is not a good selection as the duty point is to the right of the best efficiency point (BEP). In addition, the operating efficiency is at approximately 70%. The end-suction pump appears to be the better selection of the two. Not only does the end-suction pump have a higher operating efficiency at 76%, but the duty point is located to the left of the BEP.
In determining the proper pump, there are other factors besides the pump curve and efficiency that must be evaluated. The operating cost over the life of the system is a crucial element as well. The vertical in-line pump represented above operates at 11.39 brake horsepower (bhp)/8.50 kW at full load. For simplicity, we can assume that the vertical in-line pump operates 24/7, and 74,400 kWh are consumed. If the cost of electricity is $0.10/kWh, an annual operating cost of $7440 is incurred by the owner. The end-suction pump represented above operates at 10.71 bhp/7.99 kW at full load. Using the same operating hours as the vertical in-line pump, the operating cost incurred by the owner for the end-suction pump is $7000 per year. An annual savings of $440 in operating cost each year is calculated for the end-suction pump.
As one can see by the operating cost, the end-suction pump not only operates at a more suitable point on the pump curve, but also has a reduced operating cost when compared to the vertical in-line pump. For realistic operating cost analysis, the pump operating hours should be determined based on the load profile of the facility for which the pump is being selected. In lieu of calculating the operating cost based on 24/7 full load operation, an equivalent full load operating hours should be inserted in the calculations.
Several factors can have an impact on selecting the best pump to be used on a project. The flow rate, pressure losses, best efficiency point compared to the duty point, and the operating cost are all important factors when selecting a pump. Start with the required flow rate to determine which pump type is best suited for the application, then use the pump curve and operating cost analysis to finalize the selection.
Amy Lasseigne is associate director of mechanical at JBA Consulting Engineers. Her expertise is the design of multiple central plants ranging from 150 to 20,000 tons. These central plants serve casino resort facilities on the large scale as well as educational facilities and office buildings on the small scale.