Ideally, all nonresidential buildings would be commissioned, and the team would start at the onset of the project. Because that’s not always the case, commissioning authorities and experts offer advice on building projects in various stages of commissioning, recommissioning, or retro-commissioning.
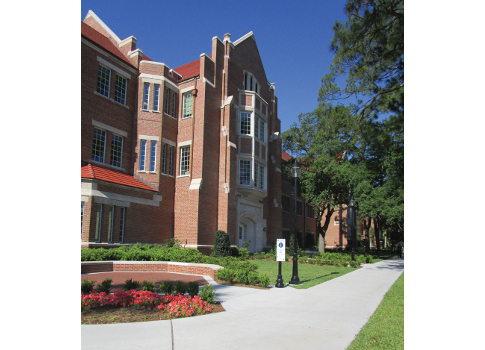
Respondents
Mark A. Gelfo, PE, LEED Fellow, GGP, CxA, EMP, Principal/Vice President, TLC Engineering for Architecture, Jacksonville, Fla.
James I. Givens, CxA, EMP, Division Manager, Field Services, RMF Engineering Inc., Baltimore
Jim Huber, CEM, CDSM, CMVP, LEED AP, NEBB CP, President, Complete Commissioning, Annapolis, Md.
Brian Lindstrom, PE, DCEP, National Director of Commissioning, Burns & McDonnell, Kansas City, Mo.
Paul Meyer, PE, CBCP, LEED AP, CEM, GBE, Senior Vice President, WSP, New York City
CSE: Please describe a recent project you’ve commissioned.
Jim Huber: Some details of the project cannot be shared; however, it was a hangar facility on a military base in Delaware. The facility is approximately 66,000 sq ft, comprised of a large hangar bay, facility operations, and office space. The project was approximately 2 yr old and had never performed properly since the project turnover; we were brought on to do third-party commissioning of the mechanical systems. The commissioning effort was originally focused primarily on the HVAC systems (geothermal water-source heat pumps, water-to-water heat pumps, boilers, and air handlers), but eventually expanded to include the building enclosure.
Brian Lindstrom: We recently commissioned two new combined heat and power (CHP) plants with more than 40 MW of N+1-redundant capacity as part of a multiphase energy-performance program for a federal research campus in the Washington, D.C., metro area. Our work was in conformance with ASHRAE Guideline 0, U.S. Green Building Council LEED enhanced requirements, the GSA P100, and mission critical facility best practices for central utility plants that included functional testing, integrated systems testing, and black-start testing. Key equipment included natural gas combustion-turbine generators (CTG), heat-recovery boilers, absorption chillers, electric centrifugal chillers, steam chillers, thermal-energy storage tanks, heat-recovery steam generators (HRSG), diesel generators, and a balance of plant (BOP) control system.
Paul Meyer: The Plant and Animal Agrosecurity Research (PAAR) Facility is a highly secure biocontainment building. It is for conducting research with organisms that cause diseases in animals classified at biosafety level 3 (BSL-3 and BSL-3 Ag). It is also needed for working with plant diseases that could cause undue economic hardship on agriculture if released into the environment. PAAR is one of only two labs nationally with capacity for both plant and animal research at the BSL-3 and BSL-3 Ag safety levels. Ohio State University operates the BSL-3 facility on the Wooster campus, and it is the university’s first BSL-3 Ag facility. BSL-3 and BSL-3 Ag refer to safety guidelines established by federal law for conducting research with a variety of microorganisms. Under federal guidelines, all facilities handling potentially infectious agents must adhere to strict procedures to ensure containment of these pathogens. Depending on the ease with which microorganisms can be transmitted, they are classified as BSL-1, BSL-2, BSL-3, or BSL-4, with BSL-4 carrying the highest risk of infection. A BSL-3 Ag facility meets the standards for handling diseases of food-producing animals classified at the BSL-3 safety level.
