Engineers must know the required air changes per hour, depending on the building type. Whether designing a laboratory in an educational facility or hospital, knowing the ventilation rates is key.
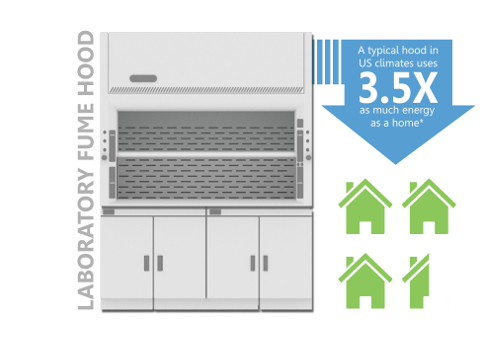
Learning Objectives
- Provide a high-level view of the various codes and standards that affect ventilation in different types of laboratories.
- Understand that keeping ventilation amounts to a minimum while still meeting safety requirements is key to energy savings.
I was at a weeklong laboratory seminar at Harvard University years ago. When we approached the portion of the seminar that involved ventilation rates, I leaned forward in my seat with great anticipation. I was finally going to get the definitive, end-all answer to the great air changes per hour (ACH) debate. I believe it was the gentleman from the Massachusetts Institute of Technology (MIT) who stood at the podium and asked the seminar participants what the correct ACH value should be when designing a laboratory. After several answers that ranged anywhere from 4 to 18 ACH, the gentleman from MIT thanked everyone for their answers and told them that they were all wrong. I was at the very edge of my seat waiting to hear the correct answer. He continued by saying that the correct answer was, and I quote, "it depends." I fell out of my chair.
I didn’t realize it at the time, but that gentleman could not have been more correct. After having spent years designing laboratories that include educational laboratories, hospital laboratories, research and development (R&D) laboratories, and compounding pharmacies, the ventilation rates depend on usage, facility standards, and code enforcement for the particular project type.
Relevant codes and standards
Several codes and standards do the majority of the heavy lifting when it comes to laboratory ventilation rate designs:
- 2014 FGI Guidelines for the Design and Construction of Hospitals and Outpatient Facilities (Includes ANSI/ASHRAE/ASHE Standard 170)
- NFPA Standard 45
- ANSI Z9.5
- OSHA
- ASHRAE Standard 90.1
- California Mechanical Code (this is an example of a local code).
Below is a summary of the ventilation portion of each code/standard that can be used as a quick reference tool when discussing laboratory ventilation with clients.
2014 FGI Guidelines for the Design and Construction of Hospitals and Outpatient Facilities (Includes ANSI/ASHRAE/ASHE Standard 170)
ACH Range: 4 to 10 (USP 797 requires 30)
This standard is coupled with ANSI/ASHRAE/ASHE Standard 170 to develop a comprehensive ventilation table. The laboratory ACH rates can be seen in data taken from Table 7.1. Table 1 shows a summary of the ventilation portion of the table.
The FGI guidelines also touch on compounding pharmacies, which can have 30 ACH in order to maintain the appropriate level of cleanliness for the process. This standard defers compounding pharmacy design to USP 797.
NFPA 45: Standard on Fire Protection for Laboratories
ACH Range: No range given
This standard provides the general statement that "laboratory ventilation systems shall be designed to ensure that fire hazards and risks are minimized." This means that you need to consult the chemical consultant on the project for the proper storage and dilution rates.
Spaces and hoods that contain chemicals are to be continuously ventilated under normal operating conditions.
While accomplishing this, the exhaust and supply systems must also be designed to prevent a pressure differential that would prevent doors from being opened when either system fails or during a fire or emergency scenario.
Laboratory ventilation systems designs are to ensure that chemical fumes, vapors, or gases originating from the laboratory are not recirculated.
The design should ensure that air pressures in the laboratory work areas are negative with respect to corridors and nonlaboratory areas of the laboratory spaces except for positive pressure cleanrooms, when doors are opened, fume hood sash positions are changed, and other short-term temporary activities that would affect static pressures. The other exception is in a designated electrically classified hazardous area with a positive air pressure system as described in NFPA 496: Standard for Purged and Pressurized Enclosures for Electrical Equipment.
Special local exhaust ventilation systems, such as snorkels, are to have sufficient capture velocities to entrain the chemical being released. It is important to not underestimate what is required to provide proper capture velocities. These calculations are in the ACGIH Industrial Ventilation guide and can range from 75 to 2000 fpm, depending on the configuration and process.