The facility comprises:
- 27,537 gross sq ft
- Two BSL-3 enhanced laboratories and four BSL-3 Ag animal-isolation rooms that can handle large animals such as cows and pigs
- Office, lockers and changing facility, decontamination areas, wash areas to clean cages, and a necropsy area for sample collection
- Special airtight construction
- Outgoing air is filtered through high-efficiency particulate air (HEPA) filters that trap microorganisms and prevent escape into other sections of the facility and the surrounding environment.
CSE: Break down the amount of commissioning projects your company has completed in the past 12 months by percentage.
Mark Gelfo: The vast majority of our commissioning work, approximately 75%, is new-building commissioning. The remaining 25% consists of a mix of retro-commissioning (retro-Cx) and energy auditing. Often, the lines are very blurred between retro-Cx (strictly returning the building to the original as-intended operating condition) and energy auditing. Building owners and requests for proposal (RFPs) often ask for retro-Cx or energy auditing when they really want an overall building energy evaluation, improvement, and implementation plan, similar to the Energy Management Association’s Energy Management Process. What most owners really want is to reduce the overall energy consumption and operating cost of their building, and not just to return the building operation to the way it was originally designed. Very little of our work would be classified as recommissioning, i.e., commissioning of a building that has previously been commissioned. We see very little recommissioning work for two very different reasons. On one end of the spectrum, most buildings that are initially commissioned are, unfortunately, never recommissioned at all. At the other end of the spectrum, some owners who have commissioned their new buildings or retro-commissioned their existing buildings have moved onto a regular continuous measurement and verification (M&V) and ongoing commissioning program, and have trained in-house personnel to perform their recommissioning. And we couldn’t be happier—who better to do commissioning than the people who are going to operating the systems and occupy the building?
Meyer: Several cities across the country have enacted legislation requiring retro-commissioning and/or energy auditing. This has driven a dramatic increase in retro-commissioning the way LEED drove new-construction commissioning growth. The New York City Local Law 87 is a great example, requiring both retro-commissioning and an ASHRAE Level 2 audit every 10 yr for buildings larger than 50,000 sq ft.
Lindstrom: We’ve done 64% commissioning (Cx), 33% retro-commissioning (retro-Cx), 3% recommissioning (re-Cx).
Huber: It’s been 62% commissioning; 31% retro-commissioning; 7% recommissioning.
CSE: How has your engineering firm met the needs of commissioning clients in other countries? Have you opened an office abroad? Sent engineers or commissioning agents for short- or long-term projects overseas?
Givens: First and foremost, you must be willing to travel—there’s absolutely no way around that. You must also be flexible, patient, and able to function remotely. We have not opened an office abroad; we have not yet seen the need to establish an overseas office. RMF Engineering has deployed its commissioning team members for both short- and long-term assignments, depending on the project details and commissioning scope requirements. In general, with diligent planning and scheduling, most international commissioning activities can be conducted on site in a matter of weeks rather than continuous months or years.
Huber: We are not an engineering firm. While we have licensed professional engineers on staff, we do not do design work—we are a dedicated commissioning firm. We have not opened an office abroad, but we have partnered with local firms in other countries where they assist with the manpower requirements for the project and we provide the on-site technical expertise. In most cases, this is the only cost-effective means we have found for large projects. In some countries, we are required to work through a local firm due to the laws of those countries. For smaller projects, we simply handle them as we would any out-of-town project in the states.
Meyer: We have engineers who travel abroad and we have offices in foreign countries. Often, our U.S. staff meets with and trains the local staff in the commissioning process.
Lindstrom: Many of our clients are multinational firms and have long recognized the value of commissioning for new and existing facilities. To meet this demand, we have established both permanent and temporary project offices internationally. For project and permanent locations, we expatriate U.S.-based commissioning leadership and resources. When feasible for longer-term projects and permanent international locations, we relocate U.S. staff and hire local resources.
CSE: What business-development techniques are you using to gain commissioning clients and/or projects?
Gelfo: Many engineers and commissioning authorities think “business development” is a dirty word, or it’s beneath them, or they’re scared of it. As an engineer, a commissioning authority (CxA), and a certified professional services marketer (CPSM) I can tell you with confidence that business development is not rocket science, you just have to do it. Most of our new-building-commissioning business development happens in two ways. First, through formal requests for quote (RFQ) and RFPs that we aggressively track and pursue, sometimes months in advance of their being released. That means talking to people—often our existing clients—and asking questions to find out what we can about the project, so we’re ready when the RFP is released. The second, which is my much-preferred method, is by doing great work. By being proactive and exceeding client expectations, and by being a valued resource and trusted advisor to our clients, so they ask us to commission all their projects and recommend us to other clients. Repeat clients are the best clients to have! Our approaches to winning retro-commissioning and winning energy-auditing work are very similar—provide great service—but we often need to make more of a business case for operational savings. The financial component becomes a much more important piece of the conversation, and we often find ourselves talking to owners and CFOs who understand capital rates and return on investment (ROI) much better than kBtus. Having case studies of our past projects to show the real savings those projects have realized is important, and we will often do a benchmarking and preliminary energy-audit analysis as part of the marketing effort to show a building owner the energy and operational savings potential for their property.
Lindstrom: Burns & McDonnell enjoys extraordinary success in winning work from repeat clients. For commissioning projects, 90% of our business is developed and expanded through repeat, enterprise-type clients. For the remaining 10%, our projects are won through strategic marketing of mega/specialty projects and developing new enterprise relationships.
Huber: We do very little advertising. Our best business-development technique is our quality work. There is a minimum cost that is required to do a project properly, and we refuse to go below that line. Our customers respect that and we understand that their budgets don’t always allow them to use us. Where many firms will adjust the scope of work to the customer’s budget, we try to explain to them why their budgets are not realistic. They can’t always do anything about it, but they respect us for it. In the past month alone, we have been called to three buildings that were commissioned by other firms because the owner tried to save money and we would not drop our price. These were new-construction and fit-out projects varying from $5 million to $150 million. Being called back to do properly what an owner has already paid others to do is the best form of advertising I can think of, and always results in repeat business from that client if they are a multiple-facility owner.
CSE: How have the characteristics of commissioning projects changed in recent years, and what should engineers expect to see in the near future?
Meyer: With each passing year, more contractors have been exposed to commissioning, making it easier to get their buy-in to the process. Fear of the unknown often creates push-back from contractors, but after they experience the commissioning process they are more likely to cooperate fully. Some contractors have realized that commissioning makes it easier for them to claim money against their schedule of values by stating “The commissioning engineer says my equipment works as required, so pay me.” Experienced contractors also know not to cut corners because the CxA will find them.
Givens: Like it or not, in many aspects of the design and construction industry, commissioning is becoming a commodity rather than a niche service. Various requirements, incentives, and jurisdictional mandates to incorporate commissioning into project requirements have contributed to this shift. This has, in turn, suppressed the commandable fees for a quality-based professional service. Instead, commissioning services are increasingly being sought out with the fee as the determining factor. As such, certain aspects of the commissioning process that may previously have been incorporated into the commissioning provider’s scope by default will likely trend toward others. Notable examples are the basis of design (BOD) and design intent document. Historically, much of this information and documentation may have been embraced by CxAs and incorporated into their scope of work. Now that commissioning fees are being driven down, and commissioning process requirements dictate that the engineer of record provide the formalized BOD and design intent information, engineers can expect to see that they are held accountable for producing and delivering such information to the team as part of commissioning projects.
Huber: The biggest change we have seen is that in the absence of commissioning standards, many owners have developed their own written commissioning standard. This is more than just an RFP or a detailed specification; these are true commissioning standards that require what is to be commissioned and how it is to be commissioned. When properly developed, these are a great thing for the industry. Many owners are becoming more educated on what true commissioning entails, and this is helping to level the playing field and remove some of the unqualified competition.
Lindstrom: As owners have increasingly realized the benefits of a thorough commissioning process, the process itself has been adapted for expanded and much more complex systems and facilities. Engineers should expect to see commissioning processes developed for nontypical systems such as baggage-handling systems at airports and information technology systems in data centers, to name a few. CxAs themselves need to broaden their knowledge of the basic facility systems to meet the demands of much more complex systems as commissioning becomes more specialized.