ANSI Z9.5
ACH Range: "Air changes per hour is not the appropriate concept for designing contaminant control systems." However, it suggests 4 to 10 ACH for fugitive emissions and odors.
This standard is the most comprehensive and is to be followed during any laboratory design. This standard does not prescribe an ACH rate. It simply states that the specific room ventilation rate shall be established or agreed upon by the owner or his or her designee. All contaminants should be controlled at the source.
The following section of the standard is in complete agreement with the gentleman from MIT I referenced earlier. It states that an air exchange rate cannot be specified that will meet all conditions: "Air changes per hour is not the appropriate concept for designing contaminant control systems."
In fact it goes further to accurately state that "excessive airflows can lead to designs that are very energy inefficient."
The standard does, however, require dilution ventilation to control the buildup of fugitive emissions and odors in the laboratory. However, source exhaust ventilation should be the primary method of capturing fumes in a fume hood. Typical dilution ventilation rates can range from 4 to 10 ACH depending on heating, cooling, and comfort needs and the number and size of exposure control devices.
The standard recommends that variable air volume (VAV) fume hoods be considered to save energy in ventilation. This is a good place to save energy as air exhausted by fume hoods needs to be replaced with conditioned air. The conditioned air will require a larger air handling unit, chiller, and boiler. The Dept. of Energy (DOE) has published data that indicates that a single fume hood uses as much energy as 3.5 homes, which really promotes reducing any ventilation associated with fume hoods.
However, if VAV hoods are used, it is recommended that they be equipped with an emergency override that would permit full design flow in the event there is a spill, even if the sash is closed.
Safety and energy usage must be considered when designing the ventilation system to account for fume hood face velocities. The fume hood manufacturer must show that the hood has passed tests using ANSI/ASHRAE Standard 110: Method of Testing the Performance of Laboratory Fume Hoods at the selected face velocity.
The typical range for face velocity is 80 to 120 fpm. It is never recommended to operate below 60 fpm
Low-flow "energy-efficient hoods" have face velocities of 60 to 80 fpm, but these types of hoods must have excellent containment characteristics and operate in ideal conditions with respect to open windows, doorways, and personnel traffic flow, as these will adversely affect the containment of chemicals within a fume hood.
Airflows to achieve the face velocities must be capable of keeping vapor concentrations between 10% and 25% of the lower flammability limit (LFL) or lower explosion limit (LEL). This would typically be calculated by the chemical consultant.
Air pressure in labs is typically negative unless trying to protect a space, such as a cleanroom, in which case the space will be positive. It is very important to design the building envelope to reduce the amount of transfer air required to maintain the correct pressurization. The standard also recognizes that it is impractical to maintain a differential pressure across an open door due to the effective large leakage area. Often a door switch with an alarm delay is used to avoid nuisance alarms associated with door openings.
A method to save energy and capital costs is to not size the ventilation system to accommodate the full flow of the fume hoods. A diversity factor may be used to anticipate the actual number of hoods in use at one time. When applying a diversity factor, a designer must consider a wide range of topics, which include but are not limited to: expansion considerations, minimum and maximum ventilation rates for each laboratory, quantity of hoods and researchers, sash management (sash habits of users), and use patterns of variable volume hoods.
It is crucial that the users agree to the diversity factor and understand the limitations to the laboratory. Not all fume hoods can be used at one time if a diversity factor is used. An airflow alarm system must be installed to warn users when the system is operating beyond capabilities allowed by diversity.
The standard also requires that an emergency ventilation system be designed when a certain type and quantity of chemicals or compressed gases are present in a laboratory that would warrant emergency ventilation. This would be determined by the chemical consultant on the team and would allow for the ACH rate in the space to be raised during a spill.
In the event of an emergency mode operation or a fire mode, typical schemes that simply turn off supply to a space and maintain exhaust flows cannot be done without taking room pressurization into consideration. The ventilation system must not create a large pressure differential that would prevent a user from opening a door to leave the area.
In general, the standard states that return air is not to be used in laboratories with hazardous chemicals or biological hazards.
As an energy-saving strategy, energy recovery systems should be evaluated to reduce the energy needed to condition a large outside air intake.
Ultimately, the ventilation rate selected for a laboratory depends on the largest airflow of thermal comfort, dilution and displacement of contaminants not captured by exposure control devices, and makeup air to account for the operation of exposure control devices such as laboratory hoods, space pressurization, or minimum code occupancy ventilation. These must all be considered before settling on the ventilation rate.
OSHA
ACH Range: No range given
OSHA requires that hood face velocities maintain an inward flow of air at all times. The average face velocity is to be at least 100 fpm with a minimum of 70 fpm at any point. A non-use setback of 60 fpm is allowed if there is an automatic control system and if the hood meets ASHRAE Standard 110 during those conditions.
This standard further requires that the face velocity be adequate to not exceed 20% of the lower explosive limits.
ASHRAE Standard 90.1
ACH Range: No range given
ASHRAE Standard 90.1 allows laboratories to be exempt from typical energy requirements with respect to energy recovery effectiveness and temperature reset strategies. This standard mandates that buildings with laboratory ventilation exhaust airflow amounts higher than 5,000 cfm shall either have VAV exhaust ventilation systems and/or provide energy recovery.
Systems serving laboratory spaces shall reduce the exhaust and makeup air volume during unoccupied periods to the largest of one of these three options: 50% of zone peak airflow, the minimum outdoor air flow rate, or the airflow rate required complying with applicable codes or accreditation standards. The standard also prescribes the allowable ventilation airflow though capture hoods (see Table 2).
California Mechanical Code
ACH Range: 4 to 10
For educational laboratories, the state code requires 10 cfm/person (at a density of 25 people per 1000 sq ft) and 0.18 cfm/sq ft.
The state’s hospital code enforcement, Office of Statewide Health Planning and Development (OSHPD), requires specific ACH rates listed in Table 3.
Who’s involved?
Knowledge of the standards and codes is not adequate information to design the ventilation system for a laboratory on its own. When developing the ventilation strategy with the user, it is important to meet with the following stakeholders and design team members:
- End user
- Environmental health and safety (EH&S) department
- Facility engineer
- Design team chemical consultant
- Lab planner
- Architect
Each member will bring a piece of the puzzle to the table. The end user will discuss how the system is used, which will affect control strategies and how the lab planner will select equipment. EH&S will convey the standards set by the owner/company. The facility engineers can provide insight into maintenance and energy usage of the building. The chemical consultant will provide data that will affect emergency exhaust requirements and fume hood face velocity to maintain LELs. The lab planner will advise on miscellaneous heat loads and number of contaminate source exhausts. Finally, the architect will assist with the envelope information that will help determine ventilation used for pressurization.
The strategies in the codes and standards above will change depending on the type of laboratory that is being designed. The following are items to consider for the different types of laboratories.
Educational facilities: The health care standards and codes do not apply. It is important to determine the chemicals that will be used and if they will require the emergency purge required by ANSI Z9.5. Unfortunately, due to the use of fume hoods in a teaching laboratory, diversity factors discussed above will likely by very small to none at all. These types of facilities can take advantage of VAV hoods and unoccupied setback, because of the scheduling of classes.
Hospitals: State codes, such as OSHPD, are the primary driver of the ventilation rates for a hospital. However, they are to be considered minimums and the final rates are to be determined by understanding how the laboratory is going to be used and what chemicals are present. Often a hospital has its own guidelines and standards that should be followed if they are more stringent than the state code. It is also important to note that some of the standards contradict each other and should be vetted if a facility is using both to design a project. An example would be ventilation for "laboratory, biochemistry." FGI requires the room to be negative and the air to be exhausted directly outdoors, whereas the state code requires biochemistry to be positive and does not require the room to be directly exhausted to the outdoors. USP 797 is to be followed if designing a compounding pharmacy.
Research and development (R&D): The health care standards and codes do not apply. Understanding usage and plans for future growth is instrumental when deciding the ventilation for R&D facilities. As noted earlier, hoods require a lot of energy. Without completely understanding how each department functions, each one will want several hoods. For example, I once worked on a project where the company started with 14 100% exhausted biosafety cabinets (BSCs). After spending some time speaking with the various departments, it was determined that only one of the BSCs was required to be 100% exhausted. This not only saved the owner the upfront cost of exhaust fans and stainless steel ductwork, it also saved the cost of larger supply air systems, boilers, and chillers to introduce conditioned outside air to make up for the air exhausted through the BSCs.
There is no single answer to what the ACH rate is when designing a laboratory. Designers need to make sure that they follow the standard of care. To provide true consulting services, the team must advise on safety, energy usage, initial cost, and the option that would be recommended to fit the particular need of the facility.
Rick Russell is a principal at Interface Engineering; he works in the San Francisco and Hawaii offices. He specializes in laboratory and health care design, and has designed educational, health care, and research and development laboratories.