Gelfo: The biggest change we’ve seen is in the quantity and types of projects that are being commissioned. Ten years ago, fewer projects were being commissioned, and those were larger or more complex projects, or projects that were pursuing LEED certification. In recent years, more projects are being commissioned, regardless of green-building-rating systems. Owners are focused on performance; they want to make sure their buildings are operating as expected. We expect the focus on actual operational performance to continue, and, obviously, commissioning, retro-commissioning, and recommissioning will play a major role in performance.
Givens: We have conducted many third-party commissioning efforts. We also have provided commissioning services on a fair number of projects designed in-house. Either way, we maintain a separation of design and commissioning—our commissioning providers are employed by a separate division within the firm.
Lindstrom: We provide commissioning as both a third-party service and as part of our integrated design-build process. Both approaches use our dedicated commissioning-practice resources that are independent of design and construction teams and emphasize collaboration to successfully achieve the owner’s project requirements.
Gelfo: Although TLC is known primarily as a mechanical, electrical, and plumbing (MEP) engineering firm, we have teams in each of our offices that are dedicated to commissioning and energy-services work, separate from our design engineering teams. We believe in the value of third-party, independent commissioning as a best practice. Our teams provide third-party commissioning on projects engineered by other firms and also, on occasion, on commission projects that have been designed by our MEP design engineers. When that does occur, our commissioning team remains completely independent of the design team and maintains an open and direct reporting path to the owner. Our commissioning and energy-services teams also perform energy auditing and retro-commissioning of existing buildings. Whether it is new-building commissioning, existing-building commissioning, or energy auditing, our goal is to work with our building owners to help them meet their goals, reduce energy consumption, and lessen operating costs.
Huber: Our firm conducts 100% third-party commissioning.
Meyer: Whether we are performing commissioning for projects designed by our firm, or designed by others, we follow the same process and approach our work as an agent of the owner’s best interest. In our company, the commissioning engineers are a completely separate group from the design engineers. Many of our commissioning engineers have backgrounds in building operations and management, and not design. We do benefit from commissioning our own designs in that we can easily approach the designers with questions or clarifications. For LEED projects where our company designed the project, we team with a third-party firm who then becomes the lead commissioning authority per LEED requirements.
CSE: On what aspect of commissioning do you see the most emphasis being placed by building owners? In what areas is your firm doing the most work?
Meyer: There are two trends, as I see it. There are owners who buy the bare-minimum scope of work such as LEED fundamental commissioning, and they always will buy low. Other owners who have experience in commissioning often start to expand the scope, adding emergency generators, electrical distribution, security, and life safety systems. Our company has a dedicated building envelope commissioning group. Owners who have experienced early façade degradation or water intrusion often buy envelope commissioning on their next project.
Lindstrom: Commissioning of HVAC systems is where the industry started and predominately emphasized acceptance-phase activities. So it is not surprising that the majority of the systems that get commissioned are still mechanical. As the industry has matured and the value of the commissioning process has become more widely demonstrated, the full process has been increasingly adopted and system types have been expanded. For critical facility applications, we see high demand for electrical, power, life safety, and security commissioning. Our production/manufacturing-type clients are demanding that even process systems be commissioned. With more emphasis increasingly placed on air quality, building enclosures also have jumped to the top of the client demand list. However, the single greatest demand we are seeing today is for whole-building commissioning. Clients increasingly recognize that efficiency, reliability, safety, productivity, and other key performance goals can only be achieved when all their facility systems are working properly in an integrated fashion.
Huber: HVAC/building automation systems (BAS) are always the highest priority, followed by electrical systems. Lately, we have seen a greater emphasis for building enclosure commissioning, and we have also seen an increase in fire protection and smoke-control systems.
CSE: What unique tools, software, or systems do you use when performing commissioning?
Lindstrom: We developed a suite of digital tools that we call the Burns & McDonnell Commissioning Cloud, or BMCx Cloud. The tools are part of a proprietary, secure, enterprise workflow technology that combines mobile computing, geographic information system (GIS), and database technologies. The BMCx Cloud enables greater efficiency, maximized quality, and enhanced communication for all team members.
Meyer: Because every commissioning project is unique, we use a combination of homemade tools and software as well as purchased systems. For many of our commissioning projects, we use the Quicx software package. The commissioning process is heavy on documentation and some form of system or software is needed to track all of the paperwork.
CSE: Is it important for one or all of your team members to be certified/accredited as a CxA?
Gelfo: Absolutely. While a credential does not guarantee experience or expertise, it does demonstrate a minimum level of competency and commitment to the commissioning profession. Most commissioning RFQs require team members to have a CxA credential. At TLC, we have earned most of our credentials through AABC Commissioning Group (ACG), with whom we have been active members for nearly 10 yr. We encourage all of our eligible, qualified Cx and energy team members to pursue and obtain the appropriate credentials, whether it be CxA, energy management professional (EMP), etc.
Huber: It’s very important—and the governmental and industry push for all commissioning certification programs to become ANSI-accredited only makes those certifications more important. We employ CxAs who are certified/accredited by National Environmental Balancing Bureau (NEBB), the Building Commissioning Association, Association of Energy Engineers, and the University of Wisconsin, and most of our CxAs are accredited by multiple organizations. We are true believers in technical commissioning versus process commissioning, and we have found the NEBB technical commissioning training and certification programs to be our preference. This is especially true when it comes to retro-commissioning versus commissioning. Unfortunately, the industry seems to want to lump these disciplines together, but they really are completely different skill sets. I also think it is very important for the commissioning firm to be certified; this ensures that the firm owns the proper instrumentation and has the necessary calibration programs and expertise to provide a quality product. It also provides assurance to the owner because the firm is covered by a quality assurance program.
Givens: We do indeed place importance on the certification/accreditation of our commissioning providers, because we see commissioning as a respectable professional service, and we feel that the personnel providing such service should be identified and recognized with appropriate credentials. That said, we have not adopted this philosophy as a strict requirement for our entire team. Anyone from our team responsible for managing a commissioning project or service will carry a suitable commissioning-industry certification. We also employ team members with vast technical experience in various trades, who are not necessarily certified/accredited. These trade specialists are responsible for the tactical execution of various aspects of the commissioning process, serving very important portions of the bigger picture overseen by the certified/accredited commissioning-process manager.
Meyer: We strongly encourage our engineers to be accredited. There are a lot of different accreditations out there for commissioning engineers. We do not have favorites when it comes to certifying bodies, and there is probably at least one staff member in our company with every commissioning accreditation. Commissioning is a relatively young profession, and accreditation is an important identifier to prove competence.
Lindstrom: Yes, CxA certifications are one of the many important credentials our commissioning managers and discipline leads are required to achieve. We support this certification because it provides another third-party assurance of competency and credibility. However, it’s important to note that—like any profession—commissioning and, more importantly, proficiency as a CxA cannot be learned from study or achievement of a certification alone. Our engineers, architects, and technicians also are required to obtain respective discipline registration/accreditation (architectural, mechanical, electrical, fire protection, controls, test and balance, NETA, etc.) as well as industry-specific accreditation (sustainability, energy, enclosure, data center, manufacturing, health care, pharmaceutical, nuclear, etc.) for their focus areas. The combination of commissioning process, discipline, and industry knowledge combined with on-the-job training, mentoring, and experience performing commissioning is the best path to ensure the most robust team of commissioning professionals.
CSE: Where in the timeline of design, bid, build does your commissioning team fall? Do you think this needs to be earlier or later, and why?
Givens: As commissioning providers, we have been integrated into the project at all phases of the timeline—predesign, during design, bid, and construction. In general, earlier is better—it enables more efficient application of the fundamental commissioning intent, and it also promotes better teamwork among the project players. However, certain project types (and certain owner/team types) benefit from one or the other—integrating commissioning early in the design phase or focusing mainly on later commissioning integration with the primary objective being functional testing, system performance, and facility acceptance/turnover.
Meyer: Some commissioning engineers think they should be hired by the owner, and then the owner looks for an architect and design engineer. While extreme, the intent is to get the commissioning engineer onboard as early as possible. The value the commissioning engineer brings to the project diminishes the later in the project he starts. Issues the commissioning engineer can find on paper are far cheaper to correct than when found in final field testing.
Huber: Our preference is to be hired before the design team. Unfortunately, that is a lesson that sometimes takes building owners a while to learn because it is a departure from conventional thinking.
Lindstrom: We have started commissioning at all possible points one could start a project, from before the design during the program-development stage to just being brought on to perform the integrated system test to after owner occupancy when problems began to surface. During lessons-learned meetings, the most typical feedback (outside of when we were brought in during early planning stages) was that we should have been engaged earlier. This feedback almost always surfaces during meetings with the full team (owner, designer, contractor, operations and maintenances staff, subcontractors, etc.). Early engagement allows us to define what success looks like with an owner’s project-requirements document and commissioning specifications. It allows us to partner with all stakeholders to promote buy-in.
CSE: How has your commissioning team trained and/or mentored younger staff? What best practices can you offer to enhance a commissioning team’s long-term success?
Givens: There is no replacement for hands-on experience. Understanding the fundamental principles of the commissioning process is certainly paramount, which is why we encourage and embrace organized training for it. However, much value comes in the application of that training amid potentially diverse project types and project teams. We have found that it is this applied, hands-on experience that has the bigger impact and lasting effect on the development of a successful commissioning team.
Gelfo: Over the past year, we have hired several new and junior energy-services (commissioning and energy-auditing) staff. It has been a good opportunity for us, not only to have additional manpower, but also for our more seasoned commissioning staff to get into “teaching mode.” The opportunity to share their knowledge and experience, both formally and informally, seems to invigorate many of our senior commissioning authorities. Some of the best practices we’ve discovered include:
- Develop a written training plan with goals, objectives, and specific training activities for the initial training period. We’re still new at this, but we’ve realize that simply having the discussion and writing it down is 90% of the battle.
- Mix of informal and formal training
– Informal: One-on-one mentoring between senior CxAs and junior staff
– Formal: TLC University classes, structured learning webinars, and conferences. - On-the-job training; a combination of office work and supervised field work.
- Having the right mix of experienced staff makes the entire team more effective.
Lindstrom: All new commissioning specialists with anywhere from 0 to 5 yr of experience are mentored under senior leadership. Each new member is assigned a specific mentor who takes personal responsibility for the individual’s development. These mentors pass on the knowledge they have learned through commissioning a large number of projects and lessons learned on those projects. An extra layer of mentoring occurs through our multiphase quality analysis/quality control (QA/QC) process, where everything that is developed (commissioning plan, functional test, etc.) is reviewed, commented, and enhanced. It is also important to keep the entire practice informed of all of the lessons learned on projects they were not necessarily involved in. We hold monthly lessons-learned meetings to formally share best practices with all our specialists across the nation.
Huber: Ultimately, there is no replacement for experience. We will not hire commissioning staff that are without a good level of design or field experience. That can be programming, installation, troubleshooting, or system design, and we prefer that our people also hold trade licenses in addition to commissioning certifications. For younger staff, they are assigned to a product and stay on that product with a senior CxA or principal throughout the project’s completion. That includes commissioning meetings, submittal reviews, test-form development, site visits, testing, and project closeout.
Meyer: We believe strongly in training and mentoring. I personally have written and taught an undergraduate course in building commissioning at a local college’s A/E program, and I use the same materials inside the company. Our company also has a formal mentoring program in which I participate. You cannot expect peak performance from your staff members if you do not train them to your standards and give them the tools they need to excel. My staff is used to my “FYI” e-mails containing the latest development or pertinent training. As I pass people in the halls, I will spot-quiz them to see if they’ve read and retained the information.